Titel: | Das Hargreaves'sche Verfahren der Sulfatfabrikation; von Dr. Georg Lunge (South-Shields). |
Autor: | Georg Lunge [GND] |
Fundstelle: | Band 218, Jahrgang 1875, S. 416 |
Download: | XML |
Das Hargreaves'sche
Verfahren der Sulfatfabrikation; von Dr. Georg Lunge (South-Shields).
Mit Abbildungen auf Taf.
X.
Lunge, über Hargreaves' Verfahren der
Sulfatfabrikation.
Ueber das Verfahren zur Darstellung von Sulfat (schwefelsaurem Natron oder
calcinirtem Glaubersalz des Handels), welches von James Hargreaves in Widnes erfunden und von demselben in Verbindung mit Robinson verbessert worden ist, sind in diesem Journale
schon vielfache Mittheilungen gemacht worden, und habe ich dasselbe ebenfalls in
meinem Aufsatze über den Stand der Sodafabrikation etc. (1875 215 58) einigermaßen ausführlich behandelt. Die folgenden Mittheilungen
werden jedoch trotzdem für die Industriellen der betreffenden Branche einiges
Interesse haben, einmal weil sie von Hargreaves selbst
herrühren (welcher sie in einem Privatvereine von Chemikern unserer Gegend machte
und welcher, soweit mir bekannt ist, sich noch nie früher mit solcher
Ausführlichkeit ausgesprochen hat) und zweitens, weil die Zeichnungen, welche ich zu
geben im Stande bin, diejenige Construction detaillirt darstellen, welche Hargreaves selbst den vielen anderen schon existirenden
auf das Entschiedenste vorzieht.
Es ist wohl kaum nöthig hervorzuheben, daß die im Folgenden erwähnten Angaben über
die erhaltenen Resultate immer mit derjenigen Vorsicht
aufzunehmen sind, welche selbst dem ehrlichsten und aufrichtigsten Erfinder (und Hargreaves gehört entschieden zu dieser Klasse) gegenüber
geboten ist. Soviel ist sicher, daß die mir anderweitig gemachten Angaben nicht ganz
so günstige Resultate aufweisen; doch ist es nur billig, Hargreaves' eigene Erklärung davon (weiter unten) pro tanto zu berücksichtigen. Dagegen sind die Mittheilungen über den
Apparat und die Operation mit demselben selbstredend vollkommen zuverlässig, und
müssen allen abweichenden Angaben in früheren Publicationen unbedingt vorgezogen
werden, als von dem Erfinder selbst herrührend und seine neuesten Erfahrungen
verkörpernd.
Hargreaves hebt damit an, daß seine Aufgabe für die
Fortentwickelung des Processes, welche er bekanntlich gemeinschaftlich mit Robinson
seit einer ganzen Reihe
von Jahren unermüdlich betreibt, fast ausschließlich die gewesen sei, thermische und
mechanische Schwierigkeiten zu überwinden. In dem eigentlich chemischen Theile des
Verfahrens ist seit fünf Jahren Alles unverändert geblieben. Bei den verschiedenen
Fabrikanlagen, welche für sein Verfahren gemacht worden sind, und für welche er
Pläne geliefert hat, sind, mit einziger Ausnahme der Fabrik von Boyd und Alexander in Dublin,
jedesmal von den Fabrikanten selbst erhebliche Aenderungen vorgenommen worden, und
Hargreaves meint, daß, obwohl er diese Aenderungen
meist bedauert und oft dagegen protestirt habe, sie doch stets dazu gedient haben,
entweder eine Berechnung zu bestätigen oder einen Irrthum ans Licht zu bringen, und
daß mithin die aus diesen Modificationen geschöpften Erfahrungen recht werthvoll
gewesen seien.
Das Verfahren besteht bekanntlich in der Production von Sodasulfat durch die directe
Wirkung von schwefliger Säure, Sauerstoff (der Luft) und Wasserdampf auf
Chlornatrium. Die gasförmigen Nebenproducte bestehen aus Chlorwasserstoff,
Stickstoff und überschüssigem Wasserdampf (jedenfalls auch überschüssigem
Sauerstoff). Die Reaction beginnt bei einer Temperatur von 750° F.
(400° C.) und wird um so intensiver, je höher die Temperatur steigt. Wenn die
Entwickelung von SO₂ nicht hinreichend stark und dieses Gas schon ganz
absorbirt ist, ehe der Gasstrom den letzten Cylinder erreicht, so wird der HCl (in
Gegenwart von überschüssigem Sauerstoff) gespalten und es entsteht Chlor und
H₂O. Dieses Chlor ist jedoch zu verdünnt, um für die Chlorkalkfabrikation
verwendbar zu sein.
Die Reaction läßt sich in folgender Weise formuliren, mit Auslassung der
überschüssigen und indifferenten Elemente:
SO₂ + O + H₂O + 2NaCl = Na₂SO₄ +
2HCL
entsprechend
SO₂ + O + HO + NaCl =
NaO, SO₃ + HCl.
Dies ist augenscheinlich ein viel einfacheres und directeres Verfahren als das
gewöhnliche mit Darstellung von flüssiger Schwefelsäure, und der Natronsalpeter
kommt dabei ganz und gar in Wegfall.Man rechnet in England, daß die Patentgebühr von 2 sh. 6 d. pro Tonne Sulfat ungefähr den
Aufwand für Natronsalpeter im gewöhnlichen Verfahren aufwiege.G. L. Das Chlornatrium
kann entweder als Steinsalz oder als Siedesalz verwendet werden und gibt die besten
Resultate, wenn es recht fein zertheilt ist, ehe es in Klumpen geformt wird. Es wird
angefeuchtet und getrocknet, wobei es den Zustand harter, flacher Kuchen annimmt,
welches in Stücke von etwa 1 1/2 engl. Zoll (38mm) Durchmesser zerbrochen werden. Die Jarrow Chemical Company zu
South-Shields ist im Begriffe, einen Apparat aufzustellen, welcher von J. C.
Stevenson
Einem der Erfinder der rotirenden Sodaöfen.G. L. erfunden worden ist und dazu dient, das Salz in Stücke von passender Größe
und Gestalt zu formen, welche dann in einem Trockenofen, ganz gleich den Backöfen
der großen Schiffszwieback-Bäckereien getrocknet werden. Die geformten
feuchten Stücke werden nämlich an einem Ende eingegeben, passiren durch die ganze
Länge des Ofens, wobei sie mit den Verbrennungsproducten in directe Berührung
kommen, und fallen trocken aus dem anderen Ende heraus.
Die Vortheile dieser Methode zur Vorbereitung des Salzes sind folgende: 1) Ersparniß
an Handarbeit durch Substitution von Maschinenkraft; 2) Vermeidung des in den
gewöhnlichen Brechmaschinen entstehenden Gruses und Staubes; 3) Ersparniß an
Brennmaterial dadurch, daß die Feuergase in directe Berührung mit dem zu trocknenden
Material kommen; 4) Regelmäßigkeit der Wirkung, indem alle Stücke von gleicher Größe
und Gestalt sind.
Das präparirte Salz wird in gußeiserne Cylinder gebracht, wo es ohne weitere
Manipulation liegen bleibt, bis es in Sulfat umgewandelt worden ist. Die Minimalzahl
der Cylinder ist acht; je mehr Cylinder angewendet werden, um so regelmäßiger geht
die Reaction vor sich und um so geringer ist die Quantität von Brennmaterial im
Vergleiche zu dem fabricirten Producte. Die Cylinderbatterie ist so angeordnet, daß
ein Jeder nach und nach als erster, mittlerer und letzter fungirt. Die schweflige
Säure wird zuerst in denjenigen Cylinder eingelassen, dessen Inhalt der völligen
Verwandlung in Sulfat am nächsten steht, und die erschöpften Gase entweichen aus
demjenigen, welcher zuletzt mit Salz chargirt war, nachdem sie eine ganze Reihe von
Cylindern passirt haben, welche weniger und weniger Sulfat enthalten.
Der in Fig. 1
und 2
dargestellte Apparat besteht aus acht Cylindern von 15 Fuß (4m,570) Durchmesser und 12 Fuß (3m,655) Höhe, welche in zwei Reihen
angeordnet und mit A₁, A₂... bezeichnet sind. Sie sind mit Thüren B zur Dechargirung des Sulfats versehen. Die Grundfläche zwischen den
beiden Reihen von Cylindern ist mit einem Gewölbe überspannt, welches mit Asche
bedeckt ist. Entlang den Seiten der beiden Cylinderreihen und über den Widerlagern
des Gewölbes laufen zwei eiserne Canäle C, welche die
schweflige Säure von den Kiesöfen zu den Cylindern leiten. Die Canäle sind gegen
Wärmeverlust durch Ausstrahlung von unten durch das Gewölbe und auf der Außenseite
durch eine Schicht Asche
geschützt, während die andere Seite an dem erhitzten Cylinder anliegt. Eine Schicht
Asche liegt ebenso oben auf den Canälen. Asche bildet das wirksamste nichtleitende
Material, indem ihre Wärmeleitungsfähigkeit nur halb so groß als die von Ziegeln
ist; außerdem kostet sie nichts und hat ein geringes specifisches Gewicht. Jeder
Schwefligsäure-Canal C hat vier Bogenröhren D, welche ihn mit jedem der Cylinder verbinden. Die
Cylinder sind unter einander durch die Circulationsbogenröhren E verbunden. Während der Arbeit sind sämmtliche
Bogenröhren verschlossen, mit Ausnahme derjenigen, welche mit dem
„Beendigungscylinder“ verbunden ist, d.h. demjenigen
Cylinder, dessen Inhalt an weitesten in der Umwandlung in Sulfat vorgeschritten ist,
und die schweflige Säure wird gerade in diese Bogenröhre eingelassen. Gesetzt, daß
A₃ der Beendigungscylinder und A₂ der Ausgangscylinder sei, so ist die
Bogenröhre zwischen C und A₃ offen und der Circulationsbogen zwischen A₃ und A₂ geschlossen, so daß
die schweflige Säure nicht direct in den Ausgangscylinder gehen kann, sondern durch
die ganze Serie hindurch streichen muß. Das Gas passirt successive durch A₃ bis A₈, A₁ und A₂,
indem es die Cylinder durch eine Oeffnung F unten in der
Dechargirungspforte verläßt; von dort geht es in den Canal G und wird durch den Saugapparat (Roots-Gebläse) entfernt.
Das Salz resp. Sulfat liegt auf beweglichen Rosten H,
welche durch Dreifüße unterstützt werden. Diese Dreifüße fallen leicht um, wenn man
kleine Zwingen herausschlägt, welche die Füße zusammenhalten, und lassen dann die
Roste ohne Unterstützung, so daß man das Sulfat herausziehen kann. Wenn das Sulfat
in A₃ fertig ist, so wird das Gas aus dem
Schwefligsäure-Canal nach A₄ eingelassen
und der Circulirbogen zwischen A₄ und A₃ geschlossen. Nachdem das Sulfat aus A₃ gezogen und Salz eingefüllt worden ist, wird
der Circulirbogen zwischen A₂ und A₃ geöffnet und A₃ zum Ausgangscylinder gemacht. Die kurzen Röhren J dienen als Beschickungsöffnungen zum Einfüllen des
Salzes. Die eine davon hat einen ringförmigen Raum um sich herum, durch welchen die
Verbrennungsproducte in das Innere des Cylinders gelassen werden können, wenn es zu
irgend einer Zeit nöthig ist, das Salz zu erhitzen, ehe man das Gas darauf wirken
läßt. Derselbe Raum gestattet auch, dem Gase im Inneren der Cylinder beim
Dechargiren derselben direct in den Feuercanal zu treten und mithin nicht die dabei
beschäftigten Arbeiter zu belästigen.
Das Gas von den Kiesöfen ist zu concentrirt, als daß man es direct in die frisches
Salz enthaltenden Cylinder einströmen lassen könnte; die Wirkung würde dann so
heftig sein, daß das Ganze zu einer harten cohärenten Masse zusammenschmelzen würde. Dies wird
dadurch vermieden, daß man die Hitze so schnell wie möglich auf den gehörigen Grad
steigen und das Salz sich mit einer Rinde von Sulfat bedecken läßt, während es am
Ausgangsende der Serie ist, wo nur etwa ein Zehntel der ursprünglich vorhandenen
schwefligen Säure noch in dem Gase zurückgeblieben ist. Die Rinde von Sulfat wächst
an Dicke, sowie die Cylinder der Eintrittsöffnung näher stehen.
Jeder Fabrikdirigent weiß, daß, wenn es möglich ist, daß ein Proceß falsch geht, ohne
die Arbeiter dabei zu belästigen, dies ganz gewiß oft genug geschehen wird, selbst
wenn sie darum wissen; wenn aber der Irrthum ohne ihr Wissen eintreten kann, und
seine Entdeckung nur durch chemische Analyse oder vielleicht durch Zufall möglich
ist, so schwindet jede Hoffnung, zuverlässige Resultate zu erlangen. Nachdem die
früheren Experimente dies zur Genüge gezeigt hatten, wurden die Verbindungen
zwischen den Cylindern so angeordnet, daß, wenn sie nicht gehörig gemacht sind, sie
von selbst die Aufmerksamkeit darauf lenken, indem sie die Arbeiter, welche ihre
Pflicht versäumt haben, belästigen und außerdem dem Dirigenten mit einem Blicke
zeigen, was vorgegangen ist. Gewöhnliche Ventile sind nicht anwendbar, sowohl wegen
der hohen Temperatur als wegen der chemischen Wirkung des Gases, und irgend welche
schweflige Säure, welche durch den Ausgang entweicht, ohne durch die ganze Serie zu
streichen, muß theilweise oder ganz verloren gehen. Um die Möglichkeit davon zu
verhüten, sind die Bogenröhren D in zwei Theile getheilt
(vergl. Längenschnitt in Fig. 3, Grundriß in Fig. 4 und
Vorderansicht in Fig. 5). Der Durchgang des Gases wird durch eine Platte verhindert,
welche in den Raum ee zwischen den beiden Theilen
des Bogens eingeschoben wird. Der Raum zwischen der Platte und den Bogenhälften wird
mit einer Mischung von Kalkmörtel und Salz verstrichen. Wenn dies nicht gehörig
geschehen ist, so entweicht die schweflige Säure nicht in den Ausgangscylinder oder
einen von den Zwischencylindern, wo sie unentdeckt bleiben könnte, sondern sie geht
direct in die äußere Luft und legt ein unzweideutiges, aber unangenehmes Zeugniß
dafür ab, daß die Arbeit nicht ordentlich verrichtet ist; der Arbeiter wird davon
belästigt, bis er nachsieht und es in Ordnung bringt. Wenn die Passage offen bleiben
soll, so wird eine andere Platte eingesetzt, welche eine derjenigen der Bogenröhre
im Querschnitt gleiche Oeffnung besitzt. Die Fuge wird ganz ebenso gedichtet, als im
Falle der undurchbohrten Platte. Der Raum zwischen den beiden Hälften der
Bogenröhren wird mittels der Lappen und Stehbolzen b
stabil erhalten. Die Oeffnung c dient dazu, damit das
Salz auch in den Theil des Cylinders gebracht werden kann, welcher direct unter der Bogenröhre liegt.
Es war keine leicht zu lösende Aufgabe, eine Batterie von Cylindern (15 Fuß im
Durchmesser und 12 Fuß hoch) so zu erhitzen, daß alle Theile jedes Cylinders eine
möglichst gleiche Temperatur hätten. Es war wirklich das erstemal, daß man es
unternommen hat, so große Massen ausschließlich durch Erhitzung von außen zu
erwärmen, und es standen nicht einmal Angaben über mißlungene Versuche zu Gebote,
aus denen man hätte lernen können, was zu vermeiden sei. Außerdem war die Aufgabe
die, die Temperatur 14 Tage lang hinreichend hoch zu erhalten, ohne mehr
Brennmaterialien aufzuwenden, als wenn man dieselben Materialen nur eine oder zwei
Stunden heiß zu erhalten hat. Den „Praktikern“ schien dieses
der Punkt zu sein, an welchem das Verfahren scheitern müsse. Sie behaupteten daher mit einer Zuversicht, welche nur bewiesene
Thatsachen geben sollten, daß dies auch wirklich der Fall sei, daß nach der Natur
der Dinge mehr Feuerung als in dem alten Processe wirklich verbraucht würde, und
Hargreaves' Verfahren daran factisch gescheitert sei. Es war Hargreaves' Aufgabe, dieser Schwierigkeit zu begegnen, und da zunächst
keine Experimentalresultate vorlagen, so mußten rein theoretische Betrachtungen als
erster Leitstern für die praktische Behandlung dienen.
Die Theorie ergab zunächst, daß die durch die Reaction frei werdenden Wärmeeinheiten
hinreichen, um sie ganz und gar durchzuführen, und noch einen großen Betrag für
Verluste disponibel lassen, ohne auf Consumption frischen Brennmaterials überhaupt
zu rechnen. Es ist unnöthig zu beweisen, daß solche Verluste nie ganz zu vermeiden
sind, wenn nicht etwa (was nicht wahrscheinlich ist) ein absoluter Nichtleiter für
Wärme aufgefunden werden sollte. Es ist aber möglich, ziemlich annähernde
Berechnungen über den unvermeidlichen Wärmeverlust zu machen und auch zu berechnen,
wie viel Feuerung nothwendig ist, um ihn zu decken. Das Brennmaterial, welches
erforderlich ist, um eine Batterie von 8 Cylindern, welche 100 Tonnen Sulfat
wöchentlich produciren, auf der gehörigen Temperatur zu erhalten, beläuft sich auf
15 Tonnen Kohlen, oder 3 Ctr. pro Tonne producirten Sulfats (15 Proc.) –
vorausgesetzt, daß die Kiesbrenner so angeordnet sind, daß die Hitze des Gases
gehörig verwerthet wird.In dem in unserem Vereine gehaltenen Vortrage gab Hargreaves keine Berechnungen, sondern stellte nur eben obige
Resultate auf, deren selbst theoretische Berechtigung somit hier
uncontrolirt bleiben muß.G. L. Die HH. Boyd und Alexander verbrauchen zwar 4 Ctr. Kohlen pro Tonne Sulfat, aber dieser
Ueberschuß läßt sich auf
vermeidbare Ursachen zurückführen, nämlich auf einen Unfall an dem
Dampfüberhitzungsapparate, welcher noch nicht reparirt ist.
Die Cylinder werden mittels Feuerherden I erhitzt. Die Feuergase streichen durch
einen horizontalen Canal II und steigen in engen senkrechten Canälen III in die
Höhe; diese letzteren haben einen Querschnitt von nur 5 Zoll (12mm), von der Absicht ausgehend, die Wärme
absorbirende Oberfläche dort, wo die Verbrennungsproducte sehr heiß sind, zu
vermindern. Die Züge sind jedoch hinreichend weit, um alle Verbrennungsproducte
abzuführen. Die Feuerherde sind mit dicht schließenden Thüren versehen, so daß, wenn
man kein Feuer braucht, sowohl die Herde, als die Aschenfälle gegen das Eindringen
von kalter Luft geschützt sind; zu gleicher Zeit dient auch das Register IV dazu,
den Zug nach dem Schornstein aufzuheben. Nachdem die Feuergase die senkrechten
Canäle verlassen haben, streichen sie in einem 10 Zoll (25mm) tiefen Raum zwischen dem Cylinderdeckel
und einer darüber angebrachten Deckplatte; sie circuliren dort um die
Chargiröffnungen und über den Cylinderdeckel; der Rauch passirt dann an den Seiten
des Cylinders herunter, unter demselben weg und geht schließlich an dem Register
vorbei nach dem Kamin zu.
Da die durch den Proceß selbst erzeugte Hitze an sich, abgesehen von den Verlusten,
mehr als hinreichend ist, um die Operation im Gange zu erhalten, und die
Wärmeverluste von der Ausstrahlung und Fortleitung der den Apparat begrenzenden
Oberflächen herrühren, so ist es klar, daß, wenn man den Apparat vergrößert und
mithin das Verhältniß zwischen Oberfläche und Inhalt verringert, zugleich das pro
Tonne Sulfat erforderliche Quantum von Kohlen sich ebenfalls verringern muß, und die
einzige Frage ist die, ob man nicht das Princip so weit verfolgen könne, um eine
frische Zufuhr von Kohlen zur Aufrechterhaltung der Temperatur in den Cylindern ganz
entbehren zu können. Dieser Schluß wird durch die beim Arbeiten mit Cylindern
verschiedener Größe gewonnenen Erfahrungen bestätigt; einer der ersten verbrauchte
etwa 2 Tonnen Kohlen Pro Tonne Sulfat; ein zweitgrößerer nur 14 Ctr.; ein wiederum
vergrößerter 6 Ctr., und die Serie von 8 Cylindern in Dublin hat mit 3 Ctr.
gearbeitet.Wie lange? Und mit Sicherheit constatirt? Und was für Kohlen?G. L.
Die Atlas Chemical Company zieht Nutzen von der
Thatsache, daß der Kohlenverbrauch pro Tonne Sulfat sich reducirt, während die
Production pro Cylinder steigt, sobald man eine große Anzahl Cylinder in einer
Batterie combinirt. Sie hat 20 Cylinder in einer Serie angeordnet, und Rücken an Rücken
aufgestellt, mit nur einer Dechargirungspforte und einem Feuerherde; dies gestattet
laterale Wärmestrahlung und Fortleitung nur auf der einen Seite. Die Wärme
absorbirende Oberfläche wird auch dadurch reducirt, daß der Rauchcanalraum reducirt
ist. Hargreaves schätzte den Kohlenverbrauch bei den
Cylindern auf 1 Ctr. (5 Proc.) pro Tonne; aber die Besitzer haben beschlossen,
einige Aenderungen vorzunehmen, welche einen weiteren Kohlenaufwand von 35 Pfd. pro
Tonne Sulfat zur Folge haben werden, wie Hargreaves
berechnet. Er fühlt sich natürlich sehr unglücklich, daß ihm Niemand etwas recht
machen will, und daß die „praktischen“ Leute sich oft ohne
weiteres über seine nach wissenschaftlichen Grundsätzen gemachten Anordnungen
hinwegsetzen.Wohl nicht immer mit Unrecht.G. L.
Die Kiesbrenner sind fast ebenso wie gewöhnlich in Schwefelsäurefabriken gebaut; sie
sind Rücken an Rücken angeordnet und es ist möglichst vermieden, irgend welche
Eisentheile der directen Wirkung des brennenden Pyrits auszusetzen. Die
Arbeitsöffnung ist ohne den eisernen Futterrahmen, welcher bei gewöhnlichen Oefen
häufig in das Innere der Brenner vorragt. Die Außenwände sind 18 Zoll (457mm) stark; am besten ist es, gewöhnliche
Mauerziegeln mit einem Futter von nur 5 Zoll (127mm) feuerfester Ziegeln anzuwenden; dies erspart nicht nur Anlagekosten,
sondern auch Wärmeverluste, da gewöhnliche Mauerziegeln die Wärme weniger leiten als
feuerfeste Steine. Der hintere Theil des Ofengewölbes ist niedriger als der vordere,
und der Gascanal ist in der dadurch hervorgebrachten Senkung angebracht; eine Mauer
erhebt sich über der Vorderseite der Oefen und gestattet es, den ganzen Raum über
den Oefen mit einer mindestens 2 Fuß (609mm) tiefen Schicht Asche zu bedecken. Die Arbeitsthür wird gegen Ausstrahlung
durch ein nichtleitendes Futter beschützt.
Figur 6 zeigt
den Durchschnitt der bei Boyd und Alexander aufgestellten Kiesöfen. Die eiserne Frontarmirung erstreckt sich
nur bis 2 oder 3 Zoll (51 bis 76mm) über
die Oberseite des Aschenfalles, wo es nothwendig ist, die Luft unter gehöriger
Controle zu halten. Man kann aus der Zeichnung sehen, daß die der Hitze des
brennenden Kieses ausgesetzte Eisenoberfläche viel geringer als gewöhnlich ist, und
die Wärmeausstrahlung steht damit im entsprechenden Verhältnisse.
Die Figuren 7
und 8 zeigen
den Betrag der Ausstrahlung von Kiesöfen mit Eisenfront, einmal für Hargreaves'
Proceß und das anderemal für den in Schwefelsäurefabriken üblichen Ofen. Die Zahlen
bedeuten englische
WärmeeinheitenErhitzung eines englischen Pfundes (553g) Wasser um 1° F. Ein Quadratfuß engl. = 0qm,0929.G. L., ausgestrahlt
per Quadratfuß in 24 Stunden, an den markirten Punkten gemessen mit einem
Thermoradiometer.
In den von Hargreaves benützten Oefen mit Eisenfront war
der Verlust 520090 englische CalorienErhitzung eines englischen Pfundes (553g) Wasser um 1° F. Ein Quadratfuß engl. = 0qm,0929.G. L. per 24 Stunden
von jeder Front; dies kommt gleich der theoretischen Verbrennung von 40 engl. Pfd.
Kohlen; aber da der effective Verbrennungswerth in dem Sulfatapparate geringer ist,
sicherlich nicht über 2000 Calorien pro Pfd., so kommt der Verlust praktisch auf 260 Pfd. Kohlen per 24 Stunden. Man kann
sagen, daß drei Viertel dieses Verlustes vermeidbar ist, und daß der unnöthige Verlust 195 Pfd. oder für 12 Oefen 2340 Pfd.
(etwa 21 Ctr.) in 24 Stunden beträgt; d.h. man muß 2340 Pfd. Kohlen unter den
Cylindern verbrennen, um den vermeidbaren Verlust der
Ofenfronten zu ersetzen.
Der effective Brennwerth der Steinkohle, welcher natürlich je nach der Natur der
Arbeit variirt und im Allgemeinen um so höher ist, je niedriger die Temperatur des
zu erhitzenden Materials, beträgt bei dem vorliegenden Verfahren im Durchschnitt
etwa 14 Proc.; er variirt von 10 Proc. in dem Beendigungscylinder bis 20 Proc. in
dem Ausgangscylinder, dessen Temperatur am niedersten ist. (Für Dampfkessel beträgt
er 50 bis 80 Proc., für Puddelöfen 3 bis 5 Proc., und für Stahlschmelzen kommt er
auf den Nullpunkt.)
Bekanntlich kann man den größten Heizeffect erzielen, wenn man die Erhitzung besorgt,
so lange die Materialien noch auf niederer Temperatur stehen, und man muß dies auch
im vorliegenden Falle anwenden. Der Dampf, welchen man mit den Kiesöfengasen zu
mischen hat, ist nur 212° F. (100° C.) heißMan sieht weiter unten, daß es meist Retourdampf von der Gebläsemaschine ist;
gespannter Dampf ist natürlich wärmer.G. L. und gibt eine gute Gelegenheit, darauf mit den Verbrennungsproducten der
Cylinderheizung zu operiren, welche noch 800 bis 850° F. haben, je nach der
Intensität der Feuerung. Man kann in der That dadurch den Dampf leicht auf
650° F. überhitzen, ehe man ihn mit den Kiesöfengasen in Berührung bringt,
und der große Vortheil, ihn dabei ganz zu trocknen, springt gleichfalls in die
Augen; für jedes Pfund flüssigen Wassers, welches vom Dampfe mitgerissen wird,
werden 960 engl. Calorien latent, wenn er getrocknet wird. Man kann den durch
Ueberhitzung des Dampfes zu erzielenden Temperaturzuwachs aus folgender Formel berechnen:
x = (WST + wst)/(WS + ws), wobei W das
Gewicht des Gases, w das des Dampfes, S die specifische Wärme des ersteren und s des
letzteren, endlich T und t
die respectiven Temperaturen bedeuten.
Eine Fabrik überhitzt absurderweise ihren Dampf, statt durch die entweichenden
Cylinderfeuerungsgase, vielmehr durch Abkühlung der schwefligen Säure, indem ihre
Dampfröhren auf den Ofengewölben liegen; sie verliert also auf der einen Seite
gerade soviel, als sie auf der anderen gewinnt, und verbraucht mehr Kohlen als bei
zweckmäßiger Einrichtung nöthig wäre.
Abgesehen von theoretischen Betrachtungen ist auch ein experimenteller Beweis für den
Vortheil des Ueberheizens von Wasserdampf geliefert worden. In der Fabrik von Boyd und Alexander war der
Wassersammler für das condensirte Wasser in einiger Entfernung von dem Ueberhitzer,
statt dicht bei demselben angelegt, und der Stoß des Wassers zerbrach eine der
gußeisernen Röhren, als es einmal mit Gewalt hineingetrieben wurde. Der Ueberhitzer
wurde dadurch außer Thätigkeit gesetzt, und sofort stieg der Kohlenverbrauch um 10
Tonnen per Woche. Obige Firma ist übrigens die einzige, welche sich fast genau an
die Pläne des Erfinders gehalten und dadurch eine bedeutend geringere Consumption
von Kohlen als andere Fabrikanten erzielt hat. Auch in Bezug auf Qualität des
Productes nimmt sie einen hervorragenden Rang ein. Folgendes ist die Analyse einer
Durchschnittsprobe einer von jener Fabrik verschifften Ladung:
Schwefelsaures Natron
99,24
Chlornatrium
0,08
Freie Säure und Feuchtigkeit
0,20
Eisenoxyd und Unlösliches
0,48
––––––
100,00
unterzeichnet von W. Plunkett,
Dublin.Ich muß mir doch bescheidene Zweifel erlauben, entweder gegen den
Durchschnittscharakter des Musters oder gegen die Genauigkeit der Analyse,
oder beides. Die Analyse, welche die nicht ganz ungewöhnliche, aber den
meisten Chemikern übernatürlich scheinende Eigenschaft hat, auf 100,00
aufzugehen, zeigt neben einer fast lächerlich geringen Quantität von
unzersetztem Chlornatrium kaum ein Drittel des Unlöslichen (Gyps, Eisenoxyd
etc.), welches man selbst bei Siedesalz von Cheshire erwarten muß, und da
Steinsalz mit verwendet wurde, so ist das Mißverhältniß und die
Unwahrscheinlichkeit noch größer. Uebrigens würde 97 bis 98 Proc.
schwefelsaures Natron schon allen Anforderungen des Handels genügen.G. L.
Wenn das Sulfat ganz aus Siedesalz gemacht wird, enthält es weniger als die Hälfte
des im gewöhnlichen Sulfat vorkommenden Eisenoxydes und eignet sich dadurch sehr gut
zur Glasfabrikation. In Belgien ist dies schon praktisch nachgewiesen worden.
Der Chlorwasserstoff und die anderen überschüssigen Gase werden aus den Cylindern
durch einen Saugapparat entfernt. Die in Dublin dazu angewendete Maschine ist ein
Roots'sches Gebläse
(Roots-Blower), construirt von Thwaites und Carbutt in Bradford. Es ist für diesen Zweck dahin
modificirt, daß die hölzernen rotirenden Kolben durch eiserne ersetzt worden sind,
weil die Temperatur und die corrosive Wirkung der Gase das Holz rasch zerstören
würden; die eisernen Kolben und der Mantel des Gebläses dagegen werden von den Gasen
nicht angegriffen, so lange die Temperatur hoch genug ist, sie ganz im gasförmigen
Zustande zu erhalten, und das Gebläse leidet factisch nicht mehr, als wenn es mit
atmosphärischer Luft arbeitete. Man kann die erforliche Temperatur mit Leichtigkeit
erhalten, wenn man die Maschine unter Dach aufstellt und sie mit einer
nichtleitenden Composition überzieht, wie sie für Bedeckung von Dampfkesseln
gebräuchlich ist.
Wenn die Friction erleidenden Theile der Maschine dieselbe Temperatur annehmen
könnten wie das durchstreichende Gas, so würde natürlich die Abnützung derselben
eine sehr starke sein; um dieses zu vermeiden, sind die Wellen so construirt, daß
sie in Lagermetallbüchsen rotiren, welche in einem hohlen Consol liegen; ein Strom
kalten Wassers fließt langsam durch das letztere und hält die Temperatur der
Lagerschalen auf niedrigem Grade, ohne daß es jedoch, gemäß der Anordnung der
Ein- und Austrittsstellen in dem Consol, einen erheblichen Abkühlungseffect
auf den Mantel des Gebläses hat. Die Figuren 9 bis 12, welche die
von Thwaites und Carbutt
construirte Maschine darstellen, werden dies deutlicher machen. Die Wellen treten
durch Oeffnungen in den Enden des Mantels aus, während die rotirenden Kolben durch
ein Zahnrädervorgelege in ihrer gehörigen relativen Stellung erhalten werden.
Stopfbüchsen sind nicht erforderlich, da die kleine, neben den Wellen eintretende
Luftmenge praktisch unwesentlich ist, und das inwendig befindliche Gas überhaupt
keine Tendenz hat, nach außen zu entweichen, außer wenn der Widerstand auf der
Austrittsseite des Gebläses zu groß ist.
Es ist ungemein wesentlich, daß die den Blower treibende Dampf-Maschine sehr
solide construirt und Stillständen für Reparaturen nur sehr selten ausgesetzt sei
– nicht allein, weil dadurch der ganze Proceß unterbrochen wird, sondern auch
weil die Maschine sich dabei abkühlt, Salzsäure condensirt wird und die Maschinerie
verdirbt. Die Dampfmaschine muß also im Stande sein, der Corrosion und rauhen
Behandlung, welche ihrer
meist in chemischen Fabriken harrt, ohne Beschädigung Widerstand leisten zu können.
Hargreaves empfiehlt als vorzüglich zweckentsprechend
die von James Robertson in Glasgow construirte Maschine,
welche in diesem Journal (1871 199 433) bereits
beschrieben ist. Eine solche Maschine hat schon 5 Monate in Dublin gearbeitet, ohne
von dem Maschinenschlosser berührt zuwerden.
Dieselbe Maschine, welche das Gebläse treibt, liefert in ihrem Austrittsdampf
denjenigen Wasserdampf, welcher zum Mischen mit dem Schwefligsäuregase gebraucht
wird; die relative Geschwindigkeit des Gebläses und der Maschine sind derartig, daß
sie ungefähr so viel Dampf ausgeben, als zum richtigen Arbeiten in den Cylindern
erforderlich ist. Die Maschine ist in der That ein Dampfmesser, welcher die Zufuhr
von Dampf im Verhältniß zu der Geschwindigkeit, mit welcher die Gase durch den
Apparat gesaugt werden, regulirt, und da man zum Mischen mit dem Gase mehr Dampf
braucht, als die Maschine zu ihrem Betriebe nöthig hat, so kostet factisch die
mechanische, zum Aussaugen der Gase verwendete Kraft gar nichts. Theoretisch braucht
man 2 1/2 Ctr. Dampf für eine Tonne Sulfat (12 1/2 Proc.), aber in der Praxis
braucht man 4, und hieraus kann man den erforderlichen Aufwand von Brennmaterial
berechnen. Ein guter, mit den besten Wärme ersparenden Einrichtungen versehener
Dampfkessel verdampft 10 Ctr. Wasser pro 1 Ctr. Kohlen, aber die meist in chemischen
Fabriken zu findenden Dampfkessel darf man nur zu 7 Ctr. annehmen; dies würde 0,57
Ctr. Kohlen für 1 Tonne Sulfat entsprechen, und wenn man 0,75 Ctr. (= 3,75 Proc. des
Sulfats) annimmt, so ist man für alle Fälle gedeckt.
In der Fabrik von Boyd und Alexander werden folgende Mengen Kohlen pro Tonne Sulfat verbraucht:
Erhitzung der Cylinder
4
Ctr.
(30 Proc.)
Vorbereitung des Salzes
3
„
(15 Proc.)
Dampf (ungefähr)
3/4
„
(3,75 Proc.)
––––––––––––––––––––
7 3/4
Ctr.
(38,75 Proc.)
Da der Dampf von einem anderweitig in Anspruch genommenen Kessel entnommen ist, so
kann man nur einen Ueberschlag, wie oben, dafür ansetzen; für die Erhitzung der
Cylinder würde 1 Ctr. (5 Proc.) weniger genügen, sobald wieder überhitzter Dampf (s.
oben) angewendet wird. (Nach später erhaltenen Nachrichten sei obiger Consum
neuerdings um 2 Ctr. verringert worden.) Die Handarbeit besteht in Folgendem:
Niederlegen des Salzes auf eine Trockendarre; Karren des getrockneten Salzes zur
Brechmaschine, von der es durch Elevatoren in 2 Tonnen haltende Wagen gehoben wird.
Die Wagen laufen auf Schienen über die Cylinder und werden durch ihre Böden in die letzteren
entleert. In den Cylindern wird es nicht berührt und erst das fertige Sulfat wird
wieder durch Handarbeit ausgezogen und nach dem Magazin gekarrt. Ein einziger Heizer
per Schicht bedient sämmtliche Cylinderfeuer, da sie selten alle auf einmal
arbeiten, und ein Mann versieht die Kiesbrenner per Schicht. Der ArbeitslohnIn Dublin ist der Arbeitslohn bedeutend niedriger als in den englischen
Fabrikdistricten.G. L. im Ganzen übersteigt nicht 6 Shilling per Tonne Sulfat. Alle diese
Kostenberechnungen beziehen sich allein auf die Annahme einer Production von 100
Tonnen Sulfat in der Woche; aber Hargreaves erwartet, daß
eine bedeutend höhere Production eintreten wird, insofern sowohl die Leiter als die
Arbeiter mehr Erfahrung gewinnen und die Resultate sich stetig bessern.
Eine Erfindung, von welcher Hargreaves bedeutende Hilfe
für die Zukunft erwartet, ist diejenige von Pohl, durch
welche Kochsalz mit einer Ersparniß von einem Drittel des Brennmaterials, und mithin
der Kosten, producirt wird. Das Salz ist zwar öfters mißfarbig durch Ruß, aber ganz
ebenso werthvoll für Hargreaves als weißes Salz, da der
Ruß in den Cylindern wegbrennt; außerdem ist das Salz in einem feinkörnigen
Zustande, welcher es für das Verfahren sehr gut tauglich macht. Im großen Maßstabe
und anhaltend ist es jedoch noch nicht verwendet worden, weil die Erfindung zu neu
ist.
Hargreaves erwähnt in seinen Mittheilungen an unseren
Verein nichts Specielles über ein sehr wichtiges Object, die Kondensation der
Salzsäure; ich will deshalb etwas aus anderweitigen Erkundigungen darüber
mittheilen. Auf der einen Seite sollte die Condensation eine leichtere Aufgabe als
bei dem gewöhnlichen Verfahren sein, insofern die Salzsäure sich nicht, wie bei dem
letzteren, stoßweise und meist in dem allerersten Stadium des Processes, sondern mit
völliger Gleichförmgkeit den ganzen Tag hindurch entwickelt. Diesem Vortheile stehen
freilich zwei sehr erhebliche Schattenseiten gegenüber, nämlich einmal die große
Verdünnung des Salzsäuregases mit Stickstoff etc. und zweitens die große Hitze, mit
welcher es aus den Cylindern entweicht. Es scheint vorläufig, namentlich in Folge
des ersteren Umstandes, ganz unthunlich, das Hargreaves'sche Verfahren mit dem
Deacon'schen Chlorverfahren zu combiniren; dies thut freilich nicht viel, da man
durch zweckmäßige Abkühlung dahin gelangen kann, das Gas zu flüssiger Salzsäure zu
condensiren und diese zur Weldon'schen Chlorbereitung zu benützen. Abkühlung ist es
eben, was man ganz wesentlich braucht, und zwar in ganz großem Maßstabe. Eine Fabrik
in Runcorn hat dazu zwei sehr lange Steintröge angelegt, welche durch 18 Reihen von 300mm weiten Thonröhren mit einander verbunden
sind; jede Reihe geht fünfmal etwa 9m in
die Höhe und ebenso oft hinunter, repräsentirt also zusammen 90m, oder die 18 Reihen zusammen 1620m Röhrenlänge, ohne auf die Kniee Rücksicht
zu nehmen.
Ich muß ferner erwähnen, daß, selbst wenn man die im Obigen enthaltenden Angaben von
Hargreaves über die Kosten für Kohlen und Arbeit als
giltig annehmen will (und sie stehen jedenfalls in starkem Widerspruche mit dem, was
man von anderen Fabriken hört, über deren Nichtbefolgung seiner Rathschläge sich
freilich Hargreaves beschwert), ein erheblicher Vortheil
des Verfahrens zur Zeit noch nicht ersichtlich ist. Wir
bezahlen allerdings hier etwas mehr Arbeitslohn bei dem gewöhnlichen Verfahren
(inclusive der Schwefelsäure) als 6 Shilling pro Tonne Sulfat, aber unsere
Arbeitslöhne sind eben überhaupt höher, und wir können nicht hoffen, bei Hargreaves'
Verfahren mit weniger Arbeitslohn auszukommen; doch wird vielleicht die oben
berührte Erfindung von Stevenson (mechanisches Formen und
Trocknen des Salzes) darin einen Vortheil ergeben. Dieselbe sollte jedenfalls auch
den Kohlenverbrauch reduciren, welcher entschieden unter allen Umständen noch viel
höher als bei dem gewöhnlichen Verfahren ausfällt. Wie man sieht, ist auch Hargreaves' größte Sorgfalt auf diesen Punkt gerichtet,
und kann man ihm die Möglichkeit eines schließlichen Erfolges keineswegs absprechen.
Das Wegfallen des Natronsalpeters wird vorläufig noch durch die Patentgebühr
aufgewogen. Im Ganzen muß man dahin urtheilen, daß das Hargreaves'sche Verfahren
entschieden sehr gute Aussichten hat; erst neuerdings haben wieder einzelne
Fabrikanten angefangen, dasselbe einzuführen, trotz der großen Anlagekosten, welche
im Falle einer schon bestehenden Sodafabrik mehr als bei einer neu zu errichtenden
in Betracht kommen. Die viel geringere Belästigung der Nachbarschaft und die viel
geringere Abhängigkeit von speciell erfahrenen Arbeitern sind Vortheile des
Verfahrens, welche sich nicht leicht in baarem Gelde abschätzen lassen, die aber in
manchen Fällen recht sehr in Betracht kommen dürften.
(Nachschrift.) Von Hrn. Hargreaves selbst wird mir direct
mitgetheilt, daß die folgenden Fabriken in voller Arbeit nach seinem Verfahren
begriffen sind:
Sullivan und Comp.,
Widnes.
Wigg, Steele und Comp.,
Runcorn.
Runcorn Soap and Alkali
Company, Runcorn.
Boyd und Alexander,
Dublin.
Diese Fabriken produciren zusammen über 400 Tonnen Sulfat wöchentlich, könnten aber
mit ihrer Einrichtung 560 Tonnen wöchentlich fabriciren, wenn sie alle auch nur so
gut wie die älteste Fabrik, die von Sullivan,
arbeiteten.
Im Bau begriffen und beinahe fertig sind ferner die folgenden Etablissements:
Jarrow Chemical Company, South-Shields;
Atlas Chemical Company, Widnes, die letztere für eine
Production von 350 bis 400 Tonnen. (Auch S. Mease und Comp. in South-Shields haben schon mit dem Bau
begonnen. G. L.)
Das nach Hargreaves fabricirte Sulfat wird jetzt sehr
stark von Glasfabriken verlangt (die größten englischen Spiegelglasfabriken befinden
sich gerade in St. Helens, dicht bei Widnes), aber es muß in diesem Falle ganz aus
Siedesalz gemacht werden, um es eisenfrei zu erhalten.
2. November 1875.
Tafeln
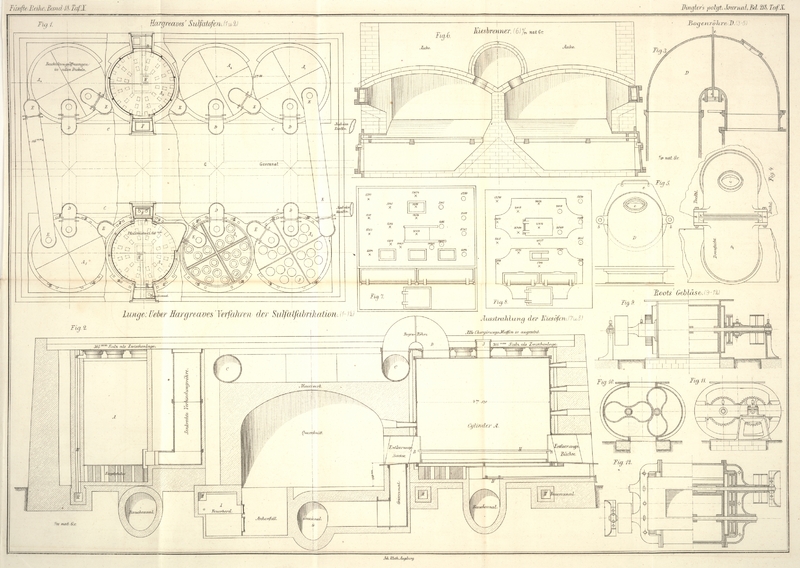