Titel: | Verarbeitung des in Yorkshire fabricirten Cementstahls. Fabrication des Gußstahles. |
Fundstelle: | Band 92, Jahrgang 1844, Nr. VIII., S. 19 |
Download: | XML |
VIII.
Verarbeitung des in Yorkshire fabricirten
Cementstahls. Fabrication des Gußstahles.Dieser Aufsaz bildet eine Fortsezung des im vorhergehenden Heft des
polytechnischen Journal Bd. XCI S. 443
enthaltenen Aufsazes.
Aus den Annales des Mines, Tom. III. 3. Lief. 1843,
durch Heßler's Jahrbuch
fuͤr Technik, Physik und Chemie Febr. 1844 S.
101.
Mit Abbildungen auf Tab.
II.
Verarbeitung des Cementstahls.
Die Operationen, denen der rohe Cementstahl unterworfen wird, haben zum Zwek, ihn
durch mehrmaliges Hizen und Ausschmieden in mehr oder weniger raffinirte oder
gegerbte Stäbe für den Handel zu verwandeln, welche dann in den zahlreichen
Werkstätten, wo man Feilen, Raspeln, Sägeblätter, Sicheln, Sensen, Bleche, Drähte,
Schneidewerkzeuge, Waffen u.s.w. verfertigt, zu diesen Gegenständen verarbeitet
werden. In manchen Fällen begreifen die Hütten, worin der Stahl im Großen gegerbt
wird, zugleich auch die Werkstätte in sich, worin er seine definitive Form erhält;
in andern Fällen gerben sich die Fabrikanten oben aufgezählter stählerner Geräthe
und Gegenstände selbst den Stahl in kleinen Feuern, wo sie ihn nachher auch
verarbeiten. Am gewöhnlichsten aber werden diese zwei Industriezweige abgesondert in
den Händen verschiedener Industrieller gefunden. Das Gerben geschieht in größeren
Etablissements, denen kräftige, durch Wasserräder oder Dampfmaschinen getriebene
Maschinen zu Gebote stehen, während die Verarbeitung des Stahles in kleinen
zerstreut liegenden Werkstätten geschieht, deren in Sheffield über 2000 vorhanden
sind.
Präparirung des Stahls. – Die einfachste der
Operationen, die mit dem rohen Cementstahl vorgenommen werden, besteht darin, daß
man die rohen Stangen ein einzigesmal hizt und hierauf mehrmals durch die Canelüren
(Einschnitte) eines Walzwerkes gehen läßt, damit die bei der Cementation
entstandenen Risse wieder zusammenschweißen. Das Hizen geschieht in einem Flammofen
mit Steinkohlen und
man trägt die rohen Stahlstäbe erst ein, nachdem der Ofen in starke Hize gekommen
und der Herd mit glühenden, schon vor einer gewissen Zeit einzutragenden Steinkohlen
angefüllt ist, so daß diese schon allen Schwefel, den sie enthielten, verloren
haben. Diese Präparirung oder Zurichtung des rohen Stahles fordert nur geringen
Aufwand an Brennstoff und Handarbeit; die hiebei erforderliche Hize ist viel
niedriger, als die zum Gerben nöthige, und der Abgang beträgt kaum 3 Proc.
Die so präparirten Stäbe passiren nun oft ein Schneidewerk, und die daraus
hervorgehenden schmäleren Stäbe dienen dann zur Fabrikation wohlfeiler Objecte,
welche zum großen Theil aus Schmiedeisen bestehen, und woran nur Theile, wie bei den
Schneidwerkzeugen und Meißeln nur die Schneide, aus Stahl bestehen. Auch für
Wagen- (Kutschen-) Federn wird der Stahl in angegebener Weise
präparirt.
Apparate zur Bearbeitung des Stahles. – Bei
Präparirung des Stahles, damit er in seiner Masse homogen werde und zur Fabrication
der Objecte mittlerer und höherer Qualität diene, wird bis auf einige secundäre
Modificationen ganz in gleicher Weise verfahren, wie in den Stahlhütten am Rhein
beim Reken oder Gerben des dort aus Spatheisenstein erzeugten Schmelz- oder
Rohstahls mittelst der Steinkohle des Ruhr- oder Saarbrukbassins. Ich habe,
selbst was die Einrichtung der Feuer und Hämmer anbelangt, in mehreren Hütten
Yorkshire's Details angetroffen, die noch deutlich an die von der englischen
Industrie nachgeahmten Vorbilder erinnern. Gehizt wird der Stahl gewöhnlich in
Schmiedessen ähnlichen Feuern oder Herden durch Steinkohlenklein aus sehr bakenden
Kohlen, und der Herd ist so eingerichtet, daß das zu hizende Stük immer von einer
Art Gewölbe aus glühenden Kohlen bedekt ist, ohne jedoch damit in Berührung zu
stehen. Manchmal hat man auch Feuer, die mit Kohks betrieben werden und mit einem
kleinen Gewölbe aus Baksteinen bedekt sind; das zu hizende Stük befindet sich dann
zwischen den Kohks und dem Gewölbe. Bis auf die Dimensionen hat dieser kleine Ofen
die nämliche Einrichtung, wie die Oefen, deren man sich in der englischen Provinz
Wallis zur Ausarbeitung der für die Weißblechfabrication bestimmten Stürze bedient.
Das Reken geschieht mittelst Schwanzhämmer von geringer Hubhöhe, welche, während sie
beim Reken und Schmieden roher Stangen eine nur mäßige Geschwindigkeit haben, oft
mehr als 300 Schläge in der Minute machen, wenn sie auf schon einmal unter dem
Hammer gewesene Stangen wirken. Die Hämmer werden in Yorkshire theils durch
Wassertheils durch Dampfkraft betrieben.
Der einfach ausgerekte Stahl wird durch zwei aufeinander folgende Operationen präparirt. Bei der
ersten Operation, Schwizen (ressuage) genannt, werden
die von der Cementation gekommenen rohen Barren einzeln gehizt und erhalten dann
unter dem Schwanzhammer eine beiläufig vierekige Gestalt, ohne daß jedoch ihr
Querschnitt beträchtlich verkleinert wird; bei der zweiten Operation gibt man der
Stange weiße Schweißhize und strekt sie zu den verschiedenen im Handel geforderten
Dimensionen aus. Dieser Stahl ist wenig homogen, unganz und taugt nur zur
Fabrication von Objecten mittlerer Qualität.
Der einmal gegerbte Stahl wird gleichfalls durch zwei
Operationen erzeugt. Bei der ersten, das Schweißen genannt, erhält ein Pak (Zange)
aus mehreren Stüken rohen Cementstahls weiße Schweißhize und wird nachher mit
Vorsicht der Wirkung des Schwanzhammers ausgesezt, so daß alle Stüke
zusammenschweißen. Um dieses Zusammenschweißen leichter und schneller zu
bewerkstelligen, legt man manchmal über und unter den rohen Stahl Stangen, welche
schon die vorerwähnte Operation des Schwizens überstanden haben. Die
zusammengeschweißte Zange wird dann ins Feuer zurükgebracht und zu den
erforderlichen Dimensionen ausgeschmiedet.
Der zweimal gegerbte Stahl wird ganz durch die nämlichen
Operationen wie die vorhergehende Sorte dargestellt, nur mit dem Unterschiede, daß
hier schon einmal gegerbte Stangen in Arbeit genommen und zu 12–18 zu einer
Zange vereinigt werden.
Endlich erzeugt man zum Behufe der Fabrication gewisser Objecte vorzüglicher Qualität
auch dreimal gegerbten Stahl.
Alle diese Arten, den rohen Stahl auszuarbeiten, haben theilweise den Zwek, dem Stahl
die Form und jene Grade von Homogeneität und Hämmerbarkeit zu geben, welche die
verschiedenen Stahlarbeiter fordern und die der rohe Cementstahl durchaus nicht
besizt. Indessen muß bemerkt werden, daß dieser Zwek nur unvollkommen erreicht wird,
und daß der rohe Cementstahl dem Reken und Gerben sich viel weniger fügt als der
Schmelzstahl. Das Schweißen erfordert mehr Zeit und Brennstoff und somit
beträchtlichere Kosten.
Wenn der Cementstahl nicht aus Eisen guter Auswahl bereitet worden, so verliert er in
den zahlreichen Hizen, denen er unterworfen wird, sehr schnell seine
Stahleigenschaften, und endlich liegt die Hauptursache der geringeren Tauglichkeit
des Cementstahles darin, daß die Operation des Gerbens die durch die Cementation
erzeugte Mangelhaftigkeit der Continuität in der Masse oder das Unganzseyn derselben
nicht vollständig behebt. Bei den Manipulationen, die ich kurz vorher beschrieben
habe, läuft man demnach Gefahr, dem Stahl seine übrigen, ihn charakterisirenden
Eigenschaften in dem Maaße zu nehmen, als man seine Homogeneität erhöht, und ein Product
zu erzeugen, welches von den Fabrikanten, die es verarbeiten sollen, zurükgewiesen
wird. Diese Umstände und die beträchtlichen Kosten, die das Gerben verursacht,
erklären ganz gut, warum die Fabrikanten in Yorkshire nach und nach vermocht wurden,
so hohe Preise für die ersten Marken oder Zeichen schwedischen Stahls zu zahlen,
welche ihnen nebst andern Vortheilen auch noch in der zweifachen oben berührten
Rüksicht völlige Sicherheit bieten. Man begreift ferner in gleicher Weise, warum die
englischen Stahlhütten auf dem Wege des Cementirens und Gerbens nicht allen Stahl
vorzüglicher Sorte erzeugen konnten, dessen die Fabriken der verschiedenen
Stahlobjecte bedurften, und warum diese Fabriken noch während der ganzen Dauer des
18ten Jahrhunderts ihren Bedarf mit Schmelzstahl des Continents completiren mußten.
Es würden in der That die Cementstahlhütten in Europa noch eine nur secundäre Rolle
spielen, wenn nicht das Genie eines simpeln Arbeiters, durch das dringende Bedürfniß
angetrieben, die neue Kunst geschaffen hätte, dem Cementstahl neben den andern
Stahleigenschaften auch Homogeneität in der Masse und Gleichförmigkeit in der Textur
zu geben, so daß er Producte liefert, die in ihren Qualitäten wenigstens auf
gleicher Stufe mit jenen des besten Schmelzstahls stehen. Und diese Kunst sicherte
den mit unbegränzten Fabricationsmitteln versehenen Cementstahlfabriken Englands den
unbestreitbaren Vorrang. Sie hat die Fabrication des Gußstahls zum Gegenstand, führte in Yorkshire bereits eine sehr wichtige
Abtheilung der Stahlarbeit herbei und ist sicherlich berufen auch auf dem Continent
eine wichtige Rolle zu spielen; sie ist aber noch Geheimniß einer geringen Zahl von
Fabriken.
Ich glaube daher der Wissenschaft einen Dienst zu erweisen, indem ich die Resultate
meiner Untersuchungen über die Vergangenheit, die Gegenwart und wahrscheinliche
Zukunft dieses interessanten Zweiges der Metallurgie hiemit mittheile.
Geschichtliches über die Erfindung des Gußstahls.
– Benjamin Huntsmann, geboren in Yorkshire 1704,
widmete sich in der kleinen Stadt Doncaster der Uhrmacherei und machte daselbst
Versuche, aus Cementstahl die für seine Kunst nöthigen Werkzeuge und verschiedene
andere Objecte zu verfertigen. In Folge des guten Erfolges seiner Versuche
errichtete er 1740 zu Handsworth, einer nächst Sheffield mitten unter den reichsten
Kohlengruben gelegenen Stadt, das erste Atelier, wo Gußstahl in regelmäßiger Art
fabricirt wurde und welches er in der Folge nach Attercliff übertrug, wo noch
heutigen Tags seine unmittelbaren Descendenten den nämlichen Industriezweig ausüben.
Er starb 1776. Bald ergriffen auch noch andere Fabrikanten und darunter vorzüglich Walker und J. Marshall diesen
Fabrikationszweig und gründeten zwei Gießereien in Sheffield und Greenoside. Es
entwikelte sich aber diese neue Fabrication nur langsam, und das ganze vorige
Jahrhundert hindurch hatten die Fabrikanten mit den Schwierigkeiten, welche die
erforderliche sehr hohe Temperatur verursachte und mit den Vorurtheilen der
Consumenten zu kämpfen, die gewohnt waren, die bessern Stahlsorten aus Deutschland
zu beziehen. Nach und nach wurden aber die technischen Schwierigkeiten überwunden,
man lernte ganz entsprechende feuerfeste Baumaterialien bereiten, die anfangs
überaus großen Fabricationskosten verminderten sich mit jedem Jahr, die Fabrikanten
stählerner Werkzeuge und anderer Objecte bequemten sich endlich, durch die
Wohlfeilheit des Gußstahls angeeifert, zu dessen Anwendung in allen Fällen, wo sie
sonst deutschen Stahl verarbeiteten, und entdekten sogar bald, daß er vor diesem
noch mehrere nüzliche Eigenschaften voraus habe.
Einfluß der Entdekung des Gußstahls auf die
Cementstahlfabrication. – Heutzutage ist die Umstaltung, welche die
Huntsmann'sche Entdekung in der Stahlfabrication
Großbritanniens hervorbrachte, ganz und gar vollendet und mit jedem Tag werden dem
Continent die Folgen hievon fühlbarer. Seit lange wird kein deutscher Stahl mehr in
England eingeführt, die Hütten von Yorkshire führen im Gegentheil jährlich
30,000–40,000 metrische Cntr. Gerbe- und Gußstahl in Stäben, Drähten
und Blechen aus. In Yorkshire bestanden, wie ich ermittelte, 51 Gußstahlhütten, in
welchen, ungeachtet der Handelsstokungen, wöchentlich 1615 metr. Cntr. rohen
Cementstahls (85,800 metr. Cntr. im Jahr) in Gußstahl umgewandelt werden. Dieses
Quantum macht ungefähr 52/100 der ganzen Production der Cementstahlhütten aus.
Gegenwärtiger Zustand der Kunst, Gußstahl zu fabriciren.
– Alle Hütten beobachten, bis auf einige wenige Nuancen, die in folgendem
beschriebene Methode.
Schmelzofen. – Es ist dieß ein Tiegelofen mit
natürlichem Luftzug, der in jeder seiner Abtheilungen (Oefen) zwei Schmelztiegel,
worin der Stahl, gegen die Verbrennungsgase geschüzt, erhizt wird, aufnimmt und
welcher in Fig.
24 und 25 dargestellt ist. Die den Figuren eingeschriebenen Zahlen bedeuten die
Dimensionen in Centimetern. Jeder Ofen (I, I) ist ein
gerades rechtekiges Prisma, dessen horizontaler Durchschnitt 54 Centimeter (1,7 Fuß)
lang und 38 Cent. (1,2 Fuß) breit ist. Im Untertheil hat er einen aus fünf
vierekigen Stäben, deren jede Seite zwischen 25 Millim. (11,25 Linien) und 35
Millim. (1,57 Linien) varirt, bestehenden Rost. Im Obertheil befindet sich eine rechtekige
Oeffnung (a, Fig. 25), die nur 33
Cent. (1,03 Fuß) lang und 30 Cent. (0,94 Fuß) breit ist, deren Mittelpunkt der Figur
mit der Mitte des Prisma zusammenfällt und welche zwischen, von den Seitenwänden des
Prisma ausgehenden kleinen Klosterbögen gebildet (belassen) ist. Der verticale
Abstand des Rostes von dieser Oeffnung beträgt 91 Cent. (2,85 Fuß). Drei Seitenwände
des Prisma verlängern sich 1,71 Met. (5,39 Fuß) unter den Rost hinab und die vierte
Seite (unterhalb des Rostes) bleibt offen, damit die zur gehörig lebhaften
Verbrennung erforderliche große Luftmenge zukann. Oben an einer der geraden
Seitenwände des Prisma ist eine 38 Cent. (1,2 Fuß) breite und 14 Cent. (5 1/12 Zoll)
hohe Oeffnung (Fig.
25) angebracht, durch welche die Verbrennungsgase in den horizontalen, 64
Cent. (2,02 Fuß) langen Canal von gleichem Durchschnitt mit der oben besagten
Oeffnung und aus diesem in die verticale Esse abziehen.
Die obere Wand (Deke) des horizontalen Canals ist an der Ofenmündung 11 Cent. (4 1/12
Zoll) dik und der horizontale Durchschnitt der Esse ist manchmal ein Kreis,
gewöhnlicher aber ein Quadrat von 30 Cent. (11 5/12 Zoll) Seite. Die ganze Höhe der
Esse über die Deke des horizontalen Canals beträgt 10,11 Met. (31,94 Fuß).
Selbst die feuerfestesten Ziegel würden der außerordentlich hohen Temperatur der
Stahlschmelzöfen nicht widerstehen können. Man bildet demnach die Wände dieser Oefen
aus einem sehr dichten, im Bruche feinkörnigen und aus reinem Quarz gebildeten,
daher ausgezeichnet feuerbeständigen Sandstein, Gannister
genannt. Da dieser Sandstein, seiner Härte wegen, mit Vortheil zum Aufschütten der
meisten in der Nähe befindlichen Straßen verwendet wird, so sammelt man sorgfältig
den Staub und Koth dieser Straßen, und diese pulverige Masse, welche im Wesentlichen
aus Quarz besteht, der mit einer Spur thierischer Materie und mit jenem feinen
Kohlenpulver gemengt vorkömmt, womit der Boden aller Fabriksdistricte
Großbritanniens imprägnirt ist, ist eben so feuerbeständig wie der Sandstein selbst
und gestattet eine wohlfeilere Anwendung, weil die bei Anwendung des Steines zum
Zuhauen nöthige Handarbeit wegfällt. Um die Ofenwände nach Entfernung der
beschädigten Partien wieder in guten Zustand herzustellen, braucht man nur das
besagte pulverige feuerfeste Material etwas zu befeuchten und damit den 28 Cent.
(10,5 Zoll) breiten Raum auszufüllen, der zwischen dem festen Mauerwerk und einem
centralen Kern von Holz enthalten ist, dem man genau die Gestalt und Stellung des
Herdes gibt. Wo dieses pulverige Material nicht in guter Qualität vorhanden ist, muß
der besagte Sandstein angewendet werden, und in diesem Falle werden die Wände, welche mit dem
Brennstoff in Berührung sind, in einer Dike von 11 Cent. (4,1 Zoll) aus entsprechend
zugehauenen und durch etwas Lehm vereinigten Sandsteinen gebildet. Der dann zwischen
dieser Sandsteinwand und dem fixen Mauerwerk noch frei bleibende Raum (Fig. 25) von
17 Cent. (6,4 Zoll) Dike wird mit befeuchtetem Straßenstaub mittlerer Beschaffenheit
ausgefüllt. In der abgebildeten Schmelzhütte, die ich als Muster dieser Hütten in
Yorkshire aufstellen kann, sind alle Oefen auf zulezt angegebene Weise
hergestellt.
Allgemeine Einrichtung und Dimensionen einer
Schmelzhütte. – Die Einrichtung der Oefen, die niemals einzeln
vorkommen, ist in allen Hütten die nämliche. Die Zahl der nebeneinandergesezten
Oefen ist nie geringer als vier und selten größer als 10. Die Essen sind alle in
einem 1,02 Met. (3,22 Fuß) diken Mauerwerke vereinigt, wo ihre geradlinigen Achsen
in einer und derselben Ebene liegen. Die Achsen je zweier aneinander stoßender Essen
sind 83 Cent. (31,15 Zoll) von einander entfernt. Die oben in jedem Ofen vorhandene
Oeffnung mündet im Boden (der Sohle) der Schmelzhütte, welcher selbst 1,20 Met.
(3,79 Fuß) über dem Niveau des Hofes (Erdreiches) liegt, und in welchen aus der
eigentlichen Schmelzhütte eine Bogentreppe hinabführt. Während des Schmelzprocesses
sind die besagten obern Oeffnungen der Oefen mit Dekeln geschlossen (Fig. 26), welche aus
breiten, mittelst Drukschrauben in einem eisernen Rahmen festgehaltenen Ziegeln
gebildet sind. Die ganze Hütte (Fig. 23) hat in der Regel
die Gestalt eines Rechtekes; die Länge der einen von dem Essengemäuer gebildeten
Seite dieses Rechtekes wird durch die Anzahl der Oefen bestimmt. In einer Hütte mit
zehn Oefen, wie die in Fig. 23 dargestellte,
beträgt diese Länge 8,3 Meter (26,22 Fuß).
Unmittelbar unter dem Hüttenraum befindet sich immer ein eingewölbter Keller (Fig. 25),
dessen Sohle (Grund), die sich im gleichen Niveau mit der Sohle des Aschenraumes der
Oefen befindet, 14,2 Meter (44,87 Fuß) unter dem Boden des Hofes (Erdreich) liegt.
Zu beiden Seite der Schmelzhütte befinden sich zwei kleine Magazine im gleichen
Niveau mit dem Hofe. Das eine dient zur Deponirung der Kohls und des feuerfesten
Thones. Auch werden hier die Schmelztiegel verfertigt. In dem andern Magazin werden
die zur Fabrication nöthigen Rohstoffe und die Fabricationsproducte aufbewahrt; auch
wird hier der rohe Stahl zerschlagen. In dieses leztere Magazin hinein verlängert
sich auch der Boden (die Sohle) der Schmelzhütte zu einem kleinen Ofen hin, worin
die Schmelztiegel zur Rothgluth erhizt werden, bevor man sie in die Schmelzöfen
einsezt. Zwei Treppen
gestatten die Kohls und den Cementstahl aus den Magazinen unmittelbar zu den
Oeffnungen der Schmelzöfen zu bringen. Eine andere Stiege sezt den Keller mit dem
Stahlmagazin in Communication und erleichtert, da sich während des Schmelzens hier
häufig die Arbeiter aufhalten, die Ueberwachung des Rostes, die keinen Augenblik
unterlassen werden darf.
Eine andere Treppe, die unter der Bogen- oder Freitreppe hingeht und zu
welcher ein Fenster führt, trägt dazu bei, daß unter das Gewölbe Luft und Licht
gelangt.
Schmelztiegel. – Die Tiegel, worin der Stahl
geschmolzen wird, machen einen wichtigen Theil des Materials aus, und es bedurfte
einer langen Reihe von Versuchen, bis man die Formen und Dimensionen der Tiegel
fand, bei welchen der geringste Brennstoffverbrauch und der kleinste Abgang an Stahl
stattfindet. Daß diese Fragen heutzutage vollkommen ins Reine gebracht sind, zeigt
die beinahe völlige Gleichförmigkeit und Uebereinstimmung, die man in dieser
Beziehung in allen Hütten findet.
Die Tiegel bestehen im Wesentlichen aus feuerfestem Thone aus der Gegend von
Stourbridge (Worcestershire), welcher in den metallurgischen Werkstätten
Großbritanniens die nämliche Rolle spielt, wie der Thon von Forges im nördlichen
Frankreich und der von Andenne in Belgien. Da jedoch dieses Material, wegen der
beträchtlichen Entfernung aus der es kommt, in Sheffield ziemlich hoch im Preise
ist, so mengt man es gewöhnlich zur Hälfte mit einem Thon geringerer Qualität aus
der Nähe von Sheffield. Man sezt ferner dem Gemenge etwas Kohkspulver und gepulverte
Scherben unbrauchbar gewordener Tiegel zu und bildet aus dem Ganzen einen
gleichartigen und sehr compacten Teig.
Eigenschaften des Thons zu den Schmelztiegeln. –
Nach comparativen Versuchen eines geschikten Fabrikanten in Sheffield, der mir die
erhaltenen Resultate mitzutheilen die Güte hatte, eignet sich der Thon von
Stourbridge besser für die Schmelztiegel, als alle andern Arten feuerfesten Thones
Großbritanniens und des Continents. Er konnte keinen Thon finden, der drei
nacheinanderfolgenden Schmelzungen widerstand, während Tiegel aus Thon von
Stourbridge oft sechs Schmelzungen aushalten. Es schien mir interessant, die Ursache
dieser Superiorität aufzusuchen. Der Thon von Stourbridge wird, an einem trokenen
Orte aufbewahrt, zu einer consistenten Masse, die sich schwer mit der Hand zerdrüken
läßt, selbst schwachen Hammerschlägen widersteht, sich mit dem Nagel rizen läßt, und
mit dem Messer zerschnitten eine gewisse Politur oder Glätte annimmt. Er hat eine
dunkelschwarzbraune Farbe und sein Bruch zeigt auffallend zweierlei Aussehen: gewisse Theile sind
matt und erdig, dabei ziemlich eben und weich anzufühlen, und die andern sind
hingegen glatt, glänzend und erinnern an das Aussehen der glänzenden Flächen, welche
gewisse braune, warzige Rotheisensteine zeigen. Er läßt sich im Mörser sehr leicht
pulverisiren und besteht, wenn man ihn nachher durch ein Seidensieb passirt,
großentheils aus beinahe unfühlbaren Partikelchen. Seine Masse ist vollkommen
homogen, denn wenn man sie wäscht und die zurükgebliebenen Fragmente dann in einem
Porphyrmörser zerreibt, so erhält man ein unfühlbares Pulver, das mit dem durch das
Waschen abgesonderten Pulver ganz identisch ist. Der trokene Thon absorbirt sehr
schnell Wasser, wenn man ihn damit in Berührung bringt, und er zerfällt dann leicht
bei Anwendung von Druk bildet aber keinen Teig wie die fetten Thonarten, die in der
Glasfabrication zu Tiegeln verwendet werden. Der Thon von Stourbridge enthält keine
andern fixen Bestandtheile als Kieselerde und Thonerde: ich fand darin auch nicht
die geringste Spur von alkalischen Erden oder Metalloxyden. Er unterscheidet sich
übrigens von den meisten andern feuerfesten Thonarten durch ein großes Verhältniß
der Thonerde, die er enthält. Die erdige Masse, welche im Wesentlichen den Thon
ausmacht, ist innig mit einem brennbaren Stoff gemengt, der beim Calciniren (Glühen)
in verschlossenen Gefäßen einen kohligen Rükstand läßt; dieser färbt jedes
Partikelchen der erdigen Masse dunkelgrau und verflüchtigt sich nur durch sehr lange
fortgeseztes Rösten. Diese so innige Mengung mit Kohlenstoff scheint zur Erhöhung
der Feuerbeständigkeit des Thons beträchtlich beizutragen. Ich fand den Thon von
Stourbridge zusammengesezt aus 0,461 Kieselerde, 0,388 Thonerde, 0,128 Wasser in
Verbindung mit flüchtigen brennbaren Stoffen, 0,015 Kohlenstoff, erzeugt durch
Calciniren in einem geschlossenen Gefäße. Der Thon von Stannington zeigt beinahe die
nämlichen äußern Charaktere, wie der von Stourbridge; nur ist seine Farbe weniger
dunkel. Er ist auch nicht so homogen, indem man durch Waschen leicht glänzende
Glimmerblättchen absondern kann; er ist auch noch weniger, wie der Thon von
Stourbridge, geneigt mit Wasser einen Teig zu bilden. In verschlossenem Gefäße
calcinirt, gibt er einen dunkelgrauen Rükstand, aber das Rösten macht diese Farbe
nicht verschwinden und verursacht keinen Gewichtsverlust. Ich fand ihn
zusammengesezt aus 0,420 Kieselerde, 0,409 Thonerde, 0,001 Bittererde, 0,013 Kalk,
Spuren von Eisenoxyd und 0,147 gebundenem Wasser. Das Gemenge beider Thonarten, das
man auch zur Tiegelfabrication verwendet, besteht für jeden Tiegel aus 5,22 Kilogr.
(1 Kilogr. = 57 Loth) getroknetem und pulverisirtem Thon von Stourbridge, 5,22 Kilogr. getroknetem und
pulverisirtem Thon von Stannington, 5,43 Kilogr. pulverisirter Tiegelscherben und
0,05 Kilogr. Kohkspulver. Man befeuchtet diese Materialien mit der zur Erzeugung
eines zusammenhängenden Teiges, der die ihm gegebene Form behält, nöthigen
Wassermenge. Ist der Tiegel auf die im Folgenden angegebene Weise geformt und in
mäßiger Rothglühhize gebrannt worden, so sieht man im Bruche deutlich, wie die
nebeneinander liegenden erdigen Theilchen und die kleinen Kohksüberreste durch ein
graues, thoniges Cement vereinigt sind. Diese Bestandtheile hängen nur schwach
zusammen und zerfallen durch den Hammerschlag leicht in Pulver. Ich fand das Gewicht
eines geglühten Tiegels im Mittel 9,08 Kilogr. oder 16 Pfd. 6 Loth. Hat der Tiegel
bereits zum Stahlschmelzen gedient, so zeigt sich seine Textur (Gefüge) vollkommen
verändert. Der Teig ist in ein glasiges Email von außerordentlicher Härte, so daß es
von der Feile nicht angegriffen wird, umgewandelt, hat eine sehr dunkle, schwarze
Farbe, die sich nur durch geringeren Glanz von jener der eingekneteten
Kohksfragmente unterscheidet. Das glasige Gefüge tritt immer mehr hervor und die
Poren werden immer weniger und kleiner (mikroskopischer), je länger der Tiegel der
Stahlschmelzhize ausgesezt bleibt. Bei einem Tiegel, der versuchsweise während fünf
Schmelzungen dieser Hize ausgesezt belassen worden, war die erdige Materie in ein
schwarzes, sehr verglastes und vollkommen homogenes Email umgewandelt, welches, aus
dem Ofen kommend, sich strekbar zeigte, wie halb erkaltetes Glas.
Art, die Tiegel zu verfertigen. – Die Fabrication
der Stahlschmelztiegel erfordert weniger Handarbeit, als jene der Tiegel, die in den
Glas- und Zinkhütten angewendet werden. Sie geschieht mittelst Formen, deren
eine man in Fig.
27 sieht. a, a ist ein innerlich sorgfältig
und rein ausgebohrter, nach oben sich etwas erweiternder und an beiden Enden offener
Cylinder aus Gußeisen und von gleicher Höhe mit den zu fabricirenden Tiegeln. b, b ist ein gußeiserner Sokel (Bodenplatte), der in
einen Holzkloz fest eingelassen und mit einer cylindrischen Vertiefung versehen ist,
in welche das untere Ende des Cylinders a, a eingepaßt
wird. Im Mittelpunkt hat der Sokel eine Vertiefung zur Aufnahme des untern Endes des
Kerns c, c aus sehr hartem und schwerem Holz (wie es die
tropischen Gegenden liefern), der die innere Gestalt der zu erzeugenden Tiegel hat
und durch den eine starke eiserne Achse hinabgeht, deren unteres Ende in der
besagten Vertiefung im Centrum des Sokels ruht, während das obere Ende einen
abgerundeten Kopf trägt, der die Bestimmung hat, Schläge eines schweren Hammers zu
empfangen. Ueber dem Holzkern c, c befindet sich eine
kreisrunde gußeiserne Scheibe e, e, die einen gleichen Durchmesser mit
dem obern Ende des Cylinders a, a hat. Wird nun das
untere Ende der Achse d des Kerns c, c in die dafür bestimmte Vertiefung des Sokels eingeführt, so bleibt
zwischen dem Kern c, c in der Form a, a ein leerer Raum, welcher genau die Gestalt hat, die
man dem Tiegel geben will.
Um nun einen Tiegel zu formen, überzieht der Arbeiter zuerst die zwei Theile der Form
mit einer Schicht Oehl, sezt dann den Cylinder a, a in
den Sokel b, b ein (wie es die Fig. 27 zeigt), bringt
hierauf in den Cylinder die oben angegebene Menge (10,92 Kilogr.) des Thonteiges und
drükt in die Mitte dieses Teiges den Kern c, c so ein,
daß seine Achse stets vertical bleibt und mit der Achse des Cylinders a, a zusammenfällt. Wenn der Widerstand des Thons
endlich so groß wird, daß ihn der Arbeiter durch bloßen Druk nicht mehr gewältigen
kann, so treibt der Arbeiter den Kern vermittelst eines mit beiden Händen geführten
Hammers so lange weiter ein, bis das untere Ende der eisernen Achse dieses Kerns in
die für dasselbe bestimmte Vertiefung im Sokel b
eingedrungen und die oben am Kern befindliche runde Eisenscheibe in die obere
Oeffnung des Cylinders hineingetreten ist, wie man dieß alles in Fig. 27 sieht. Um den
geformten Tiegel aus der Form herauszunehmen, braucht man nur den Kern
herauszuziehen, das im Boden des Tiegels durch die eiserne Achse d des Kerns gebildete Loch zu verstopfen, den Cylinder
a mit dem darin befindlichen Tiegel aus dem auf
seiner Unterlage unverrükbar befestigten Sokel b, b
herauszunehmen, den Boden des Tiegels auf eine kreisrunde Scheibe von Holz (m, Fig. 28) welche einen
etwas kleineren Durchmesser als der Tiegelboden hat und von einer eisernen Stange
n getragen wird, zu stellen und den Cylinder a, a vorsichtig zu halten, so sinkt dieser durch sein
eigenes Gewicht hinab und läßt den Tiegel isolirt auf der Scheibe m stehend zurük. Der Arbeiter vollendet hierauf die Form
des Tiegels dadurch, daß er ihn oben durch einen gelinden Druk verengt und ihm so
die in Fig.
28 genau dargestellte Gestalt gibt. Der Tiegel hat demnach seine größte
Weite 1 Decimeter (3 Zoll 11 Linien) unter seiner Mündung. Sein größter äußerer
Durchmesser beträgt 19 Centim. (7,1 Zoll) und der correspondirende innere
Durchmesser beträgt 16 Cent. (6 Zoll). Der äußere Durchmesser der Mündung ist 17
Cent.(6 Zoll 4 1/2 Linie). Die Dike der Tiegelwand nimmt allmählich ab von 3 Cent.
oder 1,13 Zoll (Dike am Boden) bis 14 Millimeter oder 6,3 Linien (Dike am obern
Rand). Die Untersäze (Untersezer), auf welche die Tiegel beim Schmelzen gestellt
werden, sind kleine Cylinder (m', Fig. 29) von 13 Cent.
(4,9 Zoll) Durchmesser und 8 Cent. (3 1/2 Zoll) Höhe, und die größte Dike der gegen
die Mitte etwas gewölbten
Dekel n' der Tiegel ist 4 Cent. (1,8 Zoll).
Es ist wesentlich, daß die Tiegel nur sehr langsam das beim Formen zugesezte Wasser
verlieren; man läßt sie deßwegen auch einige Tage in dem Locale, wo sie geformt
werden, stehen und stellt sie nachher auf Gestellen mit mehreren Etagen auf, die an
den Mauern der Schmelzhütte, wo wegen der Nähe der Schmelzöfen eine ziemlich hohe
Temperatur herrscht, wie man dieß in Fig. 24 und 25 bei M, N sieht, befestigt sind.
Die Verfertigung der Tiegel ist eine sehr mühselige Arbeit und ein guter Arbeiter
bringt mit 108 Tiegeln, die eine Schmelzhütte mit zehn Oefen beim stärksten Betrieb
jede Woche braucht, wenigstens 6 Tage zu, und ich kann nicht begreifen, warum man in
einem Lande, wo die Handarbeit so theuer ist, diese Arbeit nicht schon lange durch
eine Maschine vermindert hat, deren Einrichtung sich von selbst aufdringt und bei
welcher der Kern in die Thonmasse durch eine Schraubenspindel eingedrükt werden
könnte, welche durch eine mit dem Sokel unveränderlich verbundene Mutter ginge.
Gießform zum Gießen des geschmolzenen Stahles. –
Wenn der Stahl geschmolzen und flüssig geworden ist, so wird er in gußeiserne Formen
(Fig. 30)
gegossen, die am obern Ende offen, am untern hingegen geschlossen sind und aus zwei
Theilen bestehen, die in einander passen und die, während der Stahl eingegossen
wird, durch Keile zusammengehalten werden, die man mittelst eines Hammers zwischen
die Gießform und die zwei auf dieselbe aufgestekten schmiedeisernen Ringe r, s eintreibt. Die Gestalt der Gießformen varirt etwas
in den verschiedenen Hütten und jenach der lezten Bestimmung des durch das Gießen zu
erzeugenden Productes. Gewöhnlich erhält der Gußstahl die Gestalt achtekiger Prismen
von 25–30 Quadratcentim. (9,4–12,1 Quadratzoll) Durchschnitt und 60
Cent. (2,2 Fuß) Länge. Die Gießformen werden zum Behuf des Gießens paarweise und
gegen den Rand einer kleinen am Boden der Schmelzhütte angebrachten Grube geneigt
aufgestellt, wie Fig. 30 zeigt.
In einer Stahlgießerei sind auch noch nöthig: Zangen zum Herausnehmen der Tiegel aus
dem Feuer (Fig.
31) und zum Eingießen des Stahls in die Gießformen (Fig. 32); ein großer
Trichter von Eisenblech und eine lange Eisenstange (Fig. 33) zur Beschikung
der Tiegel. Ferner Schürstangen zum Reinigen des Rostes und gehöriger Anordnung der
Kohksstüke im Ofen; Körbe zum Transportiren und Aufgeben der Kohks; Hämmer zum
Zerschlagen der Cementstahlstangen und endlich Schraubstok und andere Werkzeuge, um im
Erforderungsfalle die Gießformen zuzurichten.
In Yorkshire werden die Kohks immer außerhalb der Stahlschmelzereien erzeugt und es
befindet sich bei jeder Schmelzhütte an dem Gebäude nur noch ein ziemlich großer Hof
zur Deponirung der Sandsteine des feuerfesten Staubes, der alten Tiegel und der
Ofenschlaken. Es ist gut, wenn in diesem Hofe die Wägen, welche den Cementstahl, die
Kohks, die feuerfesten Materialien u.s.w. zuführen, umkehren können. Für eine
Schmelzhütte, wie sie abgebildet ist, reicht eine Area von 400 Quadratmeter (1264
Quadratfuß) hin.
Rohstoff und Brennmaterial. – Der zur Fabrication
des Gußstahls zu verwendende rohe Cementstahl wird vermittelst eines Hammers in
Stüke von zweierlei Sorte zerschlagen: die einen, welche die ganze Breite der Stange
behalten, sind um 5–7 Cent. (22,5–31,5 Linien) kürzer als die Höhe des
Tiegels, so daß sie im Tiegel aufrecht gestellt werden können; die andern sind
kleine unregelmäßige, meistens 10–20 Kub. Cent. (3,6–11,2 Kub. Zoll)
große Stüke. Befindet sich bei der Schmelzhütte auch eine Werkstatt, worin Gußstahl
verarbeitet wird, so gibt man mit dem Cementstahl auch eine gewisse Menge Abfälle
und Ausschuß in den Tiegel.
Die Kohls sind in den meisten Hütten dicht, sehr hart, aus einer vollkommen
verglasten Masse bestehend, die mit zum größten Theil nur mikroskopisch kleinen
Vertiefungen besäet und hin und her mit Rissen durchzogen ist. Dieser Risse und
Sprünge wegen varirt ihre mittlere Dichte von 0,75–0,92. Eingeäschert
hinterlassen sie einen lehmigen Rükstand, der mit Säuren nicht braust und der
gewöhnlich nur durch etwas Eisenoxyd gefärbt ist. Eine Analyse von Kohks, die als
die besten zum Stahlschmelzen anerkannt sind, gab 0,837 fixen Kohlenstoff, 0,039
brennbare flüchtige Bestandtheile, 0,015 hygrometrisches Wasser und 0,109 sehr
feuerfeste lehmige Asche. Vor der Anwendung werden die Kohks in 60–190 Kub.
Centim. (22,5–71,2 Kub. Zoll) große Stüke zerschlagen. Der Staub und das
Kohksklein, welche sowohl durch dieses Zerschlagen entstehen als auf dem Boden des
Magazins zurükbleiben, werden entweder im Schmelzofen zum Anheizen und in der
Zwischenzeit zwischen zwei Schmelzungen derselben Campagne oder in dem Ofen zum
Brennen der Tiegel verwendet.
(Der Beschluß folgt im nächsten
Heft.)
Tafeln
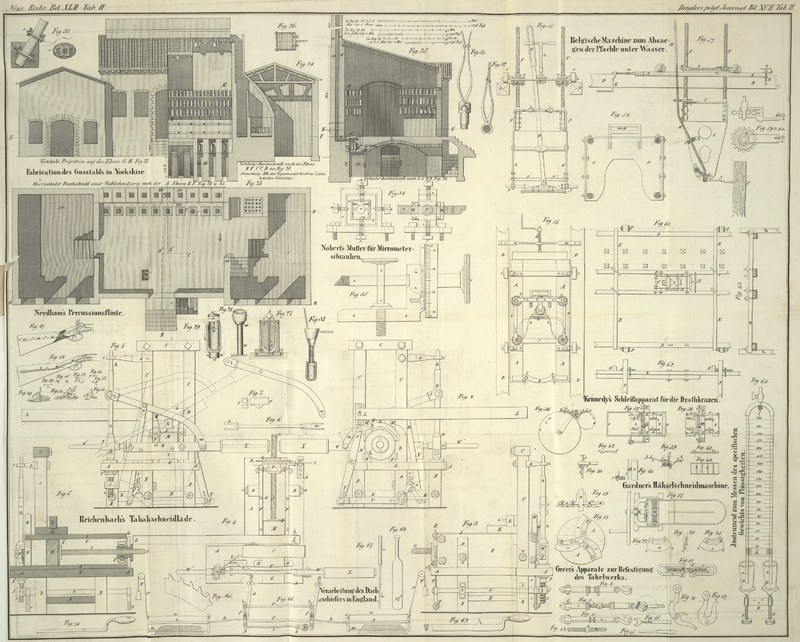