Titel: | Ueber die Herstellung von Glas. |
Fundstelle: | Band 246, Jahrgang 1882, S. 462 |
Download: | XML |
Ueber die Herstellung von Glas.
Patentklasse 32. Mit Abbildungen auf Tafel 35.
Ueber die Herstellung von Glas.
Das Schmelzen von Glas geschieht nach S. Reich
und Comp. in Berlin (* D. R. P. Nr. 17736 vom 11. Juni 1881) am besten mittels Elektricität. Die schmiedeisernen Klemmlager d (Fig. 1 bis
3 Taf. 35) an den beiden Säulen b tragen mit
4 Isolirklötzchen e aus Hartgummi die beiden aus
Guſsstahl hergestellten und galvanisch verplatinirten Elektricitätspole f, in denen die kupfernen Leitungsstangen von der
Dynamomaschine mittels Contactschrauben g befestigt
sind. Die beiden Stücke f sind durch die in die Nuthen
fest eingepaſsten Chamottekeile h von einander isolirt
und tragen das aus Platinblech hergestellte halbkugelförmige, mit feinen Löchern
versehene Sieb i. Der Zwischenraum m zwischen dem guſseisernen Kessel n und dem aus Chamotte oder Graphit hergestelltem
kleinerem Arbeitstiegel l ist mit einem Gemenge von
gleichen Theilen Holzasche und Asbest ausgestampft. Das obere Ringstück c trägt den Fülltrichter o
aus unglasirtern Porzellan, dessen Rohrverlängerung bei r genau auf die Polstücke aufgeschliffen ist.
Der Arbeitstiegel l wird stark vorgewärmt eingelegt, mit
fein gepulvertem, aus dem folgenden Satz hergestelltem Glas etwa halb gefüllt, der
Fülltrichter o aber mit demselben Glaspulver bis zu der
Erweiterung der Röhre. Dann wird der Glassatz aus 100k Sand, 40k Soda, 16k Kalk, 8k
Mennige, 600g Arsen und 280g Braunstein in den Trichter eingetragen und die
Dynamomaschine in Gang gesetzt. Geeignet hierfür dürfte die Siemens'sche Maschine Modell D2 für
gleichgerichtete Ströme sein. Das durch das glühende Platinsieb geschmolzene Glas
sammelt sich im Arbeitstiegel und wird diesem zur Ausarbeitung entnommen; doch muſs
das Platinsieb stets bedeckt gehalten werden.
Durch dieses Verfahren soll ermöglicht sein, ohne gröſsere Schmelzöfen ein
ununterbrochenes Arbeiten der Glasmacher zu erzielen und dieselben unabhängig von
den bis jetzt gebräuchlichen Schmelzöfen, in denen gröſsere Massen Glas geschmolzen
werden muſsten, zu erhalten. Für jeden Glasartikel entsteht so eine selbstständige
Schmelz- und Arbeitsvorrichtung, mit welcher der Glasmacher sich sein Glasgemenge
selbst schmilzt und ausarbeitet.
Einige Anhaltspunkte zur Beurtheilung dieses Vorschlages geben die Versuche von C. W. Siemens in London.Vgl. C. W. Siemens: Gas and Electricity as heating
agents (London 1881). Neuerdings wird der Strom auch noch um den
Tiegel geführt.F. Der von ihm
verwendete elektrische Schmelzofen (Fig. 4 Taf.
35) besteht aus einem Graphitschmelztiegel a, welcher
in einem mit schlechten Wärmeleitern b gefüllten
Gefäſse steht. Durch den Boden des Schmelztiegels ist ein Kohlenstab c,
durch den Deckel als
negative Elektrode ein Kohlencylinder d eingeführt;
letzterer ist mittels Kupferstreifen an einem in der Mitte unterstützten Balken
aufgehängt, dessen anderes Ende einen Hohlcylinder von weichem Eisen trägt, welcher
sich senkrecht in einer Drahtspule s von etwa 50 Ohm
Widerstand frei bewegen kann. Das Uebergewicht des Balkens kann durch ein
Laufgewicht g so verändert werden, daſs es die
magnetische Kraft, mit welcher der hohle Eisencylinder in die Solenoïdrolle s hineingezogen wird, ausgleicht. Die Kraft, mit
welcher die Rolle auf den Eisencylinder wirkt, ist der elektromotorischen Kraft
zwischen beiden Elektroden, oder in anderen Worten dem Widerstände des zur Rolle s parallel geschalteten elektrischen Bogens selbst
proportional. Ohne die hierdurch bewirkte selbstthätige Regulirung würde der
Widerstand des Bogens auſserordentlich schnell mit der Zunahme der Temperatur der
erhitzten Atmosphäre im Schmelztiegel abnehmen und es würde dann in der
Dynamomaschine zum Nachtheil des elektrischen Schmelzofens Wärme erzeugt werden.
Andererseits würde bei plötzlichem Sinken des unter Schmelzung befindlichen
Materials eine plötzliche Vergröſserung des Widerstandes des Bogens, wahrscheinlich
ein Erlöschen des letzteren verursachen, wenn diese selbstregulirende Wirkung nicht
stattfände. Wichtig ist ferner, daſs die zu schmelzenden Stoffe den positiven Pol
des elektrischen Bogens bilden, da an diesem die Wärme hauptsächlich erzeugt wird
und die Schmelzung der den positiven Pol bildenden Stoffe sogar stattfindet, noch
ehe der Schmelztiegel selbst entsprechend heiſs ist. Bei Behandlung von
nichtleitenden Erden oder von Gasen wird es nothwendig, für einen nicht zerstörbaren
positiven Pol zu sorgen, etwa für einen solchen aus Platin oder Iridium, welcher
indessen selbst der Schmelzung unterworfen sein und einen kleinen Teich am Boden des
Schmelztiegels bilden kann.
Bei Verwendung einer 4e-Dynamomaschine, welche
einen Strom von 36 Weber'schen Einheiten erzeugt und
bei ihrer Benutzung zur Beleuchtung ein Licht von 6000 Kerzen gibt, wird der etwa
20cm tiefe Schmelztiegel in weniger als 15
Minuten auf Weiſsglühhitze gebracht und 1k Stahl
in weiteren 15 Minuten geschmolzen, während nachfolgende Schmelzungen weniger Zeit
erfordern.
Nach den neuesten Versuchen von C. W. Siemens und A. K. Huntington (Chemical News, 1882 B. 46 S. 163)
gelingt es unter Anwendung von 5 Dynamomaschinen (Modell D2), welche durch eine 12e-Maschine
getrieben einen Strom von 250 bis 300 Ampères lieferten, leicht gröſsere Mengen von
Platin, Nickel, Wolfram und anderen Metallen zu schmelzen. 10k Stahlfeilen schmolzen in 1 Stunde, 3k Schmiedeisen in 20 Minuten; 350g Kupfer, unter Kohlenstaub geschmolzen, waren
nach ½ Stunde fast völlig verdampft. Die Menge des zu schmelzenden Stoffes und die
Schmelzdauer sind abhängig von dem Temperaturunterschied zwischen Schmelz- und
Verdampfungspunkt und dem Wärmeleitungsvermögen desselben (vgl. d. Bd. S. 327).
Zum Biegen, Färben und Ausglühen von Glas und zum Brennen
feiner Thonwaaren schlagen D. und W. H.
Thompson in Leeds (* D. R. P. Nr. 19005 vom 27. Oktober 1881) den in Fig.
5 und 6 Taf. 35
skizzirten gewölbten Ofen a mit Gasheizung vor. Durch Oeffnungen in den Seitenwänden desselben sind mit
Hähnen f versehene Bunsen'sche Brenner eingeführt. Die Verbrennungsgase entweichen durch die mit
Klappen c versehenen Kanäle n in den Schornstein m, welcher zur Regelung
des Zuges mit Seitenöffnungen d versehen ist. Die zu
behandelnden Gegenstände werden auf Wagen i gestellt,
welche auf den Schienen j laufen, worauf man die Thür
h dicht schlieſst.
Da in letzter Zeit die Nachfrage nach groſsen Glasscheiben stärker wird, die
Herstellung und Erhaltung groſser gebrannter Strecksteine aber sehr schwierig ist, so empfiehlt Moritz im Sprechsaal, 1882 S. 385 dieselben
aus Guſseisen herzustellen, indem man einen offenen flachen Kasten von 18mm Wandstärke gieſsen läſst, dessen Kehrseite
abgehobelt und mit Sand und Wasser abgeschliffen wird. Der inwendige hohle Raum wird
mit Thonplatte und Mörtel ausgefüllt, und zwar lassen sich hierzu alte zerbrochene
Strecksteine verwenden. Das Strecken auf guſseisernen Platten, welche nicht auf
schlecht leitender Unterlage aufliegen, gelingt nicht. Die genannten Streckplatten
dagegen verziehen sich im Feuer nicht und können, wenn sie vernünftig behandelt
werden, viele Jahre aushalten; man hat nur nöthig, sie von Zeit zu Zeit
herauszunehmen und mit Wasser und Sand abzuschleifen. Die Platten werden auſserdem
durch den Gebrauch mit der Zeit immer besser, da sie durch das Ausglühen weicher und
zum Strecken daher geeigneter werden. Selbst bei nicht ganz glatter Fläche hat eine
auf Guſseisen gestreckte Scheibe einen viel schöneren Glanz als eine auf dem
glattesten Thonstein gestreckte; darauf ist jedoch streng zu sehen, daſs der Stein
vor dem Auflegen des Cylinders sauber abgeputzt wird, weil sonst der kleinste
aufliegende Gegenstand sich in der Scheibe stark kenntlich macht und zwar wegen des
höheren Glanzes dieses Glases viel stärker, als wenn es auf einem Thonstein
gestreckt wird. Vielleicht dürfte es sich empfehlen, die Platte zu vernickeln.
Der Glaskühlofen von Ch. A. W. Schön in
Hamburg (* D. R. P. Nr. 19207 vom 17.
September 1880) bildet, wie aus Fig. 7 und
8 Taf. 35 zu ersehen, im Inneren nur einen Raum, welcher durch Schieber
q in zwei oder mehr Abtheilungen B und D getheilt werden
kann. Die Sohle des Kühlofens bildet eine Drehscheibe A, unter welcher Eisenschienen c so angebracht
sind, daſs an denselben in Doppellagern f ruhende
Rollen e gleiten können; ebenso befindet sich auf der
unteren Seite ein Zahnkranz g, in welchen das an der
Welle i befestigte Stirnrad h eingreift. Diese wird durch die senkrecht stehende Welle n in Bewegung gesetzt, welche schlieſslich durch das
Handrad o gedreht wird. Diese Bewegungsvorrichtung schlieſst sich an den durch die
Kanäle w erwärmten Raum B
an, in welchem die
fertigen, aber noch heiſsen Glaswaaren in auf Rädern stehende Kästen t gepackt werden. Ist ein Kasten gefüllt, so wird die
Scheibe mittels des Rades o gedreht, ein Schieber q hochgezogen und der gefüllte Wagen mit der Scheibe so
weit gedreht, bis er hinter den nächsten Schieber gelangt, welcher dann wieder
herabgelassen wird, worauf man einen neuen Wagen füllt. Auf diese Weise gehen die
Wagen durch den ganzen Ofen, bis sie vor die Oeffnung u
gelangen, wo sie als abgekühlt ausgeladen werden. Die Heizung des Ofens geschieht
mittels Generatorgas, welches durch Kanäle w zugeführt
wird.
Die Beförderung der heiſsen Glaswaaren nach dem Kühlofen geschieht mittels Band oder
Kette ohne Ende d, welches um 2 Scheiben r in der überdeckten Rinne E läuft. Zur Erwärmung der Rinne läſst man durch Kanal m die zur Heizung des Kühlofens bestimmten heiſsen
Generatorgase gehen. Von dem bewegten Bande rollen die heiſsen Glasgegenstände über
ein Blech k auf einen mit Sand bestreuten Tisch l, um in die Kästen oder Wagen gepackt zu werden.
Bei der Herstellung von Tafelglas werden die Strecköfen um den Kühlofen herumgelegt.
Jeder Streckofen ist in den Arbeitsraum G und die
Heizkammer H getheilt. Letztere enthält zwei über
einander liegende Schienengeleise a, von denen das
obere auf Querschienen z befestigt ist. Die auf den
Schienen rollenden Wagen x haben den Zweck, die heiſsen
Glascylinder in der Heizkammer zu halten, bis sie zur Verarbeitung kommen. Soll nun
Tafelglas gestreckt werden, so zieht der Arbeiter den Schieber s hoch und streckt die Cylinder des unteren Wagens,
während welcher Zeit der geladene Wagen im oberen Raum in Hitze bleibt. Ist der
untere Wagen leer, so wird derselbe in die Heizkammer zurückgeschoben, nachdem von
der anderen Seite neue Cylinder aufgegeben sind, und dieselbe Arbeit beginnt mit dem
oberen Wagen. Hat der Arbeiter eine Tafel gestreckt, so schiebt er dieselbe durch
die Oeffnung v in den Kühlofen.
Tafeln
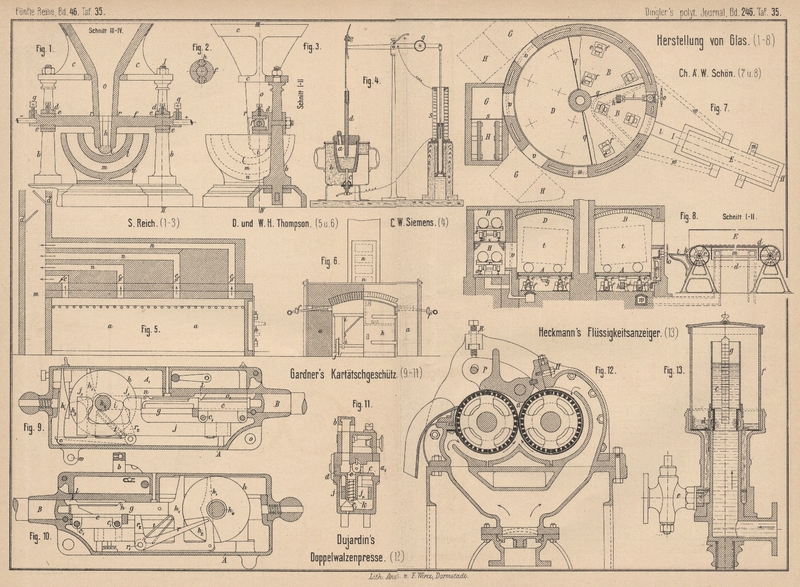