Titel: | Ueber Herstellung von Kerzen. |
Fundstelle: | Band 244, Jahrgang 1882, S. 142 |
Download: | XML |
Ueber Herstellung von Kerzen.
Patentklasse 23. Mit Abbildungen auf Tafel 12.
Ueber Herstellung von Kerzen.
Zur Herstellung von hartem und
geruchlosem Paraffin aus Paraffinmasse, Paraffinschuppen oder aus weichem
Paraffin werden diese Stoffe nach H. Ujhely in Wien
(Oesterreichisches Patent vom 9. Juli 1880) in Methyl-, Aethyl-, Propyl-, Buthyl-
und Amylalkohol, in den diesen entsprechenden Aldehyden und Ketonen, in Phenol oder
aber in Gemischen derselben mit leichten Kohlenwasserstoffen heiſs gelöst. Das aus
dieser Lösung herauskrystallisirte Paraffin wird durch Erwärmen von den letzten
Resten des Lösungsmittels befreit, dann mit Thierkohle oder den Rückständen der
Blutlaugensalz-Fabrikation entfärbt.
Die Société Petits Frères zu St.
Denis (Oesterreichisches Patent vom 17. December 1879) construirte einen Apparat zum raschen Erstarrenmachen von flüssigen
Fetten. Beim Pressen der festen Fettsäuren reiſst das abflieſsende Oleïn je
nach der Temperatur gröſsere oder geringere Mengen von Margarin und anderen festen
Stoffen mit sich. Um diese wieder zu gewinnen, dient eine ringförmige hohle Trommel
A (Fig. 4 Taf.
12), deren Seitenwände aus Kupfer durch zwei Blechreifen b und c so zusammengehalten werden, daſs
zwischen beiden Reifen ein ringförmiger Raum bleibt, welcher von kaltem Wasser
durchflössen wird. Diese Trommel wird mittels Scheiben P und Zahnräder langsam gedreht. Das Kühlwasser tritt bei o in die hohle Welle M,
flieſst durch Rohr f in den ringförmigen Raum, durch
g wieder zur Welle M
zurück und durch e zwischen die doppelten Wände des
Gefäſses B. Das aus den kalten Pressen kommende, im
Behälter R befindliche Fett flieſst auf eine durch
Gestell z getragene schräge Rinne, welche mittels eines
Kautschukbandes an die Trommel anschlieſst; etwa daneben flieſsende Tropfen fallen
in das Gefäſs C. Das so auf die äuſsere Trommelfläche
flieſsende Fett erstarrt sofort und wird durch ein federndes Schabmesser m abgekratzt, so daſs es in das Kühlgefäſs B fällt.
Der Kühlapparat für die zur Fabrikation
von Stearin angewendeten Fette von J. Meſsener in
Metz (* D. R. P. Nr. 16 029 vom 12.
April 1881) besteht aus einem halbrunden, 1m,5 langen Behälter von verzinktem Eisenblech, welcher an beiden Enden
durch zwei guſseiserne Deckel D (Fig. 5 bis
8 Taf. 12) geschlossen ist, an welchen die Pumpen sowie der
Bewegungsmechanismus der Zuführungsschnecken angebracht sind. Der kleine Raum A des Behälters dient zur Aufnahme der zu kühlenden,
durch Rohr p zuflieſsenden Fettmassen, während sich in
dem gröſseren Raum B zwei geschlossene Cylinder C befinden, welche stets von Eis oder kaltem Wasser
umgeben sind. In jedem dieser beiden fest in dem Apparat lagernden Cylinder dreht
sich ein hohler Blechcylinder von 20mm kleinerem
Durchmesser wie der Umhüllungscylinder mit am Umfang angebrachten schneckenförmigen
Gängen. Durch diese Schraubengänge werden die im Raum A
befindlichen Fettmassen durch den Kühlraum B nach den
Pumpen übergeführt. Zur schnelleren Abkühlung der Fette wird dem Inneren jeder
Schnecke durch das Rohr e von auſsen kaltes Wasser
zugeleitet, welches durch kleine Locher am Umfang des am Ende geschlossenen Rohres
in die rotirenden Cylinder tritt, und durch ein zweites Rohr f aus den beiden Schneckencylindern in den Raum B zur weiteren Abkühlung der beiden festen Umhüllungscylinder
geschafft.
Um ferner die abgekühlten Fettmassen von den Schnecken abzustreifen und den Pumpen
zuzuführen, ist auf jeder der beiden Schnecken je ein hochkantig stehender,
stählerner Abstreifer n angebracht, welcher mit den
Schraubengängen der Schnecke entsprechenden Einschnitten versehen ist. Es werden
diese Abstreifer bei jeder Umdrehung der Schnecke um einen Zahn vorgeschoben und
gleichzeitig nach jeder Umdrehung durch zwei am Umfang der Schnecke befindliche
Knaggen um die Höhe des Schraubenganges gehoben und durch die Wirkung der am Ende
des Abstreifers angebrachten Feder i in die frühere
Lage wieder zurückgebracht. Durch je zwei kleine Spiralfedern a werden die Abstreifer fest auf den Umfang der
Schnecke gedrückt und auch gleichzeitig beim Zurückschnellen der Abstreifer das
richtige Wiedereingreifen derselben in die Schneckengänge gesichert. Die abgekühlten
Massen werden durch die beiden nicht saugenden Pumpenkolben o erfaſst und durch das Rohr x zu den
gewöhnlichen Filtrirapparaten, wie sie bei der weiteren Fabrikation von Stearin
angewendet werden, übergeführt. Sind die Filtrirapparate gefüllt, so wird der
Zuführungshahn zum Filter geschlossen und die Fettmassen durch das am Windkessel w befindliche Ventil y
abermals dem Raum A des Kühlapparates zugeführt, um bis
zur etwaigen Einschaltung eines zweiten Filters nochmals gekühlt zu werden.
Die Drehgeschwindigkeit der Schnecken muſs je nach der Temperatur des zugeführten
Fettes und der zu erzielenden Abkühlung desselben geregelt werden und kann auch nach
Belieben die eine oder andere Schnecke und Pumpe je nach Bedarf unabhängig vom
Filtrirapparat in Ruhestand versetzt werden.
Die Maschine zur Herstellung von
Kerzen von A. Royau in Mans, Sarthe, Frankreich (* D. R. P. Nr. 14 452 vom 2.
November 1880) hat ein Gestell aus zwei guſseisernen, oben durch den
Gieſstisch verbundenen Seitentheilen A (Fig. 1 bis
3 Taf. 12). Die oben an den Wänden angebrachten Säulen b führen eine Art von beweglichen Rahmen, welcher aus
zwei auf den Säulen gleitenden Platten c und einem aus
zwei Theilen bestehenden, beide Platten unter sich verbindenden Querstück a
besteht. An diese sind
die oberen Enden von Zahnstangen d befestigt, welche
durch die Kurbel e hoch und niedrig gestellt werden.
Das Getriebe, an welchem die Kurbel sitzt, greift in das Zahnrad und dieses in die
Zähne der Stange, während ein Sperrhaken f in die Zähne
des Sperrrades fällt, welches fest am Getriebe und auf derselben Achse sitzt; die
Rücken der Zahnstangen werden durch Reibungsrollen w
gestützt.
Der Gieſstisch ist in 24 Theile getheilt, von denen jeder einen kleinen Tisch t bildet; für jeden dieser Tische ist eine Reihe von 5
Lichtformen bestimmt. Jede der Formen besteht aus einem Formenträger m aus Kupfer, in deren Mitte die Zinnform befestigt
ist. In den leeren Raum, welcher die Form umgibt, kann man nach Belieben kaltes oder
heiſses Wasser zulassen, indem man oben und unten an jeder Formenreihe Rohre g und h anbringt und von
diesen Röhren nach jedem Formenträger Zweigrohre g1 und h1 ableitet. Scheidewände z, welche oben in den Formenträgern angebracht sind, verhindern das
Wasser, weiter vorzudringen. Die 24 Rohre g sind von
der Hauptleitung k abgezweigt und stehen mittels dieser
durch 8 Rohre mit einer oberen Mulde l in Verbindung.
Der Wasserzufluſs aus der Mulde l in die Rohre g wird durch das Rohr i in
der Leitung k so geregelt, daſs die zu diesem Zweck in
dem Rohre i angebrachten Lichte Ventile für die
Zweigrohre bilden. Ein einziger Hebel j gestattet mit
einem Hube den Zulaſs des Wassers oder den Verschluſs für sämmtliche 24
Formenreihen. Unterhalb (den Röhren g1 entgegengesetzt) befinden sich die Rohre h1, welche die
Formenträger m mit den Rohren h verbinden. Diese Rohre h sind Abzweigungen
der Leitung n, in welche unter Druck durch das Rohr n1 das zum Erkalten der
Formen bestimmte Wasser flieſst.
Die Formenträger sind umgeben vom Gieſstisch und den Brettern p, welche an den Seitenflächen des Gestelles befestigt sind; das vordere
derselben hat die Rinne y, in welche der Talg und die
Abfälle des Gieſstisches fallen. Der Docht der Spulen r
geht beim Abwickeln durch die oberhalb in q
angebrachten Löcher. Nachdem die Dochte r die Formen
durchzogen haben, werden sie in Reihen zu je 5 an Tragstücken s befestigt. Dies geschieht durch eine Art von Kneifern
oder Zangen v, welche mittels ihrer Seitenbacken die
Dochte halten und die Enden an die Seite der Tragstücke legen. Die Dochte sind, ob
rund oder oval im Durchschnitt, geflochten und halb aus amerikanischer roher, halb
aus gebleichter Baumwolle mit einigen Flachsfäden hergestellt.
Angenommen, der Rahmen c ist herabgestiegen und befindet
sich etwas über dem Gieſstisch; die 120 Dochte sind, nachdem sie über die Formen
hinweggeschritten, an den Tragstücken befestigt. Mit der nöthigen Vorsicht geschieht
nun das Gieſsen des Stearins, Talges u.s.w. Nachdem alle Formen gefüllt sind, wird die Leitung n1, geöffnet und sofort
kreist das kalte Wasser um sämmtliche Formen. Nachdem die Abkühlung für genügend
erachtet, wird das Wasser durch den Hahn x abgelassen.
Gleich darauf öffnet man mittels des Hebels j die
Warmwasserleitung des Behälters l und das Wasser stürzt
in die Zwischenräume. Die metallene Form dehnt sich, die Kerze löst sich von der
Form und man hebt 120 Kerzen, indem man die Kurbel e in
Bewegung setzt. Die Behälter werden frei, die Formen gereinigt und ein neuer Guſs
kann beginnen.
Bei der Herstellung von Kerzen will
F. M.
Joly in Paris (* D. R. P. Nr. 15771 vom 25. Januar 1881) in Verbindung mit Kerzendochten
b (Fig. 9 Taf.
12), welche so geflochten sind, daſs sie bei der Verbrennung sich nach auſsen
krümmen, um der atmosphärischen Luft freien Zutritt zu gestatten, besondere
Dochtseelen b1
anwenden, welche aus an einander gelegten Fäden bestehen, um dadurch eine möglichst
gleichmäſsige Einführung der geschmolzenen Kerzenmasse in die Flamme zu
erzielen.
Die Maschine zur mechanischen Bearbeitung
der Kerzen von E. Rost in
Dresden (* D. R. P. Nr. 15 782 vom
28. December 1880) besteht im Wesentlichen aus einer am Umfange mit
Riefen oder Nuthen versehenen Zuführwalze A (Fig.
10 bis 13 Taf. 12)
und einer mit Kreissägeblättern besetzten Walze B,
welche hier zugleich Antriebwelle und deshalb mit Fest- und Losscheibe versehen ist.
Bei dieser Kerzentheilmaschine befinden sich an den
Enden der Sägenwelle B Fräsköpfe e, welche zur Aufnahme von passend gestalteten, 1- oder
2flügeligen Fräsmessern f bestimmt sind. Die zu
fräsenden Lichte werden mit einer Zange, von welcher beispielsweise Fig. 13
eine passende Gestalt des Maules veranschaulicht und die man auf die Unterlagen g auflegt, centrisch gegen die Fräser gehalten. Die
gegossenen langen Lichte werden auf die geneigte Platte C aufgelegt, einzeln von der langsam rotirenden Zuführwalze A in die achsialen Riefen aufgenommen und durch das
Schnittbereich der Sägen geführt. An der der Zuführung gegenüber liegenden Seite der
Walze wird dieselbe von Gurten oder anderen geeigneten, mit Spannvorrichtung i versehenen Bändern h
umgeben und so das Herausfallen der Lichte aus den Riefen so lange als nöthig
verhindert. Die zerschnittenen Kerzen fallen unterhalb der Walze nieder auf ein Sieb
D, rollen, indem sich die etwa anhaftenden Späne
ablösen und in den Spankasten F durchfallen, auf dem
Sieb abwärts und sammeln sich in den Behältern H und
J. Der Raum über dem Sieb D ist durch zwei Scheidewände in drei Abtheilungen n, m und o geschieden, wie auch der
Uebergangsraum E durch die Scheidewände a und z. Es entstehen
nämlich durch das Zertheilen drei verschiedene Arten von Kerzenstücken: bei I fertige kleine Kerzen, weiche in der Abtheilung m gereinigt werden und auf a in den Behälter G niederrollen; bei II brauchbare Kerzenstücke, sogen. Schnittkerzen, ohne
Spitzen, welche in m und zwischen a und z niedergehen und
sich in H sammeln, und endlich bei III unbrauchbare Abschnitte, welche man in J findet, von wo aus sie dem Schmelzkessel wieder
zugeführt werden. Die Hauptmasse der Späne fällt auf die Platte c nieder und wird nach Erforderniſs mit den durch das
Sieb gegangenen Spänen bei b entfernt. Unterhalb E ist ein Polster d mit
weichem Stoff belegt, damit die Kerzen beim Niederfallen nicht beschädigt, wohl aber
noch besser von Spänen gereinigt werden. Abstreicher k
greifen in die Nuthen der Zuführwalze ein, schieben die geschnittenen Kerzenstücke
aus der Walze und halten die Nuthen rein. Die Kerzenstücke aus dem Behälter H werden nun einer Drehbank oder einer
Kerzenfräsmaschine zugeführt, woselbst das Anspitzen erfolgt.
Die in Fig. 14 bis 18 Taf. 12
dargestellte selbstthätige Kerzenfräsmaschine macht
während einer Fräsperiode gleichzeitig 6 Kerzen fertig und führt zu diesem Zweck 6
verschiedene Bewegungen aus, welche sämmtlich von der mit Fest- und Losscheibe
versehenen Antriebwelle A abgeleitet sind.
Durch das Stirnrad a oder auch durch Schnurbetrieb o.
dgl. erhalten die Frässpindeln C ihre drehende
Bewegung. Der Kurbel- oder Excentermechanismus b
veranlaſst eine Schüttelbewegung des Siebrahmens D,
welcher sich unter der Tischplatte befindet und der zur Trennung der Frässpäne und
der fertigen Kerzen in die Schubkasten E bezieh. E1 bestimmt ist.
Die verschiedenen schwingenden Bewegungen werden durch Curvenscheiben auf der
Zwischenwelle B hervorgerufen, welche im vorliegenden
Falle mittels Schneckentrieb c mit der Welle A in Verbindung steht. Von der Curvenscheibe d aus erfolgt die Bewegung des Vertheilers F, eines mit Fächern versehenen Kastens, in welchen die
zu fräsenden Kerzen zuerst gebracht werden und welcher dieselben in die Fräskanäle
h zu vertheilen hat. Die Curvenscheibe e wirkt auf die Klemmer G,
welche von einer durchgehenden Schiene i zur Seite
geschoben werden und während dessen die vorher von ihnen in den Fräskanälen
festgehaltenen Kerzen um eine Kerzenstärke weiter niedergleiten lassen. f ertheilt den mit der Schiene k verbundenen Schiebern H zu geeigneter Zeit
eine Seitenbewegung, wodurch der Fräskanal nach unten frei wird, so daſs das in der
vorhergehenden Periode gefräste Licht auf das Schüttelsieb D und in den Kasten E1 niederfallen kann. Durch Vermittelung der
Druckstange l und der Winkelhebel m wird von der Curvenscheibe g aus der die Lager der Frässpindeln C
tragende Schlitten J gegen die von den Klemmern in den
Fräskanälen festgehaltenen Kerzen vorgeschoben und dabei durch Umdrehen der
Frässpindeln das Fräsen selbst ausgeführt. Die ersteren Bewegungen sind durch Anordnung
von Spiralfedern, die Schlittenbewegung der Fräser aber ist durch Anbringung eines
Gegengewichtes zwangläufig gemacht.
Die Bewegungen zur Erzielung der Drehung der Fräser K
und der Schüttelung des Siebrahmens D sind
rücksichtlich ihrer Geschwindigkeit im Allgemeinen unabhängig von einander, sowie
auch von den Fräsperioden und von den übrigen Bewegungen bemessen; die schwingenden
Bewegungen aber erfolgen innerhalb jeder Fräsperiode regelmäſsig und die einzelnen
Phasen derselben müssen, wenn der ganze Apparat richtig arbeiten soll, in ganz
bestimmten Zeiträumen stattfinden.
Die zu fräsenden Kerzenstücke werden in den Vertheiler eingelegt und bewegen sich
einzeln in den Fräskanälen nieder. Die Fräser K drehen
sich unausgesetzt mit den Spindeln C um ihre Achse und
auch das Schüttelsieb D ist fortwährend in Bewegung.
Während die Fräser die denselben achsial gegenüber stehenden, von den Klemmern G gehaltenen Lichte L
bearbeiten, sind die Schieber H geöffnet und lassen die
in der vorhergehenden Periode fertig gemachten Kerzen L, durch die Tischplatte M hindurch auf den
Schüttelrahmen D fallen. Dort werden sie von den
anhaftenden Spänen gereinigt und sammeln sich in dem Kasten E1
; die Späne fallen in den Kasten E. Wenn dann der Fräserschlitten J zurückgegangen ist, lassen die Klemmer die vorher
festgehaltenen Kerzen los und um eine Kerzenstärke nach unten fortrücken. Dabei
halten die Schieber H die Fräskanäle unten geschlossen
und der Vertheiler führt von oben her andere Kerzenstücke in dieselben ein.
Auf der gemeinschaftlichen Platte N bewegt sich der
Fräserschlitten hin und her; sie trägt den Kerzenführungsapparat, die Lager für die
Antrieb- und die Zwischenwelle, sowie für die Winkelhebelbolzen. Die mit einem
normal breiten und einem etwas breiteren Zahnrade versehene Vorgelegewelle O überträgt die drehende Bewegung der Antriebwelle,
auch während der Verschiebung des Fräserschlittens, auf die nächstgelegene
Fräserspindel und diese theilen sie sich unter einander durch directe Uebertragung
mit. Ueber die Rolle P ist die Schnur für das
Gegengewicht gelegt, welches den Fräserschlitten zurückzieht.
Nach G. Hartl (Wochenschrift des niederösterreichischen
Gewerbevereines, 1881 S. 484) sind bei der Stearinkerzenfabrikation keine anderen Fortschritte gemacht worden, als
daſs die schwefelsaure Verseifung, ohne zu destilliren, mit gutem Erfolge im Groſsen
ausgeübt wird. Die Stearinkerzen sind nicht besser, aber sie sind härter geworden,
wodurch beim Anzünden der Uebelstand eintritt, daſs, wenn man dieselben nicht mit
Vorsicht anzündet, die Kerzen durch das Ablaufen der Stearinsäure verunstaltet
werden, wodurch das Licht von den sie umgebenden Zacken und Spitzen beeinträchtigt
wird. Da durch die Einführung der künstlichen Butter- und Oleo-Margarin-Fabrikation dem Unschlitt die
leichter schmelzbaren Theile entzogen werden und die festen Rückstände, nämlich das
Stearin, zur Kerzenfabrikation verwendet wird, so hat sich der Schmelzpunkt der
reinen Stearinsäure erhöht, wodurch es unvermeidlich ist, daſs die Kerzen beim
Anzünden ablaufen, indem ein Theil des Dochtes verbrennt und die dadurch entstehende
kleine Flamme die geschmolzene Stearinsäure nicht aufsaugen kann; es ist daher
nothwendig, daſs man die Stearinkerze beim Anzünden in eine horizontale Lage bringt
und einige Male umwendet, bis die Stearinsäure der Kerze etwas geschmolzen ist,
wodurch dieser Uebelstand vollkommen vermieden wird.
Manche Stearinkerzenfabrikanten helfen diesem Uebelstande dadurch ab, daſs sie der
Stearinsäure Paraffin zusetzen, wodurch die Kerzenmasse leicht schmilzt, jedoch,
wenn an einem Orte mehrere Kerzen brennen, ein unangenehmer Geruch entsteht, welcher
besonders beim Auslöschen der Kerzen sehr lästig ist. Die Apollokerzenfabrik
verwendet einen groſsen Theil des bei der Margarinfabrikation erhaltenen Stearins
(Preſstalg) zu Phöbuskerzen und Secunda-Apollokerzen; die Phöbuskerzen sind ein
Gemenge von Stearinsäure und Paraffin, die Secunda-Apollokerzen sind aus
Stearinsäure und Fettsäure hergestellt.
Die holländischen und belgischen Fabriken verwenden sehr billiges Palmöl, erzeugen
mittels Destillation Palmitinsäure und bringen ihre schlechten Kerzen mit genau
nachgeahmten Etiquetten als Apollokerzen in den Handel. Da die holländischen und
belgischen Fabriken für ihre Rohstoffe sowie für das fertige Product nur sehr
geringe Frachten zu bezahlen haben, so ist die Concurrenz mit diesen Fabriken
unmöglich und es wird der Absatz der österreichischen Fabriken nach den
Donaufürstenthümern und der Türkei mit jedem Jahre geringer.
Die schwefelsaure Verseifung wurde kurze Zeit nach der Erfindung der Stearinsäure von
dem französischen Chemiker Frenni entdeckt und bei der
Destillation der Fettsäuren in Anwendung gebracht. Man wendete bis zu 37 Proc.
concentrirte Schwefelsäure an, um das Fett in Fettsäure zu verwandeln; groſse Mengen
Fettsäure wurden zerstört und in Theer verwandelt, die Ausbeute an Fettsäure war von
100 Th. Talg 83 bis 84 Th. und von Palmöl 80 bis 81 Th. Die schwefelsaure Verseifung
in Verbindung mit der Destillation ist in den meisten Ländern in Anwendung; in
England, Holland und Belgien wird destillirt, in Ruſsland und Frankreich ist die
Verseifung mittels Hochdruck in Anwendung; aber es gibt hier auch viele Fabriken,
welche die Destillation eingeführt haben. Das Bestreben aller Fabrikanten ist dahin
gerichtet, die Verluste an Fettsäure, welche durch die Destillation entstehen, zu
vermeiden. Bei der internationalen Ausstellung in Paris 1867 hatte Adolf de Milly Fettsäure und Stearinsäure ausgestellt,
welche durch
schwefelsaure Verseifung ohne Destillation erzeugt wurde. Die Fettsäure war grau,
die Elaïnsäure beinahe schwarz, die Stearinsäure war ebenfalls nicht besonders
schön, daher auch diese Verfahrungsweise Milly's keine
Anwendung fand. Im J. 1870 lieſs sich J. C. A. Bock aus
Kopenhagen (1872 205 560) eine Verfahrungsweise in
Oesterreich patentiren, nach welcher alle Gattungen Fette durch Schwefelsäure in
Fettsäure verwandelt werden, ohne zu destilliren. Bock
lieſs sein Patent zum Kaufe ausbieten, für welches er 300000 M. forderte. Die
vorgelegten Proben von Fettsäure und Stearinsäure waren sehr schön; insbesondere war
die Stearinsäure von ausgezeichneter Schönheit, die Kerzen hatten einen hellen Klang
und fühlten sich wachsartig an. Bock gab an, daſs nach
seiner Verfahrungsweise von 100 Th. Talg 68 bis 70 Th. Stearinsäure und 23 bis 24
Th. Elaïnsäure erhalten werden, während man bei der gewöhnlichen Fabrikation nur 44
bis 45 Th. Stearinsäure und 49 bis 50 Th. Elaïnsäure erhält. Bezügliche Versuche
aber, welche Bock in der Hartl'schen Fabrik ausführte,
miſslangen vollständig. Dagegen gelang es Hartl selbst,
die schwefelsaure Verseifung durchzuführen, aber die Ergebnisse, welche Bock versprochen hatte, waren nicht zu erreichen und
wird es kaum Jemand gelingen, aus 100 Th. Talg 70 Th. schöne weiſse Stearinsäure mit
einem Schmelzpunkt von 60° zu erhalten.
Bei der Seifenfabrikation ist der wesentliche
Fortschritt gemacht worden, daſs man an verschiedenen Orten anfängt, das bei der
Seifenerzeugung sich bildende Glycerin, welches immerwährend unbenutzt mit der
Mutterlauge weggeschüttet wurde, nutzbringend zu verwenden. Schon im verflossenen
Jahre (vgl. 1880 238 95) wurde die Gewinnung von Glycerin
aus Seifenlauge angegeben; es wurden bereits in Oesterreich und Deutschland mehrere
Patente erworben, welche bis jetzt vollkommen werthlos sind (vgl. Flemming 1882 243 330),
indem im J. 1858 von Georg Hartl ein i. J. 1873 wieder
erloschenes Privilegium genommen wurde, wodurch alle Gattungen Fette und Oele in
Fettsäuren und Glycerin zerlegt werden können. – Aus der Seifensiederlauge das darin
enthaltene Glycerin abzuscheiden, wird immerhin sehr groſse Schwierigkeiten
verursachen, indem die fremden Salze, welche in der Lauge enthalten sind, bei der
Reinigung des Glycerins viele Unannehmlichkeiten verursachen werden; es ist daher am
vortheilhaftesten, wenn die Fette und Oele vor Verwendung zur Seifenfabrikation in
Fettsäure und Glycerin umgewandelt werden.
B.
Weinstein in Hamburg (D. R. P. Nr. 17 324 vom 1. September 1881) will Paraffin- und Stearinkerzen mit Abziehbildern verzieren
und dann in dünnflüssiges Paraffin oder Stearin eintauchen, damit dieselben mit
einer dünnen, durchscheinenden Schicht bedeckt
werden.
Tafeln
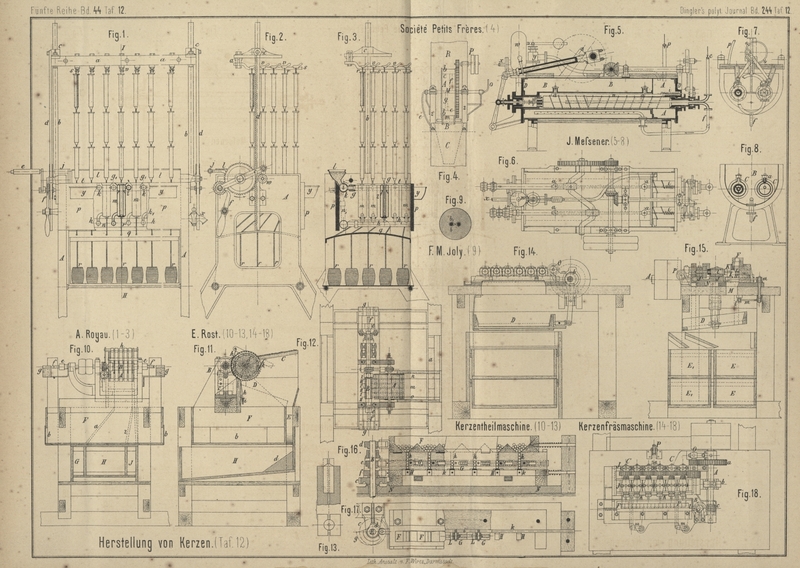