Titel: | Verbesserungen in der Metallförmerei und Gießerei, von J. Page und W. Robertson zu Dundee in Schottland. |
Fundstelle: | Band 142, Jahrgang 1856, Nr. XLIV., S. 185 |
Download: | XML |
XLIV.
Verbesserungen in der Metallförmerei und
Gießerei, von J. Page und
W. Robertson zu Dundee in Schottland.
Aus dem Practical Mechanic's Journal, April 1856, S.
5.
Mit Abbildungen auf Tab.
III.
Page's und Robertson's Verbesserungen in der Metallförmerei und
Gießerei.
Das Wesentliche dieser Erfindung, welche am 20. September 1855 in England patentirt
wurde, besteht darin, daß die Formen zu Metallgüssen von verschiedener Gestalt,
hauptsächlich aber von hohlen Gefäßen, Hohl- und Vollgeschossen, dadurch
hergestellt werden, daß man das Formmaterial zuerst eindämmt, dann gewisse Theile
aus demselben herausschneidet und es zuletzt zusammendrückt oder verdichtet, kurz ihm
durch Eindrücken eines geeigneten Modelles die Dimensionen und Verhältnisse ertheilt
welche das fertige Gußstück haben muß. Von den hierzu dienenden Apparaten der
Erfinder theilen wir folgende mit:
Fig. 17 zeigt
die Seitenansicht einer Maschine, welche aus einer schweren eisernen Platte mit zwei
Ständern an der Seite, als Gestell, besteht. Von den beiden Ständern hängen
Lagerarme herab, an denen die beiden entgegengesetzten Enden einer zwischen den
Ständern liegenden Platte gleiten; dieselbe ruht auf Zahnstange und Getrieben, deren
Welle in besondern Lagern liegt, die an dem Gestell angebracht sind; beide Enden der
Welle sind mit Handschwungrädern versehen. Statt der Bewegung mittelst Zahnstange
und Getriebe kann man auch Excentrica anwenden. Das obere Ende des Ständers zur
Rechten hat eine solche Form, daß es eine massive und eine hohle Welle aufnehmen
kann, von denen die erstere concentrisch in der zweiten steckt. An dieser Welle sind
zwei Kegelräder, einander gegenüber, angebracht, und greifen in ein drittes, an
einer kurzen stehenden Welle, welche durch einen an dem Ständer angegossenen Hals
geht und unten mit einem Handschwungrädchen versehen ist, durch dessen Umdrehung die
beiden erstern Kegelräder in entgegengesetzter Richtung umgedreht werden können.
In dem innern Ende der beiden in einander steckenden Wellen sind Schab- oder
Schneideisen angebracht, welche zum Ausschneiden oder Ausschaben des Sandes aus dem
Formkasten dienen; sie haben genau die Form des äußern Umrisses von dem zu formenden
Gußstück. Nachdem der Sand in dem Formkasten lose eingedämmt worden ist, stellt man
letztern auf die Platte und hebt diese mit Hülfe der Zugstange und der Getriebe oder
Excentrics so weit, daß die Form in den Bereich der Schabeisen gelangt. In der
gehörigen Höhe läßt man nun die Schabeisen mittelst des Handrädchens nach
entgegengesetzter Richtung sich drehen. Dieselben treten in das Formmaterial ein,
und indem sich nun die Kanten der Schneiden unterhalb in dem Sande treffen, fassen
sie einen Theil desselben und lassen die Mantelform des Gußstücks roh ausgeschabt
zurück.
Man läßt nun die Platte soweit niedergehen, daß die darauf stehende Form aus dem
Bereich der Schneideisen tritt, und setzt dann den Formkasten auf die andere Seite
der Platte, woselbst die Mantelform durch Eindrücken eines Modelles vollendet wird.
Letzteres ist an dem überhängenden Ende des Ständers zur Linken befestigt und hat
genau die äußere Gestalt des zu formenden Gußstücks, welches in dem vorliegenden
Falle in einem runden oder bauchigem Topfe oder Kochgeschirre besteht. Der
Formkasten mit der vorher ausgeschnittenen Vertiefung der halben Mantelform wird nun bis
zu dem Modell gehoben, letzteres wird in jene eingedrückt und dadurch die eine
Hälfte der Mantelform vollendet. An dem festen Topfmodell sitzen ein halbes
Einguß- und zwei halbe Henkelmodelle, so daß in der halben Form die
Vertiefungen für den halben Einguß und für zwei halbe Henkel gleichzeitig gebildet
werden. Nachdem auf diese Weise zwei Hälften der Mantelform angefertigt und über
eine gemeinschaftliche Kernform geschoben worden sind, ist die ganze Topfform zum
Abgießen vollendet.
Auch die Füße des Gefäßes können in den halben Formen dargestellt werden, indem sich
drei Stempel, deren untere Enden die Form der Füße haben, in Hülsen in den halben
Modellen verschieben lassen. Ehe man nun das Modell aus dem Formkasten entfernt,
schiebt man einen oder zwei dieser Stempel aus ihren Hülsen in den Sand, wo sie die
Fußformen bilden. Die eine Mantelformhälfte hat zwei und die andere einen Stempel,
so daß das fertige Gefäß drei gleich weit von einander abstehende Füße erhält.
Fig. 18 ist
eine Seitenansicht, so wie ein theilweiser Durchschnitt des Apparates zum
Zusammendrücken des Sandes über dem Kernmodell, und Fig. 19 ein senkrechter
Durchschnitt der zum Abguß fertigen Form, bestehend aus dem zweitheiligen Mantel und
aus dem Kern.
Den Kern verfertigt man in einem Kernkasten welcher aus zwei Hälften besteht, von
denen eine auf eine Platte gestellt wird; diese Kernkastenhälfte hat im Innern genau
die Gestalt der äußern Oberfläche des halben Kerns. Sie wird mit Sand versehen,
welcher vorher auf irgend eine Weise leicht zusammengedrückt und dann der Einwirkung
der Schabe- oder Schneideisen unterworfen wird. Der Kernkasten wird in eine
Ebene mit denselben gebracht, und es werden dieselben dann in eine drehende Bewegung
versetzt, um den Sand bis auf eine dünne Lage, welche die innere Oberfläche des
Kernkastens bedeckt, auszuschaben. Nachdem auf diese Weise zwei halbe Kernkasten
vorbereitet sind, werden sie über einen hohlen, durchlöcherten Metallkern geschoben
und zusammen auf eine Platte mit glatter Oberfläche gesetzt, nämlich zwischen eine
an der Platte festgeschraubte und eine verschiebbare Wange; letztere erhält ihre
Bewegung durch eine Schraubenspindel mit Handrad, welche durch eine Mutterschraube
geht, die ebenfalls an der Platte befestigt ist. Mittelst dieses Apparates werden
die beiden Kernkastenhälften mit der darin befindlichen Formmaterial-Lage
zusammen und gegen den Metallkern gedrückt; nachdem die Kernkastenhälften wieder aus
einander gezogen worden sind, bleibt der Sandkern vollendet auf dem Centralkern
zurück. Die Dicke der Sandlage in dem Kernkasten muß, nachdem der übrige Sand
herausgeschabt schabt
worden ist, der Art seyn, daß sie im Verhältniß zu dem ihr zu gebenden Druck steht,
da ein zu fester Kern der Vollkommenheit des Gusses eben so nachtheilig seyn würde
als ein zu lockerer. Der Centralkern muß genau zum Mantelkasten passen, weßhalb er
am Fuß mit einem scharfkantigen Ringe versehen ist, über den ein gleichgeformter
einspringender Ring des Mantelkastens greift.
Fig. 20 ist
die Vorderansicht einer Abänderung dieses Apparates um Sand- oder andere
Formen für Metallguß durch Zusammenpressung, und in diesem Falle hauptsächlich Voll- und
Hohlgeschossen die vollendete Form zu geben; die Hälfte der Form ist hier
im senkrechten Durchschnitt dargestellt. – Fig. 21 ist ein
Durchschnitt der vollendeten Form mit eingeschlossenem Kern.
Das Gerüst dieses Apparates ist ein bogenförmiger, gußeiserner Ständer, dessen innere
Seiten unten mit einander parallel gehen und mittelst der Hobelmaschine abgerichtet
sind, da sie die Platte oder den Tisch senkrecht leiten müssen. Eine liegende Welle
die mit einer Trieb- und einer Leerrolle versehen ist, geht durch Lager im
Ständer, und innerhalb desselben sind auf ihr zwei Hebedaumen angebracht, auf denen
der Tisch mittelst zweier Frictionsrollen ruht. Der Formkasten steht auf dem Tisch
und wird mittelst der Daumen oder Excentrics, durch Umdrehung der Rolle und der
Welle, zu dem festsitzenden Modell emporgehoben. Der im Kasten befindliche Theil der
Form entspricht der halben Kugel, Granate oder Bombe, und ebenso das Modell. Ehe die
Form zum Apparat gelangt, wird sie durch Ausschneiden des Sandes vorbereitet, d.h.
die Form erlangt auf diese Weise vorläufig einen kugelförmigen Ausschnitt und die
Sandlage bleibt dick genug, um durch Zusammendrücken mittelst des Modelles die
vollendeten Dimensionen zu erhalten. Das Modell wird in der Mitte des Bogens von dem
Ständer angebracht. Durch sein Inneres geht eine Röhre, durch welche man Dampf
strömen läßt, um das Modell zu erwärmen und daher das Anhängen des Materials an
dasselbe zu verhindern. Das Kranz- oder Randstück, durch welches die
Theilungsoberfläche der Form gebildet wird, liegt lose auf dem Modell, und zwischen
dasselbe und die untere Seite des Bogens wird ein Ring von Kautschuk oder sonst
einem elastischen Material gelegt. Das Randstück gibt daher dem aufwärts wirkenden
Druck der Form nach, bis es gegen die Verstärkung des Modelles drückt und dieses zur
richtigen Hälfte eingedrückt wird. Wenn der Formkasten von dem Modell zurücktritt,
so veranlaßt die Feder den Kranz ihm auf eine geringe Länge zu folgen und verhindert
daher das Abbröckeln der Kante der Theilungsfläche.
Fig. 22 ist
eine Seitenansicht der Maschine, welche einige Abänderungen des Apparates zum
Einformen und Abgießen von Metallen zeigt. Das Gestell dieser Maschine besteht aus
einem starken gußeisernen Ständer, welcher mit Halslagern für eine starke senkrechte
Stempelspindel versehen ist. Unter dieser Spindel ist eine Platte an dem Ständer
angegossen, auf welche der Formkasten gesetzt wird. Dieser hat den Zweck, die halbe
Form einer Kugel aufzunehmen. Die erste Arbeit bei diesem Förmereiverfahren besteht
darin, den Sand in dem Formkasten etwas festzudämmen, und zu diesem Zweck dient die
Stempelspindel. Sie hat ein verhältnißmäßig feines Schraubengewinde, welches mit
einem Schraubenrade im Eingriff steht, dessen Welle sich in Lagern dreht, die an dem
Ständer angebracht sind. An der Welle sitzt auch ein Zahnrad, in welches ein
Getriebe an einer andern Welle greift, an der auch ein Handschwungrad befestigt ist.
Dreht man nun dieses Handrad, so hebt oder senkt sich die Spindel. Am untern Ende
der Spindel sitzt ein Stempel, mit welchem der Sand in dem Formkasten etwas
zusammengedrückt wird und der eine kleine kugelförmige Vertiefung hervorbringt. Je
nach dem einzuformenden Gegenstande müssen die Stempel verschiedenartig geformt
seyn. Nach diesem vorbereitenden Eindämmen wird der Formkasten in eine zweckmäßige
Stellung gebracht, damit der andere Theil des Apparates auf ihn einwirken kann.
Diese Vorrichtung ist eine Abänderung von dem schon beschriebenen
Ausschabemechanismus. Er kann an demselben Gerüst, oder an einem besondern
angebracht seyn; im vorliegenden Fall findet das erstere statt, indem die Halslager
mit Armen versehen sind, die vorn eine senkrechte Platte haben. Auf dieser Platte
kann ein Schieber auf- und abgleiten, indem dieselbe mit Stiften versehen
ist, welche durch einen Schlitz gehen. Der Schieber ist mit einer Zahnstange
versehen, in die ein Getriebe mit Kurbel greift, so daß er gehoben oder gesenkt
werden kann, während ein Gewicht das Gleichgewicht hält. An dem Schieber sitzt ein
Arm, an dessen unteren Enden die Schneiden oder Schaber angebracht sind, welche dem
Viertel eines Kugelumfanges oder irgend einer andern Form entsprechen. Die Schneiden
sind durch Gelenke mit der Spindel eines Getriebes verbunden, welches in eine
Zahnstange an dem vordern Theil des Schiebers greift. Durch Umdrehen des Getriebes,
wobei die Gelenke niedergedrückt werden, senken sich die Schaber in der Richtung
ihrer Achse, und indem sie in das Formmaterial in dem Kasten eintreten, schaben sie
einen Theil desselben, welcher der anzufertigenden Form entspricht, heraus.
Der Formkasten wird nun zu einem Apparat gebracht, der dem zuerst in Fig. 22 beschriebenen
ähnlich ist und dazu dient, auf die Form die vollendende zusammenpressende Wirkung auszuüben. Sein
Gerüst besteht aus einem starken gußeisernen Ständer mit zwei Halslagern, durch
welche eine senkrechte Spindel geht, während an dem untern Theil eine Platte
angegossen ist, auf die der Formkasten gestellt wird. Die Spindel ist mit einem
Gewinde versehen, in das ein Schraubenrad greift, an dessen Welle ein Stirnrad
sitzt, in welches ein Getriebe an einer zweiten Welle greift, die auch mit einem
Handschwungrade versehen ist, durch dessen Drehung die Spindel gehoben oder gesenkt
wird. An das untere Ende der Spindel ist eine Modellhälfte angebracht und diese wird
in die Form eingedrückt, um ihr die Vollendung zu geben. Um aber der Form mit dem
Modell noch einen letzten starken Druck zu geben, ist oben an der Spindel, welche
unten das Modell trägt, noch ein Zahnrad angebracht, dessen Wirksamkeit durch die
Längenbewegung der Spindel nicht gehindert wird. Ein an einer senkrechten Welle
sitzendes Getriebe greift in dasselbe und dieser Mechanismus wird durch ein
Handschwungrädchen in Bewegung gesetzt. Durch dieses Triebwerk erhält die Spindel am
Ende ihrer niedergehenden Bewegung noch eine drehende Bewegung und das Modell wird
dadurch in die Form kräftig eingeschraubt. Soll nun das Modell zurückgezogen werden,
so wird das Triebwerk wieder in Bewegung gesetzt, damit sich das Modell in einer
Schraubenlinie nach aufwärts bewegt, wodurch das Lösen desselben von der Form
erleichtert wird.
Tafeln
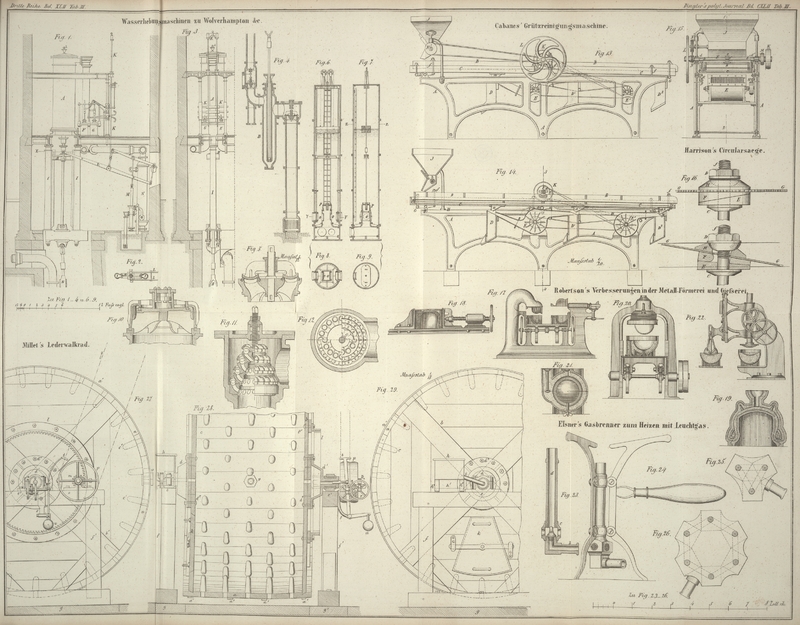