Titel: | Ueber Glasmanufaktur, von Horatius N. Fenn, M. Dr. |
Fundstelle: | Band 35, Jahrgang 1830, Nr. LXXIII., S. 297 |
Download: | XML |
LXXIII.
Ueber Glasmanufaktur, von Horatius N. Fenn, M. Dr.Hr. Dr. Fenn beschaͤftigte sich praktisch mit der Glasmachern, und theilte Hrn. Dr.
und Prof. Silliman
gegenwaͤrtige Bemerkungen auf Ansuchen des lezteren mit. Es sind noch
nicht 30 Jahre, daß Boͤhmen und zum Theile auch Bayern, den
groͤßten Theil Nordamerikas mit Glas aus seinen Glashuͤtten und
auch mit Glasmachern versah. Wenn die Amerikaner so fortfahren, werden sie uns
in 30 Jahren mit Glas versehen. A. d. Ue.
Aus Silliman's Americ. Journal. Bd. XVI. N.
1.
Mit Albbildung auf Tab.
VII.
Toͤpfe oder Haͤfen.
Fenn, uͤber Glasmanufaktur.
Es ist auf allen Glashuͤtten gebraͤuchlich, daß man sich die
Toͤpfe oder Haͤfen selbst bereitet. Wer sich nicht selbst praktisch
mit Glasmacherei beschaͤftigt hat, kann weder die Wichtigkeit noch die
Schwierigkeiten der Verfertigung dieser Toͤpfe gehoͤrig beurtheilen.
Wenn die Toͤpfe schlecht sind, geraͤth die ganze Arbeit in Unordnung:
nicht bloß die ersten Gestehungskosten der rohen Materialien, sondern auch die
Arbeit bei Zubereitung derselben und die Arbeitskosten sind rein verloren. Wenn
aber, im Gegentheile, die Toͤpfe gehoͤrig bereitet sind, so ist der
Glasmacher zum Voraus seiner Glaserzeugung sicher; er weiß, was er erhaͤlt,
und kann es zum hoͤchsten Vortheile verwenden. Er kann die Wirkung des Feuers
reguliren, die glasartigen Materialien nach Belieben wechseln, und, mit einem Worte,
die ganze Arbeit nach seinem Gutbefinden leiten und uͤbersehen. Es ist daher
hoͤchst wichtig, daß man der Verfertigung der Toͤpfe die
hoͤchste Aufmerksamkeit schenkt, damit dieselben so vollkommen als
moͤglich ausfallen.
Hierzu wird nun vor Allem wesentlich erfordert, daß die Materialien, aus welchen die
Toͤpfe verfertigt werden, durchaus von der besten Qualitaͤt sind. Man
fuͤhrt bei uns fuͤr unsere Glashuͤtten drei verschiedene Arten
von Thon zu den Toͤpfen ein: den weißen und blauen deutschen Thon, und den englischen blauen Thon.
Alle diese Thonarten sind aus der Classe des sogenannten Porzellanthones. Der blaue
Thon erhaͤlt seine Farbe von kohlenstoffhaltigen Stoffen, indem er sich in
dem Ofen weiß brennt. Wir haben in unserem Lande viele Thongruben, welche einen Thon
liefern, der Statt des auslaͤndischen eingefuͤhrten Thones gebraucht
wird. Die einzige Art, die ich anwenden sah, ist der Philadelphia- oder
New-Castle-Thon, der, wie man mir sagte, am Flusse Delaware, bei
New-Castle, unter dem Hochwasser-Zeichen gefunden wird.
Dieser Thon kommt in Massen von der Groͤße eines Mannskopfes zu uns, und ist weiß mit
rosenfarbenen Fleken von verschiedener Groͤße, die durch die ganze Masse
desselben zerstreut sind. Diese Fleken ruͤhren offenbar von Braunsteinoxyd
her, indem sie in der Hize des Ofens schwarz werden. Dieser Thon ist aͤußerst
unschmelzbar, und, wenn er im gehoͤrigen Verhaͤltnisse mit den
uͤbrigen Thonarten gemengt wird, bildet er eine Mischung zu Toͤpfen,
die jeder einzelnen Thonart fuͤr sich allein vorzuziehen ist.
Zur Verfertigung der Toͤpfe bedienen wir uns gleicher Theile rohen Thones,
gebrannten Thones und Scherben der alten Toͤpfe. Leztere erhaͤlt man
durch Zerschlagen der alten Toͤpfe, die aus dem Ofen geschafft werden mußten,
und von welchen man das anhaͤngende Glas und die Glasur abgeklopft hat. Diese
Materialien werden, jedes fuͤr sich einzeln, gemahlen und durch ein feines
Sieb durchgesiebt, dann zusammen in einen Trog gethan, und, troken, auf das Innigste
unter einander gemengt. Man gießt hierauf Wasser zu, bis die ganze Masse die
Consistenz eines Moͤrtels erhaͤlt. In diesem Zustande laͤßt man
sie 10 bis 14 Tage mit einem nassen Tuche bedekt stehen. Nach Verlauf dieser Zeit
wird sie eine teigartige Masse bilden, und beinahe eben so zaͤhe seyn. Nun
laͤßt man sie von einem Arbeiter umkehren und mit den Fuͤßen treten.
Dieser faͤngt hierauf an sie in Stuͤke von der Dike eines Zolles drei
bis vier Zoll breit zu schneiden, und legt sie auf den Boden des Troges von dem
Hinteren Ende desselben anfangend; wenn der Boden auf diese Weise bedekt ist, steigt
er auf die Stuͤke und tritt sie mit seinen Fuͤßen fest. Auf diese
Weise faͤhrt er fort, bis die ganze Masse durchgetreten ist. Diese Arbeit
geschieht taͤglich, bis der Thon fest wird, oder, in anderen Worten, bis die
Luft aus demselben ausgedruͤkt ist, so daß er, wenn man ihn schneidet, eine
vollkommen gleiche und ebene Masse bildet. Wenn er nun die gehoͤrige
Consistenz hat, koͤnnen Toͤpfe aus demselben verfertigt werden. Man
glaubt, daß er besser wird, wenn man ihn in. diesem Zustande sechs bis zwoͤlf
Monate lang liegen laͤßt, ehe man Toͤpfe daraus verfertigt, und, so
weit meine Erfahrung reicht, ist dieß auch wirklich so.
Zur Verfertigung der Toͤpfe bedienen wir uns walzenfoͤrmiger Model aus
Holz mit eisernen Reifen gebunden, und zu jeder Seite sich oͤffnend. Auf
diese legt der Arbeiter Stuͤke Tuches, die so befeuchtet sind, daß sie an den
Seiten des Models anhaͤngen, bis die ganze innere Seite damit bedekt ist.
Dieß geschieht, um die Toͤpfe leichter aus den Modeln nehmen zu
koͤnnen. Nachdem der Model so vorgerichtet wurde, schneidet der Arbeiter ein
Stuͤk Thon ab, ungefaͤhr von der Groͤße, wie er sie zur Bildung
des Bodens des Topfes und zu vier bis fuͤnf Zoll Seitenwand desselben
noͤthig glaubt. Dieses Stuͤk bringt er auf ein Brett, welches groß genug
ist den Boden des Models zu bedeken, stellt nun den Model auf dasselbe, steigt auf
den Thon, und tritt denselben rings um den Boden nieder. Der Mittelpunkt des Thones
wird nun mittelst eines eigenen hierzu verfertigten hoͤlzernen Blokes zur
gehoͤrigen Dike des Bodens des Topfes nieder gestampft, und der Rest
desselben rings um die Seiten des Models mit der Hand in der gehoͤrigen Dike
aufgeschlagen. Die Seiten des Topfes werden dann dadurch ausgebildet, daß man
innenwendig In dem Model so lang kleine Rollen von Thon mit der Hand anlegt, bis man
mit der Wand beinahe bis an den Rand des Topfes hinauf gekommen ist. Die innere Wand
des Topfes wird nun mit einem eisernen Instrumente flach gepuzt, und der obere Rand
desselben gehoͤrig zugeformt und vollendet. Man stellt jezt den Topf bei
Seite, um ihn troken werden zu lassen, und wenn man glaubt, daß er fest genug
geworden ist, um fuͤr sich allein stehen bleiben zu koͤnnen, was
gewoͤhnlich in zwei Mal vier und zwanzig Stunden der Fall ist, wird der Model
abgenommen, und der Topf an seiner Außenseite sorgfaͤltig vollendet. Mit dem
Abebenen (Puzen) und dem weiteren Festmachen des Topfes wird taͤglich so lang
fortgefahren, bis der Topf so hart und troken geworden ist, daß er keinen Eindruk
von Außen mehr aufzunehmen vermag. Der Topf waͤre nun allerdings fertig;
allein er muß noch 6 oder 12 Monate lang stehen, ehe er gebraucht werden kann; denn
die Erfahrung hat auf das Deutlichste erwiesen, daß ein Topf, der ein Jahr lang
uͤber ruhig gestanden ist, weit weniger der Gefahr ausgesezt ist, im Ofen zu
leiden, als ein ganz neuer Topf. In die Kammer, wo diese Toͤpfe aufbewahrt
werden, darf kein Frost eindringen, indem sonst das Wasser in denselben (und sie
enthalten noch immer einiges Wasser) frieren und sie zerstoͤren
wuͤrde.
Wir verfertigen unsere Toͤpfe gewoͤhnlich zwei Fuß hoch, und geben
denselben am oberen Rande 20 Zoll, am Boden 16 Zoll im Durchmesser. Der Boden ist
zwei und einen halben Zoll dik; die Seitenwand hat oben anderthalb, unten zwei Zoll
Dike. Ein Topf von dieser Groͤße faßt, nachdem er gebrannt ist, 250 Pfd.
Glas. Wir haben gewoͤhnlich zwischen 80 und 100 Toͤpfe in der
Topfkammer vorraͤthig, so daß wir nie zu neuen Toͤpfen Zuflucht zu
nehmen brauchen. Wenn die Toͤpfe gut gemacht sind, und wenn das Material
derselben gut ist, so haͤlt ein solcher Topf drei bis sechs Wochen im Ofen
aus. Wenn sie aber schlecht gearbeitet wurden, und der Thon mager (arm) ist, so
bersten sie gern an der Seite, die dem Mittelpunkte des Ofens zugekehrt ist, und
gewoͤhnlich, wann die eingesezte Masse anfaͤngt in vollkommenen Fluß
zu gerathen. Wo dieß geschieht, ist hie ganze Masse im Topfe verloren, und fließt in
die Mitte des Ofens, wo
sie sich mit der daselbst befindlichen Kohle in Asche vermengt.
Wenn ein neuer Topf eingesezt werden soll, so kommt er in den Kuͤhlofen, und
wird in demselben mit aller Sorgfalt aufgestellt. Das Feuer in diesem Ofen wird nach
und nach bis zur hellen Rothgluͤhhize verstaͤrkt, und fuͤnf bis
sechs Stunden lang auf diesem Punkte erhalten. Wenn die Arbeiter aufhoͤren zu
blasen, laͤßt man den Ofen bis zur Temperatur des Kuͤhlofens
abkuͤhlen, und bringt dann den Topf bei der Hinteren Thuͤre (dem
Tiegelloche) ein: er wird mittelst einer langen eisernen Stange und mittelst Haken
auf die Bank unmittelbar unter das Fenster oder das Arbeitsloch (the ring) gestellt.
Der Verlust, der durch mißlungene Toͤpfe entsteht (und das Mißlingen derselben
kann ungeachtet aller Sorgfalt und Geschiklichkeit der erfahrensten und
verstaͤndigsten Arbeiter nicht immer verhuͤtet werden), erhoͤht
die Erzeugungskosten des Tafel- oder Fenster-Glases schon auf der
Huͤtte um ein Bedeutendes. Wenn wir irgend eine Masse entdeken
koͤnnten, die, nebst den wesentlichen Eigenschaften des Thones, auch noch die
Tugend besaͤße, nicht gebrechlich zu seyn, so wuͤrde dadurch ein
großes Desideratum in der Glasmacherkunst erreicht werden.
Die verschiedenen Gebaͤude, die in einer Glashuͤtte, in welcher man
Tafel- oder Fenster-Glas verfertigt, nothwendig werden, sind:
1) Roͤst- oder Calcinir-Oefen zur Zurichtung der
Materialien.
2) Ein Reverberir-Ofen zum Schmelzen derselben.
3) Ein Strekofen, zum Streken und Abkuͤhlen des Glases.
4) Trokenoͤfen oder Holzdarren zum Troknen des Holzes.
5) Ein Brennofen (Tempering-oven) zum Brennen der
Toͤpfe und des Thones uͤberhaupt.
Von allen diesen Oefen das Noͤthige im Verlaufe der Beschreibung der
Arbeit.
Die glasartigen Materialien und die Verhaͤltnisse derselben, wie man sie bei
uns zum Glase braucht, sind folgende:
Verona-Sand
100 Theile
Potasche
34 –
Salz
18 –
Kalk
5 –
Hausasche
45 –
Glasscherben
30 –
––––––––
Sand
100 Theile
SodaWenn dieses Salz noch sein Krystallisationswasser hat, wo man es zu
Glas verwendet, muͤssen 440 Theile genommen werden. A. d.
O. (Sul)
60 –
Kalk
5 –
Asche
20 Theile
Saͤgespaͤne
2 –
Glasscherben
20 –
––––––––
Sand
100 Theile
Kelp
65 –
Kalk
8 –
Glasscherben
30 –
Hausasche
25 –
––––––––
Sand
100 Theile
Potasche
20 –
Kelp
28 –
Kalk
5 –
Hausasche
15 –
Glasscherben
25 –
––––––––
Sand
100 Theile
Potasche (Sul)
45 –
Kalk
8 –
Hausasche
15 –
Saͤgespaͤne
2 –
Glasscherben
30 –
Diese Mischung ist diejenige, welche wir gewoͤhnlich gebraucht haben; in
mancher Hinsicht ist sie allen uͤbrigen vorzuziehen.
Der Sand wird in den Calcinir-Ofen geworfen, und in diesem fuͤnf oder
sechs Stunden lang gegluͤht. Die Hausasche wird auf dieselbe Weise behandelt.
Der Zwek dieses Ausgluͤhens bei beiden ist: Verbrennung der Pflanzenstoffe,
und Verjagung des Wassers und der Kohlensaͤure, welche in diesen Materialien
enthalten seyn koͤnnten. Sobald dieser Zwek erreicht ist, werden diese
Materialien aus dem Ofen genommen, man laͤßt sie abkuͤhlen und siebt
sie durch ein Sieb, dessen Loͤcher 1/30 Zoll im Durchmesser balten.
Der Kalk wird in ein Hydrat verwandelt (geloͤscht) und gleichfalls
durchgesiebt. Die Potasche wird in Stuͤke gebrochen, die nicht groͤßer
sind, als eine Wallnuͤß. Das Salz braucht keine Zubereitung.
Kelp. So nennt man ein Salz, das aus der Asche unter den
Kesseln der Salzwerke zu Salina bereitet wird. Es wird
auf dieselbe Weise, wie Potasche, durch Auslaugen und Abdampfen gewonnen. Man
braucht es auf unserer Glashuͤtte als Surrogat fuͤr Salz und Potasche.
Es scheint mir ein zusammengeseztes Salz, welches aus kochsalzsaurer Potasche und
kohlensaurer oder basisch kohlensaurer Soda in beinahe gleicher Menge besteht.
Dieses Salz waͤre der Potasche bei der Glaserzeugung vorzuziehen, wenn man
sich immer auf das gehoͤrige Verhaͤltniß seiner Bestandtheile
verlassen koͤnnte; da aber dieses zuweilen sehr wechselt, so entsteht dadurch
zuweilen bedeutender Verlust.
Wenn man schwefelsaure Potasche oder Soda nimmt, so muß diese fein gepuͤlvert
werden. Saͤgespaͤne nimmt man, weil sie besser dienen als Holzkohle.
Beide zersezen die schwefelsauren Salze, indem sie sich des Sauerstoffes der
Schwefelsaͤure bemaͤchtigen, und mit derselben Kohlensaͤure
bilden, die durch die Masse entweicht, waͤhrend der Schwefel der
Schwefelsaͤure, der dadurch frei wird, durch die angewendete Hize verjagt
wird, und so das Alkali in seiner reinsten Form zur Vereinigung mit der Kieselerde
zuruͤklaͤßt.
Nachdem die Materialien auf diese Weise zubereitet wurden, werden sie so innig unter
einander gemengt, daß alle die verschiedenen Bestandtheile derselben
gleichfoͤrmig in der ganzen Masse vertheilt sind. Wo es die Umstaͤnde
erlauben, sollte man die Masse in diesem Zustande drei Monate lang ruhen lassen.
Die oben angegebenen Mischungsverhaͤltnisse der Fritte erzeugen nur sehr
geringe Verschiedenheiten in der Qualitaͤt des Glases, und die Zeit, deren
sie beduͤrfen, um in Fluß zu gerathen, ist beinahe dieselbe. Was die
verschiedenen Kosten derselben belangt, so haͤngen diese nothwendig von den
Schwankungen der Marktpreise einzelner Artikel ab, und sind daher nach denselben
verschieden.
Zuweilen, wenn naͤmlich diese Materialien nicht vollkommen frei von allen
vegetabilischen Unreinigkeiten sind, bekommt das Glas eine gelbliche Farbe. Um dieß
nun zu verhuͤten, oder, wo es bereits eingetreten ist, zu verbessern, nimmt
man zuweilen weißes Arsenikoxyd, schwarzes Braunsteinoxyd, Salpeter und die
Bleioxyde. Alle diese Oxyde scheinen dadurch zu wirken, daß sie Sauerstoff liefern,
welcher sich mit dem Kohlenstoffe verbindet, und denselben als kohlensaures Gas
entweichen laͤßt.
Um diese Materialien auf den Boden der Toͤpfe hinabzubringen, so daß sie sich
mit dem Glase vereinigen und die gewuͤnschte Wirkung hervorbringen
koͤnnen, ist es am besten, sie in nasses Papier einzuwikeln, und mittelst
einer eisernen Stange unterzutauchen. Mit schwarzem Braunsteinoxyde gelang mir
dieses Verfahren gewoͤhnlich auf die vollkommenste Weise. Die Wirkung des
Kalkes, welcher zu allen Fritten kommt, ist, wie man glaubt, Erleichterung des
Flusses; noch eine andere Wirkung, die der Kalk hervorbringt, ist
zuverlaͤssig aber diese, daß er das Glas zum besseren Waͤrmeleiter
macht, so daß es bei dem Abkuͤhlen und bei den uͤbrigen darauf
folgenden Arbeiten an demselben weniger in Gefahr ist zu brechen, vorzuͤglich
dann, wann es der Einwirkung des Demantes ausgesezt wird.
Das Holz, mit welchem der Werkofen, worin das Glas geschmolzen und geblasen wird, geheizt wird,
ist zwischen drei- und vierthalb Fuß lang, und so fein gespalten, daß ein
Scheitchen nicht mehr als zwei Zoll im Durchmesser hat. Alles dieses Brennholz muß
in der Darrstube (im Darrofen, Kiln) getroknet werden.
Sechs solche Darrofen sind in der Mitte der Glashuͤtte angebracht, und jeder
derselben faßt eine halbe Maß (cord) Holz. Wenn der
Werkofen im Gange ist, braucht er in 24 Stunden sechs Maß (cords) Holz.
Der Werkofen selbst wird entweder aus feuerfesten Baksteinen, aus demselben Thone,
wie die Toͤpfe, oder aus irgend einem natuͤrlichen Sandsteine erbaut,
der so wenig als moͤglich, oder gar nicht schmelzbar ist bei der Temperatur
des Glasofens.Talg ist das beste Material zu einem Glasofen, wo er, wie in
Kaͤrnthen, in schoͤnen derben Bloͤken zu haben ist.
Gewiß findet sich auch solcher Talg in Amerika. A. d. Ue.
Der Sandstein, den man gewoͤhnlich hierzu waͤhlt, kommt von Haverstraw am North-River.
In dem Werkofen stehen 10 Toͤpfe, fuͤnf zu jeder Seite desselben, auf
Baͤnken, die der Laͤnge des Ofens nach hinlaufen, und die 10 Zoll hoch
uͤber der Sohle (tone) stehen: so nennt man
naͤmlich den Raum in der Mitte des Ofens zwischen den Toͤpfen. Jedem
Topfe nach Außen gegenuͤber ist der Fensterstein (ring
stone), durch welchen ein Loch laͤuft, (das Arbeitsloch, the ring) von ungefaͤhr 7 1/2 Zoll im
Durchmesser. Durch dieses Loch kommt die Fritte in den Topf und wird das Glas zum
Blasen herausgenommen. Diese Loͤcher sind zugleich auch die einzigen
Zugloͤcher, wodurch der Zug mittelst kleiner Ziegelsteine (cookies) regulirt wird. An jedem Ende des Ofens ist ein
Feuerherd von hinlaͤnglicher Groͤße, um die Toͤpfe durch
denselben in den Ofen bringen zu koͤnnen. Nachdem die Toͤpfe eingesezt
wurden, werden die Herde mit einer Thuͤre aus Baksteinen von acht Zoll Dike
geschlossen. In dieser Thuͤre bleibt eine Oeffnung von vier Zoll im
Durchmesser, durch welche das Holz in den Ofen gebracht wird. Unten an der Sohle der
Thuͤre bleibt auch noch eine Oeffnung, um der Luft Eingang zu verschaffen,
und die Sohle des Herdes (the lock stone) ist zu
demselben Ende gleichfalls durchbohrt.
Der Ofen wird an seinen vier Eken von Saͤulen aus Baksteinen getragen.
Gewoͤhnlich bringt man an jedem derselben einen Roͤstofen an, der
mittelst eines Zuges mit dem Werkofen in Verbindung steht. Durch diese Einrichtung
erspart man Brennmaterial, welches sonst fuͤr die Roͤstoͤfen
einzeln verbrannt werden muͤßte.
Wenn ein Werkofen erbaut ist, so braucht man drei bis vier Wochen um den Ofen
auszuheizen, d.h., ihn auf jene Temperatur zu erhoͤhen, welche zum Schmelzen
des Glases nothwendig ist. Wenn diese Temperatur einmal erreicht ist, wird sie auf
folgende Weise immer gleichfoͤrmig unterhalten. Der Heizer (the Stoaker) faͤngt seine Arbeit damit an, daß er
zwei Scheite trokenen Holzes nimmt, und eines derselben durch das Loch in der
Baksteinthuͤre, die ihm zunaͤchst steht, einbringt, hierauf um den
Ofen herumgeht, und in das Loch der anderen Baksteinthuͤre das andere Scheit
auf dieselbe Weise einfuͤhrt. Auf diese Weise geht er immer um den Ofen herum
und versieht sich zugleich mit dem noͤthigen Holze. Sein Gang ist so
bemessen, daß er, immer gleichen Schritt haltend, in diesem Schritte drei
(englische) Meilen in Einer Stunde zuruͤklegen wuͤrde.Die englische Statute-Mile hat 5280 engl.
Fuß, oder 1609 Meter. A. d. Ue. Auf diese Weise versieht er sechs Stunden lang den Ofen regelmaͤßig
und ununterbrochen mit Holz, nach welcher Zeit er von einem anderen Heizer
abgeloͤst wird, den er nach 6 Stunden neuerdings wieder abloͤst. Wir
verwenden zu diesem Dienste immer alte und unbrauchbar gewordene Blaͤser,
indem sie mit der Art bekannt sind, in welcher das Feuer unterhalten werden muß,
wenn Glas mit der moͤglich kleinsten Menge Holzes auf die schnellste Weise
geschmolzen werden soll. Obschon diese Arbeit hoͤchst einfach zu seyn
scheint, so kann man doch durch einen erfahrnen und geschikten Heizer bei jeder
Schmelzung an zwei Stunden Zeit ersparen.
Das Schmelzen. Nachdem der Ofen bis zur sogenannten
Weißhize gehizt wurde, wird die Fritte (mixing) durch
die Fenster oder Arbeitsloͤcher mittelst einer eigenen eisernen Schaufel in
die Toͤpfe eingetragen. Wenn nun die Toͤpfe gefuͤllt sind,
werden die Ziegelsteine (cookies) in den Fenstern wieder
vorgelegt, und das Feuer auf den hoͤchsten Grad gebracht, auf welchem es so
lang regelmaͤßig unterhalten wird, bis die ganze Fritte vollkommen im Fluß
ist. Waͤhrend dieser Arbeit untersucht der Werkmeister (Master stoaker) gelegentlich das Glas mit einem eisernen
Staͤbchen, um zu sehen, ob es mit dem Flusse gehoͤrig vorwaͤrts
schreitet. Nachdem nun der erste Einsaz oder Eintrag (laying in)
geschmolzen ist, wird neuerdings Fritte zugesezt, und hiermit so lang fortgefahren,
bis die Glasmasse nur mehr drei Zoll weit vom Rande des Topfes absteht. Damit die
Mischung der verschiedenen Einsaͤze der Fritte gehoͤrig, und so innig
als moͤglich geschieht, um eine vollkommen gleichfoͤrmige Masse zu
erhalten, wird jezt umgeruͤhrt.
Dieses Umruͤhren geschieht entweder mittelst eines eisernen Stabes, oder
besser mittelst eines Erdapfels an einem eisernen Staͤngelchen. Diesen
fuͤhrt man bis auf den Boden des Topfes durch das geschmolzene Glas hinab, wo dann
die ploͤzliche Verwandlung des in demselben enthaltenen Wassers in Dampf in
der ganzen Masse eine Bewegung erzeugt, die dem Aufwallen beim Sieden
aͤhnlich ist, und das Glas bis an den Rand des Topfes hebt. Da sich hierauf
die Masse bald wieder sezt, werden die Toͤpfe mit Glasscherben
gefuͤllt, und die Baksteine wieder in die Fenster eingelegt.
So wie das Feuer fort unterhalten wird, steigt Luft aus der Fritte in Form einer
Menge von Blasen auf, die an der Oberflaͤche bersten, bis endlich die
fluͤssige Masse vollkommen klar wird.
Wenn man sich nun einmal von der Klarheit der Fritte uͤberzeugt hat,
laͤßt man den Ofen sich etwas abkuͤhlen, und erhaͤlt ihn eine
Stunde lang oder uͤberhaupt so lang in dieser Temperatur, bis das Glas an dem
oberen Rande der Toͤpfe anfaͤngt steif zu werden. Waͤhrend
dieser Zeit werden die Thuͤren an dem Ofen geoͤffnet, um die Schlaken,
Asche und Kohlen, die sich waͤhrend des Schmelzens auf der Sohle des Ofens
angehaͤuft haben, herauszuschaffen. Das Feuer wird nun wieder
allmaͤhlich verstaͤrkt, bis die Glasmasse (the
metal) die zum Blasen gehoͤrige Consistenz erhaͤlt. Nun
werden die Blaͤser angestellt, und der Werkmeister
am Ofen (Master-stoaker)
uͤbertraͤgt die Aufsicht auf den Ofen dem Blasmeister (Master blower), der
waͤhrend des Blasens die Heizung des Ofens zu besorgen hat. Wenn der Ofen neu
ist, so werden im Durchschnitte vier und zwanzig Stunden zum Schmelzen erfordert,
und wenn er bereits sechs Monate im Feuer steht, dreißig Stunden. Gewoͤhnlich
haͤlt man einen Ofen neun Monate lang im Gange, vom September bis Junius, und
verwendet dann die uͤbrigen drei Monate zur Ausbesserung desselben. Ein Ofen
mit zehn Toͤpfen von gewoͤhnlicher Groͤße erzeugt zwischen
sieben hundert und tausend Kisten (boxes) Glases im
Monate, je nachdem naͤmlich die Arbeit mehr oder minder gut gelingt.
Das Blasen. Fuͤr jeden Topf ist ein Blaͤser
und ein Junge oder Lehrling bestellt. Der Blaͤser faͤngt seine Arbeit
damit an, daß er zuerst das Ende seiner Pfeife durch das Fenster einfuͤhrt,
und dieselbe so lang darin laͤßt, bis sie beinahe rothgluͤhend wird,
worauf er sie in Wasser stoͤßt, wo dann das Oxyd abspringt und eine reine
metallene Oberflaͤche laͤßt. Diese wird in die Glasmasse des Topfes
(the metal) eingetaucht, und, indem sie in derselben
umgedreht wird, bleibt eine gewisse Menge von lezterer an ihr haͤngen. Der
Blaͤser nimmt nun diese Masse heraus, und richtet sie, wenn es nothwendig
ist, mit dem Streicheisen (strike iron) zu, worauf sie
wieder in den Topf gebracht wird, bis endlich durch wiederholtes Eintauchen eine
hinlaͤngliche Menge zur Bildung eines Cylinders daran haͤngen bleibt,
wozu, nach der Glashuͤttensprache (der Amerikaner), drei Sammlungen (three gatherings) nothwendig sind. Der Arbeiter bringt nun die Glaskugel
in eine geringe Entfernung von dem Fenster im Ofen, und dreht sie daselbst einige
Augenblike lang ununterbrochen um, damit sie die gehoͤrige Temperatur
bekommt. Hierauf nimmt er sie heraus, und streicht mit dem Streicheisen die
halbfluͤssige Masse nahe an das Ende der Pfeife, die er dann in einen hohlen
Untersaz, einen ausgehoͤhlten hoͤlzernen Blok, bringt, in welchem sich
etwas Wasser befindet: in dieser Hoͤhlung dreht er sie einige Augenblike, um
der Masse die gehoͤrige Form zu geben. Nun fuͤhrt er das
Mundstuͤk der Pfeife an die Lippen, blaͤst nach und nach den Ballen
(die Blase) auf und faͤhrt dabei immer mit dem Umschwenken fort, bis dieser
die gehoͤrige Groͤße erreicht hat. Auf diese Weise bildet sich eine
hohle Kugel an dem oberen Ende der Blase. Diese Kugel fuͤhrt der Arbeiter
durch das Fenster neuerdings in den Ofen, um ihr daselbst wieder die
gehoͤrige Hize zu geben, die sie bei der vorigen Arbeit verloren hat, nimmt
sie dann wieder aus dem Feuer und sezt das Mundstuͤk neuerdings an die
Lippen, und schwingt, auf einer Bank stehend, die Pfeife von einer Seite zur
anderen, dreht sie im Kreise, und blaͤst die Kugel auf. Waͤhrend dieß
geschieht, wird durch die Centrifugalkraft, unterstuͤzt und berichtigt durch
die Gravitation noch waͤhrend des Aufblasens, die Kugel in einen hohlen
Cylinder (die Tute) verwandelt, der mit einem Ende an der
Pfeife haͤngt, und an dem anderen Ende von einer hohlen Halbkugel geschlossen
wird. Der Cylinder wird nun nahe an das Fenster gehalten, so daß er an seinen
aͤußersten Enden erweicht wird; man schlaͤgt ferner ein Loch durch den
Mittelpunkt desselben und schwenkt ihn schnell im Kreise, wo dann durch die
Centrifugalkraft, die auf die erweichte Hemisphaͤre wirkt, dieselbe Anfangs
in eine Flaͤche, die quer uͤber die Waͤnde des Cylinders
laͤuft und senkrecht auf dieselben steht, verwandelt, und endlich, so wie die
Umdrehung fortgesezt wird und die Oeffnung im Mittelpunkte sich erweitert,
ploͤzlich in die Weite der uͤbrigen Theile des Cylinders ausgedehnt
wird. Man haͤlt nun den Cylinder einige Augenblike uͤber senkrecht,
bis das Glas ganz abkuͤhlt, wo er dann dem Jungen uͤbergeben wird,
welcher denselben auf einer hoͤlzernen Unterlage von der Pfeife absprengt,
indem er den Hals mit einem nassen Eisen beruͤhrt. Noch ist eine andere
Arbeit nothwendig, um den Cylinder ganz zu vollenden, die man das Kaͤppeln (cappling)
nennt. Man nimmt zu diesem Ende etwas fluͤssige Glasmasse mit einer eisernen
Stange aus dem Topfe, und bringt sie mittelst Zangen rings um jenes Ende des
Cylinders, welches an der Pfeife hing. Dieser gluͤhende Glasfaden sprengt,
wenn er mit dem bereits erkalteten und noch nicht im Kuͤhlofen behandelten
Glase in Beruͤhrung kommt, die Kappe weg, und laͤßt einen reinen Cylinder
zuruͤk. Um nun den Cylinder zum Streken (flattening) herzurichten, wird ein gluͤhendes
Eisen von einem Ende des Cylinders zu dem anderen gefuͤhrt, wo dann, wenn man
dasselbe zuruͤkzieht, und mit einem nassen Finger uͤber die Stelle
faͤhrt, uͤber welche man das Gluͤheisen gezogen hat, der
Cylinder beinahe der ganzen Laͤnge nach in einer geraden Linie springt,
worauf er zum Streken aufbewahrt wird.
Das Streken. Bei dieser Arbeit sind zwei
Gegenstaͤnde zu bezweken: erstens, die Verwandlung der Cylinder oder Tuten in
Flaͤchen; zweitens das Abkuͤhlen (Anlassen, annealing tempering) des Glases. Der hierzu noͤthige Bau besteht
aus drei Theilen: A dem Hintertheile oder Eingange in
den Strekofen. B dem eigentlichen Strekofen und C dem Kuͤhlofen. Diese Oefen werden dadurch zu
dieser Arbeit hergerichtet, daß man die Temperatur des Kuͤhlofens auf
ungefaͤhr 500° F. (212° R.) mittelst des Zuges, a, erhoͤht, welcher mit einem darunter
angebrachten Herde und Roste in Verbindung steht. Der Ofen B wird bis zur Gluͤhhize gebracht, was durch den Zug b geschieht, waͤhrend das Hintertheil, welches
mit diesem Ofen in Verbindung steht, seine Hize durch denselben erhaͤlt,
welche jedoch, da das Gewoͤlbe, das denselben dekt, viel niedriger ist, als
das Gewoͤlbe des Ofens, immer nach und nach abnimmt, so daß sie am Eingange
dieses Hintertheiles niedriger ist als die Hize des siedenden Wassers. Da nun die
Tuten oder Cylinder noch nicht abgekuͤhlt oder angelassen wurden, so wird es,
wenn sie nicht brechen sollen, unerlaͤßlich, die Hize mit der groͤßten
Vorsicht an denselben anzubringen. Dieß wird nun durch die Anlage dieses
Hintertheiles leicht moͤglich. Innerhalb desselben sind naͤmlich auf
dessen Sohle zwei eiserne Stangen angebracht, die der ganzen Laͤnge nach
(gewoͤhnlich 10 Fuß lang) hinlaufen. Wenn nun diese Oefen auf die
gehoͤrige Hize gebracht sind, wird eine eiserne Platte uͤber den Zug,
a, gelegt, welche denselben gaͤnzlich
schließt: man wirft einige Spreißel Holz in den Ofen, um denselben in der Hize zu
halten, und den Arbeitern zu leuchten. Ein Junge muß nun die Tuten (Cylinder)
herbeitragen, und sie auf die eisernen Stangen in dem Hintertheile legen, auf
welchem er sie mittelst eines Stabes nach und nach vorwaͤrts schiebt, bis
dieses ganze Hintertheil voll ist. Ein Mann, der bei der Oeffnung, D, aufgestellt ist, bringt nun mittelst einer eisernen
Stange die Tute, welche zuerst in das Hintertheil eingebracht wurde, auf den Stein
E, dessen Temperatur so hoch steht, daß, da das Glas
biegsam ist, die Tute sich auf demselben flach ausbreitet. Man fuͤhrt jezt
einen hoͤlzernen Blok, der an einer eisernen Stange angebracht ist,
uͤber diese Glasplatte, und druͤkt dieselbe fest auf dem Steine an.
Nachdem dieß geschehen ist, schiebt dieser Arbeiter die Platte mittelst eines anderen Eisens,
das man den Schieber (the cropper) nennt, unter der
Scheidewand der Oefen durch auf den Stein F. Auf diesem
Steine laͤßt man sie liegen, bis sie kuͤhl genug geworden ist, um ihre
Form behalten zu koͤnnen. Ein anderer, bei G
angestellter, Arbeiter zieht sie dann an das Hintertheil des Ofens, wo er sie
beinahe senkrecht auf ihre Kante stellt.
Jede Tute geht nach und nach durch alle diese verschiedenen Manipulationen durch, bis
zulezt alle zusammen in den Kuͤhlofen uͤbertragen werden. Wenn dieser
voll geworden ist, laͤßt man das Feuer ausgehen, und verstreicht jede
Oeffnung des Ofens mit Moͤrtel. Im Winter laͤßt man die Glastafeln
eine Woche lang in dieser Lage, im Sommer zehn Tage: nach Verlauf dieser Zeit wird
der Ofen geoͤffnet, und nachdem das Glas kuͤhl genug geworden ist, um
es ohne Nachtheil herausnehmen zu koͤnnen, wird es herausgenommen und in die
Schneidstube gebracht, in welcher es nach und nach bis zur Temperatur der
Atmosphaͤre, abkuͤhlt.
In der ganzen Glasmachern ist vielleicht nichts, was dem Zuschauer so viel
Vergnuͤgen gewaͤhrt und so viel Erstaunen abzuloken vermag, als die
Leichtigkeit, mit welcher ein erfahrner Glasschneider seine Arbeit verrichtet.
Wirklich fordert auch keine bloße Handarbeit in irgend einem Gewerbe mehr Zeit und
Geduld, um die erforderliche Geschiklichkeit zu erlangen, als gerade diese. Man hat
allerlei verschiedene Meinungen uͤber die Art aufgestellt, nach welcher der
Demant bei dem Zerschneiden des Glases wirkt. Wenn der Demant quer uͤber eine
Glastafel hingezogen wird, und einen guten Schnitt bildet, so ist die Linie, die er
gezogen hat, kaum merklich, und der Bruch erstrekt sich doch durch die ganze Dike
der Tafel. Der Glasschneider beurtheilt das Gelingen seines Schnittes mehr mit dem
Ohre, als mit dem Auge. Wenn der Schnitt gut geraͤth, so entsteht ein eigener
knarrender Laut. Wenn hingegen eine weiße Linie unter einem knirschenden Laute zum
Vorscheine kommt, kann man sicher seyn, daß die Tafel nicht durchgeschnitten ist. Es
scheint beinahe in dem lezteren Falle, daß der Bruch, Statt von der Spize des
Demantes senkrecht abwaͤrts zu steigen, sich seitwaͤrts erstrekt, und
von da wieder nach der Oberflaͤche zuruͤkkehrt, und auf diese Weise
kleine Glasstuͤke losreißt, die muschelfoͤrmig sind. Ich waͤhle
zum Glasschneiden immer vollkommen ganze Demante, mit dreiekig rhomboidalen
Flaͤchen (triangular rhomboidal faces), deren
Kanten nicht gerade, sondern etwas convex sind, sie moͤgen uͤbrigens
Oktaëder oder Dodekaëder seyn. Die ganz eigene Feinheit, die die Kante
des Demantes haben muß, wenn sie gut schneiden soll, wird durch anhaltenden Gebrauch
derselben, ungeachtet aller Haͤrte des Demantes, doch sehr bald
abgenuͤzt, und
das Auge haͤlt oft noch eine Demantkante fuͤr scharf, die es nicht
mehr ist.
Das gewoͤhnliche Tafel- oder Cylinderglas steht weit unter dem
Kronenglase. Einige Maͤngel desselben haͤngen nothwendig von der
Verfahrungsweise bei seiner Verfertigung ab, und lassen sich nimmermehr
gaͤnzlich verhuͤten. Andere Fehler hingegen lassen sich durch Fleiß
und Geschiklichkeit gaͤnzlich beseitigen.
Der geringere Glanz oder die geringere Politur, die unregelmaͤßige
Zuruͤkwerfung des Lichtes von der Oberflaͤche desselben, die leichten
Krazer und Rize, die man mehr oder minder an allen diesen Arten von Glas wahrnimmt,
gehoͤren zu den unvermeidlichen Nebeln; viele derselben koͤnnen jedoch
durch aufmerksame und sorgfaͤltige Behandlung dieses Glases in einem hohen
Grade vermindert werden.
Der geringere Glanz ruͤhrt vorzuͤglich davon her, daß das Glas bei dem
Streken noch ein Mal gehizt werden muß. Wenn die Temperatur nicht hoͤher
getrieben werden duͤrfte, als bloß nothwendig ist, um das Glas biegsam zu
machen; so wuͤrde die Verminderung des Glanzes so unbedeutend seyn, daß man
sie kaum wahrnehmen koͤnnte; da aber eine groͤßere Hize die Arbeit des
Strekens sehr erleichtert, so gerathen die Arbeiter immer in Versuchung, eine
staͤrkere Hize anzuwenden. Es ist wahrscheinlich, daß diese große Hize das
Alkali von der Oberflaͤche des Glases, welche mit derselben in unmittelbare
Beruͤhrung kommt, verfluͤchtigt, und daß die Kieselerde, die hierdurch
ihres Aufloͤsungsmittels beraubt wird, die Ursache dieser Truͤbheit
des Glases wird. Dieselbe Wirkung hat, bekanntlich, auch Statt, wenn eine
Fensterscheibe lang den Einfluͤssen der Witterung ausgesezt gewesen ist, und
zeigt sich ganz besonders deutlich an Glasstuͤken, die Monate lang in den
Strekoͤfen lagen: sie werden so matt und undurchsichtig, daß sie
Porzellanscherben aͤhnlich werden.
Das unvollkommene Zuruͤkwerfen der Lichtstrahlen ruͤhrt von der
Unmoͤglichkeit her, eine Glasplatte in vollkommen gleiche Beruͤhrung
mit dem Steine zu bringen, indem immer Luft und Staub zwischen beiden vorhanden ist.
So wie heute zu Tage die Strekofen gebaut sind, wird auch die hoͤchste
Sorgfalt diesen Fehler nicht gaͤnzlich vermeiden koͤnnen.
Die leichten Rize und Krazer entstehen durch das Schieben der Glasplatte von einem
Steine auf den anderen. Diese Fehler koͤnnten auf folgende Weise vermieden
werden. Man verfertigt eine sehr dike (1/4 bis 1/3 Zoll dike) Glastafel, legt diese
auf den Stein, und die Tute oder den Cylinder auf sie, und laͤßt jenen auf
dieser sich streken. Beide Platten werden dann zugleich auf den anderen Stein
hinabgeschoben, die obere Glasplatte wird von der unteren weggenommen, und die untere dike, die man den
Lieger (legger) heißt,
wird wieder auf den vorigen Strekstein zuruͤkgeschoben. Alles sogenannte
falsche Kronen, glas (imitation crown) wird auf diese
Weise gestrekt, und wenn dieses Glas sorgfaͤltig nach obiger Art behandelt
wurde, kommt es beinahe dem Kronenglase der Qualitaͤt nach gleich, und hat
zugleich noch den wichtigen Vorzug, daß es diker ist.
So unvollkommen indessen das Cylinder- oder Tafelglas auch gewoͤhnlich
seyn mag, so ist es doch bei seinem geringen Preise (es ist um die Haͤlfte
wohlfeiler als Kronenglas) eines ungeheueren Absazes sicher, vorzuͤglich in
jenen Gegenden unseres Landes, wo die Einwohner mit ihrem Landgute bereits ins Reine
gekommen sind, und ihre alte Residenz, die Huͤtte aus unbehauenen
Baumstaͤmmen, mit bequemeren und eleganteren Wohnungen zu vertauschen
beginnen. Im Staate von New-York sind gegenwaͤrtig bereits nicht
weniger als acht Glashuͤtten, welche Tafel- oder Cylinderglas
verfertigen, und jaͤhrlich zwischen 60 und 80,000 Kisten Glas zu Markte
bringen. Die Concurrenz der Glashuͤtten ist in dem gegenwaͤrtigen
Augenblike bereits so groß in unserem Lande, daß der Preis des Tafelglases
gegenwaͤrtig bei uns um volle zwei Drittel niedriger steht, als er vor
zwoͤlf Jahren gestanden ist.Die Freunde der freien Einfuhr behaupten immer, daß, wo Einfuhr fremder
Waaren verboten ist, die Fabrikate wegen des Monopoles, das die Fabrikanten
hierdurch erhalten, im Preise steigen und in der Guͤte sinken.
Nordamerika liefert uns neuerdings den Beweis, den zuerst England, dann
Oesterreich und Preußen, endlich Frankreich und zulezt Nußland durch seine
Einfuhrverbote vor Jahrhunderten und Jahrzehenden geliefert haben:
„daß Einfuhrverbote den Preis der Fabrikate nicht nur nicht
vertheuern, sondern maͤchtig verringern, sobald die Fabriken
keine Privilegien besizen;“ daß also obige Einwendung gegen
Einfuhrverbot nichts anderes, als eine gelehrte Professorsgrille ist. Die
gelehrten Herren, die sich fuͤrchten, die paar Lappen, mit welchen
sie ihre Nuditaͤt à priori und à posteriori zu bedeken gezwungen sind,
theuerer bezahlen zu muͤssen, wenn diese Lappen nicht mehr aus dem
Auslande eingefuͤhrt werden duͤrfen, belieben nur, wenn es
ihnen gefaͤllt, eine Tinten- und Papier-Fabrik zu
errichten, und sie werden bald sehen, daß ein Hr. Collega sich
bemuͤhen wird, ihre Lumpenware noch wohlfeiler und noch
schoͤner zu liefern. Es ist heute zu Tage in der ganzen Welt so
eingerichtet, daß dort, wo Ein Fabrikant reich werden koͤnnte, ein
halbes Duzend Fabrikanten desselben Artikels sich, so bruͤderlich in
diese vermeinten Reichthuͤmer theilen, daß allen nichts anderes
uͤbrig bleibt als Gottes Segen: „im Schweiße deines
Angesichtes sollst du dein Brot verdienen.“ U. d. Ue. Tafelglas hat gegenwaͤrtig bei uns gerade den Preis des Einfuhrzolles
auf auslaͤndisches Glas, so daß folglich das auslaͤndische Glas von
unseren Maͤrkten gaͤnzlich ausgeschlossen ist. So viel ich weiß, ist
bis jezt nur eine einzige Glashuͤtte in unserem Lande, die Kronenglas
verfertigt, und diese ist zu oder bei Boston. Sie hat bisher mit Vortheil, wie ich
hoͤre, gearbeitet, obschon ihr das Brennmaterial vier Mal hoͤher zu
stehen kommt, als es an vielen anderen Oertern bei uns nicht der Fall ist. Bei dem
Unternehmungsgeiste, der Nationalgeist bei uns geworden ist, bei den einladenden Verhaͤltnissen
unserer gegenwaͤrtigen Lage und den vielen Localvortheilen, die wir auf eine
auffallende Weise vor anderen voraus haben, bleibt es wahrhaftig ein
Raͤthsel, zu erklaͤren, wie wir vergessen konnten unsere Capitalien
auf einen so eintraͤglichen Erwerbszweig zu verwenden. Es ist sehr zu
wuͤnschen, daß wir in Hinsicht auf einen eben so schoͤnen als
nothwendigen Artikel nicht laͤnger mehr vom Anstande abhaͤngen.Bayerische Glashuͤttenmeister, die bekanntlich sehr schoͤnes
Kronenglas verfertigen, duͤrften diesemnach in Nordamerika ihr
Gluͤk machen. A. d. R.
Tafeln
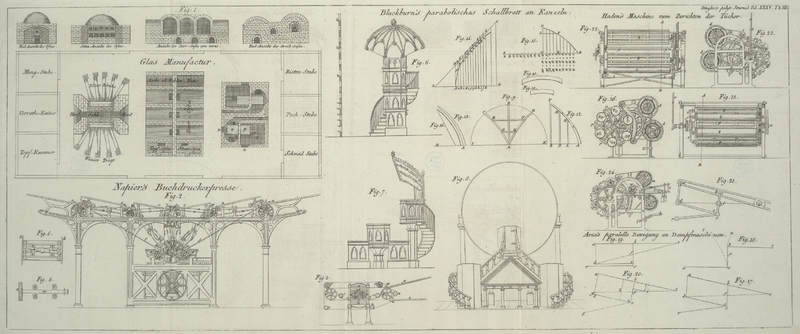