Titel: | Ueber das von den HHrn. Becchi und Haupt erfundene Verfahren zum Zugutemachen der Kupfererze; vom Bergingenieur E. Petitgand zu Paris. |
Fundstelle: | Band 147, Jahrgang 1858, Nr. XXXI., S. 101 |
Download: | XML |
XXXI.
Ueber das von den HHrn. Becchi und Haupt erfundene Verfahren zum
Zugutemachen der Kupfererze; vom Bergingenieur E. Petitgand
zu Paris.
Aus der Revue
universelle, Bd. II S. 249.
Mit Abbildungen auf Tab.
II.
Petitgand, über Becchi's Verfahren zum Zugutemachen der
Kupfererze.
Die Methoden zum Zugutemachen der Kupfererze auf dem nassen Wege oder zur
Cementkupfergewinnung, veranlaßten zahlreiche Versuche um sie zu verbessern, deren
Erfolg jedoch im Allgemeinen ziemlich unsicher geblieben ist. Ohne die Wirksamkeit
des einen oder des andern Verfahrens in Abrede stellen zu wollen, glauben wir, daß
die erfolgreiche Anwendung derselben durch verschiedene eigentümliche Umstände
bedingt ist. Die meisten dieser Kupferhüttenprocesse bezwecken das Zugutemachen
armer Erze, welche am häufigsten vorkommen und meistens die Hüttenkosten des
gewöhnlichen Verfahrens nicht zu tragen vermögen, und es läßt sich daher nicht
läugnen, daß wenn diese Methoden umsichtig angewendet werden, sie im Hüttenwesen
wesentliche Dienste zu leisten vermögen und daher den Abbau von
Kupfererz-Lagerstätten gestatten, die jetzt gar nicht gebaut werden
können.
Diese Betrachtungen veranlaßten uns zunächst zur nachfolgenden Mittheilung eines
neuen Verfahrens, welches wir im Frühjahr 1857 auf einer Reise durch die wichtigsten
Kupferbergwerke im Toscanischen im Betriebe sahen.
Dieses Verfahren, welches von den HHrn. Becchi, Professor
der Chemie zu Florenz, und C. Haupt (aus Freiberg),
Hüttendirector zu Massa, erfunden wurde, besteht in einer Verbindung des nassen
Weges oder der Cementation, mit dem trocknen Wege oder der Schmelzung; es gründet
sich hauptsächlich auf die Reactionen des Kochsalzes auf die aus mehreren
Schwefelmetallen zusammengesetzten Sulfuride. Es scheint uns einigermaßen mit dem
Augustin'schen Verfahren zur Extraction des Silbers
aus silberhaltigen Kupfererzen Aehnlichkeit zu haben, welches eine Zeit lang im
Mansfeld'schen angewendet wurde, um das Silber aus dem dortigen Kupferstein von sehr
complicirter Zusammensetzung zu gewinnen. Man wird übrigens aus dem Folgenden
ersehen, daß das Verfahren nur bei wesentlich kieseliger Gangart wirksam seyn
kann.
Die Erfinder stellen zur Begründung ihrer Methode Formeln auf, welche wir nicht
discutiren wollen, da sie uns irrig zu seyn scheinen, und mit der angenommenen
Theorie nicht übereinstimmen.
Der Betrieb nach dieser Methode steht auf der Kupferhütte Capannevecchie im Gebirge
von Massetano, unweit Massa marittima, etwa 30 Kilometer von dem Hafen Follonica, in
ausgedehnter Anwendung. Dabei müssen wir dankend die Gefälligkeit der Beamten jener
Hütte anerkennen, welche uns in den Stand fetzten, das neue Verfahren genau zu
studiren und in allen seinen Einzelheiten zu verfolgen, kurz alle Betriebsresultate
kennen zu lernen.
Beschaffenheit des Erzes. – Das behandelte Erz
kommt von einem sehr mächtigen Quarzgange im Jurakalk, in welchem sich sehr
regelmäßig Kupferkies, in Begleitung von sehr wenig Blende und Schwefelkies
eingesprengt findet. Der Kupfergehalt dieses Erzes beträgt durchschnittlich 1 3/4
bis höchstens 2 Procent.
Gang des Hüttenbetriebes. – Das auf die Halden, an
deren Fuß die Hütten liegen, geförderte Erz erleidet eine Handscheidung, um die
tauben Quarzstücke auszuhalten; es wird dann in Stücke von höchstens 4 bis 5
Centimeter Größe zerschlagen. Darauf bildet man auf einer Unterlage von Holz und mit
abwechselnden Schichten von Kohlen kleine Rösthaufen, wie sie am Harz, in Sachsen
und auf vielen anderen deutschen Hütten üblich sind. Solche runde Haufen enthalten
200 bis 250 Tonnen (à 20 Ctr.) Erz.
Erste Röstung. – Nachdem die Haufen entzündet
worden sind, bleiben sie 12 bis 14 Tage im Brande. Nachdem sie hinlänglich erkaltet
sind, zieht man sie auseinander, zerschlägt die zusammengebackenen Stücke, und hält
die unvollkommen gerösteten Stücke für eine folgende Röstung aus.
Diese erste Röstung hat nach den Erfindern des Verfahrens nur den Zweck, die
Zerkleinerung des Erzes zu erleichtern und wohlfeiler zu machen. Sie liefert jedoch
noch ein anderes, und zwar sehr wichtiges Resultat, indem sich dabei ein großer
Theil des Schwefels entwickelt, und überdieß bilden sich schwefelsaure Salze und
selbst Oxyde in beträchtlicher Menge; hierdurch müssen die folgenden Processe
wesentlich befördert werden.
Zweite Röstung. – Das auf diese Weise geröstete
Erz wird mittelst Pochwerken oder senkrechter Mühlsteine in Pulver verwandelt;
dieses wird durchgesiebt und gelangt in Flamm-Röstöfen. Dieselben haben die
Einrichtung der Freiberger Röstöfen, mit doppelter Sohle mit einem Feuerraum in der
Mitte; jede Sohle wird mit 2000 bis 2500 Kilogr. Material besetzt.
Uns scheint diese Art von Oefen zu dem vorliegenden Zweck nicht sehr vortheilhaft zu
seyn, weil man zu Capanne-vecchie nur Holz und Reißbündel verbrennen kann.
Die Oefen mit zwei übereinander liegenden Sohlen, deren man sich auf dem
Extractionswerke im Mansfeldschen, ferner am Rhein, in Belgien, Ungarn etc. zum
Rösten bedient, verdienen offenbar den Vorzug.
Sobald die Oefen besetzt sind, feuert man stark und unterhält das Feuer 2 1/2 bis 3
Stunden, so daß die Röstung unter dem Einfluß einer hohen und wohl unterhaltenen
Temperatur erfolgt, während die Arbeiter das Erz mit eisernen Rechen häufig
durchrühren, um die Entwickelung der Gase zu erleichtern und die Oxydation zu
befördern.
Chlorirung. – Man kann die Röstung als beendigt
ansehen, wenn die schwefligen Dämpfe aufhören von der Oberfläche des Erzes
aufzusteigen; man vermindert alsdann das Feuer, und sobald der Ofen dunkelroth zu
werden beginnt, setzt man Kochsalz zu, nämlich 2 bis 8 Proc. des eingebrachten
Erzes, je nach dessen Kupfergehalt. Es wird dann sogleich stark umgerührt und dieß
ohne Unterbrechung 10 bis 12 Minuten lang fortgesetzt. Nach einigen Augenblicken der
Ruhe zieht man das Gemenge aus dem Ofen und schreitet zu einer andern Röstung,
welche auf dieselbe Weise ausgeführt wird.
Dieser letztere Proceß ist der wesentliche Theil des Zugutemachens; er erfordert eine
außerordentliche Aufmerksamkeit, denn eine schlecht ausgeführte Röstung oder der
unzeitige Zuschlag des Salzes, können den ganzen Erfolg in Frage stellen.
Wir wollen nun das Resultat der Röstung besprechen. Die Erfinder behaupten, daß die
mit Kochsalz und Kieselerde in Berührung gebrachten Metalloxyde unter dem Einfluß
einer hohen Temperatur und des Wasserdampfes sich auf Kosten des im Kochsalz
enthaltenen Chlors in basische Chloride (Oxychloride) verwandeln, während das
Natrium als Natron frei wird, welches man durch Schwefelsäure neutralisirt, damit es
nicht einen Theil des löslichen Kupfersalzes präcipitirt.
Nimmt man die Theorie der Erfinder an, oder besser diejenige welche wir vorschlagen
und die mit den Daten der Wissenschaft besser übereinstimmt, so ist es einleuchtend,
daß die flüchtigen Chloride, welche entstehen müssen, nämlich die Chloride des
Arseniks, Antimons, Eisens, Zinks, sich verflüchtigen werden, während das
Kupferchlorid und Oxychlorid, welche in der Gangart geblieben sind, durch eine
zweckmäßige Auslaugung gewonnen werden können.
Dieß ist die von den Erfindern aufgestellte Theorie, welche nothwendig berichtigt
werden muß; denn wenn man diesen Hüttenproceß gehörig ausführen und nöthigenfalls verbessern will, so
muß man die wissenschaftlichen Grundsätze, auf denen er beruht, gehörig kennen.
Wenn, wie die Erfinder behaupten, das Kupferoxyd, ohne durch das Kochsalz zersetzt zu
werden, in Kupfer-Oxychlorid verwandelt würde, so müßte man nothwendig
annehmen, daß das Natrium des Kochsalzes auf Kosten des im Wasserdampf enthaltenen
Sauerstoffs in Natron übergeht, während der frei gewordene Wasserstoff
Chlorwasserstoffsäure bildet, die ihrerseits das Kupferoxyd angreift. Diese Reaction
kann aber nicht stattfinden, weil die Chlorwasserstoffsäure und das Natron sich
unvermeidlich und unmittelbar in Kochsalz und Wasser umwandeln würden, so daß also
kein Resultat erfolgen würde. Nimmt man aber auch diese Theorie an, so würde dennoch
keine Bildung von Oxychlorid stattfinden, während gerade hierauf die Erfinder ein
besonderes Gewicht legen.
Unsere Theorie ist folgende:
Indem das Chlornatrium auf das Kupferoxyd einwirkt, bildet sich in Folge einer
doppelten Zersetzung einestheils lösliches Kupferchlorid, und anderntheils Natron,
welches sich dann mit der Kieselerde zu Natronsilicat verbindet. Die anderen im Erz
enthaltenen Metalloxyde werden auf ähnliche Weise chlorirt. Da das Natronsilicat
übrigens (obwohl in geringerem Grade) die alkalischen Eigenschaften des Natrons hat,
so erscheint es uns zweckmäßiger für den Erfolg des Processes zu seyn, das Kochsalz
und die Kieselerde auf schwefelsaure Metalloxyde reagiren zu lassen. Die frei
gewordene Schwefelsäure würde alsdann das Natronsilicat zersetzen, um neutrales
schwefelsaures Natron zu bilden, welches auf eine Lösung von Kupferchlorid keine
Wirkung ausübt.
Nach dieser Abschweifung fahren wir fort den Gang der Arbeit zu beschreiben, und zwar
mit Beihülfe der beigegebenen Abbildungen, von denen Fig. 15 einen
Querdurchschnitt nach der Linie XY der Fig. 16 und
Fig. 16
einen Grundriß der Anordnung der Betriebsapparate darstellt.
M Raum, welcher die aus den Röstöfen kommenden Erze
aufnimmt.
A Gefäße zum Auslaugen des Erzmehls.
B Gefäße zur Aufnahme der zu fällenden Lösung.
C Gefäße zum Fällen der Oxyde.
D Gefäße zum Absetzen des Niederschlags und zum
nachherigen Abziehen des Wassers.
R Gerenne für die Rückstände.
G Gerenne in welchen das Wasser herbeigeführt wird.
G' Gerenne für die Herbeiführung des Kalkwassers.
G'' Becken worin das Kalkwasser bereitet wird.
E Treppen.
F Oefen zum Trocknen der Oxyde.
P Esse.
Das auf angegebene Weise chlorirte Erz wird in ein länglich viereckiges Gefäß A gebracht, dessen Boden durchlöchert ist und mit
Strohbündeln, die als Filter dienen, bedeckt wird; es werden etwa 4/5 der Höhe des
Kastens mit Erzmehl angefüllt. Man feuchtet alsdann die Masse nach und nach mit
geringen Wassermengen an, und wenn man annehmen kann, daß sie gänzlich durchdrungen
ist, füllt man das Gefäß bis zum Rande mit Wasser an, welches jedoch nicht auf
einmal eingelassen wird. Die aufgelösten Metalltheile fließen in ein zweites Gefäß
B von gleichen Dimensionen ab, welches auf einer
zweiten Ebene so angebracht ist, daß sein Rand mit dem Boden des ersten Gefäßes A gleich liegt. Sobald das Gefäß B gefüllt ist, leitet man aus dem Gefäße. G''
mittelst des Gerennes G' eine gewisse Quantität
Kalkmilch herbei; man rührt die gemischte Lösung nach allen Richtungen durch, und
läßt sie alsdann in das Concentrationsgefäß C ab, worin
sich der Niederschlag absetzt. In dem Maaße als sich der Absatz verdichtet, zieht
man das klar geworbene Wasser durch einen Hahn ab, um in das Gefäß C wieder Lösungen geben zu können. Zuweilen wendet man
Aschenlauge zum Fällen der Oxyde an, dieß hängt aber von der Menge der Asche ab,
welche man beim Verbrennen von Holz und Reisig auf den Rosten der Röstflammöfen
erhält. Weit zweckmäßiger würde es seyn, die Fällung durch Eisen zu bewirken, man
verwirft aber dieses Mittel als zu theuer. Nachdem der Niederschlag im Absetzgefäß
D eine teigige Consistenz erlangt hat, wird er
mittelst Schaufeln ausgeschlagen und auf eine benachbarte Sohle, welche bedeckt,
aber gehörig gelüftet ist, geworfen, oder sogleich auf die Sohle eines der
Trockenöfen F gebracht, wo die Masse, ehe sie zu den
Schmelzöfen gelangt, getrocknet wird. Hiermit ist nun das Verfahren auf dem nassen
Wege beendigt.
Ehe man einen zweiten Auslaugeproceß beginnt und hierzu den Rückstand aus den Gefäßen
schafft, probirt man ihn mittelst Ammoniak, ob er eine blau gefärbte Flüssigkeit
liefert. In diesem Falle enthält er noch Kupfer, und man muß alsdann eine gewisse
Wassermenge, die mit Schwefelsäure angesäuert ist, herbeiführen, welche die
unaufgelöst gebliebenen Oxydtheilchen angreift und auflöst.
Um 10 Tonnen oder 200 Ctr. chlorirtes Erz zu rösten, auszulaugen, zu fällen und die
Oxyde zu trocknen, sind sechs bis acht Tage erforderlich. Diese sogenannten Oxychloride haben das Ansehen einer leichten, etwas
lockern Erde von grünlicher Färbung; sie gewähren ein Ausbringen, welches bis auf ein
Zehntel, dem ganzen durch die chemische Analyse gefundenen Kupfergehalt des
behandelten Erzes entspricht und enthalten 25 bis 30 Proc. metallisches Kupfer.
Ich habe eine Probe dieses Oxychlorids an das Probirbureau der Pariser Bergschule
gesandt; sie gab folgende Resultate:
Sand und Kieselerde
6,0
Eisenoxyd und Thonerde
4,6
Zinkoxyd
2,6
KupferoxydKupferchlorid
26,8 4,4
= 24,12 Kupfer
schwefelsaurer Kalk
38,8
Wasser
16,8
–––––
100,0
Eine zweite, von dem Chemiker F. Weil vorgenommene
Analyse, gab dieselben Resultate.
Schmelzproceß. – Diese Oxyde werden hernach auf
dem trockenen Wege reducirt; man setzt sie in einem kleinen Freiberger Krummofen
durch. Sie sind natürlich leichtflüssig und erfordern nur 1 Theil Kohle auf 3 bis 4
Theile, je nachdem die Masse mehr oder weniger trocken ist.
Das Resultat des ersten Schmelzens besteht in armen Kupferschlacken, in Stein mit 45,
50 und 55 Proc. Kupfer, und in wenigem Schwarzkupfer.
Dieser Stein wird auf gewöhnliche Weise geröstet und gibt dann bei einem zweiten
Schmelzen Schwarzkupfer und wenige Schlacken, die so reich sind daß sie einem
folgenden Schmelzen auf Stein zugeschlagen werden können.
Das Schwarzkupfer wird hernach im kleinen Herde gahr gemacht.
Wir werden unten die Hüttenkosten, welche das Verfahren auf dem nassen Wege
veranlaßt, mittheilen. Zur Würdigung des Werthes dieses Verfahrens geben wir jetzt
eine Uebersicht der Processe, wodurch arme Erze auf gewöhnliche Weise, d.h. auf dem
trocknen Wege zugutegemacht werden.
Wenn die Kupfererze sehr reich sind, so ist ihr Zugutemachen sehr einfach. Durch
Rösten werden sie in Oxyde verwandelt, dann auf Schwarzkupfer verschmolzen, dessen
Gahrmachen, je nach der Beschaffenheit der Gangarten und dem Vorhandenseyn von
Eisen, mehr oder weniger langwierig oder schwierig ist.
Ganz anders verhält es sich aber, wenn, wie es am häufigsten der Fall ist, die Erze
arm sind; solche sind auch fast stets geschwefelte und mit andern Schwefelmetallen
verbunden, daher sehr unrein. Sie müssen zuvörderst behufs des Anreicherns einer
mechanischen Aufbereitung unterworfen werden, wodurch sie einen Theil ihrer
unhaltigen Gemengtheile oder Gangarten verlieren, welche sich ihrer Reduction
widersetzen oder einen zu hohen Brennmaterialaufwand veranlassen würden.
Diese unerläßlichen, vorbereitenden Processe sind sehr verschieden und hängen von
einer Menge örtlicher Eigentümlichkeiten ab. Die Aufbereitungskosten belaufen sich
per Tonne aufbereiteten Erzes auf 30, 45 bis 50 und
60 Francs und oft höher, abgesehen von den unvermeidlichen Verlusten, welche bei den
Wäscharbeiten vorkommen und nicht unter 25 bis 30 Procent betragen. Sehr häufig ist
diese Concentration unmöglich, entweder weil die Gangart des Erzes aus Schwefelkies
oder andern ähnlichen Mineralien besteht, die eine fast gleiche Dichtigkeit mit dem
Kupferkies haben, oder weil sich der Kupferkies in so feinen Theilchen in der
Gangart eingesprengt findet, so daß sie bei der Aufbereitung mit dieser verloren
gehen würden. Nenn man solche Erze vollständig abrosten und dann auf Schwarzkupfer
verschmelzen wollte, so würde man ungeheure Verluste erleiden, die man durch
unvollständiges Rösten und wiederholte Schmelzprocesse vermeidet; durch letztere
erhält man Kupferstein, der sich bei jedem Schmelzen mehr concentrirt, wobei sich
Arsen und Antimon, die fast immer in geschwefelten Kupfererzen vorkommen,
verflüchtigen und das Schwarzkupfer auch reiner von Eisen wird, sich daher leichter
und mit geringerm Abgange gahr machen läßt.
Dieses Verfahren wendet man auf sehr vielen deutschen Kupferhütten, z.B. am
Unterharze an; es ist sehr complicirt und langwierig, und beansprucht ohne die
mechanische Aufbereitung 7, 8 bis 9 verschiedene Hüttenprocesse, nämlich wiederholte
Röstungen und Schmelzungen, sowie wiederholtes Gahrmachen, ehe Gahrkupfer erlangt
wird. Soll nun eine solche Zugutemachung Vortheile gewähren, so muß man wohlfeiles
Brennmaterial benutzen können. Im Allgemeinen verbraucht man beim Zugutemachen von
Erzen mit 10 bis 12 Proc. Kupfergehalt 1 Theil Holzkohle auf 1 Theil Erz, um reines
oder gahres Metall darzustellen; in den Hütten zu Swansea in Wales verbraucht man
sogar auf 1 Theil Erz 11/2 bis 1 3/4 Theile Steinkohlen (freilich von sehr geringer
Güte).
Bei weniger reichen Erzen und theurern Kohlen wird natürlich der Kupferhüttenbetrieb
weit kostbarer und hin und wieder mißlich. Daher hat man auch, wo keine günstigen
Umstände behülflich sind, das Zugutemachen der armen Erze fast überall
aufgegeben.
Es ist sehr schwierig, die Produktionskosten des auf trocknem Wege erzeugten Kupfers
für Erze mit einem Gehalte von 1 1/2, 2 bis 4 Proc. genau zu bestimmen. In den
verschiedenen Hütten auf dem Continent, die wir zu besuchen Gelegenheit hatten und
welche durch geringe Ankaufspreise der Materialien begünstigt werden, betragen die
Hüttenkosten, bei Erzen von 4 bis 4 1/2 Proc. Metallgehalt, mit Inbegriff der
Brennmaterialien, der Zuschläge, der Abnutzung der Gezähe, der Arbeitslöhne, per 100 Kilogr. Gahrkupfer 76 bis 120 Francs, und bei
ärmern Erzen von 1 1/2 bis 2 Proc. Gehalt, 260 bis 280 Fr. und darüber.
Um die vielen Nachtheile und großen Schwierigkeiten, womit die Verhüttung armer
Kupfererze verbunden ist, zu heben, sind zahlreiche Gewinnungsmethoden auf dem
nassen oder dem elektrochemischen Wege erfunden worden
und es werden dergleichen noch fortwährend erfunden.Die bis Ende 1854 bekannt gewordenen derartigen Processe findet man
aufgeführt in Kerl's metallurgischer Hüttenkunde,
Bd. II S. 273 etc. Von diesen Processen haben nur wenige die versprochenen Resultate geliefert,
nicht sowohl wegen ihres relativen Werthes, als wegen der zu ihrer Ausführung
verwendeten unerfahrenen Arbeiter und wegen zu bedeutender Anlagekosten. Mehrere von
diesen Methoden zur Cementkupfergewinnung werden jedoch mit Vortheil angewendet, wie
z.B. zu Stadtbergen in Westphalen und zu Linz am Rhein.Kerl a. a. O. S. 277.
Das von Becchi und Haupt
herrührende Verfahren hat mit den erwähnten Processen einige Aehnlichkeit und
ermöglicht, wie diese, das Zugutemachen der armen Kupfererze, welche im Toscanischen
und in andern Ländern sehr ausgedehnt vorkommen; wenn es aber, wie zu
Capanne-vecchie, mit gutem Erfolg angewendet wird, so ist dieß nur eine
einzeln stehende Thatsache, die seine Unfehlbarkeit nicht beweisen kann. Es wurde
später zu Temperino in der Campigliese eingeführt, scheint aber dort keine so
genügenden Resultate gegeben zu haben. Rührt dieß nun von der geringen
Geschicklichkeit der Arbeiter, von der Beschaffenheit der Erze, oder von der
unvollkommenen Röstung her? Wir können uns nicht darüber aussprechen; ohne den Werth
der Erfindung zu schwächen, liefert der geringere Erfolg am letzterwähnten Orte nur
den Beweis, daß neue Versuche gemacht werden müssen, ehe das Verfahren definitiv
angenommen werden kann. Dieß ist aber bei fast allen neuen Erfindungen der Fall; die
meisten gelingen erst nach zahlreichen Versuchen.
Wir glauben jedoch, daß der schlechte Erfolg des Processes zu Temperino hauptsächlich
von der Unvollkommenheit der Haufen- und der Ofenröstung herrührt. Die oben
(S. 104) erwähnten Reactionen werden nur auf Kupferoxyd ausgeübt, denn das Schwefelkupfer kann
durchaus nicht chlorirt werden. Die ganze Menge des Schwefelkupfers, welche das der
fraglichen Behandlung unterzogene geröstete Erz enthält, wird in dem unlöslichen
Rückstand der Operation vollkommen unangegriffen zurückbleiben.
Das Gesagte wird vollständig durch die Resultate der Analyse des gerösteten Erzes, welches man zu Temperino zu gute zu machen versucht hat, bestätigt; der schon erwähnte
Hr. Weil hat diese Analyse mit der größten Sorgfalt
ausgeführt.
Das geröstete Erz enthält in 100,000 Theilen:
Halb-Schwefelkupfer
KupferSchwefel
1,9000,480
2,380
Kupferoxyd
KupferSauerstoff
1,4900,548
1,866
Eisenoxyd, Schwefeleisen,
ThonerdeZinkoxyd, Schwefelzink
32,269
Schwefelsäure mit einem Theil der
Oxyde verbunden
1,370
kieselige Gangart (in den Säuren
unlöslich)
62,115
–––––––
100,000
Gesammter Schwefelgehalt des Erzes
4,66 Proc.
–––––––––
Metallisches Kupfer in dem
Schwefelkupfer
1,90
Metallisches Kupfer in dem
Kupferoxyd
1,49
–––––––––
Gesammter Kupfergehalt des gerösteten
Erzes
3,39 Proc.
Die Analyse Weil's zeigt daher, daß das geröstete Erz von
den 3,39 Proc. metallischen Kupfers, nur 1,49 Proc. als Oxyd enthält, und daß
folglich das Kupferausbringen durch das fragliche Verfahren in keinem Fall diese
letztere Zahl übersteigen kann, weil die 1,90 Proc. metallisches Kupfer, welche im
geschwefelten Zustande noch im Erz enthalten sind, in den Rückständen des Processes
unangegriffen verbleiben.
Man hat deßhalb bei dem zu Temperino mit jenem Erz unternommenen Betriebe zu keinen
guten Resultaten gelangen können.
Aus diesen Thatsachen darf man folgern, daß wenn es gelänge, das sämmtliche in dem
Erz enthaltene Kupfer zu oxydiren, das Ausbringen wahrscheinlich dem
Gesammt-Kupfergehalt des Erzes nahe kommen würde.
Wir haben nun noch den Betrieb des neuen Verfahrens zu Capanne-vecchie in Beziehung auf die Kosten zu verfolgen. Diese
Selbstkosten sind auf einen Posten von 10,000 Kilogr. Erz, welche gewöhnlich in
einer Campagne verarbeitet werden, berechnet. Die betreffenden Angaben beruhen auf
unseren eigenen Untersuchungen, sowie auf den uns mitgetheilten Hüttenbüchern und
Rechnungen.
Die zerschlagenen und grob geschiedenen Erze werden in Haufen von 250 bis 300 Tonnen
geröstet. Die Gewinnungs- und Förderungskosten bis auf die Halden, dann die
Kosten für das Zerschlagen und Scheiben betragen zusammen per Tonne 7 bis 8 Francs.
Erster Proceß. – Haufenröstung. 300
Tonnen.
Arbeitslöhne. – Die Herrichtung der Rösthaufen
mit Holzbett und
Holzkohlenschichten
150 Lire.
Holzkohlen. – 15 Lasten oder 2250 Kil. à 7 Lire die Last
110 „
Holz.
– 550 Reisigbündel, jedes 3 Kil. an Gewicht,
und 1500 Kil. Scheitholz à 25 Lire
155,05 „
––––––––––
Zusammen
415,05 Lire.
––––––––––
Es kosten daher 10 Tonnen (10,000
Kilogr.) 14 Lire oder
11,70 Fr.
Zweiter Proceß. – Zermahlen. 10
Tonnen.
Abnutzung der Mühlsteine,
Transport der gerösteten Erze zur Mühle,
Pochen, Zermahlen, Transport des Erzmehles zu
den Röstöfen, zusammen beiläufig 24 Lire
per 10 Ton., oder
18,32 Fr.
Dritter Proceß.
–
Röstung und Chlorirung.
Dauer der Röstung: 2 1/2–3
Stunden; die 10 Tonnen bilden 2
Chargen für den Doppelröstofen mit
Sohlen zu beiden Seiten des Herdes:
400
Reisbündel, Ankauf und Transport
16 Lire
250 Kilogr.
Kochsalz
36 „
Arbeitslöhne
für 4 Röster und 2 Gehülfen
10 „
Reparatur
und Unterhalt der Gezähe
0,10 „
–––––––
Zusammen
62,10 L.
52,50 Fr.
Vierter Proceß.
– Auslaugung und Fällung.
Transport des Erzmehls von den Oefen nach
den Auslauggefäßen, Füllen und Entleeren
derselben; Fällen durch Kalk, Ablassen
der Flüssigkeiten, Trocknen der Oxyde,
an Gedinge à 2 Lire
die Tonne, für 10 Tonnen
20,00 L.
Schwefelsäure
von 35°, die 100 Kil. 24 L.
10,00 „
Gebrannter
Kalk, 500 Kil.
6,00 „
Holz zum
Trocknen der Oxyde
1,10 „
–––––––
Zusammen
37,10 L.
31,50 Fr.
–––––––––
Gesammtsumme
114,02 Fr.
Man erhält am Ende dieser verschiedenen Processe 600 bis 650 Kilogr. Oxyd, welches
mehr oder weniger Kalk und im Durchschnitt, nach den dortigen Proben, 28 bis 30
Proc. Kupfer enthält. Es ist jedoch anzunehmen, daß diese Proben nicht sehr genau
sind, denn nach den oben angeführten Analysen beträgt der Metallgehalt nur 24,12
Proc.
Rechnet man der obigen Geldsumme 1/10 für unvorhergesehene Kosten, Abnutzung und
Reparatur der Apparate, Verluste, Versehen etc. hinzu, so gelangt man zu der runden
Summe von etwa 125 Francs, daher die Productionskosten von 100 Kil. 20 bis 21 Fr.
(also für 1 Zollctr. 2 2/3 bis 2 5/6 Fr.) betragen.
Die Oxyde werden auf dem trocknen Wege reducirt; man wendet zu Capanne-vecchie
den Freiberger Krummofen dazu an, dessen Construction nichts Eigentümliches
darbietet. Es sind bei dem Betriebe desselben 8 Arbeiter beschäftigt, welche 15 Fr.
Lohn erhalten. In 24 Stunden werden 10 Tonnen Oxyd mit 18 Last oder 2700 Kil.
Holzkohle, welche 110 Francs kosten, durchgesetzt. Ein Flammofen, mit einem zur
Verbrennung von Holz vorgerichteten Rost und von geringeren Dimensionen als die
gewöhnlichen, würde wohl zweckmäßiger zur Reduction so leichtflüssiger Substanzen
seyn.
Man erhält, wie schon oben bemerkt wurde, reichen Stein und Schwarzkupfer; der
geröstete Stein wird auf Schwarzkupfer verschmolzen, dessen Gehalt 90 bis 92 Proc.
beträgt.
Vor Einführung der beschriebenen Methode betrugen zu Capanne-vecchie die
Förderungs-, Aufbereitungs- und Schmelzkosten per 1000 Kil. aufbereitetes Erz 29 bis 30 Francs, und man gewann daraus
kaum 11 bis 12 Kil. Gahrkupfer. Dieselben Verhältnisse findet man in manchen Hütten
des westlichen Deutschlands, wie am Unterharz, in Hessen etc., obgleich der Preis
der Materialien den Betrieb begünstigt, wo sich aber die Kosten per 1000 Kil. auf 200 bis 250 Fr. belaufen. Zu Szaska im
Banat sollen jedoch die Gestehungskosten nur 178 Fr. betragen.
Bei dem jetzt zu Capanne angewendeten gemischten Verfahren gewinnt man 16 bis 18
Kilogr. Gahrkupfer mittelst einer Ausgabe von 10 bis 15 Francs.
Faßt man die obigen Daten zusammen, so ergeben sich als Productionskosten für 100
Kilogr. Gahrkupfer:
Erz, 5500 Kilogr.
Nasser Weg.
– Oxyde, 425 bis 450 Kilogr.
85
Fr.
Schmelzung.
– Schmelzkosten und
Darstellung des Kupfersteins
12 Fr.
Rösten und Schmelzen des Steins auf
Schwarzkupfer
18,50 „
Gahrmachen
5
„
––––––
35,50 „
––––––––
Summe
120,50 Fr.
Das beschriebene neue Verfahren verdient daher wegen seiner einleuchtenden Vortheile
schon jetzt, ungeachtet der Verbesserungen welche es in der Folge erhalten wird, die
Beachtung des praktischen Hüttenmannes in hohem Grade. Es zeichnet sich besonders
dadurch aus, daß man die armen Erze ohne andere Aufbereitung als eine Handscheidung
auf der Halde, benutzen kann, daß es keine kostbaren und lange Zeit beanspruchenden
Anlagen erfordert, daß der Betrieb nicht viel Zeit erheischt und in jeder
bestehenden Hütte eingeführt werden kann, da die neuen Anlagen sich auf die Räume
zum Auslaugen und Fällen beschränken. Auch findet bei dem neuen Verfahren im
Vergleich mit den bisherigen Methoden der geringste Metallverlust statt.Das Verfahren der HHrn. Vecchi und Haupt ist auf dem ganzen Continent, in England
und in den Vereinigten Staaten patentirt (die Beschreibung des Patents,
welches sich Hr. Hähner für dasselbe in England
ertheilen ließ, wurde im polytechn. Journal Bd. CXLIII S. 439
mitgetheilt).Ohne im geringsten das Verdienst der Erfinder beeinträchtigen zu wollen,
bemerke ich, daß schon die alten Dokimasten, unter andern Orschall, das Kochsalz zum Ausbringen des Kupfers
aus seinen Erzen angewendet haben. Ich selbst habe seit 1843 das Kochsalz
bei der Behandlung der Blenden benutzt. Petitgand.
Tafeln
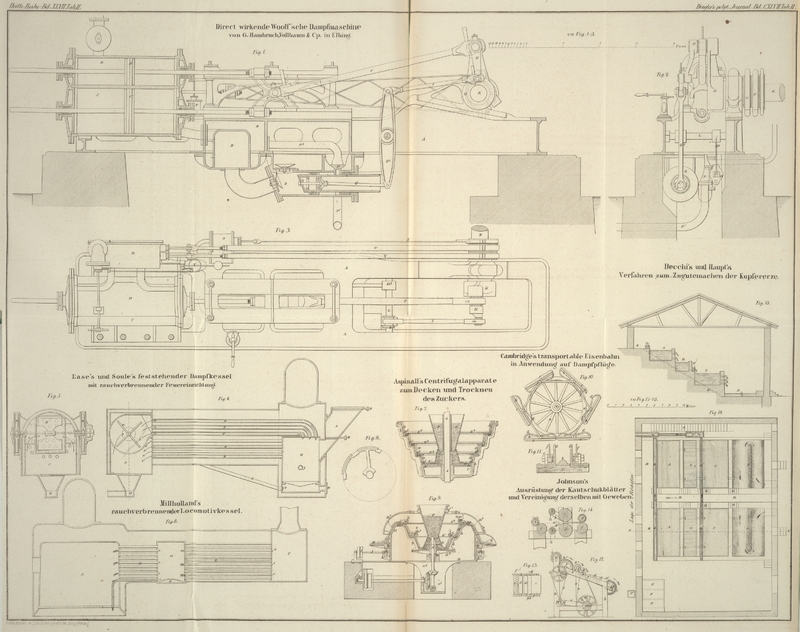