Titel: | Ueber Neuerungen in der Eisenerzeugung. |
Fundstelle: | Band 235, Jahrgang 1880, S. 369 |
Download: | XML |
Ueber Neuerungen in der
Eisenerzeugung.
(Fortsetzung des Berichtes S. 124 dieses
Bandes.)
Mit Abbildungen auf Tafel 38.
Neuerungen in der Eisenerzeugung.
Verbesserungen in dem Verfahren zur Herstellung von Eisen
und Stahl und in den hierzu dienenden Oefen von C.
W. Siemens in London (* D. R. P. Nr. 2495 vom 4. November 1877). Im
Anschluſs an die früheren Besprechungen dieses Verfahrens (1873 208 218. * 209 1.
1875 217 69. 1878 230
84. 181. 506) sei bemerkt, daſs es bei der Reduction der Eisenerze in rotirenden Oefen von groſser Wichtigkeit ist, daſs sich
die Flamme frei in dem Arbeitsraum bewegt, damit ein gleichmäſsiger Hitzgrad erzeugt
und eine vollständige Verbrennung der Gase erzielt wird, welche fast nur aus
Kohlenoxyd bestehen, das theils von auſsen eingeführt, theils im Ofen selbst erzeugt
ist. Dies wird dadurch erreicht, daſs der Durchmesser der rotirenden Kammer A (Fig. 1 Taf.
38) so weit vergröſsert ist, daſs er der Länge derselben nahezu gleicht; ferner wird
die Trennungsmauer b zwischen den zu- und abgehenden
Gasen, wie Horizontal- und Querschnitt Fig. 2 und
3 zeigen, mindestens 35cm dick gemacht
und dadurch dem eintretenden Gasstrome erschwert, sofort wieder auszutreten.
Um die schnelle Zerstörung des Ofenfutters zu verhindern, wird der hintere Boden der
rotirenden Kammer aus starken Eisenplatten hergestellt, auf welche ein U-förmiger
Eisenring mit der Oeffnung nach auſsen angenietet wird. Ein gleicher Ring wird auf
den festen Theil, welcher die Verbindung mit den Regeneratoren herstellt,
aufgenietet. Beide Ringe bilden den Ofenhals. Durch ein durchlöchertes Rohr werden
Wasserstrahlen gegen diesen Hals und den Boden der rotirenden Kammer, sowie auch
gegen den festen Theil, welcher die Verbindung mit den Regeneratoren herstellt,
geleitet und dadurch Backstein- und Eisenoxydfütterung dieser Theile vor dem
Schmelzen bewahrt.
Statt die Regeneratoren wie bisher aus aufgeschränkten Backsteinen aufzubauen, sind
sie hier mit Zickzackkanälen H eingerichtet. Manchmal
ist nur der obere Theil auf diese Weise hergestellt, da sich dort der aus der
rotirenden Kammer kommende Staub am meisten absetzt; der übrige Theil wird dann wie
gewöhnlich construirt, oder es wird die in Fig. 7 und
9 Taf. 38 angegebene Anordnung des Aufschränkens der Backsteine gewählt.
Um den Apparat zu vereinfachen, werden in manchen Fällen die Gasregeneratoren
weggelassen und das Gas in fortdauerndem Strome durch einen aus feuerfestem Material
construirten Kanal in die rotirende Kammer eingeführt. Dieser Kanal liegt zwischen
den beiden Luftregeneratoren, deren Querschnitt und Heizfläche in diesem Falle
vergröſsert wird. Die Generatoren G werden nahe an den
Ofen gelegt, um jeden Wärmeverlust zu vermeiden, und zur Regelung der Gaszuströmung
werden Ventile aus feuerfestem Thon verwendet. Die durch das Umsteuerungsventil h in die Zickzackkanäle eingetretene Luft geht erhitzt
abwechselnd durch den einen der nach den Regeneratoren E und F führenden Kanäle c oder e, während die
Verbrennungsgase jeweilig durch den anderen entweichen.
Gegen den hinteren Theil des Ofens um den Hals a
desselben liegt ein ringförmiger Behälter aus Eisenblech f (Fig. 5 Taf.
38), welcher mit Wasser gefüllt ist. Die Kammer ist zu diesem Zweck auf ihrem
Umfange mit einer Reihe von Ventilen f2 versehen, welche, wie aus
Fig.
6 näher ersichtlich, durch Federn auf ihren Spitzen gehalten werden. Die
Ventilstangen sind mit kleinen Rollen versehen, welche, wenn sie bei der Umdrehung
der Kammer in die Höhe kommen, gegen eine feste Schiene f3 anstoſsen und von dieser niedergedrückt
werden; dies öffnet die Ventile und hält dieselben eine Zeitlang offen, so daſs eine
gewisse Menge des in der Kammer enthaltenen Wassers entweichen und in den Behälter
z flieſsen kann, während frisches kaltes Wasser
durch das Rohr f1 in
dem Maſse, als die Oeffnungen unter demselben weggehen, zuflieſst und die Kammer
kühl hält.
Die zur Erhitzung der Luft dienenden Regeneratoren E und
F (Fig. 2)
bestehen aus einer Anzahl horizontaler Kanäle H (Fig.
1 und 3) aus
feuerfesten Steinen, durch welche die Feuergase nach dem zum Schornstein führenden
Kanäle S abgehen. Zur Reinigung sind in den Mauern
Oeffnungen angebracht, welche durch die Thüren g
geschlossen werden können, während die gröſseren Thüren g1 mit Backsteinen und Sand verschlossen
werden. Die oberen Kanäle sind höher als die unteren und werden durch Querriegel o (Fig. 1) aus
Backsteinen versteift.
Der direct von der senkrechten Leitung i des Generators
G führende Gaskanal d
ist in der Scheidewand b angebracht, welche die beiden
Regeneratoren von einander trennt, so daſs das Gas sich auf seinem Wege durch diesen
Kanal etwas erwärmt, bevor es durch die vorspringende Düse d1 in die rotirende Kammer eintritt. Die
Menge des zutretenden Brenngases wird entweder durch eine Klappe oder durch ein
Ventil v im Kanal i
geregelt. In dem Trichter t (Fig. 4) des
Generators befinden sich zwei Beschickungsregulatoren, bestehend aus zwei
cylindrischen Behältern, welche in einer äuſseren Hülse liegen und an einem Punkte
ihres Umfanges eine groſse Oeffnung haben, so daſs, wenn man sie mit Hilfe der
Schnecke und des Getriebes n abwechselnd dreht, sie
sich aus dem Trichter mit Kohle füllen und ihren Inhalt alsdann in den Gasgenerator
entleeren, welcher auf diese Weise in regelmäſsigen Zwischenräumen mit einer stets
gleichen Menge Brennmaterial beschickt wird.
Die Darstellung des Eisens geschieht in folgender Weise. Nach
Herstellung der Oxydfütterung beschickt man den Ofen mit Erz oder einem Gemenge von
Erz und den Fluſsmitteln und Kohle oder anderen Reductionsmitteln, wozu es in
manchen Fällen vortheilhaft ist, noch eine gewisse Menge von granulirtem Guſs in
Bruchstücken zu fügen. Wenn nach 2 stündiger Heizung und Drehung die Reduction des
Metalles vollendet ist, beginnen die Gangart des Erzes und die Fluſsmittel zu
schmelzen und es entsteht eine verhältniſsmäſsige eisenarme Schlacke, welche man
durch ein vorn am Ofen angebrachtes Abstichloch auslaufen läſst.
Hierauf wird zum Schweiſsen des Eisens der Hitzgrad und die
Umdrehungsgeschwindigkeit vergröſsert, bis sich eine oder mehrere Luppen gebildet
haben, welche alsdann herausgenommen und wie gewöhnlich gezängt werden. Wenn die
Luppen zum Zängen nicht heiſs genug sind, so bringt man dieselben in einen
Schweiſsofen mit Schlackensohle, was den Vortheil hat, daſs das Eisen vollständig von Schlacke
gereinigt und in seinen physischen Eigenschaften verbessert wird. Die Zugabe von
Guſseisen bezweckt die Erzielung eines heftigen Aufwallens des reducirten Eisens,
wenn es sich zu Luppen formt; durch dieses Aufwallen wird die Ausstoſsung der
fremden Stoffe erleichtert und überdies der Vortheil erzielt, daſs das auf diese
Weise dargestellte Eisen einen Zusatz von etwas Kohlenstoff enthält, an welchem das
direct aus den Erzen dargestellte Eisen stets Mangel hat.
Die Schlacke, welche nach Herausnahme der Luppen in dem Ofen
zurückbleibt, ist verhältniſsmäſsig reich an Eisen; man vermengt dieselbe mit etwas
Walzhammerschlag oder anderem reichhaltigen Eisenoxyd und läſst das Gemenge im Ofen
erhärten, während man diesen entweder unter einem von auſsen aufgespritzten
Wasserstrahl langsam dreht, oder indem man ihn in Ruhe läſst, wenn man eine flache
Stelle in der Fütterung herstellen will, durch welche das Rutschen der folgenden
Beschickung vermieden wird. Dieses Rutschen wird auch dadurch verhindert, daſs man
in das stehende Bad der noch flüssigen Schlacke groſse Stücke von Eisenerz oder
anderen feuerfesten Stoffen einwirft.
Soll flüssiges Metall gewonnen werden, so ist eine Fütterung von
Kohlenstoff am geeignetsten. Dieselbe kann von dem aus den Gasretorten kommenden
Graphit, von Koke oder Anthracit gemacht werden. Zu diesem Zwecke werden die Stoffe
pulverisirt, mit feuerfestem Thon oder Theer vereinigt, an Ort und Stelle
festgestampft und dann erhitzt.
Der Schmelzofen, welchen C. W.
Siemens jetzt zur Umwandlung von Eisen in Stahl mit Zugabe von Guſs und
Roherz und mit oder ohne Zugabe von Abfalleisen verwendet, unterscheidet sich, wie
die Schnitte Fig. 7 und
8 Taf. 38 zeigen, dadurch von den früheren Oefen, daſs sich jede
Luftzuströmungsöffnung k von ihrem Regenerator K hinter einer entsprechenden Oeffnung l der Gasregeneratoren L
erhebt, so daſs der wagrechte Luftstrom oberhalb des senkrechten Gasstromes in den
Ofen eintritt. Ferner ist wesentlich, daſs jede Lufteinmündung breiter ist als die
entsprechende Gaseinmündung, so daſs das Gas von der Luft auf drei Seiten umhüllt
wird. Die Schaulöcher m hinter den Luftkanälen werden
durch Stopfen verschlossen. Die Regeneratoren bestehen aus einer Reihe senkrechter
Wände aus feuerfesten Steinen, welche, wie Fig. 7 und
9 zeigen, durch enge Zwischenräume von einander getrennt sind und durch
feuerfeste Querriegel versteift werden. Sie sind so eingerichtet, daſs die auf- oder
absteigenden Ströme oftmals getheilt werden und alle Theile derselben mit der
Oberfläche der Wände, von welchen sie Wärme empfangen, oder denen sie ihre Wärme
abgeben, in Berührung kommen. In Folge dessen können die Regeneratoren viel leichter
gereinigt werden, als bei den früheren Constructionen der Fall war. Die
Luftregeneratoren K können dieselbe Einrichtung haben.
Da dieselben jedoch der Ablagerung des Ofenstaubes weniger ausgesetzt sind, so
können sie in der bisherigen Weise mit Aufschränkungen gebaut werden. Zwischen den
beiden Regeneratorpaaren befindet sich ein Kanal n,
welcher mit den Hohlräumen o unter und an den Seiten
der Ofensohle in Verbindung steht, so daſs die Luft in diesen Räumen sich frei
bewegen kann, wodurch Sohle und Wände des Ofens wirksam kühl gehalten werden. Sollte
Metall durch die Sohle abflieſsen, so fällt dasselbe auf eine zu diesem Zweck in dem Kanäle n aufgeschüttete Sandschicht, von wo es leicht entfernt
werden kann.
An der Seite der Schmelzkammer sind Oeffnungen q (Fig.
8 und 10) in
solcher Höhe angebracht, daſs man die auf dem Metallbade schwimmenden Schlacken
entweder ununterbrochen oder zeitweilig ablassen kann, ohne daſs man das Metallbad
selbst abzustechen braucht.
Hat man sich durch eines der bekannten Mittel davon überzeugt,
daſs das Metall hinlänglich entkohlt ist, so sticht man dasselbe in eine Gieſskelle
ab, welche mit feuerfestem Thon gefüttert und im Innern durch eine Gasflamme zur
Rothglut erhitzt wird. ½ Stunde vor dem Abstich wirft man reichhaltiges Spiegeleisen
und kieselhaltiges Ferromangan in kleinen Stücken in die Gieſskelle und vertheilt
dasselbe auf dem Boden der Kelle, woselbst es erhitzt und dann von dem aus dem Ofen
kommenden Metalle leicht in Fluſs gebracht wird. Der übrige Theil des Spiegeleisens
wird dem Metallbade vor dem Abstiche zugesetzt.
Die erforderliche Menge des beizugebenden kieselhaltigen
Ferromangans hängt von dem Silicium- und Mangangehalte ab, welchen man dem Metalle
zu geben wünscht, und einer der Hauptvortheile dieses Processes besteht darin, daſs
das Mangan oder Silicium sich nicht oxydiren kann, man daher im Stande ist, dem
Metalle eine vorher ganz bestimmbare Menge Mangan und Silicium beizugeben.
Gleichzeitig wird dabei an Mangan gespart und die Fabrikationsmittel werden
vereinfacht.
Will man alte Eisen- oder Stahlschienen oder andere Abfälle in
Guſsstahl umwandeln, so bringt man einen Theil derselben in den Ofen und füllt den
Rest noch im Verhältniſs von 3 Th. Eisen oder Stahl zu 1 Th. Guſs. Es ist rathsam,
diese Stoffe vorher zu erhitzen, ehe man sie in den Ofen bringt. Man ändert hierauf
nach Bedarf die Natur des Bades durch Zugabe von Metall oder Erzen vor dem Einführen
von Spiegeleisen oder Ferromangan, welches in der oben angegebenen Weise bewirkt
wird.
Schachtofen zum Reinigen von Roheisen. Wenn man nach
Fr. Krupp in Essen (* D. R. P. Kr. 7117 vom 1.
August 1878) in einem Schachtofen, welcher mit Eisenerzen, Bauxit, Magnesia,
Kohlenschiefer oder einem anderen basischen Futter ausgestampft ist, oder ein
vorwiegend aus Kohlenstoff bestehendes Futter hat, oder aber aus einem
doppelwandigen Gefäſse besteht, zwischen dessen Doppelwänden sich Kühlwasser bewegt
und dessen Herd oder Vorherd eine basische oder neutrale Ausstampfung hat, Roheisen
mit basischen Eisenoxyden mit oder ohne Zuschlag von Manganoxyden und Kalk
herunterschmilzt, so verliert das Eisen den gröſsten Theil seines Gehaltes an
Mangan, Silicium, Schwefel und Phosphor. Auſserdem wird ein Theil des Erzes reducirt
und so das Ausbringen vergröſsert. Ob der Kohlenstoff des Eisens angegriffen wird,
ist bei dieser Reinigung im Schachtofen gleichgültig, da hier bei genügender Koke
das Schmelzproduct stets mit einer Temperatur in den Herd oder Vorherd gelangen
muſs, die höher ist als der Schmelzpunkt des Endproductes, möge dieses nun Guſseisen
oder schon Stahl sein. Das im Schachtofen zu reinigende Eisen braucht daher kein
Mangan zur Conservirung des Kohlenstoffes zu enthalten. Das Eisen würde nur dann an
seiner Dünnflüssigkeit verlieren, wenn noch im Herde oder Vorherde eine wesentliche
Entkohlung stattfände. Am besten wird sich für das vorliegende Verfahren der Ofen mit gekühltem Schachte
ohne Ausfütterung des Schmelzraumes eignen, da sich hier die Wände von selbst mit
einer Erzschicht überziehen und somit alle Reparatur im Schmelzraum vermieden wird.
Als Boden des Schachtes kann man ebenfalls ein Kühlgefäſs anwenden und einen mit
Kohlenfutter versehenen, leicht auswechselbaren Vorherd.
Der obere Theil eines solchen Ofens A (Fig. 11
Taf. 38) ist an der Gichtbühne B aufgehängt; der Wind
tritt rund um den Schacht durch den Schlitz a ein. Das
flüssige Eisen läuft durch das in der Mitte des gekühlten Schachtbodens befindliche
Loch b in den fahrbaren Vorherd B, welcher bei c gegen den Schacht durch eine
leichte Ausschmierung abgedichtet wird.
Um die Reinigung möglichst vollkommen zu machen, empfiehlt es sich durch eine hoch
angebrachte Düsenreihe die eigentliche Schmelzzone des Ofens möglichst in die Höhe
zu rücken, so daſs die Beschickung schon über dieser Hauptdüsenreihe schmilzt,
während eine oder mehrere untere Düsenreihen nur dazu dienen, das geschmolzene Eisen
nachzuheizen. Da man aber in der Höhe des Ofens beschränkt ist, so kann man mit
Vortheil einen Etagenofen derart anwenden, daſs der
untere Ofenschacht den Vorherd des oberen Ofenschachtes bildet. Beim Austreten aus
einem oberen Schachte kann man das Eisen mit dem Erz in den unteren Schacht laufen
lassen, in welchem Falle man nur den Weg der flüssigen Massen verlängert, oder man
kann bei diesem Austreten auch wieder durch einen Ueberfall das Eisen von der
Schlacke trennen.
Einen solchen Ofen zeigt Fig. 12
Taf. 38 im Durchschnitt. Eisen und Erz werden zuerst in dem Schacht A heruntergeschmolzen. Das flüssige Eisen läuft,
während die Schlacke in den Schlackenüberfall D durch
das Loch a abflieſst, bei b in den zweiten Schacht B des Etagenofens,
in welchem es mit frischem Erz und Koke heruntergeschmolzen wird. Das fertig
gereinigte Eisen gelangt durch den Schlackenüberfall E
bei d in den fahrbaren Vorherd C, während die Schlacke bei c überflieſst.
Beide Schächte des Ofens sind mit oberen Haupt- und unteren Nebendüsen versehen.
Durch diese Doppelreinigung kann ein Eisen mit 1,6 Proc. Phosphor leicht auf 0,1
Proc. gebracht werden, da jeder Ofen etwa 75 Procent des Phosphorgehaltes
entfernt.
In einem niedrigen kleinen Versuchsofen ohne Vorherd mit einem
Futter von Graphit wurden aus einem Roheisen von untenstehender Zusammensetzung
folgende Abstiche erhalten:
Roheisen
I
II
III
IV
V
Kohlenstoff
3,73
3,43
3,43
3,00
3,40
3,40
Silicium
0,47
0,002
0,002
0,004
0,005
0,002
Mangan
3,56
0,45
0,35
0,128
0,210
0,470
Kupfer
0,25
–
–
–
–
–
Phosphor
0,60
0,273
0,20
0,136
0,187
0,210.
Das Reinigungserz hatte 98,2 Proc. Eisenoxyd, 0,1 Proc.
Manganoxydul, 0,1 Proc. Kalk, 0,54 Proc. Phosphorsäure, 1,1 Proc. Wasser und Gangart. Beim
Herunterschmelzen der ersten 600k Eisen war der
Ofen noch sehr wenig gefüllt, so daſs, wie Analyse I zeigt, noch 0,273 Proc.
Phosphor in dem abflieſsenden Eisen enthalten waren. Besser stellte sich der zweite
Abstich des schon mehr gefüllten Ofens, während erst der dritte (III) als völlig
normal angesehen werden kann; das Eisen war dünnflüssig und trennte sich vollkommen
von der Schlacke. Bei IV und V war der von den flüssigen Massen im Ofen durchlaufene
Weg wieder kürzer, in Folge dessen der Phosphorgehalt wieder etwas gröſser. Die an
Phosphor reichste Schlacke, welche erhalten wurde, hatte folgende
Zusammensetzung:
Kieselsäure
17,60
Eisenoxydul
41,28
Manganoxydul
26,30
Thonerde
7,25
Kalk
1,46
Magnesia
0,36
Phosphorsäure
5,28
Schwefel
0,66.
Das Zuschlagen von Kalk bei dem Processe wird den Gebrauch von bedeutend weniger Erz
ermöglichen, da die Kieselsäure der Kokes dann von Kalk und nicht von Erz gebunden
wird.
Dieses Reinigungsverfahren kann nach Krupp auch am
Hochofen in der Weise ausgeführt werden, daſs man das aus dem Hochofen flieſsende
Eisen durch einen hohen, mit Erz und Kokes oder mit Erzbriquettes gefüllten
Cupolofen oder Etagenofen laufen läſst, oder indem man das Eisen in eine Pfanne
absticht, diese über einen Cupolofen bringt und das Eisen durch eine möglichst
kleine Oeffnung in den Cupolofen auslaufen läſst. Das Verfahren eignet sich ferner
nicht nur für die weitere Verarbeitung des flüssigen Eisens im Siemens-Martin-Ofen
oder im vereinigten Flamm- und Bessemer-Ofen u. dgl., es eignet sich auch ganz
besonders für den Puddelproceſs, bei welchem dann nochmals Phosphor entzogen wird.
Aus dem Cupolofen kann man ganz nach Bedarf das gereinigte Eisen entnehmen und es
flüssig in den Puddelofen bringen, dessen Herd, da das Eisen fast frei von Mangan
und Silicium ist, nicht in der Weise angegriffen werden kann, wie es sonst beim
Beschicken mit flüssigem Eisen der Fall ist.
Tafeln
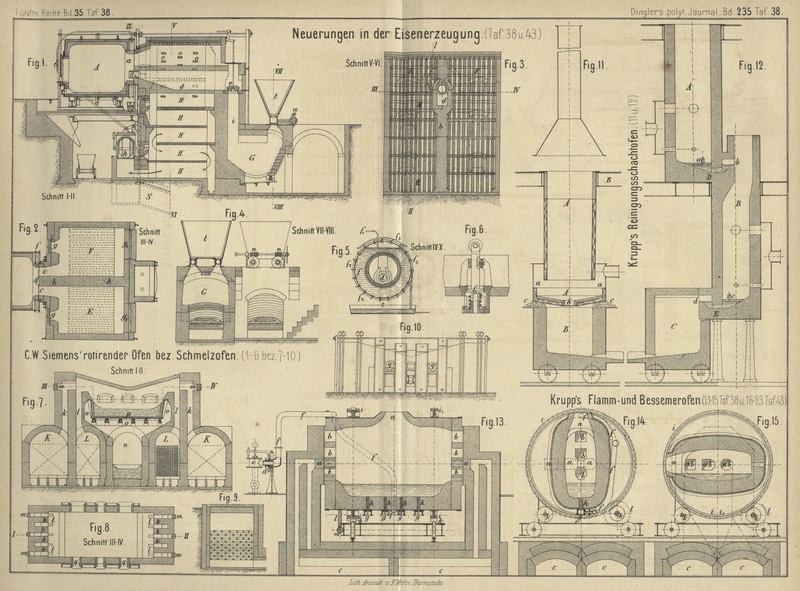