Titel: | Notizen über die Fabrication von Schienen, Achsen und Radreifen in England; vom Maschinenmeister G. Welkner in Hannover. |
Fundstelle: | Band 129, Jahrgang 1853, Nr. XCVIII., S. 432 |
Download: | XML |
XCVIII.
Notizen über die Fabrication von Schienen, Achsen
und Radreifen in England; vom Maschinenmeister G. Welkner in
Hannover.
Aus dem Notizblatt des hannover'schen Architekten- und
Ingenieur-Vereins, 1853, Bd. II S. 400.
Mit Abbildungen auf Tab.
VII.
Welkner, über die Fabrication von Schienen, Achsen und Radreifen in
England.
Die englischen Eisenwerke erblasen Roheisen Nr. I, II, III und IV. Nr. I und II sind
die besten für die Gießereizwecke bestimmten Sorten, während Nr. III und IV mit
Zusatz von Millcinders erblasen werden, dünnflüssig und kohlenstoffärmer sind und
zur Fabrication von Schmiedeisen aller Art verwendet werden. – Nr. III ist
das bessere, Nr. IV das schlechtere Eisen, welches häufig noch als mottled (halbirt) oder white
(weiß) fällt, welche Sorten stufenweise noch schlechter sind, und zu Schienen und
Eisen für den gewöhnlichen Handel (merchant iron)
bestimmt wird. – Auf einigen Werken ist es üblich, zur Erzielung eines
besonders festen und zähen Eisens (s. g. boiler plate pig
iron) in dem Hohofen außer dem Millcinders noch Abfälle von Schmiedeisen,
namentlich feine Blechschnitzeln, bis 8 Procent der Beschickung zuzusetzen (nach Stirlings Patent, s. Seite 212 in diesem Bande des
polytechn. Journals); man kann dieß Eisen IIIa
nennen.
Die Fabrication der verschiedenen Schmiedeisen-Sorten aus dem Roh- (pig) Eisen ist so verschieden, wie die Preise und
Qualität, welche mit dem Mehr oder Weniger der darauf verwandten Arbeit Hand in Hand
gehen. Schienen sind am billigsten, es wird aber auch in der Regel nicht viel Arbeit
zur Herstellung von guter Qualität aufgewandt, während bei manchen Eisensorten, die
den zwei- bis vierfachen Preis haben, das Mehr an aufgewandter Arbeit und
Auslagen damit im richtigen Verhältnisse steht. – Freilich ist nicht zu
übersehen, daß die Qualität der verwandten Rohmaterialien bedeutenden Einfluß hat,
wie in dieser Beziehung die Eisenfabriken des mittleren und nördlichen Englands
(Staffordshire und Yorkshire etc.) gegen die in Süd-Wales wegen ihrer bessern
Eisensteine und Kohlen bedeutend im Vortheil sind. – Einige Eisenwerke, wie
Low Moor und Bowling, sind besonders begünstigt und haben z.B. eine ausgezeichnete
Kohle, die aber sehr tief und nur in 18'' dicker Lage vorkommt, und deßhalb
kostspielig zu gewinnen ist.
Für die Schienenfabrication wird das Roheisen direct gepuddelt. Die Luppen werden
unter Squeezers (statt Hämmer) gezängt und in Slabs Nr. I, Flacheisen von 4–6'' Breite und 1''
Dicke, ausgewalzt. – Diese Slabs sind an den
Kanten sehr rissig und enthalten noch einen guten Theil Schlacke. Da sich diese
Fehler bei der nächstfolgenden Bearbeitung noch nicht ganz verlieren, so würde eine
direct aus Nr. I Eisen gebildete Schiene in der Regel unbrauchbar ausfallen und,
wenn auch im Allgemeinen mehr hartes krystallinisches Metall enthaltend, doch zu
ungleichförmig wegen eingesprengter Schlacken seyn, weiche und unganze Stellen
haben, die sich rasch entzwei fahren.
Die allgemeine Methode, Schienen zu fabriciren, ist deßhalb, den Kern der Schiene
(Fig. 14,
a und b) aus Nr. I Eisen
zu machen und diesen mit einer Hülle von Nr. II Eisen zu umgeben. Zu dem Ende wird
Eisen Nr. I aufgeschnitten, zu piles zusammengelegt,
geschweißt und wieder in Slabs Nr. II ausgewalzt. Aus
1/4 bis 1/2 von Eisen Nr. II und 3/4 bis 1/2 Eisen Nr. I wird dann obenstehender pile (a) zusammengelegt,
etwa 4' lang, geschweißt und ausgewalzt, wo dann die 18' lange Schiene wie
obenstehend (b) eine etwa 1/4'' bis 3/8'' starke Schicht
Eisen Nr. II bekommt, welche sauber aussieht und etwas weicher, aber gleichmäßiger
beschaffen ist als der Kern; dagegen muß es aber häufig wieder vorkommen, daß eben
der verschiedenen Qualitäten wegen die Schweißung zwischen den beiden Eisensorten
nicht gut wird, die Hülle sich also beim Fahren abblättert. Um diesem Uebelstande zu
begegnen, nehmen einige Ingenieurs in ihre Schienen mindestens die Hälfte Nr. II
Eisen, so daß die Hülle
des Kopfes 1/2'' bis 5/8'' stark wird. Ein Abblättern wird dadurch ziemlich sicher
auch bei unvollständiger Schweißung vermieden. Gut ist es auch, die Ecken der piles aus Winkeleisen zu bilden, wodurch die Ecken des
Kopfes jedenfalls am gesundesten werden. Es gelten diese Angaben für die in England
allgemein üblichen doppelköpfigen Schienen. Für flachbasige Schienen möchte eine
Vorschrift, wonach der Fabrikant verpflichtet wird, zu ihrer Herstellung wenigstens
2/5 Eisen Nr. II zu nehmen und es so anzuordnen, daß dasselbe (Fig. 15, a und b) bei der fertigen
Schiene am Kopfe 5/8'' stark aufliegt und theilweise aus Winkeleisen gebildet wird,
das einzige Mittel seyn, aus zwei Eisensorten überhaupt eine gute dauerhafte Schiene
herzustellen.
Außerdem möchte es zwei Methoden geben, gute Schienen zu machen, die aber wegen
größerer Kostspieligkeit bislang keinen Eingang gefunden haben, nämlich: entweder
direct aus besserem Eisen Nr. I, und zu dem Ende müßte das Roheisen sorgfältiger
gepuddelt, nicht unter Squeezers, sondern unter dem Hammer gezängt, dann zu Eisen Nr. I ausgewalzt werden;
der daraus gebildete pile müßte zuerst erhitzt und unter
dem Hammer zusammengeschweißt, nochmals erhitzt und zur Schiene ausgewalzt werden.
Die so fabricirte Schiene würbe jedenfalls eine möglichst harte seyn, ziemlich
gleichförmiges Material enthalten, aber im äußern Ansehen Manches zu wünschen übrig
lassen. Eine bessere Methode, die eine schönere Schiene vollkommen so hart und von
gleichmäßigerem Materiale verspricht, möchte die seyn, das gepuddelte Eisen in
Luppen zu hämmern und zu Nr. I Eisen auszuwalzen, dieses
zu schneiden und zu schweißen, nochmals auszuwalzen und so die ganze Schiene aus Nr.
II zu bilden, die piles aber unter dem Hammer zusammen
zu schweißen, nochmals zu erhitzen und dann erst zur Schiene auszuwalzen. Ich bin
der Meinung, daß die Fabrikanten diese letztere Methode gegen eine Mehrzahlung von
20 Sh. pr. Tonne gegen den gewöhnlichen Schienenpreis
machen können; die Schienenfabrikanten werden sich aber zu einer solchen
Fabricationsmethode deßhalb schwerer entschließen, weil sie in gleicher Zeit nur ein
bedeutend kleineres Quantum solcher Schienen anfertigen könnten, auch ihre
Etablissements durch Anlage von Stirn- und Dampfhämmern bedeutend erweitern
müßten.
Etwas Aehnliches, nämlich ein Nachschweißen der Schienen-piles vor dem Walzen zur Schiene geschieht jetzt schon
in Wales. Nachdem der ursprünglich 4' lange pile aus
Eisen Nr. I und II unter den Walzen zusammengeschweißt und etwa 6' lang geworden,
wird er nochmals ererhitzt und dann erst zur Schiene ausgewalzt; man sieht sich
hierzu veranlaßt, weil
das Wales-Eisen zu viel Schlacke enthält, die sich bei der ersten Schweißung
nicht alle entfernen läßt.
Im Allgemeinen darf man annehmen, daß in Staffordshire und Yorkshire zu den Schienen
ein besseres Material genommen wird, als in Wales, daß aber das Wales-Eisen,
obgleich schlechter als das der übrigen Eisendistricte, doch härter ist und sich
deßhalb zu Eisenbahnschienen besonders eignet. Aus diesem Grunde hat sich die
Hauptschienenfabrication auch nach Süd-Wales gezogen, wo deßhalb für die
specielle Schienenfabrication die besten Einrichtungen getroffen sind. So z.B. nimmt
man auf dem Werke zu Conzett bei New-Castle zu den Schienen durchgängig
sorgfältiger zubereitetes Material, als es in Wales der Fall ist, dahingegen sind in
Wales die Einrichtungen zum Walzen, Richten, Abschneiden, Lochen etc. der Schienen
vollkommener.
Die Selbstkosten der englischen Schienenfabrikanten kann ich nicht genau angeben, sie möchten aber etwa, wie folgt, seyn:
Arbeitslohn
pr. Ton.
für Blasen
2 Sh. –
D.
„ Puddeln
4 „ 6 „
„ Squizen und Walzen
6 „
– „
„ die
Hälfte zu schweißen und walzen
6 „
– „
„ Packetiren, Schweißen und Walzen
der Schienen
8 „
– „
„ Richten, Lochen etc.
6 „
– „
––––––––––––––
1 Pfd. 12 Sh. 6 D.
Generalkosten, als:
Zinsen, Unterhaltungskosten etc.
100 Proc
1 „ 12 „ 6 „
–––––––––––––––
= 3 Pfd. 4 Sh. – D.
Materialien:
3 1/2 Ton. Eisenstein
11 „ 6 „
Zuschlag
2 „ – „
4 Ton. Kohlen und zu Kohks à 3 Sh.
12 „ – „
––––––––––––––
4 Pfd. 15 Sh. 6 D.
so daß die Fabrikanten zu dem Preise von 5 Pfd. pr. Ton. verkaufen können, wenn man schlechte Schienen
mit in Anschlag bringt, die als vergeblich gewalzt einen weiteren Ausfall
bringen.
Zur Fabrication alles anderen und besseren Eisens wird das Roheisen zuerst raffinirt
(refined), wobei ihm Kohlenstoff entzogen und
fremdartige Beimischungen theilweise entfernt (verschlackt) werden. Das raffinirte
Eisen wird gepuddelt, unterm Hammer gezängt, zu Slabs
Nr. I ausgewalzt, diese
zerschnitten, aufgepeilt, geschweißt und schlechtere Eisensorten daraus fertig
gewalzt. Zu besseren Sorten: Blechen, Winkeleisen, breite Flacheisen etc. werden Slabs Nr. II daraus gewalzt, diese zerschnitten und zu
dem vorliegenden Zweck aufgepeilt, geschweißt und gewalzt. Einige Fabrikanten nehmen
für besonders zähes Eisen beim Puddeln bis 5 Procent Scrap-Eisen zu, es darf aber erst zugesetzt werden, wenn das Eisen
im Ofen aufgehört hat zu kochen, am besten sind ganz feine Eisenabfälle. Bei allen
diesen Fabricationsmethoden fällt das Eisen sehr verschieden aus und ist immer desto
besser, je mehr Arbeit auf die einzelnen Manipulationen verwendet wird. Ein Mangel
aber an allen so hergestellten Eisensorten bleibt immer ein zu sehniges Gefüge, was
namentlich bei langen schmalen Formen, die nur nach einer Richtung gewalzt werden,
bedeutend auftritt. Es läßt sich das nicht anders als durch Hämmern des Eisens vor
dem Walzen beseitigen.
Ganz frappant tritt der Unterschied des Hämmerns und Walzens hervor, wenn man die
Fabricationsmethoden in Low Moor und Bowling, wo unstreitig das beste Eisen gemacht
wird, mit der auf gewöhnlichen Eisenwerken vergleicht; während hier durchweg das
oben beschriebene Verfahren besteht, wird dort alles Eisen zu Eisen Nr. I, II und
III gehämmert, so daß die Stücke nur durch die Walzen zu
gehen brauchen, um schließlich die verlangte regelmäßige Form zu erhalten.
Vergleicht man die Resultate dieser (Low Moor) Fabricationsmethode mit denen der
gewöhnlichen, so geht daraus unzweifelhaft hervor, daß man zur Erzielung eines
wirklich guten allen Anforderungen entsprechenden Schmiedeisens ein theilweises
Hämmern anwenden muß. Es möchte sich besonders empfehlen das Eisen Nr. II, nachdem
es zu dem zu walzenden Gegenstande aufgepeilt ist, zunächst zu schweißen und unter
dem Hammer nach allen Richtungen zu hämmern, dann das Stück nochmals zu erhitzen und
erst dann auszuwalzen.
Diese Fabricationsmethode, welche man jetzt schon bei Stücken über circa 5 Centner schwer aus dem Grunde anwendet, weil das
Schweißen solcher großen Stücke unter den Walzen nicht in einem Male vollkommen zu
beschaffen ist, würden sich freilich die Fabrikanten etwas theurer bezahlen lassen,
wie denn auch der Grund des Preisaufschlages, welcher für schwerere Stücke über
4–5 Centner zwischen 1 und 8 Pfd. Sterl. die gewöhnlichen Preise übersteigt,
hauptsächlich in den zu ihrer Herstellung unumgänglich erforderlichen Hammerarbeiten
zu suchen ist. Wie weit das übrigens gehen kann, folgt auch daraus, daß z.B. zu
einer Zeit, wo die Staffordshire-Preise für beste Kesselbleche unter 4
Centner schwer 10 Pfd. St. war, der Preis für solche Bleche in Low Moor sich auf 23
Pfd. Sterl. stellte (man s. über die Eisenhütte
„Low-Moor“ Seite 97 in diesem Bande des polytechn. Journals).
Hier ist zu bemerken, daß ich in Low Moor eine dort gemachte Blechplatte von 22'
lang, 4 1/2'' breit, 3/4'' dick sah, und daß ich auf dem Conzett-Werke
mehrere Blechplatten von 30' Länge, 33'' Breite, 3/4'' Dicke, die unbeschnitten ein
Gewicht von nahe 30 Centnern hatten, walzen sah. Zu ihrer Herstellung walzte man
Stücke von etwa 10 Centnern, nachdem sie etwas gehämmert waren, aus, legte im
Schweißofen drei Stücke aufeinander und ließ das so im Ofen zusammengeschweißte
Stück von 30 Centner durch die Walzen gehen. Auch machte man Bleche von 4' 8''
Breite, 1/2'' Dicke und 16' Länge. Ich mache diese Angaben, um zu zeigen, auf welche
Blechgrößen man in England rechnen kann, bemerke aber, daß sich kleine Blechplatten
bis 4 Centner schwer mit viel mehr Sicherheit gut und solide fabriciren lassen, als
große, während die Preise für letztere unverhältnißmäßig größer seyn müssen.
Ein aus Eisenabfällen zusammengeschweißtes (Scrap) Eisen,
wenn es mit der gehörigen Vorsicht gemacht, d.h. möglichst gleichartige Stückchen zu
einem größeren unter dem Hammer gut zusammengeschweißt werden, eignet sich ganz
besonders zu beweglichen Theilen an Locomotiven und wird auch in der Regel hierzu
angewendet. Im Allgemeinen nehmen die Locomotivfabriken zu allen solchen Theilen nur
gehämmertes, niemals gewalztes Eisen; das Eisen von Hood
und Cooper in Leeds zeichnet sich besonders aus.
Das Eisen zu Krummachsen für Locomotiven wird nur gehämmert (Fig. 16). Man schmiedet
Platten von etwa 2'' bis 3'' Dicke und 2' im Quadrat und schweißt davon 4 bis 6
Stücke so zusammen, daß die Hauptfaserrichtung kreuzweise kommt und ein Stück von
etwa 3 1/2' lang, 2' breit und 8'' dick entsteht; alsdann werden die Schenkel a, a und die Mitte b
zwischen den Kurbeln ausgereckt und zuletzt die Kurbel A
gegen die Kurbel B gedreht.
Von geraden Achsen werden wohl die der Patent axle tree
compagny zu Locomotiven und Wagen am meisten verwandt; sie machen ihre
Achsen, indem sie um einen oder mehrere Bolzen von Rundeisen, welche zunächst allein
zusammengeschweißt werden, eine Platte schweißen (Fig. 17).
Saudfort und Oven's Patent-Achsen, Rotherham near
Sheffield (auch in Sunderland gemacht), werden, wie Fig. 18 zeigt, aus 12
Segmentstücken a in Längen von etwa 3 1/2'
zusammengeschweißt und ausgereckt. Die Stäbe a werden
aus Scrap-Eisen geschmiedet und dann gewalzt. Der Preis in Sunderland war im Monat September v.
J. per Cntr. 12 Sh. und 1 Sh.
Patent-Vergütung.
Viele Locomotivfabrikanten machen übrigens ihre Achsen selbst, so weit ihr Vorrath
von Scrap-Eisen dazu ausreicht. Wilson in Leeds
machen auch Wagenachsen aus Scrap-Eisen.
Locomotiv-Radbandagen werden in Low Moor auf folgende Weise gemacht: man
fabricirt durch auf einander folgendes Schweißen und Hämmern Nr. III Eisen und
bildet dann aus 2 Stücken Eisen, a und b, c (Fig. 19), wo die Fasern
von a horizontal, die von b
und c vertical liegen, einen 4' langen pile: b und c die vorher
schon zusammengeschweißt sind, werden nun mit a
zusammengeschweißt und so lange erhitzt und geschmiedet, bis man einen etwa 6'
langen tyreförmigen Stab erhält, der in einer Hitze ausgewalzt, von Länge
geschnitten und auf einer Maschine rund gerichtet wird. In der Regel werden die
Tyres auch auf dem Werke geschweißt. Bowling und Kirkstall Werke arbeiten ähnlich,
Kirkstall Werke haben aber keine eigene Roheisenfabrication.
Hood und Cooper's Tyres werden ihrer Härte wegen besonders gelobt.
Außerdem werden Wagenrad-Tyres und auch Locomotivrad-Tyres für den
Continent auf verschiedenen Staffordshire- und Yorkshire-Eisenwerken
angefertigt und, wenn auch sorgsamer als gewöhnliches Eisen, so doch in der Regel
durch bloßes Walzen hergestellt.
Tafeln
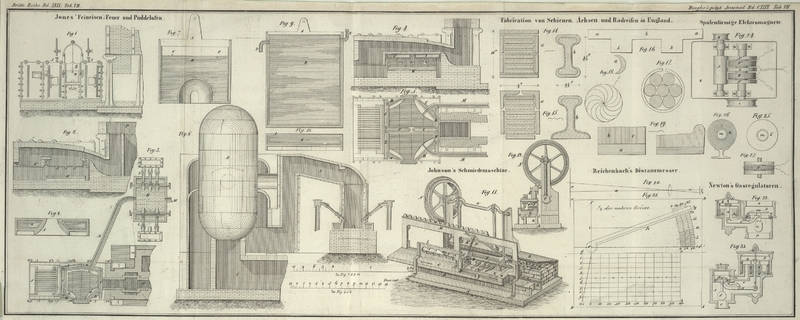