Titel: | Ueber Neuerungen im Eisenhüttenwesen. |
Fundstelle: | Band 243, Jahrgang 1882, S. 398 |
Download: | XML |
Ueber Neuerungen im Eisenhüttenwesen.
Patentklasse 18. Mit Abbildungen im Text und auf
Tafel 33.
(Fortsetzung des Berichtes S. 121 Bd.
242.)
Ueber Neuerungen im Eisenhüttenwesen.
Auf der Herbstversammlung des Iron and
Steel Institute (vgl. Engineer, 1881 Bd. 52 *
S. 271 ff.) sprach W. D. Allen aus Sheffield über eine
beim Bessemern benutzte mechanische Vorrichtung, um eine
innige Mischung des in die Gieſspfanne ausgegossenen Metalles mit dem
Spiegeleisen oder dem Ferromangan zu erzielen. Der Apparat besteht aus
einer verticalen Welle, welche an einer passenden Stelle der Gieſsgrube in zwei
Wandlagern gelagert ist und mittels Kegelräder a von
irgend einem Motor aus in Umdrehung versetzt werden kann.
Textabbildung Bd. 243, S. 398
In den unteren Theil des Wellenschaftes wird ein Bolzen
eingesetzt, dessen unteres Ende zwei schraubenförmig gebogene Flügel von etwa 630mm Länge, 130mm
Höhe und 12mm Dicke trägt. Befindet sich das
Metallgemisch in der Gieſspfanne, so dreht man diese unter den Apparat, hebt sie,
bis der Bolzen und die Flügel unter der Schlackendecke in das Metallbad eintauchen,
und versetzt die Welle in Umdrehung. Bolzen und Flügel sind mit feuerfestem Thon
umkleidet und dann geschwärzt. Während der Drehung kann man behufs vollständigerer
Erreichung des Zweckes die Gieſspfanne auf- und absteigen lassen. Bei diesem Vorgang
werden groſse Mengen theils mechanisch eingeschlossenen, theils durch die innigere Mischung des
Spiegeleisens bezieh. Ferromangans mit dem Bessemermetall neu erzeugten Gases frei.
Die aus dem so behandelten Metall gegossenen Blöcke sind vollkommen gesund, ohne
Blasen, und geht das Gieſsen ebenso ruhig wie das von Tiegelguſsstahl von statten.
In den Werken der Henry Bessemer Company in Sheffield
ist ein solcher Apparat schon seit 3 Jahren in Thätigkeit. – Kupelwieser's Vortrag ist bereits S. 42 d. Bd. wiedergegeben.
In einem auf derselben Versammlung von S.
G. Thomas und Gilchrist gehaltenen Vortrage
wurde darauf aufmerksam gemacht, daſs beim basischen
Proceſs das Ausbringen für jedes Birnenfutter geringer ist als beim sauren
Verfahren und daſs in Folge dessen Einrichtungen zum öfteren und leichteren
Auswechseln der Birnen getroffen werden müssen, daſs jedoch eine Vergröſserung der
Dampfkessel-, Gebläsemaschinen- und der Krahn-Anlagen beim Arbeiten mit basischem
Futter nicht nothwendig ist. In Deutschland macht je eine von zwei mit 3 Birnen
versehenen Gieſsgruben in 24 Stunden 24 und mehr Hitzen. In einer nach dem
Holley'schen System gebauten Anlage (vgl. 1881 239 * 132) mit 2 Birnen würde die
Zahl der Hitzen auf 50 steigen können. Es hängt dies von der Dauer des Futters ab.
Groſse Ausbesserungen am Futter müssen jetzt nach 35 bis 90, durchschnittlich nach
56 Hitzen vorgenommen werden. Richards bessert die
Birnen mittels eines flüssigen Gemisches von Kalkstein mit Theer aus, ohne erstere
abzukühlen. Man ist dadurch im Stande, ein ganz abgenutztes Futter in 15 Stunden
wieder herzustellen. Die basischen Böden halten gewöhnlich wie die sauren 14 Hitzen
aus; besondere Düsen werden nicht eingesetzt, sondern der Boden um Stahlstäbe
gestampft. Im Durchschnitt braucht man auf 1t
Stahl etwas weniger als 50k feuerfestes Material.
Diesem steht ein Verbrauch von 30k an Ganister und
Düsen beim sauren Proceſs gegenüber. Der Aufwand an Kohle für 1t feuerfesten Materials
beträgt beim basischen Verfahren 850k bis 3t,5. Auf einigen Werken, wo das Material im
Cupolofen gebrannt wurde, brauchte man 750 bis 1050k Kokes für 1t feuerfesten Materials.
Bei guten Ofenconstructionen scheinen jedoch 1200k
Kohlen oder 800k Kokes zu genügen. Die Kosten des
basischen Materials belaufen sich je nach der Gegend auf 20 bis 27 M. für 1t, eingerechnet den Theer, auf 1,50 M. für 1t fertigen Stahles. An Zuschlagskalk braucht man
im Durchschnitt 13,5 bis 17,5 Procent des Roheisens oder 150k für 1t Stahl.
Die Schlacke kann man als Zuschlagsmaterial beim Hochofen verwerthen und ersetzt sie
wegen ihres Eisen-, Mangan-, Kalk-, Magnesia- und Phosphorgehaltes mehr als eine
gleiche Menge Kalkstein. Der Abbrand beträgt im Durchschnitt 15 gegen 12 Proc. beim
sauren Verfahren. Die Dauer des Blasens einschlieſslich Nachblasen beträgt 13 bis 25, im
Durchschnitt 18 Minuten. In den meisten Werken wird weiſses Roheisen verblasen. Richards in Eston jedoch benutzt weiſses, graues und
verschiedentlich halbirtes Roheisen. Zu Creusot und in Eston wird das Eisen direct
vom Hochofen genommen.
Einige interessante Angaben über die Homogenität von Stahlblöcken gab G. J. Snelus
aus Workington (vgl. Engineering, 1881 Bd. 32 S. 397).
Angeregt durch frühere Versuche von Stubbs, nach
welchen in sich abkühlenden Stahlblöcken Kohlenstoff, Schwefel und Phosphor sich in
dem am längsten flüssig bleibenden Kerne des Guſsblockes ansammeln, stellte Snelus einen Stahlblock von 2m,130 Höhe und 470mm Seitenlänge her. Derselbe bestand aus absichtlich gröſsere Mengen
Unreinigkeiten enthaltendem Bessemerstahl und wurde in der Sandform einem fast
48stündigen Erkalten überlassen. Sodann wurde eine Scheibe 535mm vom Kopfe und eine andere 110mm vom Boden abgeschnitten. Während erstere ein
vollständig blasiges Aussehen hatte, war letztere vollkommen dicht. Von beiden
Stücken genommene Bohrproben hatten folgende Zusammensetzung:
Kopf
Boden
Eisen
98,304
99,038
Kohlenstoff
Graphitchemisch gebund
0,760
0,350
Silicium
Spur
Spur
Schwefel
0,187
0,044
Phosphor
0,191
0,044
Mangan
0,558
0,514
–––––––
––––––
100,000.
99,990.
Die Richtigkeit dieser Analysen wurde durch eine Wiederholung derselben von zwei
verschiedenen Personen bestätigt. Es wurden sodann von jeder Scheibe 6 Bohrproben
genommen, welche auf einer Linie von einer Ecke bis zum Centrum des Metallblockes
neben einander lagen. Diese Proben zeigten folgende Zusammensetzung:
Nr.
Kopf
Nr.
Boden
Kohlenstoff
Schwefel
Phosphor
Kohlenstoff
Schwefel
Phosphor
1
0,44
0,032
0,044
1
0,44
0,048
0,060
2
0,54
0,048
0,060
2
0,42
0,056
0,062
3
0,57
0,080
0,086
3
0,41
0,048
0,054
4
0,61
0,096
0,097
4
0,40
0,048
0,054
5
0,68
0,120
0,111
5
0,38
0,048
0,058
6
0,77
0,187
0,142
6
0,37
0,044
0,052
Die Probe 6 wurde der Mitte des Guſsblockes entnommen.
Bei schnell erkaltenden, z.B. in Eisenformen gegossenen Blöcken ist natürlich die
Zusammensetzung der Schichten nicht so verschieden.
Von einem Siemens-Martin-Guſsblock, für die Blechfabrikation bestimmt, 1m,065 hoch, mit 535mm bezieh. 431mm Seitenlänge am Kopf und
560mm bezieh. 458mm Seitenlänge am Fuſse, wurden 2 Scheiben geschnitten, die eine 260mm vom Boden, die andere 110mm vom Kopf. Die Bohrproben hatten folgende
Zusammensetzung:
Kopf
Boden
Eisen
99,324
99,356
Kohlenstoff
Graphitchemisch gebund
0,210
0,190
Silicium
–
–
Schwefel
0,056
0,044
Phosphor
0,068
0,050
Mangan
0,342
0,360
–––––––
–––––––
100,000.
100,000.
Ein gewöhnlicher Bessemerschienenblock von 1m,26 Höhe und 295mm bezieh. 350mm Seitenlänge am Kopf
bezieh. Boden, aus welchem 320mm von ersterem und
90mm von letzterem 2 Scheiben geschnitten
waren, zeigte folgende Zusammensetzung:
Kopf
Boden
Eisen
98,723
98,759
Kohlenstoff
Graphitchemisch gebund
0,420
0,420
Silicium
Spuren
Spuren
Schwefel
0,046
0,039
Phosphor
0,056
0,044
Mangan
0,755
0,738
–––––––
–––––––
100,000.
100,000.
Man sieht aus den beiden letzten Analysen, daſs die
Verschiedenheiten in der Zusammensetzung der einzelnen Partien von kleineren und
schnell abgekühlten Guſsblöcken nicht so groſs sind, als daſs dadurch auch
wesentliche Unterschiede in den physikalischen Eigenschaften herbeigeführt werden
könnten. Bei groſsen Guſsblöcken sind diese Thatsachen aber sehr wohl in Rechnung zu
ziehen und können darauf leicht bis jetzt unerklärliche plötzliche Brüche von
Stahlconstructionen zurückgeführt werden. So besaſs z.B. die Bodenprobe des ersten
groſsen Metallblockes, nachdem sie zu einer Stange ausgeschmiedet worden, eine
Tragfähigkeit von 7231k für 1qc, die Kopfprobe dagegen nur eine solche von
5240k. Dabei sei noch erwähnt, daſs sich die
obere Scheibe nur schwer, die untere dagegen sehr leicht schneiden lieſs.
Die Eggertz'sche Kohlenstoffprobe,
wie man sie gegenwärtig in Bessemerwerken allgemein anwendet, erweist sich, wie man
neuerdings oftmals zu bemerken Gelegenheit hatte und wie im Engineering and Mining Journal, 1881 Bd. 32 S. 168 näher ausgeführt ist,
als nicht genau, wenn der zu untersuchende Stahl gehärtet ist. So wurde z.B. der
Kohlenstoffgehalt eines Stahles mittels der Eggertz'schen Methode vor dem Härten auf
0,8 Proc. bestimmt, dagegen nach dem Härten auf nur 0,55 Proc. Nach dem Tempern wies
die Farbe der Lösung wieder auf einen Gehalt von 0,8 Proc. Die Gegenwart von Mangan
scheint die Richtigkeit der Probe nicht zu beeinfluſsen, so daſs man sie sogar zum
Bestimmen des Kohlenstoffes im Ferromangan benutzen kann.
Die Gegenwart von Phosphor, Schwefel und Kupfer, allein oder in Verein mit Mangan,
wirkt ebenfalls auf die Richtigkeit der Probe nicht störend ein. Dasselbe ist der
Fall mit Silicium, Nickel und Vanadium. Chrom gibt der Lösung eine graublaue Färbung,
welche erst nach starker Verdünnung verschwindet. Aehnlich wirkt Kobalt. Statt die
Musterproben aus einer Lösung von Zucker in Alkohol herzustellen, verwendet Eggertz für dieselben die Chloride von Eisen, Kobalt
und Nickel (vgl. Wagner's Jahresbericht, 1881 S. 8). Man kann auf diese Weise röthlich, grünlich und
bräunlich gefärbte Lösungen erhalten. Indem man neutrale Chloride benutzte und 1,5
Proc. Salzsäure haltiges Wasser bei Eisenchlorid, 0,5 Proc. Salzsäure haltiges
Wasser bei den beiden anderen Chloriden zusetzte, erhielt man Lösungen, welche 0g,01 Metall in 1cc enthielten. 8cc der Eisenlösung
wurden sodann mit 6cc Kobalt- und 3cc Nickellösung unter Hinzufügung von 0,5 Proc.
Salzsäure haltigem Wasser gemischt und wurde so eine künstliche, unveränderliche
Musterprobe hergestellt, welche dieselbe Färbung hatte wie eine Eisenlösung, von
welcher 1cc 0,1 Proc. Kohlenstoff enthält.
Ramdohr, Blumenthal und Comp. in Halle a. S. lieſsen
sich ein neues Verfahren zur Herstellung von basischem
Ofenfuttermaterial (D. R. P. Nr. 16271 vom 1. März 1881) patentiren,
welches in fertig gebranntem Zustande nur aus Magnesia besteht. Die Herstellung des
Materials geschieht durch innige Mischung von bei sehr hoher Temperatur und bei 300
bis 400° gebrannter Magnesia mit Eisenoxyd und einer Chlormagnesiumlösung. Die Menge
der wenig gebrannten Magnesia beträgt ⅙ bis ⅕ der ganzen Mischung, während für die
Lösung eine Concentration von etwa 30° B. am passendsten gehalten wird. Letztere
dient nur dazu, der Mischung die nöthige Plasticität zu geben, während das Eisenoxyd
beim späteren Brennen der Masse das Chlor als Eisenchlorid austreiben soll. Die
festen Körper werden vor der Mischung fein pulverisirt, dann mit der Lösung
angemacht, um als fertige Masse zum Ausstampfen von Oefen oder, unter vorheriger
starker Zusammenpressung, zum Formen von Düsen, Steinen, Retorten u.s.w., welche
nach der Erhärtung in stärkster Weiſsglut gebrannt werden, verwendet zu werden.
Das Patent von Franz Melaun in
Königshütte (* D. R. P. Nr. 15761 vom 24. Februar 1881) bezieht sich auf eine Einrichtung der Bessemerbirnen, um während des
Betriebes einen schadhaften Boden auswechseln zu können, ohne die Birne von innen
abkühlen zu müssen (vgl. 1881 240 * 305). Zu diesem Zwecke ist der Birnenmantel bei
c (Fig. 11
Taf. 33) fast auf seinem ganzen Umfange durchbrochen und ist hier zwischen dem
oberen und unteren Futter a bezieh. b eine Fuge gelassen. Der innere Durchmesser des
Futters b ist bedeutend gröſser als der des oberen, so
daſs der cylindrische Boden in einer horizontalen Ebene mit a zusammenstöſst. Der Boden wird durch den mit dem Mantel fest verbundenen
Windkasten in die Birne eingepreſst und kann man ihn, um dabei eine Deformation des
oberen Theiles zu vermeiden, mit einer leichten Blechhülle umgeben (vgl. 1881 242 128).
Nachdem der Boden in gewöhnlicher Weise im Windkasten befestigt ist, wird die Fuge
c mit Façonsteinen von auſsen sorgfältig
ausgemauert und zuletzt der Ring r heruntergeschoben,
so daſs ein Auseinandertreiben der Steinlage unmöglich gemacht ist. Die Einrichtung
scheint ganz praktisch zu sein und kann beim basischen Betrieb eine gewisse
Erleichterung schaffen. Nur ist nicht recht verständlich, weshalb Melaun einen cylindrischen
Boden verwendet. Ein conisch gestalteter Boden läſst sich viel dichter und fester in
sein Lager pressen als ein cylindrischer. Die Herstellung des richtigen
Verhältnisses zwischen Conicität und Höhe böte keine Schwierigkeiten.
Um beim Ersatz von schadhaften Düsen nicht allein diese durch neue ersetzen zu
können, sondern auch den im Boden um dieselben ausgebrannten Raum mit feuerfester
Masse auszufüllen, führt Melaun (* D. R. P. Nr. 15088
vom 3. März 1881) durch eine besondere Oeffnung in der Wölbung der Haube einen
starken Vorhalter g (Fig. 12
Taf. 33) in die Birne ein, welcher den Boden über der ausgebrannten Stelle a bedeckt, und preſst nun die plastische (erforderlichen Falles mit einem dünnen Blechmantel umgebene)
Düse, deren Masse um das dem ausgebrannten Raum entsprechende Volumen gröſser
genommen wird, als sie eigentlich sein sollte, in die betreffende Stelle ein. Der
Preſsstempel b besitzt Nadeln, welche die Windkanäle
der Düse ausfüllen. Um ein Auseinandertreiben des unteren Düsenendes beim Einpressen
zu verhindern, wird der Stempel b in einem auf die
Bodenplatte d gesetzten Cylinder c geführt. Will man gebrannte Düsen verwenden, so
müssen sie behufs Ausfüllung des Raumes a mit einem
plastischen Kopf versehen sein. Der Vorhalter g besteht
aus einer starken Stange, welche am unteren Ende eine excentrische Scheibe p trägt, um die Möglichkeit der Ueberdeckung
sämmtlicher Düsenöffnungen von einem Punkte aus zu bieten. Das obere Ende der Stange
ist mit Schraubengewinde versehen, welches in einem mit der Haube drehbar
verbundenen Bügel gelagert ist. Durch Drehen des letzteren wird der Vorhalter gegen
den Boden gepreſst. – Die Vorrichtung dürfte wohl wenig praktischen Werth besitzen;
denn für den Ersatz einer Düse muſs Mantel und Futter der Haube durchbrochen werden,
um den Vorhalter g auf den Boden herablassen zu können.
Nach geschehener Ausbesserung muſs die Oeffnung sorgfältig wieder geschlossen
werden, damit beim späteren Kippen kein Eisen durch die etwa vorhandenen Fugen
durchtreten kann. Die Benutzung des Apparates bei einem Düsenersatz während des
Betriebes, d.h. bei gekippter und gefüllter Birne, ist unmöglich.
Um das Steigen des Bessemereisens in den
Formen zu verhüten, hat man schon die verschiedensten Wege eingeschlagen.
Neben der zu diesem
Zwecke versuchten Einführung von chemischen Reagentien in den Stahl (vgl. Tchernoff 1881 239 136) dämmte man auch die sich in den
Formen entwickelnden Gase durch über der Metalloberfläche erzeugten Druck zurück.
Eine diesen Zweck erfüllende Einrichtung wurde an C. W.
Siemens in London (* D. R. P. Kl. 31 Nr. 12037 vom 29. Juni 1881)
patentirt. Dieselbe gestattet die Erzeugung des benöthigten Druckes durch
Einspritzen von Wasser in die hermetisch geschlossene Form auf die flüssige
Metalloberfläche. Um den in Fig. 13
Taf. 33 skizzirten Apparat zu benutzen, ist es vor allem nöthig, Form und Untersatz
durch starke Bolzen und Splinte mit einander zu verbinden. Der Deckel a, welcher in bekannter Weise durch den Keil b auf der Form befestigt wird, besitzt an der unteren
Seite einen vorspringenden, mit Wasserkühlung versehenen Rand, welcher in den
flüssigen Stahl eintaucht. Innerhalb dieses Randes liegt das Sicherheitsventil c, welches unter Zusammendrückung der Feder durch den
Gewichtshebel geschlossen gehalten wird. Das nach vollendetem Guſs und Befestigung
des Deckels durch die Ventilöffnung innerhalb des vorspringenden Randes
eingespritzte Wasser verdampft und drückt den flüssigen Stahl in den Raum d, wo derselbe bald erstarrt und einen dichten
Verschluſs zwischen Form und Deckel bildet.
Das Wasser kann man auch durch Ammoniumcarbonat oder ein Gemenge von salpetersaurem
Alkali mit Holzkohle ersetzen. Andere in der Glühhitze groſse Mengen Dämpfe
entwickelnde Körper, welche schmelzbar sind, kann man in den Boden des Deckels
gieſsen, um letztere in Vorrath erzeugen und je nach Bedarf ohne weitere
Vorbereitung benutzen zu können. Bei e ist ein Stück
Holz angedeutet, welches mit einer mit Pech gefüllten Höhlung behufs Erzeugung des
Druckes versehen ist.
Diese Deckelconstruction scheint eine vollkommene Dichtung zwischen Deckel und Form
zu bewirken und dürfte, ohne Hebelventil, für die Verwendung in Bessemer- und
Siemens-Martin-Werken sehr geeignet sein. Das Sicherheitsventil könnte fortfallen,
wenn man eine durch Versuche zu bestimmende Wassermenge einspritzen würde.
H. Tholander in Forsbacka, Schweden (* D. R. P. Nr.
16479 vom 30. Juni 1881) schlägt den entgegengesetzten Weg ein, indem er über dem
Metall in der Birne nach Beendigung des Processes oder in der Gieſspfanne ein
theilweises Vacuum mittels eines durch gepreſste Luft oder Dampf betriebenen
Ejectors erzeugt. Bei Benutzung der Gieſspfanne zu diesem Zwecke wird dieselbe mit
einer seitlichen Oeffnung (vgl. Fig. 14 und
15 Taf. 33) an den Birnenmund angeschlossen (vgl. 1881 240 * 304) mit
einer im Grundriſs eiförmigen Haube d, welche auf der
Flansche a aufsitzt, bedeckt, verschmiert und die Luft
durch das bei e angebrachte Gebläse durch die Oeffnung
g in der Haube aus der Birne und Gieſspfanne entfernt.
Das Gebläse besteht aus einer in a verschiebbaren Röhre
e, welche durch einen Querarm k mit der Ventilstange f
verbunden ist. In e bewegt sich die Regulirspindel m, während die gepreſste Luft oder der Dampf bei h in das Gebläse eintritt. Zur Vergröſserung der
Luftverdünnung kann man auf g ein sich allmählich
erweiterndes Rohr oder um g noch eine ringförmige,
durch Dampf oder Luft gespeiste Düse aufsetzen. Das Gebläse kann man, bei Verwendung
von Gieſspfannen gewöhnlicher Construction, auch direct auf den Birnenmund
befestigen. – Diesem Verfahren wäre ein praktischer Werth nicht abzusprechen, wenn
wirklich ein wenn auch nur theilweises Vacuum in der Birne erzeugt wurde; dies
wirklich zu erreichen, dürfte jedoch auf groſse Schwierigkeiten stoſsen, da die
Fugen bei der groſsen Hitze und der Kürze der Zeit unmöglich dicht zu halten
sind.
Der Umschmelzcupolofen von Heinr. Krigar in Hannover (* D. R. P. Er. 15919 vom 12.
April 1881) unterscheidet sich von den bekannten Krigar'schen Cupolöfen mit
besonderem Sammelraum dadurch, daſs er zwei Schächte
zur Aufnahme getrennter Beschickungssäulen besitzt. Der
obere luftdicht zu verschlieſsende Schacht a (Fig.
16 Taf. 33) nimmt das Brennmaterial, der offene Schacht b das Roheisen auf. Von dem Windkasten d aus wird durch die Düse c Wind in das Brennmaterial geblasen. Die brennenden Gase durchstreichen
die Roheisensäule und treten am oberen Ende von b aus
dem Ofen aus. Das niederschmelzende Eisen sammelt sich in dem Vorherd mit bekannter
Einrichtung und kann bei o abgestochen werden.
Natürlich kann der Ofen auch zum Umschmelzen von anderen Materialien dienen.
Um Tiegelguſsstahl schneller und
gleichmäſsiger herzustellen und an Tiegelmaterial zu sparen, bringt Th. Hampton in Sheffield (D. R. P. Nr. 16366 vom 19.
Juni 1881) die Materialien in flüssigem Zustande in die glühenden Tiegel und reinigt
oder kohlt sie in diesen je nach Bedarf. Nach dem in der Patentschrift angegebenen
Verfahren werden die besten schwedischen Roheisensorten in einem Cupol- oder
Flammofen niedergeschmolzen und dann in einer Bessemerbirne entsilicirt und
entkohlt. Sodann kellt man das Metall in die vorher erhitzten Tiegel, welche die
nöthigen Materialien zum Rückkohlen, zur Reinigung oder zur Legirung mit anderen
Metallen enthalten, und setzt dieselben so lange in die Tiegelöfen, bis die nöthige
Homogenität des Metallgemisches erreicht ist. Dieses Verfahren mag auf den ersten
Blick viel für sich haben. In der Praxis aber dürfte das Auskellen des Eisens aus
der Birne oder Gieſspfanne in die vorher erhitzten Tiegel, das Luttiren und die
Weiterschaffung dieser in die Tiegelöfen doch nicht so einfach sein, daſs dadurch
wesentliche Vortheile dem alten Verfahren gegenüber erreicht würden.
Das Patent Nr. 15638 vom 23. October 1881 von J. v. Ehrenwerth in Leoben und J. Prochaska in Graz betrifft ein Verfahren zur Herstellung von Ziegeln aus Erz, Kohle und Roheisen und Verwendung dieser
Ziegel bei der Fluſseisendarstellung. Hiernach wird Erz und Kohle, letztere als
Holz-, mineralische Kohle oder Kokes in Erbsen- bis Nuſsgröſse, in offene oder
geschlossene Formen gebracht und werden dann die Zwischenräume mit grauem, halbirtem
oder weiſsem Roheisen ausgegossen. Bei dem Zusatz der so hergestellten Ziegel zu dem
im Flammofen befindlichen geschmolzenen Roheisenbad, oder umgekehrt beim Zusatz des
flüssigen oder festen Roheisens zu den Ziegeln wirkt der Sauerstoff des Erzes
oxydirend auf den Kohlenstoff des Roheisens, entkohlt dieses, während aus dem Erz
reines Eisen entsteht; andererseits soll die eingemengte Kohle die Verwendung einer
verhältniſs-mäſsig groſsen Menge von Erz zur Gewinnung des darin enthaltenen Eisens
auf directem Wege gestatten. – Der Proceſs beruht im Wesentlichen auf demselben
Principe wie das Füttern beim Hochofen und bietet nur in der Herstellung der Ziegel
als Zusatz bei der Fluſseisendarstellung etwas Neues.
J. Haldemann in London (D. R. P. Nr. 16399 vom 20.
November 1880) lieſs sich ein besonderes Verfahren zur Herstellung von Eisenplatten mit innerem Stahlkern patentiren, wonach der
Stahl in ganzen Platten oder Bruchstücken in einen Kasten von Puddeleisen
eingeschlossen wird, so daſs möglichst wenig Luft zu demselben treten kann; das so
hergerichtete Paket wird mit Draht oder Bandeisen gebunden. Der Kasten besteht aus
einer Boden- und einer Deckplatte und je 2 Seitenwänden, welche aus einer im rechten
Winkel umgebogenen Puddeleisenschiene gebildet sind. Bei Herstellung von Platten
legt Haldemann besonderen Werth darauf, daſs die Boden-
und Deckplatte etwa 13mm über die Seitenwandungen
des Kastens vorstehen. Das Neue des Verfahrens besteht nun darin, daſs das so
hergestellte Paket in einem Schweiſsofen äuſserst langsam erhitzt wird, bis der
Stahlkern theilweise oder ganz geschmolzen ist. Sodann wird scharf gefeuert, bis die
Eisenhülle schweifswarm ist und das Paket in diesem Zustande unter die Walzen oder
den Hammer gebracht. Während der langsamen Erwärmung findet an den Berührungsstellen
des Stahles und des Eisens eine Wanderung des Kohlenstoffes statt, so daſs das Eisen
gekohlt, der Stahl aber entkohlt wird. Sind die Materialien mit einer Oxydschicht
bedeckt, so wird diese unter Entwicklung von Kohlenoxyd zu Eisen reducirt. Die
nachherige Bearbeitung des Paketes unter Walzen oder Hämmern bringt die einzelnen
Stahl- und Eisenmolecüle, deren Kohlenstoffgehalt von auſsen nach innen zunimmt, in
Berührung und bewirkt eine Schweiſsung des teigigen Eisens mit dem flüssigen
Stahl.
Zum Schweiſsen von Stahl benutzt
C. Freytag in Magdeburg (D. R. P. Nr. 15692 vom 2.
Februar 1881) Bariumoxyd. Gründe für die Benutzung dieses Pulvers, welches erst im
Knallgasgebläse schmilzt, sind in der Patentschrift nicht angegeben.
Um einen ununterbrochenen und ökonomischen Betrieb von
Eisen-Temperöfen zu ermöglichen, ordnet man dieselben nach dem Patente der Fischer'schen Weicheisen- und
Stahlgieſserei-Gesellschaft in Traisen, Niederösterreich (* D. R. P. Kl. 31
Nr. 14885 vom 5. October 1880) in zwei einander gegenüber stehenden Reihen an und
legt zwischen sie ein Geleise, auf welchem ein fahrbarer Generator ein Befeuern
sämmtlicher Oefen gestattet. Der Generator A (Fig.
17 und 18 Taf. 33)
trägt auf seinem Gewölbe ein Rohr B, welches mit dem zu
befeuernden Ofen bei c durch einen Sandverschluſs
verbunden wird. Die Gase treten von hier in den Kanal d, setzen bei e ihren Theergehalt ab und
gelangen, indem sie das Ventil f und den Kanal g durchziehen, durch die Schlitze h in den Ofenraum k. Hier
treffen sie mit erhitzter Luft zusammen, welche die zu kühlenden Oefen auf dem Wege
l, m, n, o, k durchstreicht, und gelangen endlich
durch die Kanäle u und s
in die Esse. Die Schieber p und r aus Chamotte sind auf den oben ebenen Gewölben der Kanäle o und u aufgeschliffen und
mit Schlitzen versehen, um so ein Oeffnen und Schlieſsen der Kanäle zu gestatten.
Die Oefen k besitzen abnehmbare Ofengewölbe, welche
mittels eines über sämmtliche Oefen auf Schienen laufenden Krahnes behufs
Beschickung der Oefen von oben abgehoben oder ausgewechselt werden können.
St.
Tafeln
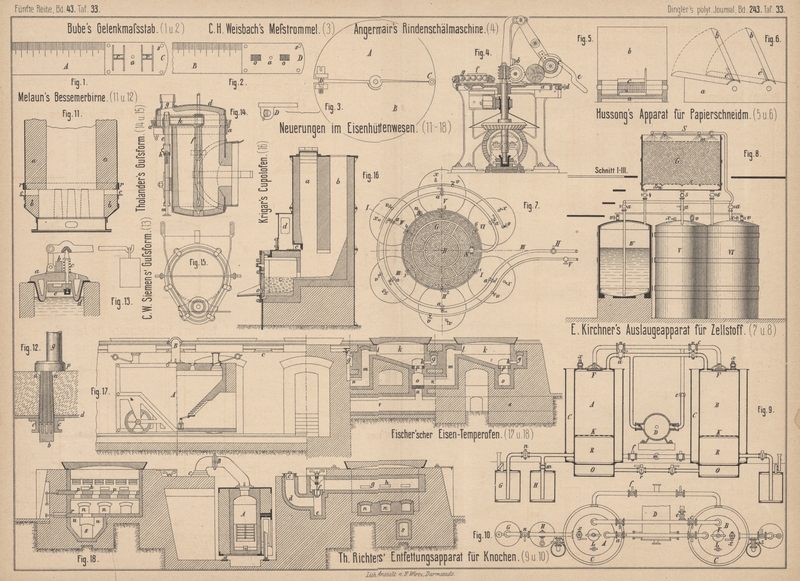