Titel: | Hafnerei-Betrieb der Messingfabrik zu Achenrain in Tirol; vom Hütteningenieur Bethmann. |
Fundstelle: | Band 156, Jahrgang 1860, Nr. XXXIV., S. 114 |
Download: | XML |
XXXIV.
Hafnerei-Betrieb der Messingfabrik zu
Achenrain in Tirol; vom Hütteningenieur Bethmann.
Aus Hartmann's allgemeiner berg- und
hüttenmännischen Zeitung, 1860, Nr. 13.
Mit Abbildungen auf Tab.
II.
Bethmann, über den Hafnerei-Betrieb der Messingfabrik zu
Achenrain in Tirol.
1. Anfertigung der
Messingschmelztiegel.
Das Material zur Anfertigung derselben bilden:
1) die von alten, nicht mehr zu verwendenden Schmelztiegeln
gebliebenen Ueberreste,
2) Passauererde,
3) Graphit.
Die von alten, nicht mehr zum Guß tauglichen Schmelztiegeln gebliebenen Ueberreste
werden sauber von Schlacken und sonstigen schädlichen Bestandtheilen gereinigt, in
einem Pochwerke zerkleint und durch ein feines Sieb geschlagen.
Dasselbe geschieht mit der Passauererde.
Die Passauererde bezog man aus der Nähe von Passau. Dieselbe hat eine dunkelgraue
Farbe, ist bituminös, wenig sandig und scheint der Steinkohlenformation
anzugehören.
Den Graphit endlich bezog man ebenfalls aus Passau. Es ist auffallend, daß der
Graphit zur Anfertigung von Schmelztiegeln aus dem Auslande, aus Passau, bezogen
werden muß, da doch Oesterreich selbst sehr reich an Graphit ist. Von Hafnerluden in
Mähren und von Schwarzbach in Böhmen gehen jährlich Tausende von Centnern nach
England und Amerika. Der Hauptgrund davon liegt in dem hohen Kieselerdegehalt, und
mögen die beigefügten Analysen darüber Aufklärung geben.
Die Proben sind in Rothglühhitze in Sauerstoff verbrannt, und die erhaltene Asche
analysirt.
Es ergab sich in dem Graphit von
Hafnerluden:
von Schwarzbach:
von Passau:
57 Proc. Asche
12,5 Proc. Asche
38 Proc. Asche
49,2 Kieselerde
5,1 Kieselerde
26,4 Kieselerde
0,1 Kalkerde
0,8 Eisenoxyd
1,2 Eisenoxyd
6,5 Eisenoxyd
7,0 Thonerde
6,1 Thonerde
25,1 Thonerde.
Gewöhnlich besteht die Mischung aus
3 Theilen Schmelztiegelsand und
1 Theile Passauererde.
Diese Mischung variirt jedoch, indem man zu den schon zu sehr ausgebrannten Tiegeln,
deren Masse daher trockener und spröder ist, etwas mehr Passauererde und etwas neuen
Graphit zusetzt. – Dieser nach obigen Verhältnissen zusammengeschüttete Sand
wird circa 1/2 Stunde nach allen Seiten umgeschaufelt,
und muß dieß sehr sorgfältig geschehen, weil sich diese pulverige Masse schwer
vermischen läßt. – Ist dieß geschehen, so setzt man frisches Wasser zu und
mengt diese Masse tüchtig durch. Den so entstandenen Teig läßt man hierauf etwa 12
Stunden zum Anziehen liegen, tritt denselben nach dieser Zeit mehrere Stunden durch,
je nachdem er weicher oder härter ist, schlägt ihn hierauf in einen Haufen dicht und
fest zusammen und deckt ihn mit einem leinenen Tuche zu, damit die Oberfläche nicht
hart wird, sondern eine gleichmäßige Frische behält. Dieser Proceß des Abtretens
geschieht so 8 Tage lang hinter einander; dann bleibt diese Masse 8 bis 10 Tage
ruhig zugedeckt liegen, nur ist dabei darauf zu achten, daß nicht durch
Temperatur-Einflüsse ein Theil mehr oder der andere weniger austrocknet, und
daher ist ein öfteres Umdrehen erforderlich. Durch die Anhäufung und Bedeckung entsteht eine Gährung,
Wärmeerzeugung und damit eine Auflockerung der Masse, die späterhin bei Anfertigung
der Tiegel durch Schlagen, resp. Pressen, aufgehoben wird. Hat diese Masse nun die
richtige Festigkeit erlangt, so beginnt die Anfertigung der Tiegel.
Die Anfertigung der Tiegel kann auf zweierlei Weise geschehen: entweder macht man
dieselben in einer Form, oder man fertigt sie auf einer Drehscheibe an.
a) Anfertigung der Schmelztiegel in einer Form.
Man nimmt zu so viel Böden, als man am folgenden Tage Tiegel zu machen gedenkt,
von der betreffenden Masse, ballt sie mit der Hand zu Kugeln und läßt sie etwas
trocknen. Diese so geballten, etwas mehr getrockneten Kugeln schlägt man in die Form (Fig. 28, abcd), die auf einem mit Graphit gepuderten
Untersatze (Fig. 29) steht, und macht den Boden des Tiegels daraus. Hierauf nimmt
man von der etwas frischeren Masse und schlägt die Form mittelst eines Stoßkolbens (Fig. 30) bis oben
fest voll, wodurch die Seitenwände des Tiegels entstehen. Jetzt wird der Kern (Fig. 31)
eingetrieben, die über der Form hervorquellende Masse mit einem Draht
abgeschnitten, der Kern ausgehoben, angefeuchtet, und dann damit die inneren
Flächen des Tiegels durch Drehung desselben fest ausgerieben, so daß ein nasser
Glanz entsteht, und alle noch vorhandenen Unebenheiten verschwinden. Ist dieß
geschehen, so läßt man den so entstandenen Tiegel einen Tag in der Form stehen,
öffnet hierauf die aus zwei Hälften bestehende Form und setzt den Tiegel auf ein
mit Graphit gepudertes Bret zum Trocknen. Die Tiegel können luftig stehen,
dürfen jedoch der Sonne nicht ausgesetzt seyn; auch müssen dieselben auf dem
Brete mindestens einmal täglich gedreht werden, damit sie nicht ankleben.
Außerdem muß man dieselben täglich sorgfältig besichtigen, ob nicht kleine
Luftbläschen oder Risse entstanden sind. Die Bläschen öffnet man mit einem
Messer und drückt dieselben hierauf ebenso wie die Risse sorgfältig mit der Hand
zu. Dieses Verfahren muß so lange fortgesetzt werden, bis die Tiegel fest und
ausgetrocknet sind.
b) Anfertigung der Schmelztiegel auf der Drehscheibe.
Man verfährt zu Anfang wie oben, läßt die Masse zu den Böden ebenfalls etwas
trocknen, nimmt die geballten Kugeln und macht den Boden daraus, indem man den
Kern auf die Drehscheibe (Fig. 32, ab) steckt und so die Masse darauf
festschlägt. Hierauf nimmt man ebenfalls von der etwas frischeren Masse, schlägt
vom Boden an (der bei diesem Verfahren oben ist) nach Unten zu die Seitenwände des
Tiegels um den Kern fest, bis der Tiegel zu seiner bestimmten Höhe gelangt ist.
Jetzt wird das Drehholz (Fig. 33, ab) angehalten, und die Drehscheibe sammt
Kegel und darauf befindlichem Tiegel mit dem Fuße gedreht, bis der Tiegel eine
glatte und gleich starke Hülle erhalten hat. Ist der Tiegel nun so weit
gediehen, so hebt man ihn sammt Kern von der Drehscheibe ab, dreht beide Theile
um, und setzt dieselben auf ein mit Graphit eingepudertes Bret; worauf der Kern
vorsichtig ausgehoben wird, und der Tiegel frei zum Trocknen stehen bleibt.
Die Behandlung dieser Tiegel beim Trocknen ist dieselbe, wie bei denen in der
Form angefertigten.
Die auf der Drehscheibe angefertigten Tiegel haben vor denen, die in Formen
gemacht werden, den Vortheil, daß man keine Formen braucht, und dieselben gleich
nach ihrer Vollendung frei zum Trocknen hinstellen kann; es ist jedoch die
Anwendung der Formen bei kleineren Tiegeln eine Nothwendigkeit, da ein Boden von
nur geringem Durchmesser bei sofortigem Aufsetzen ohne Form die Last der
Seitenwände nicht tragen und der Tiegel zusammenstürzen würde.
In früheren Zeiten, als die Messingfabrik noch Eigenthum des k. k.
österreichischen Aerars war, bezog man die Schmelztiegel aus
Groß-Almerode bei Cassel in Hessen und wurden dieselben hinsichtlich
ihrer Güte sehr geschätzt; auch wurden Graphittiegel aus Passau (daher der Name
Passauer Tiegel), welche aus einem Gemenge von 2 Theilen Graphit und 1 Th.
feuerfestem Thon angefertigt sind, bezogen und zum Schmelzen vorzüglich
brauchbar gefunden.
Diese Schmelztiegel ertrugen hier durchschnittlich 30 Güsse. Dieselben
Anforderungen kann man allerdings noch nicht an die hier gefertigten stellen;
doch haben dieselben bei sorgfältiger Behandlung schon 20 bis 25 Güsse
ertragen.
Die Stärke der Wände richtet sich nach der Größe des Tiegels; ebenso die letztere
nach der Art des Gießens und der Construction der Schmelzöfen. Der Verfasser
wird später bei Beschreibung der Schmelzöfen darauf zurückkommen.
2. Anfertigung der feuerfesten
Steine.
Einen Hauptbetriebszweig der Hafnerei bildet noch die Anfertigung feuerfester Steine.
Achenrain ist die einzige Fabrik Tirols, wo feuerfeste Steine erzeugt werden. Die
Consumtion derselben ist bei der großen Anzahl von Fabriken, welche sich in
unmittelbarer Nähe befinden, nicht unbedeutend, und geschieht die Anfertigung
derselben wie folgt:
Die zur Anfertigung feuerfester Steine nöthigen Materialien sind:
1) Passauererde,
2) Quarz oder reiner Quarzsand;
3) werden hier die alten feuerfesten Brocken verwendet.
Die Passauererde ist dieselbe, wie die bei den Schmelztiegeln verwendete, und wird
auch ebenso bearbeitet.
Quarz aus älterem Gebirge wird geglühet, mit Wasser abgelöscht, dann gestampft oder
zerkleint und durch ein betreffendes Sieb geschlagen.
Quarzsand aus Flötzgebirgen muß rein seyn, und darf keine Eisentheile enthalten. Ein
Versuch mit Säuren genügt, den Eisengehalt zu erkennen.
Dieser Quarzsand wird durch ein Sieb von höchstens 1 Millimeter großen Oeffnungen
geschlagen, dann rein gewaschen und getrocknet.
Die alten, noch vorhandenen feuerfesten Brocken werden in einem Pochwerke zu Pulver
zerkleint, und, je nachdem die anzufertigenden Steine mehr oder weniger Hitzgrade zu
ertragen haben, durch ein feineres oder gröberes Sieb geschlagen. Dieses so
erhaltene Pulver wird im trockenen Zustande mit einem Gemenge von 2 Theilen
Quarzsand und 1 Theile Passauererde, welche Bestandtheile wie oben angeführt
bearbeitet seyn müssen, vermischt, mit Wasser angefeuchtet, zwei bis dreimal mit den
Füßen durchgetreten und umgeschaufelt.
Die Erfahrung hat gelehrt, daß ein verhältnißmäßiger Zusatz von Holzkohlenklein unter
diese Masse dieselbe nicht allein bei der Bearbeitung zäher und bindender macht,
sondern dem Steine auch im gebrannten Zustande eine schwammigere Eigenschaft gibt.
Es ist eine größere Ausdehnung und Zusammenziehung möglich und ein Zerspringen
derselben nicht zulässig. Der Verfasser hat diese Methode seit einer Reihe von
Jahren in Anwendung gebracht; auch ist dieselbe zweckmäßig bei Kohksöfen-
oder sonstigen Feuerungs-Thüren, wo eine feuerfeste Masse angewendet wird, um
die eisernen Thüren vor dem Zerspringen zu schützen.
In Belgien wendet man fälschlich statt des Holzkohlenkleines Sägespäne an, und sind
dieselben nicht anwendbar wegen ihres Gehaltes 1) an Wasser, 2) Gerbsäure, und weil
sie 3) den Stein zu porös machen.
Holzkohlenklein dagegen ist: 1) wasserfrei, 2) Raum ausfüllend, und 3) dadurch den
Stein fester machend, ohne Spaltungen, die durch den Zusatz von Sägespänen wegen
deren Dampferzeugung hervorgebracht werden.
Nachdem nun diese so zubereitete Masse mehrere Stunden zum Anziehen still gelegen,
kann dieselbe in die betreffenden Formen (Fig. 34, ab) eingeschlagen werden. Dieß sind einfache Holzkasten ohne
Boden und Deckel, welche dieselbe Form haben, als man den Steinen geben will. Um ein
leichteres Ausheben zu erreichen, wird die Form vorher mit einem sehr feinen, gut
trockenen Sande eingepudert. Nachdem die Form vollgeschlagen und abgestrichen ist,
schlägt man dieselbe auf ein ebenfalls eingepudertes Bret um, hebt sie vorsichtig ab
und läßt den Stein trocknen. Dieß geschieht entweder in freier Luft, oder in einem
geheizten Locale. Bei gutem Wetter trocknen diese Steine, je nach Verhältniß ihrer
Größe, in 5 bis 8 Tagen so weit aus, daß sie in den Brennofen (Fig. 35, abc) eingesetzt werden können. Die Steine werden
so in den Ofen eingesetzt, daß die kleinsten Zwischenräume wenigstens 3/4 Zoll
betragen und mehrere Hauptzüge von 4 Quadratzoll gebildet werden, um ein
gleichmäßiges Durchziehen der Flamme und dadurch ein gleichmäßiges Brennen der
Steine zu erzielen.
Hat man einen neuen Ofen, so muß derselbe natürlich, bevor man ihn zum Brennen
benutzen kann, gut ausgetrocknet werden.
Der Proceß des Brennens der Steine zerfällt in drei Theile:
1) Anwärmen des Ofens. Es wird etwas Holzkohle auf den
Rost geworfen und angezündet, und ein mäßiger Luftzutritt bewirkt, so daß der Ofen
in eine gelinde Temperatur gesetzt wird. Die Farbe der Steine wird durch den
verlorenen Wassergehalt dunkler.
2) Vorfeuern. Es werden in steigender Menge Holzsplitter
zugesetzt. Die Farbe der Steine wird Heller.
3) Stärkste Hitze. Es wird fort gefeuert. Die Steine
nehmen eine weißglühende Farbe an.
Dieß ist das Zeichen, daß dieselben ganz durchgebrannt sind. Jetzt wird das Feuer
eingestellt, der ganze Ofen möglichst luftdicht verschlossen und so eine langsame
Abkühlung bewirkt. Werden die Steine im heißen Zustande aus dem Ofen entfernt, so
verlieren dieselben ihren Klang und ihre Farbe; sie verblassen, indem sie zu schnell
Feuchtigkeit anziehen; sie bekommen Risse und fangen an zu bröckeln.
Es ist daher unbedingt nöthig, die Steine, bevor man sie ausbricht, im Ofen erst
abkühlen zu lassen.
Tafeln
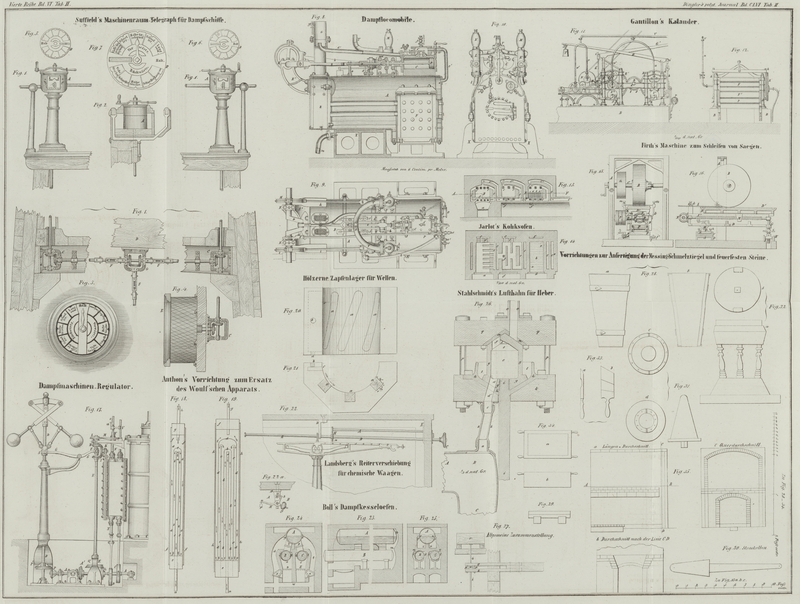