Titel: | Ueber die Fabrication schmiedeeiserner Scheibenräder für Eisenbahnwaggons; von Wilhelm Bansen, Walzwerksdirector in Bubna bei Prag. |
Fundstelle: | Band 202, Jahrgang 1871, Nr. L., S. 218 |
Download: | XML |
L.
Ueber die Fabrication schmiedeeiserner
Scheibenräder für Eisenbahnwaggons; von Wilhelm Bansen, Walzwerksdirector in Bubna bei
Prag.
Mit Abbildungen auf Tab.
IV.
Bansen, über Fabrication der schmiedeeiserner Scheibenräder für
Eisenbahnwaggons.
Die schmiedeeisernen Scheibenräder haben sich durch ihre einfache und solide
Construction, sowie durch ihre billige Anschaffung auf den norddeutschen,
französischen und belgischen Eisenbahnen rasch Eingang verschafft. Dieselben sind
eine Nachahmung des Bochumer Gußstahlrades und
concurriren in Norddeutschland auch mit demselben. Die schmiedeeisernen
Scheibenräder besitzen einige Aehnlichkeit mit den Ganz'schen Schalengußrädern, zeichnen sich vor diesen aber durch ihr größeres
Minder-Gewicht, ihre gefälligere Form und größere Widerstandsfähigkeit aus.
Vor dem Bochumer Gußstahlrad und dem Ganz'schen
Schalengußrad haben sie auch noch den großen Vorzug, daß, wenn der Laufkranz (Tyre)
abgenutzt ist, derselbe wie bei den Speichenrädern immer wieder erneuert werden
kann, was dem Bochumer Gußstahlrad und dem Ganz'schen
Schalengußrad abgeht.
So viel mit bekannt, wurde das erste schmiedeeiserne Scheibenrad in Deutschland auf
der Hermannshütte zu Hoerde in
Westphalen angefertigt
und ist es das alleinige Verdienst des rühmlichst bekannten früheren
Ober-Ingenieurs der Hermannshütte Hrn. R. Daelen,
die Fabrication dieses Zweiges in's Leben gerufen und auf die Vollkommenheit
gebracht zu haben, wie sie noch jetzt besteht und in kurzer Zeit auf noch vier bis
fünf anderen Eisenwerken Rheinlands und Westphalens eingeführt wurde.
Bevor die jetzt allgemein angewendete Methode der Fabrication durch Schmieden und
Walzen von den rheinischen und westphälischen Eisenwerken, welche Räder fabriciren,
als am rationellsten angenommen wurde, hat dieselbe mehrfache Phasen durchgemacht.
Der Erfinder, Hr. Ober-Ingenieur Daelen wollte
zuerst das Rad vermittelst Walzens herstellen. Zu diesem Behufe construirte er ein
Walzwerk bestehend aus zwei conischen Walzen, welche Fabricationsmethode aber aus
technischen Gründen, welche hier zu erläutern, zu weit abführen würde, verworfen
werden mußte.
Nach vielen anderen Versuchen, welche theilweise wohl gelangen, aber einem
rationellen Betrieb „das schmiedeeiserne Scheibenrad dem Bochumer
Gußstahlrad concurrenzfähig zu machen“ nicht entsprachen, kam Hr. Daelen auf die noch heute gebräuchliche Fabricationsart,
welche dem angestrebten Zweck entspricht, und die ich im Folgenden zu erläutern
suchen werde.
Das Material, welches zur Herstellung des Scheibenrades gewählt wird, muß ein gutes
gar gepuddeltes Korneisen seyn, damit es beim Façonschmieden keine
Kantenrisse erhalte und sich auch gut breiten lasse.
Die Packetirung geschieht am besten aus 3 nebeneinander liegenden, in 10–12
Bogen kreuzweise übereinander gelegten, 9 Linien starken Rohschienen (Luppen) a von circa 12 Zoll Länge
und 4 Zoll Breite, wodurch das Packet eine quadratische Form erhält (Fig. 16). Diese 10 bis 12
Lagen werden oben und unten mit circa 1 1/4 Zoll starken
Deckeln (Platten) b abgeschlossen, welche den Zweck
haben, daß die kreuzweise gelegten Lagen a sich beim
Einsetzen in den Schweißofen nicht verschieben und daß die fertigen Scheiben eine
glatte rißfreie Oberfläche erhalten.
So hergestellte Packete werden nun in einen gewöhnlichen Schweißofen chargirt,
nachdem sie Schweißhitze erhalten, unter einen 50 bis 60 Ctr. schweren Dampfhammer
gebracht und hier die Lagen durch mehrere volle Schläge fest aufeinandergeschweißt.
Nachdem eine feste Schweißung erzielt worden, wendet der Schmied das Packet auf dem
Amboß und formt es unter dem Hammer erst zu einem Achteck und geht in eine
cylindrische Form von circa 10 Zoll im Durchmesser über.
Hierbei hat der Schmied aber wohl darauf zu achten, daß die Deckel b des
Packetes und also auch die Lagen a, aus welchen dasselbe
gebildet ist, scheibenförmig gelagert bleiben.
Solche rund abgeschmiedete Packete kommen, nachdem eine Partie angesammelt wurde,
wieder in den Schweißofen, erhalten darin Weißglühhitze und werden unter demselben
Hammer, welcher jetzt aber Gesenke nach Fig. 17 erhalten hat, in
diese durch rasche und volle Schläge so lange eingetrieben, bis das Packet die
Gesenkformen a, a, welche die Nabe der Scheibe bilden,
ausgefüllt und die um die Nabe sich bildende Wulst b, b
eine Dicke von 2 1/2 Zoll erreicht hat.
Zur Fixirung der beiden Gesenke sowohl im Hammerbär als auch in der Chabotte dienen
die beiden Stifte c, c.
Die derart hergestellten Packete, jetzt Façonstücke genannt, werden nun so
rasch als möglich aus dem Gesenk herausgehoben, und nach einem in der Nähe des
Hammers liegenden Walzwerk mit nach Figur 18 geformten Walzen
gebracht und zwischen diesen Walzen, ohne weiter vorgewärmt zu werden, in der Weise
ausgewalzt, daß man das Façonstück durch die Walzen erst einmal unter Druck
Passiren läßt, es hierauf horizontal um 90 Grad dreht, wieder durch die Walzen läßt,
hierauf die obere Walze senkt und das Durchwalzen unter jedesmaligem Drehen der
Scheibe und Senken der Oberwalze so lange fortsetzt, bis die Scheibe das
vorgeschriebene Maaß erhalten hat.
Hierbei muß erwähnt werden, daß das Walzenpaar so construirt ist, daß ein Druck nur
auf den Scheibentheil a, a (Fig. 18) ausgeübt wird,
dieser also allein gestreckt wird, die Nabe b aber ohne
Druck die Walzen passirt, wie es auch aus der Figur ersichtlich ist.
Nachdem so die Scheibe vermittelst Walzens vollendet ist, wird dieselbe zum
Durchbiegen (Wellen) und zum Lochen unter einen zweiten ebenfalls in der Nähe des
Walzwerkes stehenden Dampfhammer von 50 bis 60 Ctr. Hammergewicht gebracht, welcher
mit Gesenken nach Fig. 19 versehen ist.
Die noch rothglühend von den Walzen kommende Scheibe wird auf das in der Chabotte
befestigte Amboßgesenk b (Fig. 19) gelegt, das
Obergesenk a auf die Scheibe aufgelegt und zwar mittelst
eines gabelförmigen Hebels, dessen Gabel sich in die beiden in das Obergesenk
eingegossenen Ohren einlegt und welcher wie jeder gewöhnliche Schmiedehebel auf
einer Laufschiene an einer Kette hängend am Hammer angebracht ist. Hierauf läßt man
den Hammer mehrere wuchtige Schläge auf das Obergesenk a
machen, in Folge dessen die Scheibe die Form der Gesenke annimmt.
Nachdem so die Durchbiegung geschehen, nimmt der Schmied einen bereit liegenden circa 3 Zoll im Durchmesser haltenden, 6 Zoll langen
Dorn, setzt denselben in die nur wenig stärkere Bohrung d des Obergesenkes, so daß er auf der Nabe aufsitzt, setzt auf diesen Dorn
einen zweiten, welchen er oberhalb des Obergesenkes mit einer Zange festhält, und
treibt den auf der Nabe aufsitzenden Dorn durch Schläge des Hammers auf den zweiten
Dorn in die Nabe. Er setzt dann, wenn der zweite Dorn so tief gegangen ist, daß er
ihn nicht mehr halten kann, einen dritten schwächeren Dorn auf den zweiten und läßt
den Hammer wieder auf den dritten Dorn wirken, wodurch der erste Dorn durch die Nabe
getrieben wird und das durch denselben ausgestoßene Eisen vor sich her schiebend in
die Oeffnung e, welche sich nach der Mündung zu stark
erweitert, austritt und durch die folgenden Dorne, welche noch nachgetrieben werden,
vollständig aus der Oeffnung e ausgetrieben wird.
Die letzten Dorne fallen dann, da sie schwächeren Durchmessers sind, leicht durch das
getriebene Nabenloch und durch die Amboßöffnung.
Das Amboßgesenk b ist an seinem oberen Umfang durch einen
schmiedeeisernen rothwarm aufgezogenen Ring r gebunden,
um ein Zerspringen desselben durch die harten Schläge des Hammers zu verhüten, Zu
demselben Zwecke ist auch das Obergesenk a an seinem
oberen Umfange mit einem rothwarm aufgezogenen Ringe armirt.
f ist eine halbkreisförmige eingedrehte Nuth, um den
abfallenden Cinder (Hammerschlacke), welcher sich durch die Schläge des Hammers beim
Erkalten der Scheibe von dieser ablöst, aufzunehmen, da sich sonst derselbe in die
Scheibenfläche einschlagen und die Scheibe ein rauhes, unansehnliches Aeußere
bekommen würde.
c ist ein schmiedeeiserner Ring zu dem Behufe eingelegt,
um bei einem etwaigen schiefen Einführen der Dorne das gußeiserne Gesenk b zu schützen, da der Ring c, wenn einmal beschädigt, leicht durch einen neuen zu ersetzen ist.
Die so weit fertigen Scheiben werden nun, da sie in ihrer Größe mehr oder weniger von
einander verschieden sind, auf einen Durchmesser beschnitten. Man stach dieselben zu
Anfang einfach auf Drehbänken ab, doch kam diese Art der Appretur wegen des
zeitraubenden Auf- und Abspannens der Scheiben und der für diesen Fall zu
geringen Leistungsfähigkeit der Drehbank, zu theuer zu stehen und man ging bald auf
folgendes Verfahren über. Die Scheiben wurden mittelst einer Reißspitze auf den zu
beschneidenden Durchmesser vorgezeichnet und unter einer gewöhnlichen
Schenkel-, respective Hebelschere, wie sie in Walzwerken allgemein
gebräuchlich sind, in der Weise beschnitten, daß die Scheibe vor der Schere in einer Kette
hängend, welche durch das Nabenloch durchgesteckt ist, und in der Höhe der
Schermesser auf einem unter der Nabe durch die Kette gehenden Vorsteckkeil
aufsitzend unter die Messer gebracht, erst in ein Vieleck und allmählich rund
beschnitten wird. Diese ganze Arbeit verrichtet nur ein Mann und ist die
Leistungsfähigkeit einer Schere die dreifache einer Drehbank.
Die Scheiben sind nun soweit fertig, daß dieselben zur Ausschweißung der
Unterbandage, das ist derjenigen Kranzfläche auf welche der Laufkranz (Tyre)
aufgezogen und befestigt wird, zur Vorbereitung kommen.
Fig. 20
stellt ein zur Ausschweißung der Unterbandage vorbereitetes Rad dar. a ist die beschnittene Scheibe, welche in die
kreisförmig gebogene Unterbandage c, deren
zusammenstoßende Enden verschweißt seyn müssen, fest eingepaßt wird. Der Schweißring
b wird zum Vorschluß aufgelegt und Unterbandage,
Scheibe und Schweißring mit drei Stück 1/2 Zoll starken Nieten, welche auf dem
ganzen Umfang gleichmäßig vertheilt sind, vernietet, damit bei der weiteren
Manipulation sich kein Theil ablöse.
Die Manipulation des Verschweißens der Unterbandage c mit
der Scheibe a und dem Schweißring b auf der ganzen Kreisfläche, ist eine der schwierigsten und wichtigsten
Arbeiten bei der ganzen Fabrication und muß mit großer Umsicht gehandhabt werden.
Die Schweißung wird unter einem 60 bis 190 Ctr. schweren Dampfhammer in einem
sogenannten Schweißamboß Fig. 21 vollzogen. Es ist
c' das gußeiserne Amboßgesenk, welches in der
Dampfhammer-Chabotte festgekeilt ist.
Um es vor dem Zerspringen durch die harten Schläge des Hammers zu bewahren, ist es
mit rothwarm aufgezogenen Ringen r armirt. b ist eine schmiedeeiserne Einlage, welche die
vorgeschriebene Wellenform der zu schweißenden Scheiben erhält; dieselbe wird mit 4
Stück 3/4 Zoll starken Setzschrauben an das Amboßgesenk befestigt. Für diese Einlage
b wurde Schmiedeeisen aus dem Grunde gewählt, weil
Gußeißen beim Schweißen einer größeren Anzahl von Scheiben radiale Risse bekam,
welche sich dann in die Scheiben einprägten und dadurch das Aussehen derselben
schädigten. a zeigt ein im Gesenk liegendes fertig
geschweißtes Scheibenrad. c ist das auf der fertig
geschweißten Scheibe ruhende Obergesenk; dasselbe ist im Hammerbär fest verkeilt und
wird mit demselben gehoben und fallen gelassen.
Das Verfahren beim Schweißen ist nun folgendes. Die nach Fig. 20 vorbereiteten
Scheibenräder erhalten in einem Schweißofen Schweißhitze. Nachdem der Schweißer den
richtigen Hitzegrad erkannt hat, hebt er das Scheibenrad mittelst einer an einer
Kette hängenden Gabel aus dem Ofen, bringt die Scheibe so schnell wie möglich nach dem
Hammer und legt dieselbe in das Gesenk c', dann läßt er
den Hammer mit dem daran befestigten Obergesenk c rasch
hintereinander 5 bis 6 volle Schläge machen, womit die Schweißung vollzogen seyn
muß. Hierauf wird der Hammerbär mit dem Obergesenk gehoben, die auf der Oberfläche
der Scheibe a angesammelten Schlacken abgekehrt und die
Scheibe mittelst der eingelegten Platte d, welche auf
dem Bolzen e ruht, durch Bewegung des Hebels f aus dem Gesenk gehoben. Die unter der Scheibe a angesammelten Schlacken werden ebenfalls weggekehrt,
hierauf die Scheibe horizontal um 90° gedreht, in das Gesenk wieder eingelegt
und die Scheibenfläche durch leichte Schläge und Begießen mit Wasser geglättet.
Die nun fertig geschweißten Scheibenräder werden aus dem Gesenk herausgehoben und zum
Erkalten bei Seite gelegt. Hierauf kommen die Räder zur Appretur auf die Drehbank;
hier werden die Nabenlöcher ausgebohrt und Unebenheiten in der Fläche weggedreht und
nach Vollendung dieser Arbeiten auf die Achsen mittelst Wasserdruck aufgezogen.
Nach diesem Aufziehen wird die Kranzfläche der Unterbandage, welche den Laufkranz
(Tyre) aufnehmen soll, auf den vorgeschriebenen Durchmesser abgedreht und der Tyre
in der gewöhnlichen und allgemein bekannten Weise rothwarm aufgezogen.
Zur Sicherung, daß sich der Tyre von der Unterbandage während des Betriebes nicht
ablöse, wird Tyre und Unterbandage mit auf. Fig. 22 und 23
verzeichneten Schrauben verschraubt und nachdem diese Arbeit geschehen, der
Laufkranz noch einmal überdreht, womit die Arbeiten beendet sind.
Fig. 22 zeigt
den Querschnitt eines fertigen Scheibenrades der bergisch-märkischen
Eisenbahn, Fig.
23 den Querschnitt eines Scheibenrades der Aachen Düsseldorfer Eisenbahn.
(Technische Blätter, Jahrg. 1871, Heft II und III, S. 213.)
Tafeln
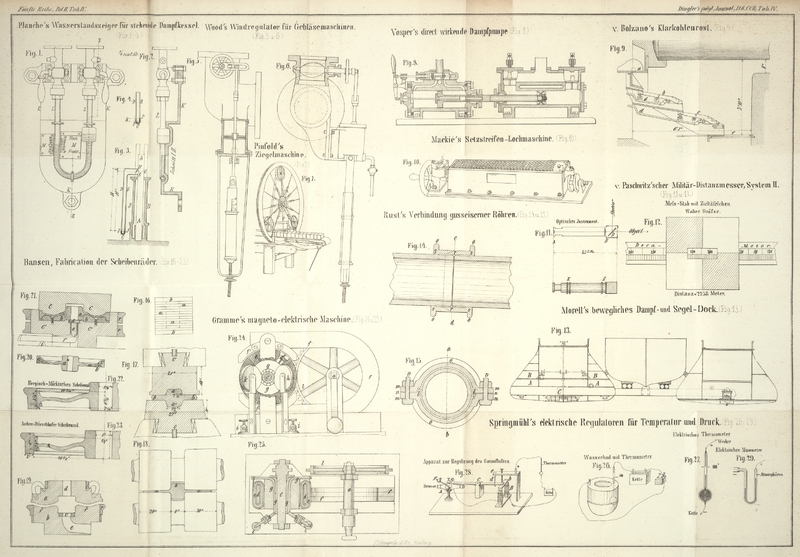