Titel: | Der Kryolith-Sodaofen; von Prof. Julius Thomsen in Copenhagen. |
Autor: | Julius Thomsen [GND] |
Fundstelle: | Band 167, Jahrgang 1863, Nr. XCV., S. 363 |
Download: | XML |
XCV.
Der Kryolith-Sodaofen; von Prof. Julius
Thomsen in Copenhagen.
Mit Abbildungen auf Tab.
V.
Thomsen, über den Kryolith-Sodaofen.
Die Zersetzung des Kryoliths bezüglich der Sodafabrication geschieht mittelst
kohlensaurem Kalk auf trocknem Wege. Schon lange bevor ich die erste
Kryolith-Sodafabrik gründete, hatte ich mich überzeugt, daß nur diese
Zersetzung eine zweckmäßige und ökonomische Fabrication gestattet, und daß die
ebenfalls von mit entdeckte Zersetzung des Kryoliths auf nassem Wege für technische
Zwecke sich bedeutend kostspieliger stellt.
Die Zersetzung des Kryoliths mittelst Kalkstein wird durch Erwärmung der Mischung
unterstützt; sie tritt schon weit unter der Glühhitze ein, wenn die Bestandtheile
sehr fein gepulvert sind, wird jedoch erst vollständig, wenn die Temperatur die
Nothglühhitze erreicht. Da aber die Mischung von Kryolith und Kalkstein bei einer Temperatur,
welche die Rothglühhitze nur wenig übersteigt, schon zu schmelzen beginnt, und es
für den nachfolgenden Auslaugeproceß von außerordentlicher Bedeutung ist, daß die
Masse nicht bis zum Schmelzen erwärmt wird, so ist die Zersetzung auf dem trocknen
Wege von besonderen Schwierigkeiten begleitet. Die Zersetzung geschieht bekanntlich
im Flammofen; die Temperatur des Ofens muß aber zwischen bestimmten, ziemlich engen
Grenzen liegen. Ist der Ofen zu warm, dann schmilzt die Mischung; ist er zu kalt,
dann geht die Zersetzung nicht vollständig von statten. Ferner ist die Mischung des
Kryoliths mit Kalkstein ein schlechter Wärmeleiter, und der Ofen kann deßhalb nur
mit einer dünnen Schicht beschickt werden. In den gewöhnlichen Flammöfen ist eine
zweckmäßige Zersetzung nicht zu erreichen; die Temperatur des Ofens muß nämlich so
gleichförmig seyn, daß ein homogenes Product erzielt werden kann, ohne eine sehr
hohe Feuerbrücke und einen dadurch bedingten sehr bedeutenden Kohlenverbrauch. Bei
den gewöhnlichen Flammöfen ist aber die Hitze größer in der Höhe der Brücke als in
der Höhe der Füchse; es findet also ein Temperaturunterschied nach der Länge des
Ofens statt; ferner geschieht die Erwärmung nur von oben, und es ist also ein
beträchtlicher Temperaturunterschied dicht am Herd und an der Oberfläche der
Beschickung. Diese Uebel lassen sich durch fleißiges Umrühren der Masse nicht
beseitigen, denn es bilden sich stets geschmolzene Theile, welche beim Umrühren die
halbgebrannten Theile umschließen und der Zersetzung entziehen. Die Asche (die
geglühte Mischung) eines solchen Ofens enthält stets viele Klumpen, welche theils
unzersetzte, theils geschmolzene Masse enthalten und sich nur sehr schwierig und
theilweise auslaugen lassen. Ist die Asche aber gut geglüht, dann bildet sich eine
poröse Masse ohne Staub und ohne Klumpen von solcher Härte, daß sie sich mit der
Hand nicht zerdrücken läßt.
Ich bin daher gezwungen gewesen, für die Kryolith-Sodafabrication einen
besonderen Ofen zu construiren, bei welchem eine gleichmäßige Temperatur durch seine
ganze Länge dadurch erreicht wird, daß derselbe mit zwei entgegengesetzten
Feuerungen, deren Hitze theils direct, theils indirect wirkt, versetzen ist. Die
Construction dieses Ofens, Fig. 30–33, ist
folgende:
Der Herd C des Ofens ist aus feuerfesten Thonplatten von
20 Zoll im Quadrat und 3 Zoll Dicke gebildet; die Platten ruhen auf gemauerten
Pfeilern, welche 9'' im Quadrat halten und 12'' hoch sind. Die Pfeiler sind so
versetzt, daß die Flamme von der Feuerung A sich unter
dem ganzen Herd regelmäßig vertheilt. Die drei vordersten Pfeiler, welche dem Feuer
am nächsten sind, müssen aus sehr feuerfesten Steinen hergestellt werden. An den Seiten herum ruhen
die Platten auf den Seitenmauern, welche unter dem Herd 2 Zoll dicker als über
demselben sind. Der untere Zug D, E, welcher also die
Breite des ganzen Herdes hat und nirgends eine geringere Höhe als 12 Zoll, geht bei
E in die zweite Feuerung B; an dieser Stelle, unter der Feuerbrücke H,
steigt die untere Fläche so, daß der Zug nur 5–6 Zoll Höhe behält. Die
vereinigte Flamme der beiden Feuerungen zieht dann über den Herd nach den Füchsen
I, I, und durch diese in den Canal K, welcher durch die ganze Breite des Ofens geht. Der
Canal K communicirt: 1) hinten mit dem Canal L, welcher zum Hauptzugcanal N hinuntergeht, kann aber durch den Schieber O
von diesem abgesperrt werden; 2) mit der Oeffnung m,
welche die Flamme in den Raum P, zwischen dem Gewölbe
und den Pfannen F, leitet. Dann geht der Zug durch die
Füchse Q, Q, Q in den horizontalen Canal R, welcher durch S mit dem
Hauptcanal in Verbindung steht. – Ist der Schieber T geschlossen, der Schieber O dagegen offen,
so geht die Flamme aus dem Ofen direct in den Hauptcanal, ohne die Pfannen zu
erwärmen; ist aber O geschlossen und T offen, dann geht der Zug unter den Pfannen hin.
Die beiden Röste sind gleich groß, 3 Fuß lang und 15 Zoll breit; die Roststäbe sind
Stabeisen von 5/4 Zoll im Quadrat; die Schürlöcher U und
O sind mit beweglichen Thonplatten zu schließen. Die
Vordermauer W der Feuerung, welche 18 Zoll dick ist, ist
nicht mit den Seitenmauern verbunden; sie ruht auf den eisernen Balken y und z, und wird oben durch
ein Gewölbe X geschlossen. Dadurch wird es möglich, eine
Reparatur an den Feuerungen, den einzigen Stellen welche von der Hitze stark
angegriffen werden können, auszuführen, ohne daß die übrigen Theile des Ofens dabei
leiden; die Reparatur beschränkt sich dann auf das Herausnehmen dieses kleinen
Theiles der Vordermauer. Bei einem Ofen, welcher jetzt 8 Monate lang im Betriebe war
und gegen 1000 Tonnen Asche verarbeitet hat, ist noch keine solche Reparatur nöthig
gewesen. – Die Fabrik Oeres und besitzt jetzt zwei solcher Oefen, welche
täglich 10 Tonnen Asche liefern; der eine Ofen ist seit 10, der andere seit 8
Monaten im Betriebe; eine Reparatur des ersten Ofens zeigte, daß das Gewölbe über
der Feuerung A die einzige Stelle ist, wo der Ofen
angegriffen wird und nach der Verstärkung dieses Gewölbes wird hoffentlich eine
Reparatur, welche beiläufig nur acht Tage dauert, bloß einmal jährlich erforderlich
seyn. – Durch das fleißige Reinigen des Rostes mittelst eines eisernen Hakens
wird derselbe stets frei von Schlacke erhalten.
Durch die Feuerbrücke H geht ein Canal a, welcher kalte Luft durch kleine Oeffnungen in der
gegen den Feuerraum B gekehrten Seite leitet, wodurch
die Brücke abgekühlt und der Rauch besser verbrannt wird.
Die Seitenmauern b, b müssen besonders gut fundirt
werden, da die Stabilität des Ofens wesentlich darauf beruht. Das Gewölbe ist 9 Zoll
dick aus vertical stehenden Steinen gemauert und steht ganz frei. Die Fugen gehen
der Länge des Ofens parallel, und das Hauptgewölbe bildet mit dem Gewölbe über dem
Rost B ein zusammenhängendes Ganzes mit fortlaufenden
Fugen. Die Verankerung (Armirung) des Ofens besteht aus gußeisernen Platten von 3' × 2', 3 Stück an
jeder Seite, welche durch ein Parallelogramm, das auf die Mitte jeder Platte drückt,
gegen die Seitenmauern gehalten werden; dadurch wird der Druck des Gewölbes
vollständig unschädlich gemacht, welches bei der Armirung ohne Waagebalken nicht
erreicht werden kann. Die vorderste der oberen eisernen Stangen, welche der Flamme
von m am meisten ausgesetzt ist, wird mit einem eisernen
Rohr oder mit thönernen Röhren umgeben.
Um die Canäle K und R
reinigen zu können, werden an passenden Stellen Löcher angebracht. Deßgleichen
befinden sich in der einen Seitenmauer vermauerte Löcher von 5 Zoll im Quadrat, um
den unteren Zug zu reinigen; diese Löcher liegen zwischen je zwei Reihen von
Pfeilern. Der Ofen kann aber jahrelang gehen, ohne daß der untere Zug D, E sich mit Asche füllt.
Die Arbeitslöcher d, d werden stark überwölbt, da dieses
Gewölbe einen Theil des Druckes des Hauptgewölbes tragen soll.
Die Beschickung des Ofens geschieht durch die Trichter 6. Es ist Sorge zu tragen, daß
die Pfannen, welche auf dem Ofen angebracht werden, von Anfang an dicht sind, damit
keine Lauge durch dieselben auf das Gewölbe dringt.
Der Herd des Ofens hat einen Flächenraum von 96 Quadratfuß; seine Breite ist 8 Fuß
und die ganze Länge 13 Fuß. Der Ofen wird täglich 12 Mal beschickt, jedesmal mit
1000 Pfund (500 Kilogr.), und er verarbeitet also täglich etwa 6 Tonnen Mischung,
entsprechend 2 1/2 Tonnen Kryolith. Die Heizung geschieht mit Steinkohlen, wovon
täglich circa 4/5 Tonnen verbrannt werden, also 1/7 bis
1/8 vom Gewicht der Mischung. Durch die vom Herd abziehende Wärme wird in den auf
dem Ofen stehenden Pfannen gleichzeitig das ganze Eindampfen der Sodalaugen bis zur
Krystallisation erreicht, und ehe der Rauch in den Schornstein gelangt, zieht er
unter einer eisernen Platte von etwa 60 Quadratfuß Fläche hin, auf welcher das
Trocknen des Kalksteins erfolgt. Für einen täglichen Verbrauch von 50 Centner
Kryolith sind also zum Glühproceß, zum Abdampfen der Laugen und zum Trocknen von 75 Centnern
porösen Kalksteins im Ganzen 16 Centner Steinkohlen hinreichend.
Ueber die Zweckmäßigkeit dieses Ofens kann jetzt kein Zweifel mehr stattfinden.
Erstens ist der Verbrauch an Brennmaterial sehr gering,
er beträgt nur 1/7 bis 1/8 des Gewichts der Mischung; zweitens gibt er ein durchaus gleichförmiges Product, denn die Asche wird
durch und durch glühend, ohne daß irgend ein Theil derselben schmilzt, so daß sie
leicht und vollständig ausgelaugt werden kann, und drittens ist die Zersetzung des Kryoliths so vollständig, daß die Ausbeute
fast den theoretischen Werth erreicht: es geben nämlich 100 Pfund reiner
Kryolith 197 Pfund Soda, während die theoretische Ausbeute 204 Pfund beträgt, so daß
also wenigstens 96 1/2 Procent des Kryoliths zersetzt werden, und dieses Resultat
wird durch ein dem fabrikmäßigen Auslaugen ganz analoges Verfahren erreicht, ohne
daß die Asche zerschlagen oder zerrieben wird, und ohne daß man sie genauer
auslaugt, als es in der großen Fabrication geschehen kann.
––––––––––
Bezüglich eines kürzlich in diesem JournalS. 199 in diesem Bande. erschienenen Aufsatzes des Hrn. Directors Dittmar
„über den Ofen des Harburger Alaunwerks“ habe ich noch ein Paar
Worte hinzuzufügen.
Die Zersetzung des Kryoliths geschah in der Copenhagener Fabrik anfangs, in den
Jahren 1857–1859, in eisernen Retorten, von denen je drei in einem kleinen
Ofen lagen. Die durch die Zersetzung entwickelte Kohlensäure, deren Gewicht ungefähr
1/5 des Gewichts der Mischung von Kryolith und Kalkstein beträgt, wurde für die
Sättigung der Lauge verwendet. Da die entwickelte Kohlensäuremenge dreimal so groß
als die zur Sättigung der Lauge erforderliche ist, und da der Lauge reine
Kohlensäure geboten wurde, so konnte die Sättigung in kleinen Apparaten und in
kurzer Zeit (3–5 Stunden) geschehen, während die Sättigung mit Kohlensäure
vom Kohksofen sehr große Apparate erfordert und 9–12 Stunden dauert.
Die sich damals stets erniedrigenden Preise der englischen Soda, welche bekanntlich
jetzt über 40 Proc. niedriger sind als vor fünf Jahren, machten eine große Oekonomie
nothwendig. Nur in einer Beziehung konnte aber eine größere Oekonomie eintreten,
nämlich im Glühproceß, und dieser Theil der Fabrication ist der einzige, welcher
seit dem Beginn der Fabrication eine Modification erlitten hat.
Im Winter 1859–1860 ließ ich daher zwei Flammöfen bauen, welche nach demselben
Princip wie die oben beschriebenen Oefen construirt und nur kleiner waren, so daß
sie bloß mit einer Feuerung versetzen wurden. Der Herd
war ebenfalls aus großen Steinplatten hergestellt; die Flamme zog unter dem Herd hin
und kehrte oberhalb desselben wieder zurück, so daß also der Herd von unten und die
Beschickung gleichzeitig von oben erwärmt wurde. Die Feuerung war an demselben Ende
angebracht wie die Arbeitslöcher, so daß die stärkere Erwärmung durch Strahlung vom
Feuer und die durch die Arbeitslöcher bewirkte Abkühlung sich gegenseitig
neutralisirten, und der Herd eine gleichförmige Hitze erhielt. Die Asche aus diesem
Ofen war in allen Beziehungen derjenigen gleich, welche aus den oben beschriebenen
Oefen erhalten wird, porös und ohne geschmolzene Theile. Der Vortheil dieser
Flammöfen war also erwiesen; es war der Kohlenverbrauch und die Handarbeit geringer,
und die Asche stets von homogener und vorzüglicher Beschaffenheit.
Als ich im Jahre 1860 durch verschiedene Geschäfte abgehalten wurde mich mit dem
Detail der Fabrik zu beschäftigen, wurde ein Chemiker, Hr. Göcker, bei derselben angestellt. Die Fabrication sollte in diesem Jahre
vergrößert werden, und es waren also neue Oefen nothwendig. Anstatt nun die
Erfahrung zu benutzen, welche die von mit construirten Flammöfen geliefert hatten,
machte Hr. G. den Vorschlag, den gewöhnlichen Sodaofen einzuführen, obgleich hier
ganz andere Verhältnisse stattfinden als beim Sulfatofen, wo eine Schmelzung erzielt
wird. Meinem Rathe entgegen wurden zwei solche Oefen gebaut, um die Stelle der
früheren zu vertreten. Es ist also nicht ganz correct, wenn Hr. Dittmar sagt, daß Hr. G. die Retortenöfen als unpraktisch
verwarf, denn diese Construction war damals schon verlassen; es wäre correcter
gewesen, wenn er gesagt hätte, daß Hr. G. das Princip der kleinen Flammöfen verwarf,
eben dasjenige Princip welches jetzt an den oben beschriebenen großen Oefen
durchgeführt worden ist und sich als vollkommen zweckmäßig erwiesen hat. Das
praktische Resultat war, daß die Asche aus den neuen Oefen 87 Procent zersetzten
Kryolith ergab, während die kleinen Flammöfen und die Retortenöfen 93 Procent
zersetzten Kryolith ergeben hatten, und daß die Asche theilweise geschmolzen wurde,
wodurch zahlreiche Klumpen entstanden und der Auslaugeproceß sehr erschwert wurde.
Der Verbrauch an Brennmaterial war ein sehr bedeutender, nämlich für 50 Centner
Kryolith 12 Tonnen (66 Kubikf.) Kohks, während der von mit construirte Ofen für
dieselbe Menge Kryolith nur 5 1/2 Tonnen Steinkohlen verbraucht.
Während diese Oefen noch im Gange waren, wurde die Harburger Fabrik eingerichtet; die
Apparate wurden nach denjenigen, die sich damals in der Copenhagener Fabrik
befanden, copirt; mein Gutachten wurde nicht verlangt, und so wurde also in Harburg
der fragliche Ofen gebaut, wenige Monate bevor die entsprechenden Oefen in
Copenhagen als unpraktisch verlassen wurden. Hr. Director Dittmar wird sich erinnern, daß in Harburg die Ausbeute an Natron aus dem
Kryolith, wenigstens anfangs, sich sehr ungünstig stellte, und daß man in der
Harburger Fabrik den Grund in der Beschaffenheit des Kryoliths suchte. Die
wiederholten Klagen veranlaßten mich im Juli vorigen Jahres die Harburger Fabrik zu
besuchen, und ich fand da dieselben Nebel, an denen die Copenhagener Fabrik gelitten
hatte, in der Zeit wo die entsprechenden Oefen arbeiteten. Das theilweise Schmelzen
der Mischung, das Sieben der glühenden Asche, das Zermalmen und wiederholte Glühen
der Klumpen und das durch den unzweckmäßigen Glühproceß erschwerte Auslaugen der
Asche, waren die Ursachen, welche die Ausbeute verringerten und den Verbrauch an
Brennmaterial und Arbeitskraft vergrößerten. Ich gab Hrn. Dittmar den Rath, die Copenhagener Fabrik zu besuchen, und die dort
stattfindenden Verhältnisse zu untersuchen. Leider kam Hr. Dittmar nach Copenhagen während ich in London war; wäre dieser Fall nicht
eingetreten, so würde Hr. Dittmar von seiner Reise gewiß
eine größere Ausbeute gehabt haben; er würde sich dann durch Versuche mit sowohl
reinem als unreinem Kryolith überzeugt haben, daß die schwache Seite der Harburger
Fabrik wesentlich die Construction des Ofens ist, und daß die von mit construirten
Oefen, welche damals in Copenhagen arbeiteten, eine vollständige und zweckmäßige
Zersetzung hervorbringen.
Es ist mit unerklärlich, daß Hrn. Dittmar, wenn er nicht
mit einem von bedeutendem Vorurtheil befangenen Blick die Fabrication angesehen hat,
die Vollkommenheit der neuen Oefen entgangen ist; das bloße Ansehen des Products
wird jedem Sachverständigen zur Beurtheilung derselben fast schon genügen. Hr. Dittmar beruft sich auf Analysen, welche er mit Asche von
der Copenhagener Fabrik angestellt hat, und die ihm einen geringeren Natrongehalt
als die Harburger Asche ergab; dabei hat er aber nicht berücksichtigt, daß eine
Untersuchung der Asche für sich allein durchaus kein richtiges Resultat bezüglich
der Ausbeute aus dem Kryolith geben kann; ferner daß (wovon er sich durch
zweckmäßige Glühversuche überzeugen kann), gerade die hochgradige Asche eine
geringere absolute Ausbeute an Natron liefert, als wenn
die Asche etwas niedriger gehalten wird, wie es in Copenhagen geschieht.
Man kann nämlich vom Gewicht der Aschenprobe, welche zur Untersuchung verwendet wird,
nicht auf das Gewicht des der Asche entsprechenden Kryoliths schließen, denn dazu
muß man den Verlust beim Glühen (welcher etwa 20 Proc. beträgt) genau ermittelt
haben.
Die Controlversuche werden deßhalb in Copenhagen folgendermaßen angestellt: Es werden
1000 Pfund der Mischung von bekannter Zusammensetzung abgewogen und dem gewöhnlichen
zweistündigen Glühen unterworfen. Durch Wägen der Asche wird der Verlust
(Kohlensäure, Wasser etc.) bestimmt. Von der Asche werden zwei Mal 20 Pfund
abgewogen, ausgelaugt, auf Natron bestimmt und auf Kryolith berechnet. Das Mittel
aus zwei solchen nacheinander mit demselben Ofen angestellten Proben bildet das
Resultat. Auf diese Untersuchung gründet sich die Bestimmung, daß 100 Pfd. reiner
Kryolith eine Lauge geben, welche einen 194 bis 198 Pfund Soda entsprechenden
Natrongehalt zeigt, wovon sich jeder Sachverständige beim Besuch der Copenhagener
Fabrik überzeugen kann.
Der Werth des Harburger Ofens im Verhältniß zu den oben beschriebenen Oefen würde
sich leicht und bestimmt herausgestellt haben, wenn Hr. Director Dittmar in seinem Aufsatz zwei Zahlen mitgetheilt hätte,
nämlich die Menge des für 100 Centner Kryolith erforderlichen Brennmaterials und die
absolute Ausbeute an Natron oder Soda.
Hr. Dittmar nennt es einen Irrthum, daß die Apparate der
Harburger Fabrik eine Copie derjenigen der Copenhagener Fabrik seyn sollen; die
Originalität der dortigen Einrichtung, auf welche Hr. Dittmar Anspruch macht, reducirt sich aber wesentlich auf ein eisernes
Rollirfaß, das seit einigen Monaten in Harburg benutzt wird, um die Mischung, wenn
sie von den Kollergängen heruntergebracht ist, aufs Feinste zu zermalmen, wodurch
eine um circa 4 Procent höhere Ausbeute als früher
erzielt werden soll. Ein solcher Apparat kann vielleicht da von Nutzen seyn, wo die
Kollergänge von unzweckmäßiger Beschaffenheit sind; in der Copenhagener Fabrik aber,
wo die Asche 96,5 Procent zersetzten Kryolith zeigt, würde ein solcher Apparat nur
einem bedeutenden Kraftaufwand beanspruchen, ohne entsprechenden Nutzen zu
gewähren.
Hr. Dittmar ist noch stets der irrigen Meinung, daß nur
aus reinem Kryolith gute Producte dargestellt werden können, obgleich die fremden
Stoffe bloß aus Schwefelmetallen und Eisenspath bestehen; ich werde daher nächstens
die Fabricationsmethoden zum Gegenstand eines Aufsatzes machen.
Wenn endlich Hr. Dittmar der Meinung ist, daß ich
vergessen habe die großen Verdienste zu erwähnen, welche Hr. Göcker sich um die Kryolithindustrie erworben hat, so bin ich, der die
technischen Kenntnisse und den praktischen Werth des genannten Mannes kennt und
ehrt, der Meinung, daß
derselbe keine größeren Ansprüche auf große Verdienste bezüglich der
Kryolithindustrie machen wird, als Hr. Director Dittmar
selbst.
Tafeln
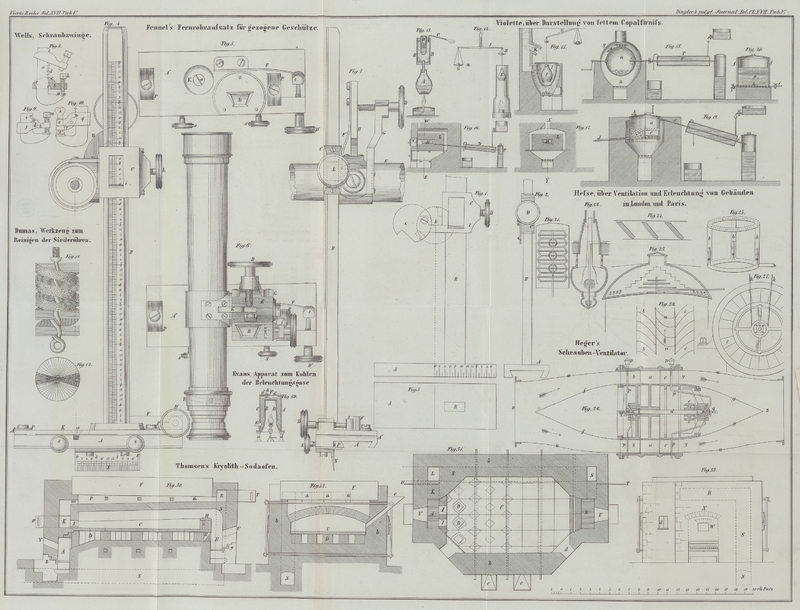