Titel: | Der continuirlich arbeitende Glasofen und Glashafen des Hrn. Friedr. Siemens zu Dresden; von Dr. Herm. Wedding zu Berlin. |
Fundstelle: | Band 204, Jahrgang 1872, Nr. LI., S. 190 |
Download: | XML |
LI.
Der continuirlich arbeitende Glasofen und
Glashafen des Hrn. Friedr.
Siemens zu Dresden; von Dr. Herm. Wedding zu Berlin.
Aus den Verhandlungen des Vereines zur Beförderung des
Gewerbfleißes in Preußen, 1871 S. 316.
Mit Abbildungen auf Tab.
IV.
Wedding, über den continuirlich arbeitende Glasofen und Glashafen
von Siemens in Dresden.
Das allgemein übliche Verfahren bei der Glasfabrication ist in großen Umrissen
folgendes: Die Materialien, aus denen das Glas gebildet werden soll, werden zu einem
Theile in Häfen eingetragen, deren mehrere in einem Ofen stehen. Bei ganz oder bis
auf eine kleine Oeffnung geschlossenen Arbeitslöchern wird die Masse bis zu ruhigem
Flusse eingeschmolzen; dann werden zur Füllung der Häfen in jeden noch zwei oder
mehrere Portionen des Glassatzes nachgegeben und diese ebenfalls geschmolzen, wobei
der Ofen allmählich seine höchste Temperatur erreicht (Heißfeuern). Der Inhalt wird nun behufs gleichmäßiger Vermischung
umgerührt, nochmals bei geschlossenen Arbeitslöchern stark erhitzt (Läutern), um die Masse so dünnflüssig zu machen, daß von
ihr noch eingeschlossene Gasblasen entweichen können, und dann bei ermäßigtem Zuge
wieder erkalten gelassen (Kaltschüren), bis die Masse die
zur weiteren Verarbeitung nöthige Consistenz hat.
Dieses Verfahren hat mehrere, übrigens längst anerkannte Mängel, welche wesentlich
auf folgenden Punkten beruhen:
1) Die Wärmemenge welche zum Schmelzen des Glases, d.h. zur
Bildung der Glasmasse aufgewendet wird, ist eine sehr große und die Temperatur eine
weit über den Schmelzpunkt gesteigerte, weil die zu schmelzenden, kalt eingesetzten
Stoffe in einer großen Masse aufgehäuft die Hitze nur sehr langsam auf sich
einwirken lassen. Die Wärme wird nämlich nur von den Hafenwänden aus nach Innen
abgegeben: es bildet sich zuerst außen eine geflossene Masse, welche ein sehr
schlechter Wärmeleiter ist und das Schmelzen der Masse im Inneren verzögert.
2) Auch das Läutern erfordert eine übermäßig hohe Temperatur,
weil die im Hafen befindliche verhältnißmäßig hohe Glassäule das Entweichen der in
den unteren Theilen eingeschlossenen Gasblasen nur gestattet, wenn die Masse äußerst
dünnflüssig ist.
3) Die für diese ersten Operationen aufgewendete Wärme geht in
der Periode des Kaltschürens zum größten Theile wieder verloren. Der Betrieb bedarf
daher einen im Vergleich zu der erforderlichen Wärmemenge ungemein hohen
Brennmaterialverbrauch.
4) In Folge der hohen Hitzegrade während des Schmelzens und
Läuterns, und in Folge des darauf folgenden erheblichen Temperaturwechsels leidet
das Material der Häfen und des Ofens stärker, als es bei einer gleichmäßigeren und
geringen Erhitzung der Fall seyn würde.
5) Die intermittirende Arbeit ist nicht geeignet, die zur
Bedienung des Ofens nöthigen Arbeitskräfte vollständig auszunutzen.
Die genannten Mängel haben schon seit langer Zeit zu Versuchen eines continuirlichen Schmelzens geführt. Diese Versuche haben
sich in zwei Richtungen bewegt: Man hat einerseits die Häfen ganz abgeworfen und den
Herd eines Flammofens an die Stelle gesetzt. So hat Donzel in Lyon bereits im Anfang der vierziger Jahre gearbeitet; aber er,
wie die übrigen, scheiterten daran, daß in einem ungetheilten Herde eine hinreichend geläuterte Glasmasse nicht
herzustellen war. Andererseits hat man die Häfen beibehalten, dieselben entweder
durch eine nicht bis auf den Boden reichende Scheidewand in zwei Abtheilungen
getrennt, deren eine die rohen Materialien, deren zweite die fertige Glasmasse
enthalten sollte, oder aber die in einem höher stehenden Hafen geschmolzene Masse
beständig in einen tiefer liegenden abfließen lassen. In den beiden letzteren Fällen
fehlt das so nothwendige Zwischenglied des Läuterns ganz, und beide Einrichtungen
haben sich daher nur für das Verarbeiten bereits einmal geschmolzener Glasbrocken bewährt, mithin eine sehr
beschränkte Anwendung gefunden.
Hr. Siemens zu Dresden hat nunmehr einen (ihm patentirten)
Ofen construirt, welcher auf Grund der richtigen Erfahrung, daß das specifische Gewicht der Glasmasse in dem Maaße wächst, als
die Schmelzung derselben vorschreitet, die geeignete Lösung des Problemes,
die angeführten Uebelstände der gegenwärtig üblichen Glasschmelzmethode zu
beseitigen, bietet.Wir verweisen auf den Bericht von Hrn. B. Friehling über den Siemens'schen
Glasschmelzofen mit continuirlichem Betriebe, im polytechn. Journal Bd. CCIII S. 14 (erstes Januarheft
1872). A. d. Red.
Dieser Ofen ist in Fig. 1 bis 4 abgebildet. Er ist
bezüglich der Feuerung in der bekannten Art der Regeneratorgasöfen eingerichtet und
erzeugt das Glas in einer einzigen Wanne, welche indessen
durch Zwischenwände in den Schmelzraum
A, den Läuterraum
B und den Arbeits-
oder Kühlraum
C getheilt ist. Die Flamme streicht über die Glasmasse
und erhitzt dieselbe nur von der Oberfläche aus. Die nach begonnener Schmelzung im
Raume A befindliche Glasmasse wird von Zeit zu Zeit mit
einer höchstens 40 Centimeter starken Schicht frischer Materialien bedeckt.
Dieselben werden von der Flamme erhitzt, aber die schmelzenden Theile rinnen sofort
nieder und sammeln sich mit fortschreitender Schmelzung nach dem specifischen
Gewichte an. Boden und Seitenwände sind zum Schutze gegen die Hitze mit
Luftkühlungen e, e', e'' versehen, in denen vermittelst
der kleinen Schornsteine s, s' die nöthige Circulation
erhalten wird. Diese Canäle haben auch noch den Vortheil, etwa durch die Fugen der
Wanne gehendes Glas von dem Eintritt in die tiefer gelegenen Regeneratoren
abzuhalten. Das am vollkommensten geschmolzene Glas befindet sich auf dem Boden des
Raumes A und wird von dort durch die Canäle a, a aufsteigend in die Läuterungsräume geführt, wo es
zuerst über eine gekühlte Brücke fließt. Hierbei kommt alles Glas zuvörderst an die
Oberfläche, erhält hier von Neuem Hitze und gibt, da es keinen Druck über sich hat,
leicht die eingeschlossenen Gasblasen ab. Das geläuterte Glas sinkt im Raume B wieder zu Boden. Vollkommen verarbeitungsfähig tritt
das Glas nun unter der Scheidewand v hindurch in die
letzte Abtheilung der Wanne C. Hier wird es nur noch
schwach erhitzt und kann mit dem richtigen Grade der Abkühlung durch die Oeffnungen
c, c entnommen und verarbeitet werden.
Die Flamme streicht, wie die Zeichnung zeigt, quer über die Wanne. Gas und Luft
strömen einzeln durch die abwechselnd stehenden Oeffnungen
g und l, während der
verbrannte Gasstrom durch die entgegengesetzt liegenden Oeffnungen in die Canäle G und L, die Regeneratoren
R und A, und von dort
zum Schornstein gelangt. Durch diese rechtwinkelig zur Längsachse des Ofens
geleitete Feuerung ist es möglich, jedem Ofentheile eine bestimmte Temperatur zu
ertheilen. Aus diesem Grunde ist auch die gekühlte Zwischenwand bis an die Firste
der Wanne geführt und dadurch der am meisten Hitze brauchende Schmelzraum A ganz von den übrigen Ofentheilen getrennt, während die
Zwischenwand v nicht bis an das Gewölbe der Wanne
reicht, damit ein Theil der Flamme in den Arbeitsraum streichen und diesen
hinreichend warm halten kann. Die Gas- und Luftcanäle g und l sind nach außen nur durch Thonglocken
verschlossen, so daß man durch sie leicht das Innere des Ofens beobachten kann.
Der Erfinder bemerkt zu der beschriebenen Einrichtung des Ofens mit Recht
Folgendes:
„Die Eigenschaft der Glasmasse, ihr specifisches Gewicht mit dem
fortschreitenden Schmelzzustande zu vergrößern, bildet zwar das diesem
Schmelzverfahren zu Grunde liegende Princip; derselbe Umstand ist aber auch die
Ursache aller Schwierigkeiten, welche sich dem Erfolge entgegenstellen, weil in
den Theilen der Wanne, in denen das Glas umgekehrt, d.h. von unten nach oben
steigt, eine Stagnation des specifisch schwereren Glases und folglich eine
allmähliche Entglasung desselben befördert wird.“
Um keinen praktischen Nachtheil aus diesem Umstande wachsen zu lassen, muß man vor
allen Dingen die aufsteigenden Passagen a bis auf das
geringste zulässige Maaß verengen; auch ist es vortheilhaft, den Arbeitsraum C nach unten zusammen zu ziehen oder ihn sehr flach zu
machen (26 Centimeter ist die Höhe der Glasmasse in der Zeichnung).
Sollte dennoch im Arbeitsraume mit der Zeit eine Entglasung eintreten, so muß der
Glasschmelzer ein Stückchen Holz auf den Boden bringen, um ein lebhaftes Aufwallen
der Glasmasse hervorzurufen.
Hr. Siemens hat dasselbe Princip auch auf Häfen angewendet, obwohl dabei offenbar viele Vorzüge,
welche der Wannenofen bietet, verloren gehen.
Fig. 5 bis
8 zeigen
einen solchen Hafen in den verschiedenen Durchschnitten. Auch hier ist A der Schmelz-, B der
Läuterungs-, C der Arbeitsraum. Der letztere ist
bedeckt. Der Raum A muß stets ganz oder nahezu voll
gehalten werden. Das geschmolzene Glas geht durch den Canal a in den Läuterraum B, sinkt hier wieder zu
Boden und tritt durch den Verbindungscanal b in den
Arbeitsraum C. Die Höhe des Glasspiegels nimmt in Folge
des zunehmenden specifischen Gewichtes in den drei Abtheilungen ab. Uebrigens ist
noch zu bemerken, daß in B sich ansammelnde, nicht
vollständig in Glas übergegangene Bestandtheile von Zeit zu Zeit abgezogen werden
müssen.
Der Erfinder hat den Wannenofen auf seiner Flaschenfabrik zu Dresden bereits seit
1870 in Betrieb und gefunden, daß die Leistung desselben stärker als die eines
daselbst arbeitenden zwölfhafigen Ofens gewöhnlicher Art ist. Die Mehrproduction
beträgt auf gleichen Brennmaterialaufwand bezogen über 50 Proc., die Production ist
pro Monat 180,000 bis 200,000 Flaschen.
Der Wannenofen erfordert 4 Mann zur Bedienung, während der zwölfhafige Ofen 5
Arbeiter erfordert. Die Glasmacher können dabei in zwölfstündigen Schichten
regelmäßig abwechseln, während bei dem gewöhnlichen Ofen 1/3 der Zeit verloren
geht.
Tafeln
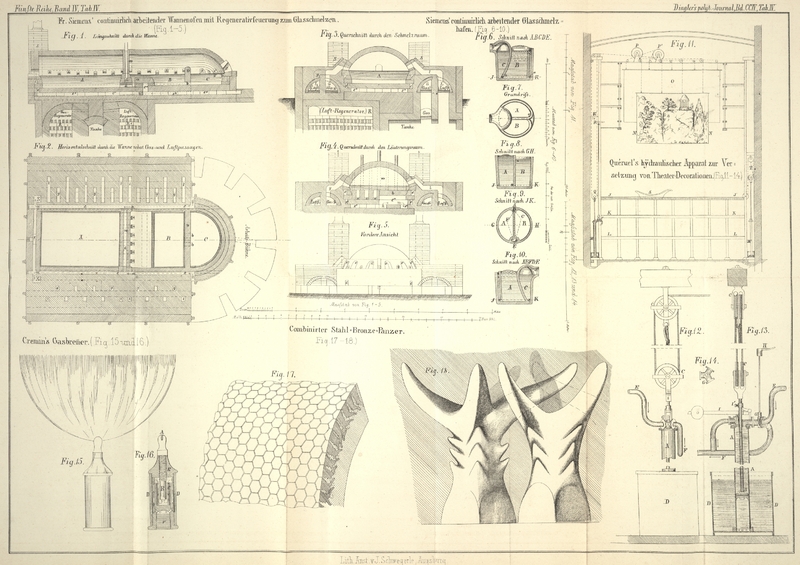