Titel: | Ueber die Gewinnung von Ammoniak. |
Fundstelle: | Band 234, Jahrgang 1879, S. 383 |
Download: | XML |
Ueber die Gewinnung von Ammoniak.
Mit Abbildungen auf Tafel 32.
Ueber die Gewinnung von Ammoniak.
Nach dem Vorschlage von P. S. Brown
in Carrickfergus (* D. R. P. Nr. 6198 vom 1. September 1878) werden die Ammoniak
haltigen Flüssigkeiten der Leuchtgasfabriken durch Kohle filtrirt, dann mit
Schwefelsäure neutralisirt und zur Krystallisation eingedampft.
J. Barrow schlägt nach dem
englischen Patente Nr. 891 vom 5. März 1878 vor, das Gaswasser mit Sodarückständen
oder Gaskalk zu destilliren. Der Rückstand von kohlensaurem Kalk soll wieder in der
Sodafabrikation oder nach dem Glühen in geschlossenen Retorten unter Einleiten von
Wasserdampf zur Gasreinigung angewendet werden. Das überdestillirende
Schwefelammonium wird in Schwefelsäure oder Salzsäure aufgefangen, der dabei
entweichende Schwefelwasserstoff in bekannter Weise verwerthet.
Um das bei der Kokesfabrikation
entweichende Ammoniak zu gewinnen, setzen Th.
Scholz und L. Thieme in Dresden (* D. R. P.
Nr. 2653 vom 24. Januar 1878) auf die aufsteigenden Zuglöcher A (Fig. 3 Taf.
32) der gewöhnlichen Kokesöfen einen Deckel a,
verbinden dieselben aber seitlich mit einem wagerechten, viereckigen Kanal B, der die Gase zum Rohre C führt. Der sich
hier ansammelnde Theer wird durch den Steg v gezwungen,
aus dem Rohre w abzuflieſsen.
Das feststehende Eisenrohr C erweitert sich mit seinem
oberen Theil von 12cm lichter Weite auf 25cm, um die Vertheilungsvorrichtung L für die Salzsäure zu umschlieſsen. Der bewegliche,
ebenfalls aus Guſseisen hergestellte Theil der Esse wird von der Spindel f getragen, welche durch den Bügel e mit dem feststehenden Theil C verbunden ist. Die aus Porzellan gefertigte Vertheilungsvorrichtung L, welche 12cm hoch
über der Mündung des Rohres C auf der durch den Steg
b getragenen Spindel c
ruht, bildet einen 6cm tiefen und 14cm breiten Teller mit einem 17cm hohen und 4cm
breiten hohlen Stutzen und ist somit leicht um seine Achse drehbar. Im Boden dieser
Vertheilungsvorrichtung befinden sich nahe am Rande eine groſse Anzahl kleiner
Löcher, welche die durch den Trichter H zugeführte, aus
der Rinne G zuflieſsende Salzsäure als feinen Regen
hindurch lassen und so angeordnet sind, daſs die ausflieſsenden Strahlen eine
Reaction auf den Teller ausüben, so daſs derselbe auf der Spindel herumgedreht wird.
Die Säure sammelt sich im unteren Theile der Erweiterung bei o an, von wo sie durch das Rohr d und den
Trichter k nach einer Sammelgrube abflieſst. Die
Ofengase können also ungehindert von dem Rohr C aus
durch den Salzsäureregen hindurch in den geneigten, um die Spindel f drehbaren Theil E der
Vorrichtung gelangen, welcher durch ein Gegengewicht K
ausbalancirt ist und durch ein Blech l nach der
Windrichtung gestellt wird.
Eine Rinne F führt der oberen Hälfte des feststehenden
Essentheiles Wasser zu, damit der ringförmige Zwischenraum, welcher von der 25cm breiten Zarge y
und der Rohrmündung gebildet wird, ausgefüllt und somit das Austreten von Rauch
gehindert, zugleich aber der drehbare Essentheil E
gekühlt wird. Das Wasser flieſst durch den Trichter t
zu einem entsprechenden Sammelbehälter.
Die durch das Zusammentreffen von Ammoniak mit Salzsäure gebildeten Salmiaknebel
werden theils von der flüssigen Salzsäure gelöst durch das Rohr d abgeführt, theils gelangen sie mit den Rauchgasen in
den kälteren Theil der Esse, verdichten sich hier und werden durch das
mitcondensirte Wasser schlieſslich durch das Rohr t
entfernt. Die Länge des drehbaren Essentheiles E
richtet sich nach dem Ammoniakgehalt der Rauchgase aus den Kokesöfen; die Höhe des
aufrechten und festen Theiles bestimmt sich durch den Widerstand, welchen der obere
Essentheil in der Hauptsache dem Durchgange der Gase bereitet. Sie wird so groſs
genommen, daſs der Auftrieb der heiſsen Abzugsgase diese Widerstände überwindet,
aber auch nicht gröſser, weil die Condensationsesse sonst ohne Einfluſs auf den
Luftzug im Kokesöfen sein muſs. Entweichen aber aus den Kokesöfen die Gase mit hoher
Hitze, so sind sie
arm an Ammoniak; es wird dann der Deckel a abgehoben
und so die Condensationsesse ausgeschaltet.
Zur Darstellung von schwefelsaurem
Ammoniak aus dem Stickstoff der Bruchmoore oder Grünlandsmoore gibt H. Grouven in Leipzig (* D. R. P. Nr. 2709 vom 13. März
1878) folgendes Verfahren an, durch welches es gelingen soll, 98 Procent des
vorwiegend im Pflanzenprotein des Moores enthaltenen Stickstoffes als Ammoniak zu
gewinnen.
Die zur Herstellung von 3500k schwefelsaurem
Ammoniak aus 20 500k Moortrockensubstanz nebst 42
500k zugehörigem Wasser erforderlichenerforlichen Einrichtungen sind auf Taf. 32 in Fig. 4 im
Grundriſs angedeutet, während Fig. 5 und
6 die Schnitte I-II und III-IV zeigen.
Die Moormasse mit dem erforderlichen Feuchtigkeitsgehalt wird durch Menschenhände
oder Maschinenkraft in faustgroſse Stücke zerrissen, auf 100° erhitzt und mit 10
Proc. Wiesenkreide vermischt, um den Schwefelgehalt des Moores zu binden. Die
heiſse, feuchte Moormasse wird dann in sogen. „Ciniröfen“
A destillirt. Die in diesen Oefen stehenden, mit
Sicherheitsventil versehenen fünf Cylinder a sind oben
mit Deckeln verschlossen, nach deren Oeffnen ein Trichter zur Einfüllung der
Moormasse auf die Cylinder aufgesetzt werden kann; während der Füllung ist der im
Ofen befindliche Theil der Cylinder durch den Schieber b gegen Luftzutritt abgesperrt. Nach Füllung des oberen Theiles der
Cylinder und Schluſs der Deckel tritt durch Oeffnen der Schieber b die Moormasse in den erhitzten Theil. Von dem
Verbrennungsraum X für die durch das Rohr m zugeführten Torfgase, deren Zutritt durch das Ventil
n geregelt wird, ist durch die wagerechte
Chamottewand r der Sammelraum z getrennt, in welchen die aus dem Torf entwickelten Gase durch
entsprechende Oeffnungen in der Wand der Cylinder a
einströmen. Die bei der Vergasung der Moormasse gebildete Asche füllt den unteren
Theil des Cylinders, welcher unterhalb des Gasraumes z
in einen mit Wasser gefüllten Behälter y ausmündet,
wodurch die Cylinder unten gasdicht abgeschlossen werden. Um den Stand der Asche in
bestimmter Höhe zu erhalten, ist dieser Behälter mit dem Rührwerk p versehen, durch dessen langsame Umdrehung die Asche
weggeräumt wird.
Aus dem Sammelraume z treten die Gase und Dämpfe nun
durch das Rohr x nach dem unteren Theile der
Ammoniumöfen B, deren 6 Cylinder f mit einer Contactmasse gefüllt und oben und unten mit
Deckeln versehen sind. Die Masse ruht auf siebartigen Unterlagen, welche zur
Beseitigung der unwirksam gewordenen Contactsubstanz entfernt werden können.
Zwischen diesen Sieben und dem unteren Deckel treten die aus dem Torf entwickelten
Gase und Dämpfe in die Cylinder ein, durchströmen dieselben und gehen oben seitlich
durch das Rohr T in den Kühlapparat C. Die aus dem Cinirofen entweichenden Gase bestehen nämlich aus
alkalischen Dämpfen, Kohlenwasserstoff Wasserdampf, Wasserstoff, Kohlenoxyd und
Kohlensäure. Die Durchleitung dieser Gase durch die glühende poröse Masse soll nun
eine Zersetzung des Wasserdampfes mit den Kohlenstoff haltigen Bestandtheilen des
Gases bewirken, so daſs 70 Procent des Kohlenstoffes zu Kohlensäure und 30 Proc. zu
Kohlenoxyd verbrennt, der sämmtliche organisch gebundene Stickstoff aber in
kohlensaures Ammoniak verwandelt wird. Zur Herstellung dieser Contactmasse werden
52k eines 3 bis 4 Proc. Kali enthaltenden,
lufttrocknen Thones mit 250k Wasser unter
beständigem Umrühren gekocht, so daſs ein gleichmäſsiger dünner Thonbrei entsteht;
dann werden 100k gepulverte, lufttrockne
Wiesenkreide und 136k trockne Moorerde zugesetzt.
Aus der so erhaltenen Masse werden Drainröhren von etwa 25mm Durchmesser gepreſst, die nach dem Trocknen in
Stücke zerschlagen und in die Cylinder eingefüllt werden. Hier verliert die Masse
beim Glühen noch 63 Procent ihres Gewichtes, ohne ihr Volum zu verkleinern, so daſs
1l derselben nur 270 bis 300g wiegt. Wesentlich ist es, daſs die Masse 47 bis
50 Proc. Kalk enthält, da selbst 5 Proc. mehr oder weniger bereits einen Einfluſs
auf die Wirkung derselben ausüben. Die im Ofen herrschende Temperatur darf nur
innerhalb geringer Grenzen schwanken, welche mittels eines später zu beschreibenden
Pyrometers bestimmt wird.
Für einen günstigen Erfolg ist es noch wichtig, daſs in die mit der Contactmasse
gefüllten Cylinder keine atmosphärische Luft eintritt, da die Gegenwart von
Sauerstoff die Bildung des Ammoniaks erschwert. Auch darf die Torfmasse keine Stoffe
enthalten, welche beim Glühen Sauerstoff, Chlor oder Schwefel abgeben, da hierdurch
die Ammoniakausbeute ebenfalls verringert wird. Das Gasgemisch muſs 12 bis 13
Stunden mit der glühenden Contactmasse in Berührung bleiben und 2,5mal so viel
Wasserdampf enthalten, als theoretisch zu der angegebenen Zersetzung erforderlich
wäre. Nach je 4 bis 5 Stunden muſs durch die glühende Masse mittels des kleinen
Gebläses O atmosphärische Luft kurze Zeit
hindurchgeblasen werden, um sie wirksam zu erhalten. Nach 4 bis 5 Tage langem
Gebrauch wird sie dann durch frische Masse ersetzt.
Das aus diesen Cylindern austretende Gasgemenge enthält als Vergasungsproducte von
50k des von Wasser freien Moores 1k,75 Stickstoff als Ammoniumcarbonat, gemischt mit
etwa 32cbm Kohlensäure, 14cbm Kohlenoxyd und 88cbm Wasserstoff. Dieses Gasgemisch wird mittels des Saugers L durch das Rohr T
zunächst in den Kühlapparat C gezogen. Hier vertheilen
sich die Gase und Dämpfe von der Vorkammer i aus in die
Röhren c, um dann, nachdem sie etwa ⅔ ihres Gehaltes an
kohlensaurem Ammoniak abgesetzt haben, aus der Kammer k
durch das Rohr V nach den mit Gyps gefüllten Apparaten
F (Fig. 4 und
6) zu gehen, während sich die verdichtete Flüssigkeit im Gefäſs S sammelt, um von hier aus unter Luftabschluſs durch das gebogene
Rohr U nach den Gypsdigestoren G (Fig. 4) zu
flieſsen. Als Kühlflüssigkeit wird das gewonnene schwefelsaure Ammoniak verwendet,
welches durch das Rohr u in den Kühlapparat eintritt
und denselben stark erwärmt durch das Rohr v verläſst,
um auf die Krystallisationspfanne D zu flieſsen.
Um den für die Umsetzung des kohlensauren Ammoniaks erforderlichen Gyps in die
passende Form zu bringen, werden 60k gebrannter
Gyps mit 40k trocknem Wiesenkreidepulver gemischt.
Auf dieses Gemenge läſst man nach und nach 40l
Wasser von 15 bis 20° in Regenform laufen, wodurch sich dasselbe beim Uebergange des
Gypses in Hydrat zu kleinen Kügelchen formt, von denen 1l nur 660 bis 670g wiegt. Bei 300°
getrocknet, muſs ihr Gewichtsverlust sich immer zwischen 32 bis 33 Proc. bewegen.
Die Kreidegypskügelchen bilden, obgleich mit den Fingern leicht zerdrückbar, doch
eine Füllung, die so viele Zwischenräume hat und so porös bleibt, daſs selbst bei
einer Säulenhöhe von 5m dem Gasdurchgang kein
erheblicher Widerstand bereitet wird. Bei Anwendung von Gypskügelchen ohne
Kreidezusatz hat sich gezeigt, daſs die Kügelchen beim Durchströmen der Ammoniakgase
sich bald mit einer schmierigen schwefelsauren Ammoniaklösung überziehen, welche
nicht blos den Gasdurchgang verstopft, sondern auch das Innere der Kugeln der
Einwirkung des kohlensauren Ammoniakgases entzieht. Zur völligen Absorption des
Ammoniaks gebraucht man das 7fache Volum von diesem Gypsschrot für die in 1 Secunde
durchstreichende Gasmenge. Für die vollständige Umsetzung des Ammoniaks ist es noch
wichtig, daſs die Temperatur auf 35 bis 40° erhalten wird, mit welcher die Gase aus
dem Kühlapparate heraustreten. Die Absorptionsapparate F sind daher in einer besonderen Kammer aufgestellt, welche dauernd auf
diesem Wärmegrad erhalten wird. Die Absorptionscylinder sind mit Einsätzen versehen,
welche dieselben bis auf einen Raum im unteren Theile des Cylinders füllen, in den
das Gas in der Pfeilrichtung eintritt. Die Einsätze haben einen siebartigen Boden
und sind vollständig mit Kreidegypsschrot gefüllt. Ihr cubischer Inhalt ist so
bemessen, daſs jedes Gastheilchen beim Durchströmen sämmtlicher Cylinder nahezu 5
Secunden lang mit dem Schrote in Berührung und Wechselwirkung bleibt. Unter Bildung
von kohlensaurem Kalk verwandelt sich das kohlensaure in schwefelsaures Ammoniak.
Die mit schwefelsaurem Ammoniak gesättigte Schrotportion wird nun herausgenommen und
in den Gypsdigestorien G zu dem aus dem Kühlapparat C gewonnenen kohlensauren Ammoniak hinzugeschüttet.
Hier vollzieht sich unter Zusatz von weiterem Stuckaturgyps und bei fortwährendem
Umrühren während der ersten halben Stunde bei Erhaltung der Masse auf 35 bis 40° die
Umwandlung des kohlensauren Ammoniaks in schwefelsaures Ammoniak. Die Digestorien
können behufs
Beschleunigung des Processes mit mechanischem Rührwerk versehen sein. Das
Gesammtresultat ist eine etwa 18procentige Lösung von schwefelsaurem Ammoniak. Diese
Lösung wird nach dem Absetzen in den Behälter J (Fig.
4) abgelassen, aus dem die Pumpe K sie durch
die Filterpresse H drückt. Da diese Presse hoch steht,
so flieſst die Ammoniumsulfatlösung durch das Rohr u
zum Kühler C, aus welchem sie bei v heiſs auf die Krystallisationspfanne D läuft, in der sie weiter abgedampft wird, unter
Zusatz von 1 bis 2 Proc. Kammersäure zur Neutralisation des freien Ammoniaks.
Die Torfgase werden nun, so weit sie nicht im Kühler C
und den Gypsapparaten F verdichtet sind, durch das
Gebläse L weiter geführt. Ein Theil derselben dient zum
Betriebe der Gaskraftmaschine M, welche die beiden
Luftsauger L und O, die
Filterpreſspumpe K, die Rührwerke der
Gypszersetzungsapparate G, die Aschenrührer p, die Drainröhrenpresse bei N, Wasserpumpe und Hebewerke treibt. Der andere Theil der Gase geht durch
das Rohr m und die Ventile n zum Heizen der Oefen A und B, während die Verbrennungsproducte durch die Rohre o und die Ventile s theils
in den Regenerator Q zum Vorwärmen der für beide Oefen
erforderlichen atmosphärischen Luft und den Regenerator P zum Erhitzen der Brenngase, theils aber zur Krystallisationspfanne D und den Vorwärmer E
gehen und von hier in den gemeinschaftlichen Schornstein R entweichen.
Für das erwähnte Pyrometer werden drei Legirungen durch Zusammenschmelzen von 72g, 75g und 80g Kupfer mit bezieh. 28g, 25g und 20g reinem Antimon hergestellt, die sich nach dem
Erkalten leicht in scharfkantige Stücke von 3 bis 5g zerschlagen lassen. In ein 17mm weites
und 1m langes Porzellanrohr (Fig. 7),
welches an einem Ende mit einem Korkstopfen w
verschlossen ist, füllt man etwas Kohlenpulver, dann ein Korn x der ersten Legirung, wieder Holzkohlenpulver und ein
Korn y der zweiten Legirung, dann nochmals Kohlenpulver
und schlieſslich einen Asbestpfropf z. Dieses für die
Ammoniumöfen bestimmte Pyrometer wird in einen der Cylinder desselben eingeschoben.
Schmilzt die zweite Legirung bei y, während die erste
nur an ihren scharfen Kanten abgerundet wird, so ist die Hitze normal; ist sie zu
schwach, so bleibt y ungeschmolzen, ist sie zu stark,
so schmilzt auch x. Dasselbe Pyrometer wird für die
Cylinder des Cinirofens angewendet; nur wird hier bei y
ein Korn der 80procentigen Legirung und bei x ein
solches der 75procentigen Legirung eingeschoben.
Tafeln
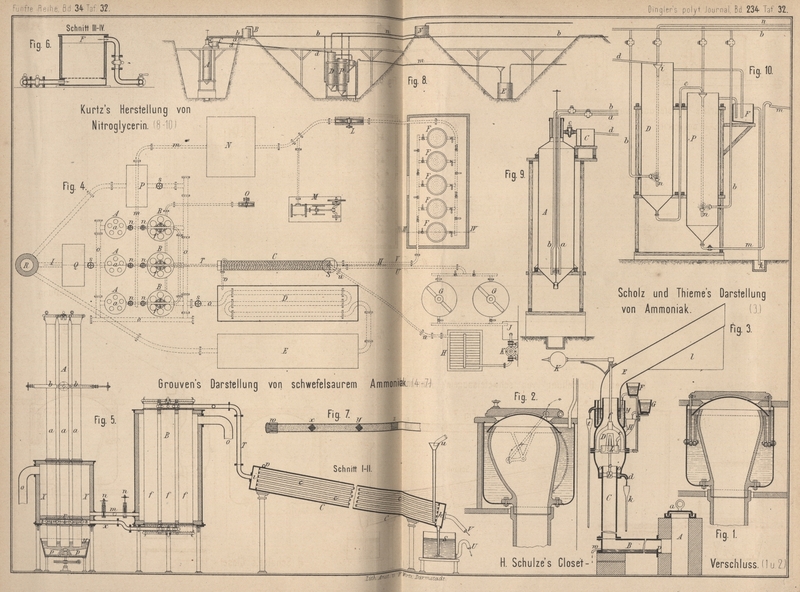