Titel: | Ueber Neuerungen im Eisenhüttenwesen. |
Autor: | St. |
Fundstelle: | Band 248, Jahrgang 1883, S. 498 |
Download: | XML |
Ueber Neuerungen im Eisenhüttenwesen.
(Patentklasse 18. Fortsetzung des Berichtes Bd.
247 S. 327.)
Mit Abbildungen im Texte und auf Tafel 35.
Ueber Neuerungen im Eisenhüttenwesen.
Ch. Cochrane aus Stourbridge machte in einem auf der am
15. August 1882 in Leeds stattgehabten Versammlung der Mechanical Engineers gehaltenen Vortrage auf die groſse Wichtigkeit
aufmerksam, welche die
Stellung der Formen auf das Ausbringen eines
Hochofens hat. Dieselbe kann oft die Ersparniſs, welche sich eigentlich aus
dem groſsen Rauminhalte eines Ofens oder aus einer besonders hohen Windtemperatur
ergeben müſste, aufheben. So ist es vorgekommen, daſs ein Ofen von 580cbm Inhalt durch eine falsche Stellung der Formen
und eine dadurch herbeigeführte Versetzung der Schachtwände auf 340cbm Fassungsraum zusammengeschrumpft war, während
der Verbrauch an Kokes sich von 1,05 auf 1t,25 für
1t Eisen erhöhte. Der diametrale Abstand
zweier Formen betrug anfänglich 1m,83. Nach einer
Auseinanderziehung auf 2m,13 stieg das Ausbringen
von 483t Eisen auf 599t, während der Verbrauch an Kokes in Folge des stärkeren Betriebes auf
603t verblieb. Dieselben Erscheinungen
wiederholten sich an 3 anderen Cleveländer Hochöfen.
Für Oefen von 27m,43 Höhe und 8m,7 Kohlensackdurchmesser und einer Windpressung
von etwa 0at,25 hat sich eine Entfernung der
Formen von 2m,13 am besten bewährt. Die Erhöhung
der Windpressung um 0at,07 verlegt die höchste
Hitze nur um etwa 5cm weiter gegen die Ofenmitte
hin. Dasselbe findet statt bei der Erniedrigung der Windtemperatur. So herrschte
z.B. bei Wind von 650 bis 700° die gröſste Hitze in einem Ringe, welcher sich in
einem Abstande von 35cm vor den Formen befindet.
Bei einer Temperaturverminderung von 175° rückte dagegen der Abstand des Ringes von
den Formen auf etwa 45cm vor. Legte man dagegen
die formen weiter ins Ofeninnere hinein, so war dies gleichbedeutend mit einer
Verminderung des Gestelldurchmessers. Nähere Ausführungen des höchst interessanten
Vortrages finden sich in Engineering, 1882 Bd. 34 * S.
162.
Nach dem Engineering and Mining Journal, 1883 Bd. 35 S.
43 sind auf den Edgar Thomson Steel Works 2 Cowper'sche Winderhitzungsapparate von 6m,4 Durchmesser und 22m Höhe in Betrieb. Bei denselben liegt die Verbrennungskammer an einer
Seite (vgl. Fig. 1 und
2 Taf. 35), so daſs die Gase dieselbe von unten nach oben, die
Regeneratorkammer dagegen von oben nach unten durchstreichen müssen. Statt wie
gebräuchlich letztere mit über einander gesetzten einfachen Steinen zu füllen, werden in derselben von unten nach oben
durchgehende kreisrunde Kanäle von 0m,15
Durchmesser angeordnet. Dieselben werden dadurch gebildet, daſs Steine von der Form
regulärer 6seitiger Prismen und mit einem Mittelkanale versehen neben und über
einander gestellt werden. Die Horizontalfugen der einzelnen Steine sind gegen
einander versetzt. Ein Ansetzen von Flugstaub, welches gewöhnlich in den Ecken der
Durchgangsöffnungen stattfindet, wird durch Anwendung von Kanälen mit rundem
Querschnitte vermieden. Die Apparate haben eine Heizfläche von ungefähr 8500qm und können durch dieselben in der Minute
ungefähr 510cbm Luft durchgeblasen werden, um
deren Temperatur auf 570° zu erhöhen. Dieselbe Temperatur wurde erzielt beim
Durchblasen von 849cbm Luft; dabei betrug die
Essentemperatur 177°. War in Folge des letzteren Umstandes der Zug in den Apparaten nicht
groſs genug, so wurden die Kesselgase direkt in die Esse geleitet und dadurch die
Temperatur der letzteren auf 271° erhöht. Um Zugstörungen zu vermeiden, sind im
unteren Theile der 72m hohen Esse 10m hohe Scheidemauern aufgeführt, welche für jeden
Apparat einen besonderen Kanal bilden. Der lichte Durchmesser der Esse beträgt unten
4m,87, in der Höhe von 12m,5 aber nur 4m,52.
Textabbildung Bd. 248, S. 500
Statt der Steine mit 6eckigem Querschnitte und runden Oeffnungen schlägt J. H. Const. Steffen in Ars a. d. Mosel in Stahl und Eisen, 1883 S. 329 Steine des beistehend skizzirten Querschnittes vor. Dieselben besitzen
einen oblongen Querschnitt von 120mm Wandstärke mit abgeschnittenen Kanten, so daſs
4 Steine an einander gelegt zwischen sich eine Durchgangsöffnung freilassen, die
derjenigen gleich ist, welche in den Steinen selbst liegt, nämlich 167mm × 397mm. Steffen behauptet, daſs diese Steine sich leichter
herstellen lassen und einen besseren Steinverband geben als die regulären Prismen
mit 6 Seiten.
Es herrscht vielfach die Ansicht, daſs bei Verhüttung von stark Zink haltigen
Eisenerzen die Erhitzung des Windes in Whitwell-Apparaten unzweckmäſsig sei und daher die Röhrenapparate jenen vorzuziehen seien. Es ist jedoch nach Stahl und Eisen, 1883 S. 165 der Zinkstaub als nicht
ganz unbesiegbarer Feind hinzustellen. Der gröſste Theil Zinkstaub, an 40 Proc.,
setzt sich bereits in dem dem Gasfange zunächst liegenden Rohre ab, in so fern
dieses mit einigen winkeligen Biegungen und den nöthigen Staubsäcken versehen ist.
In den Waschkästen bleiben weitere 35 Proc., von da bis zu den Einströmungen 13
Proc. zurück und verbleiben für die Röhrenapparate 12 Proc., wovon noch ungefähr der
vierte Theil, also 3 Proc., die Apparate durchstreicht und sich in dem zum Kamine
führenden Kanäle sammelt. Es verbleiben mithin als Ablagerung im Apparate 9 Procent
des mit den Gasen dem Hochofen entführten Zinkstaubes. Bei zweckmäſsiger Gasleitung
wird der Unterschied zwischen der Ablagerung von Zinkstaub in Whitwell- und
Röhrenapparaten kein so erheblicher sein, als angenommen wird. Ein in ersterem
angebrachter tiefer offener Kanal würde als Sammelpunkt des Zinkstaubes gute Dienste
leisten. Daſs bei plötzlichem Niedergange von Zinkschwamm im Hochofen die
Beschaffenheit der Hochofengase beeinträchtigt werde, läſst sich vermeiden durch
frühzeitige Beseitigung des angehäuften Zinkschwammes und durch Anordnung von
Hilfsgasgeneratoren, mittels deren die durch die Hochofengase geheizten Apparate
gespeist werden können, wenn die Hochofengase allein nicht genügen. Auch liegt die
Erfahrung vor, daſs in einem mit starker Pressung und heiſsem Winde betriebenen Ofen
nur unter abnormen Witterungsverhältnissen sich bedeutende Ansätze bilden.
Die Reinigung der Cowper'schen Winderhitzungsapparate bietet nach einem Berichte von H. Fehland (Daselbst 1883 S. 332) doch keine so groſsen
Schwierigkeiten, wie man sonst allgemein annimmt. Innerhalb des Versatzmauerwerkes
findet allerdings eine schwache Sinterung der Steine mit dem Gichtstaube statt. Mit
einer Stahlbürste läſst sich dagegen dieser Ansatz binnen 2 Tagen vollständig
entfernen, nachdem der Apparat vorher 2 Tage mit geöffneten Klappen gestanden und
sich abgekühlt hat. Man hofft, die zur Abkühlung nothwendige Zeit durch Einblasen
von kalter Gebläseluft noch abkürzen zu können. In den Kanälen des Apparates findet
sich nur loser Staub.
Das * D. R. P. Nr. 21269 vom 20. Januar 1882 von A. L.
Holley in Brooklyn betrifft eine Einrichtung, welche Verwendung findet,
wenn die Bessemerbirne so niedrig über der Hüttensohle
liegt, daſs eine Entfernung derselben aus dem Trageringe nach unten behufs
Auswechselung unmöglich ist, es sei denn, daſs man unter der Birne einen Graben zur
Aufnahme des Geleises anordnet (vgl. 1881 239 * 465). Um
nun letzteres zu vermeiden, hebt man den Tragering von der um 180° gekippten Birne
nach oben ab. Zu diesem Zwecke fahrt man zuerst den hydraulischen Wagen unter die
gekippte Birne und fängt diese ab; sodann nimmt man die oberen Lagerdeckel der
Tragezapfen ab, löst die Verbindung zwischen Windrohr und Windkasten und kann nun
den Tragering mittels irgend einer Hebevorrichtung nach oben abheben. Der abgenutzte
Mantel kann nun fortgefahren und durch einen neuen Mantel ersetzt werden. Die
Verbindung des letzteren mit dem Trageringe geschieht auf die bekannte Weise. Diese
Einrichtung wird natürlich nur bei der Einführung des Holley'schen auswechselbaren Birnenbodens in alte Bessemerhütten
getroffen, bei denen ein Umbau unmöglich ist, oder zu groſse Kosten verursachen
würde. Die Fortschaffung der abgenutzten Birnen nach unten ist jedenfalls einfacher
und besser, weil man dabei keines Deckenkrahnes bedarf.
Ueber die basischen Futter der Bessemerbirnen berichtet
das Génie civile 1882 S. 351 folgendes: Die nach dem
Patente D. R. P. Nr. 5869 (vgl. 1879 234 308)
hergestellten Dolomitziegel werden gar nicht mehr benutzt. Die jetzt gebräuchlichen
Ziegel bestehen aus einer Mischung von gebranntem gemahlenem Dolomit mit Theer. Der Dolomit wird zerkleinert in einem Kupolofen mit
abwechselnden Lagen von Kokes im Verhältnisse von etwa ¼ seines Gewichtes gebrannt.
Dabei wird die Hitze durch Anwendung eines kräftigen Gebläses so hoch getrieben,
daſs ein theilweises Fritten stattfindet und der Dolomit ein glasiges Aussehen
erhält. Nachdem die gebrannte Masse von Kokes- und Schlackerückständen befreit, wird
sie gemahlen und mit etwa 7 Proc. Theer zu einer plastischen Masse verarbeitet.
Diese wird zur Herstellung der Ziegel oder zum Ausstampfen der Birnen und Böden
benutzt. Durch das Fritten wird ein allzu schnelles Eindringen der Feuchtigkeit in
die gebrannten Stücke
verhindert und dadurch eine etwas längere Aufbewahrung ermöglicht, ohne daſs die
Stücke zerfallen. Das Mahlen und Mischen des Dolomits mit Theer geschieht in zwei
verschiedenen Kollergängen mit einem Walzengewichte von etwa 5t. Zum Betriebe dieser und des Kupolofen-Gebläses
dient eine Dampfmaschine von etwa 20e. Da der im
Handel vorkommende Theer selten frei von Wasser ist, vielmehr oft bis zu 18 Proc.
desselben enthält, so muſs dieses vor der Verwendung durch Abdampfen entfernt
werden. Dies geschieht in guſseisernen, durch eine Rostfeuerung geheizten Kesseln,
aus welchen der entwässerte Theer mittels eines Dampfstrahlgebläses in eine
Meſskammer gesaugt und von hier in den Mischkollergang gelassen wird. Durch eine
Dampfschlange kann der Theer in der Kammer auf der erforderlichen Temperatur
gehalten werden.
Gestampfte Futter sollen sich, weil sie keine Fugen besitzen, besser bewähren als aus
einzelnen Ziegeln hergestellte und man sucht deshalb die mechanischen Vorrichtungen
zum Ausstampfen der Birnen möglichst zu vervollkommnen.
Im Stahlwerke Rothe Erde bei Aachen wird nur der untere
Theil der Birne mit basischem Futter versehen, der obere Theil dagegen mit sauren
Steinen ausgemauert und die Mündung wieder aus basischen Ziegeln gebildet. Der
hierzu verwendete Dolomit enthält 3 Proc. Silicium, während der Gehalt an Eisenoxyd
und Thonerde ungefähr 4 Proc. beträgt. Die Herstellung der losen Böden geschieht in
Formen, die mit Nadeln zur Bildung der Windkanäle versehen sind (vgl. Rühle 1879 232 * 140). Die
Austrocknung der Böden in einem langen Heizraume, welcher gleichzeitig viele Böden
aufnimmt, dauert 18 bis 20 Tage. Die Brenndauer der Formsteine beträgt 3 bis 4 Tage.
Die losen Böden werden in bekannter Weise von unten in die Birne eingesetzt und wird
die Fuge zwischen Boden und Futter durch Einwerfen von plastischen Ballen aus
Dolomit und Theer durch den Birnenhals gedichtet. Die so hergestellten Böden halten
18 bis 20, das übrige Futter hält etwa 60 Hitzen aus.
Delafond berichtet in den Annales des mines, 1882 S. 366 über vergleichende Untersuchungen des zu
Creuzot ausgeführten sauren und basischen Verfahrens. Das Ergebniſs derselben ist in 4 graphischen Tafeln
zusammengestellt. Die chemischen Analysen ergaben ferner, daſs der saure Stahl noch
ansehnliche Mengen Silicium enthält, der basische Stahl dagegen nur Spuren. Phosphor
und Schwefel enthält der saure Stahl immer mehr als der basische. Der Marigangehalt
schwankt bei beiden Sorten sehr erheblich. Die Durchschnittszusammensetzung des
sauren bezieh. basischen Stahles betrug:
Kohlenstoff
0,40
bezieh.
0,43 Proc.
Silicium
0,30
„
Spar
Mangan
0,66
„
0,76
Phosphor
0,075
„
0,060
Schwefel
0,040
0,029
Eine charakteristische Eigenschaft des basischen Stahles ist
demnach das fast gänzliche Fehlen des Siliciums.
Die Zerreiſsproben des sauren bezieh. basischen Stahles ergaben folgenden
Durchschnitt:
Bruchbelastung auf 1qmm
73,20
bezieh.
72k
Dehnung
17,20
„
16,10 Proc.
Hiernach sind die Festigkeitsverhältnisse bei den Stahlsorten
ungefähr gleich. Die kleinen Hohlräume, welche sich früher im basischen Stahle immer
vorfanden, hat man durch Erhöhung der Temperatur der Hitzen zu vermeiden gewuſst. Zu
diesem Zwecke wurde eine Temperaturerhöhung des Hochofenganges, sowie das Vorwärmen
des Kalkzuschlages für die Birne und schlieſslich ein höherer Gehalt an Phosphor im
Roheisen erforderlich.
Delafond bestätigt ferner, daſs die Entphosphorung des Roheisens in mit basischem Futter
ausgekleideten Herden praktisch und ökonomisch ausführbar sei. Der Herd
wird aus derselben Dolomit-Theermasse, welche zum Ausstampfen der Birnen benutzt
wird, gebildet. Das Gewölbe und die Wände des Ofens bestehen aus Quarzziegeln,
welche durch eine Schicht von Bauxitziegeln von dem basischen Herde getrennt sind.
Der Einsatz besteht aus Roheisen von beliebigem Phosphorgehalte, dem allmählich
gefrischtes Eisen zugesetzt wird. Während der Frischperiode setzt man 3 bis 4mal
gebrannten Kalk zu, nachdem man vorher die dünnflüssige Schlacke von dem Bade
abgezogen hat.
Durch die hochbasische Schlacke und den Sauerstoff der Luft wird zuerst das Silicium
fast vollständig entfernt; es folgen dann der Phosphor und die übrigen Metalloide.
Die Beendigung des Frischprozesses wird durch Schöpfproben bestimmt und die
Rückkohlung des überfrischten Productes durch Zusatz von Spiegeleisen oder
Ferromangan bewirkt. Das Ausbringen einer Hitze beträgt 15t, die Dauer derselben 12 Stunden. Die
Durchschnittszusammensetzung eines im Herdofen aus Phosphor haltigem Roheisen und
Puddeleisen dargestellten Fluſseisens ist folgende:
Kohlenstoff
0,16 Proc.
Silicium
Spur
Schwefel
0,03
Phosphor
0,03
Mangan
0,25
Als Vorzüge des Herdschmelzens vor dem Blasen in der Birne werden folgende angegeben:
1) Die Herstellung und Unterhaltung des basischen Futters bietet bedeutend weniger
Schwierigkeiten. 2) Die Temperatur des Bades wird durch die Ofenfeuerung unabhängig
von der Zusammensetzung des als Einsatz verwendeten Roheisens geregelt. 3) Das
Zusetzen des Kalkes und das Abziehen der Schlacke geschieht mit Leichtigkeit in
jedem dazu geeigneten Augenblicke, während in der Birne hierfür das Ende der Hitze
abgewartet werden muſs und nur dann in genügendem Maſse erfolgen kann, wenn die
Schlacke hinreichend flüssig ist; da dies nicht immer der Fall, so ist in der Birne
beim Rückkohlen die Gefahr einer Phosphorreduction gröſser als im Flammofen. 4) Die
längere Dauer der Frischperiode macht die Entnahme und Prüfung der Schöpfproben
unabhängig von der Zeitdauer, so daſs die Leitung der Hitzen erleichtert wird.
Nach einer Abhandlung von F. Gautier im Génie civil, 1882 S. 385 wird das Pressen des Stahles im flüssigen Zustande in dem
Stahlwerke von Withworth in Manchester in der Weise
ausgeführt, daſs der Stahl in Formen gegossen wird, welche aus einzelnen auf
einander stehenden Stahlringen gebildet und im Inneren mit feuerfester Masse
ausgekleidet sind. Die Formen stehen auf Wagen, die nach dem Gieſsen unter die
hydraulische Presse gefahren werden. Der Kolben der letzteren wird durch einen
feuerfesten Stein vor dem Zusammenschweiſsen mit dem Stahle geschützt und übt einen
Druck von 600at aus, welcher je nach der Gröſse
des Guſsblockes 20 bis 45 Minuten dauert. Der gröſste Theil der im Stahle
enthaltenen Gase wird absorbirt und nur ein kleiner Antheil entweicht durch die
Formfugen. Beim Erkalten des Blockes werden jedoch die Gase theilweise wieder frei,
wodurch am oberen Ende des Blockes ein Hohlraum entsteht, dessen Gröſse mit der des
Blockes zunimmt, so daſs ein Block von 400mm
Durchmesser oft bis zur Hälfte hohl ist. Durchschnittlich muſs ungefähr ⅓ seiner
Länge abgeschnitten werden, um ein gesundes Schmiedestück zu erhalten. Durch das
Pressen des Stahles soll seine Bruchfestigkeit sowie seine Dehnung vermindert
werden, letztere um etwa 4 Proc. (Vgl. 1881 239 137. 1877
225 * 423.)
Je länger der Kopf eines Guſsblockes flüssig bleibt, um so gleichmäſsiger kann sich
derselbe beim Erkalten zusammenziehen und um so weniger Hohlräume werden dabei
entstehen. F. A. Krupp in Essen (* D. R. P. Kl. 31 Nr. 21324 vom 25. Juni 1882) umgibt deshalb
den Kopf des Guſsblockes an den Seiten und oben mit flüssiger Schlacke oder Sand.
Beim Gieſsen ohne Druck besitzt die Form einen doppelwandigen Aufsatz, in welchen
die Schlacke gefüllt und welcher oben durch einen Deckel geschlossen wird. Letzterer
kann auch fortfallen und die Schlacke direkt auf den Block gegossen werden. Fig.
5 Taf. 35 stellt eine Form dar, wie sie beim Gieſsen unter Druck (vgl. 1882 245 * 20) benutzt wird. Wie ersichtlich, ist hierbei in
die Form ein doppelwandiger Einsatz eingehängt, welcher nach vollendetem Gusse bis
über seinen! Rand mit Schlacke gefüllt wird. Zu demselben Zwecke kann man auch eine
gewöhnliche Form mit Aufsatz anwenden und über diese eine luftdicht verschlossene
Glocke setzen. Um die Erstarrung des Guſsblockes noch regelmäſsiger von unten nach
oben verlaufen zu lassen, schlägt Krupp vor, die Form
mit ihrem unteren Ende in Wasser oder eine andere Flüssigkeit, deren Temperatur
durch Zu- und Abfluſs beliebig regulirt werden kann, zu setzen, oder die Form durch
einen Luftstrom zu kühlen.
F. Asthöwer
und Comp. in Annen (* D. R. P. Nr. 21473 vom 28. März 1882) lagern die Walzen
eines Triowalzwerkes so, daſs die Ständer direkt die
Stöſse der einzelnen Walzen aufnehmen. Zu diesem Zwecke wird die Oberwalze F (Fig. 10
Taf. 35) in bekannter Weise mittels der Drucksehraube G
und der Ankerschrauben i eingestellt. Die Lager B der Mittelwalze E
besitzen an ihren oberen bezieh. unteren Seiten schräge Flächen, auf bezieh. unter
welche sich in Aussparungen der Ständer angeordnete Keile d und e legen. Durch Verstellen der letzteren
mittels der in den Ständern selbst geführten Schrauben h kann die Mittelwalze genau eingestellt werden. Die gleiche
Nachstellvorrichtung ist zur Hälfte für die Unterwalze D vorgesehen.
In der Revue industrielle, 1882 * S. 413 ist eine Walzvorrichtung beschrieben, welche denselben Zweck
verfolgt wie die Maschine von Reese (vgl. 1882 243 * 458). Die Maschine ist von Chuwab construirt und dient zum Abrunden, Glätten und Beschneiden von Kolbenstangen, Uebertragungswellen, cylindrischen Achsen,
gröſseren Schraubenbolzen u. dgl. Die zu bearbeitenden Gegenstände werden
jedoch der Maschine nicht kalt, wie bei Reese, sondern
sehr warm zugeführt, nachdem sie vorher mit einem Holzschlägel gerade gerichtet
worden sind. Die Maschine besteht aus 2 Ständern, in welchen die Unterwalze fest
gelagert ist, während die Oberwalze in bekannter Weise verstellt werden kann.
Zwischen den Walzen, welche aus Hartguſs bestehen, sind die Ständer eingeschnitten,
um Arbeitstücke von beliebiger Länge glätten zu können. Die Walzen drehen sich,
entgegengesetzt den gewöhnlichen Walz Vorrichtungen, in gleicher Richtung, so daſs
sie das Walzstück, welches etwas jenseits der Verbindungslinie der Mittelpunkte der
Walzen liegt und sich gegen eine einstellbare Stütze lehnt, um seine eigne Achse
drehen. Der Antrieb der Walzen geschieht von einer fest gelagerten Riemenscheibe
aus, auf deren Welle ein Trieb gekeilt ist, welcher in ein Zahnrad greift, dessen
Welle mit den eingreifenden Stirnrädern der Walzen durch 2 Arme verbunden ist. Da
nun die Welle des Zwischenzahnrades in einem Curvenschlitze der Walzenständer
geführt wird, so findet in jeder Höhenlage der Oberwalze ein richtiger Zahneingriff
des Triebes mit dem Zwischenzahnrade und des letzteren mit den beiden
Walzenstirnrädern statt. Die zum Beschneiden der Enden des Walzstückes dienenden Kreissägen sind an den beiden Walzenständern angeordnet
und können durch Hebel gegen das Walzstück gedrückt werden. Der Antrieb der Sägen
wird durch Reibungsräder bewirkt.
Alb. L.
Murphy in Philadelphia (* D. R. P. Nr. 18246 vom 31. Juli 1881) walzt Röhren aus röhrenförmigen Packeten. Zu diesem Behufe
werden um eine fertige Röhre von entsprechend groſsem Durchmesser Flacheisenstäbe
oder Walzeisen von anderem Querschnitte gelegt, das Ganze mit Draht zusammengebunden
und dann in den Schweiſsofen gebracht.
Statt Stab-Profileisen beim Erkalten sich selbst zu überlassen, wodurch häufig,
besonders bei unregelmäſsigen Querschnitten, ein Krummziehen hervorgerufen wird,
spannen Max
Wille in Magdeburg und H. Kraemer jun. auf Elsterstein bei St. Ingbert (*
D. R. P. Nr. 21434 vom 23. Juli 1882) die Stäbe
zwischen 2 Greifzangen A und B (Fig. 11
Tafel 35) ein, wovon die eine am Kühlbette befestigt, die andere dagegen durch ein
Handrad C mit Doppelschraube angezogen werden kann.
Zwischen dem Befestigungshaken und der Zange ist eine Pufferfeder eingeschaltet, um
ein Reiſsen des Stabes beim durch das Erkalten hervorgerufenen Zusammenziehen zu
vermeiden. Auſserdem muſs letzterem noch durch Nachlassen der einen Zange Rechnung
getragen werden.
Um eine schnellere Schmelzung der Kupolofenposten herbeizuführen, brechen die Amerikaner die
Masseln in einer Maschine in Stücke von 15 bis 17cm Länge. Die betreffende Maschine ist von Blake construirt und besitzt nach dem Engineering, 1883 Bd. 35 S. 198 drei stumpfe Schneiden,
von denen die untere a (Fig. 4 Taf.
35) in einem Ambosse befestigt ist, während die beiden oberen b und c auf einem am
Maschinengestelle geführten Schlitten l angeordnet
sind; letzterer wird von den Gummipuffern d in solcher
Höhe gehalten, daſs eine Massel von der Rollbahn e aus
bequem zwischen die Schneiden eingeführt werden kann. Mittels der Riemenscheiben f, dem Rädervorgelege h,
der Kurbel i und des Kniehebels k wird dem Schlitten l eine auf- und
abgehende Bewegung ertheilt und dadurch die unter die Schneiden b und c geschobene Massel
über der Schneide a gebrochen. Die Zugstange m zwischen der Kurbel und dem Kniehebel ist in der
Länge verstellbar, so daſs der Hub des Schlittens l
vergröſsert oder verkleinert werden kann.
Otto Gmelin in Budapest verbessert die gewöhnliche Kupolofeneinrichtung wesentlich dadurch, daſs er den
Schachtmantel statt aus einem einfachen Eisencylinder aus einem doppelwandigen
Cylinder, welcher durch Wasser gekühlt wird, herstellt. Diese Ausführung bietet den
früher gemachten Vorschlägen, das Ofenmauerwerk, welches beim Gmelin'schen Ofen ganz fortfallen kann, durch
Kühlkästen oder Ringe zu unterbrechen, bedeutende Vortheile, weil dieselbe die bei
Anwendung von eingemauerten Kühlkästen in Folge der ungleichen Ausdehnungen von
Mauerwerk und Eisen auftretenden Risse gänzlich vermeidet. Der Gmelin'sche Kupolofen hat nach der Oesterreichischen Zeitschrift für Berg- und
Hüttenwesen, 1882 S. 526 folgende Einrichtung: Der Schacht des Kupolofens
wird aus einem eisernen Doppelcylinder a a1 (Fig. 8 und
9 Taf. 35) gebildet, dessen ringförmiger Hohlraum oben offen, unten
dagegen wasserdicht abgeschlossen ist. Der Doppelcylinder steht auf einem 300 bis
350mm hohen Ringe von feuerfestem Mauerwerk
c, welches oben durch eine Guſsplatte abgedeckt und
auſsen von einem einfachen Eibenmantel umschlossen wird. An der den Ofenschacht
bildenden inneren Fläche, welche gerauht ist, sind die Nietköpfe linsenförmig
abgeplattet, um mit
einem feuerfesten Futter von 30 bis 50mm Stärke
bekleidet werden zu können. Dem unteren Theile des Doppelcylinders wird an zwei
gegenüber liegenden Stellen d kaltes Wasser unter Druck
zugeführt, welches, nachdem es den Mantel gekühlt hat, oben bei e offen ausflieſst, so daſs die den Ofen bedienenden
Arbeiter sich durch den Augenschein leicht von der regelmäſsigen Kühlung des
Schachtes überzeugen können. Die obere Ringöffnung des Doppelcylinders wird durch
eine Guſseisenplatte k einfach abgedeckt. Die
Formöffnungen f und der Schlackenabstich g werden durch beide Wände des Doppelcylinders
verbindende Stutzen aus Kesselblech gebildet. Der Eisenabstich liegt in dem
feuerfesten Mauerwerke c.
Die Reinigung des Doppelcylinders von in seinem Hohlräume sich absetzendem Schlamme
geschieht durch den Hahn l und die Reinigungsöffnungen
m.
Der Ofen soll den bekannten Kupolöfen gegenüber folgende Vortheile besitzen: Die
schädliche Einwirkung des Windes, dessen Pressung eine beliebige sein kann, fallt
fort, da das in Höhe der Düsen liegende Futter durch die Wasserkühlung genügende
Festigkeit besitzt, um dem Winde widerstehen zu können; der vollständig aus
Mauerwerk hergestellte Herd c ist der Einwirkung des
Windes entzogen, da er mit Eisen gefüllt ist. Die Erhaltung des Ofens in
betriebsfähigem Zustande fordert geringere Kosten; dieselben werden durch
Beschaffung des Kühlwassers etwas erhöht, fallen aber immer geringer aus als die bei
anderen Kupolöfen. Eine Verletzung der feuerfesten Auskleidung während des Betriebes
ist ohne Belang; findet sie innerhalb der Schmelzzone statt, so setzt sich sofort
eine Schlackenkruste auf das gekühlte Eisen ab, welche eine weitere schädliche
Einwirkung der Hitze, Schlacke und der niedergehenden Materialien auf dasselbe
verhindert. Der Kalkzuschlag kann beliebig gesteigert werden, weil sich der Kalk nur
schwer mit den festen sauren Ofenwandungen verbinden wird. Einer basischen
Auskleidung des Ofens steht natürlich nichts im Wege. Eine Verlegung der Schmelz-
und Reductionszone nach oben findet selbst bei längerem Betriebe nicht statt, da die
Kühlung den Schacht in seinen einzelnen Höhen immer auf gleicher Temperatur erhält.
Es wird an Brennmaterial gespart, weil das Austrocknen und Vorwärmen des Ofens
wegfällt, durch die Schmelzung an Mauerwerk keine Wärme absorbirt wird, die Wände im
Laufe des Betriebes keine unregelmäſsigen Formen annehmen, eine stärkere Erhitzung
der oberen Materialschichten, wie schon oben angedeutet, nicht stattfindet und die
Pressung des Windes nicht mit Rücksicht auf das Mauerwerk niedrig gehalten zu werden
braucht.
Die Wärmeabgabe durch die Schachtwand an das Kühlwasser beträgt beim Gmelin'schen Ofen ungefähr 15 Procent der gesammten in
demselben entwickelten Wärmemenge, mithin etwa das 3 fache der Wärmeausstrahlung
beim ausgemauerten Ofen. Die letztere Eigenschaft, welche das Arbeiten an ausgemauerten
Oefen so beschwerlich macht, fällt beim Gmelin'schen
Ofen fast ganz weg. Abgesehen hiervon wird die Arbeit noch dadurch erleichtert, daſs
geringere Schlackenmengen fallen und das Putzen der Formen nur seltener nothwendig
wird. Ein Gmelin'scher Kupolofen von 4m Höhe und 850mm
lichtem Durchmesser (zwischen der feuerfesten Auskleidung gemessen) hat während
einer einjährigen Betriebszeit bei einem Winddrucke von 400 bis 450mm Wassersäule und einem Kokesverbrauche von
ungefähr 8 Proc. (ungerechnet Füllkokes) stündlich 4500 bis 5000k Eisen niedergeschmolzen (vgl. F. Fischer 1879 231 39). Der
Verbrauch an Kühlwasser betrug durchschnittlich 1351 in der Minute; dasselbe verläſst den Ofen mit einer durchschnittlich um
40° erhöhten Temperatur. Eine Reinigung des Doppelcylinders vom Schlamme und
geringfügige Ausbesserungen des Thonbeschlages fanden nur alle 3 Monate statt. Der
Doppelcylinder ist an keiner Stelle schadhaft geworden. (Vgl. auch * D. R. P. Nr.
22859 vom 9. September 1882.)
Bekanntlich kann man im Kupolofen nur reine Kokes benutzen, wenn es darauf ankommt,
dem umzuschmelzenden Eisen keine Verunreinigungen zuzuführen. Mangel an reinen Kokes
führte zur Verwendung gasförmiger Brennmaterialien. E.
Dufréné in Paris (* D. R. P. Nr. 18483 vom 28. Mai 1881) ordnet den Generator in direkter Verbindung mit dem Kupolofen an.
In letzterem sind über dem Sammelraume S (Fig.
6 und 7 Taf. 35)
mehrere Bögen p geschlagen, die durch eine mittlere,
oben und unten bei e und f
durchbrochene Querwand M unterstützt werden und durch
freie, nicht zu breite Spalten von einander getrennt sind. Auf diesen Bögen ruht die
Beschickung, bestehend aus dem Umschmelzeisen und den Zuschlagsmaterialien.
Dieselben müssen so locker auf einander liegen, daſs noch ein genügend freier
Querschnitt zum Durchlasse der Verbrennungsgase verbleibt. Da ein Herunterwerfen der
Masseln von der Gichtöffnung die Bögen zerstören würde, so werden die Masseln in
einen Kübel geladen und mittels zweier Ketten bis auf die Bögen heruntergelassen.
Durch Anziehen einer Kette wird der Kübel umgestürzt. Der Generator G, welcher mit dem Kupolofen durch die Oeffnung D in Verbindung ist, besteht aus einem eisernen
doppelwandigen Cylinder mit Decke. In letzterer ist einer der bekannten
Begichtungstrichter angeordnet. Unten wird der Cylinder durch den Rost begrenzt,
welcher allseitig geschlossen ist und dem durch das Rohr r Gebläsewind zugeführt wird. Ein Theil der letzteren durchströmt in
Schraubenwindungen die 3 Abtheilungen der doppelten Wand und trifft durch die Decke
am oberen Theile des Verbindungskanales D mit den hier
ausströmenden Gasen zusammen. Dieselben verbrennen und schmelzen, nachdem sie durch
die Schlitze q zwischen den Bogen getreten sind, die
Beschickung herunter. Das Eisen tropft in den Sammelraum und wird bei F abgestochen.
L. M. F.
Besson in Lyon legt bei seinem Kupolofen mit Gasfeuerung (* D. R.
P. Nr. 19051 vom 13. December 1881) mehr Gewicht auf eine schnellere Schmelzung des
Schmelzgutes und erreicht diese dadurch, daſs er den Kupolofenschacht A (Fig. 3 Taf.
35) mit einer Art Flammofen B verbindet, in dessen Herd
der Sammelraum C angeordnet ist. Die Generatorgase
werden dem Flammofen durch das Rohr D zugeführt und von
dem durch die Düse E in den Ofen tretenden Gebläsewinde
verbrannt. Die so gebildete Stichflamme trifft nun direkt das aus dem Schachte
nachrutschende Schmelzgut und führt eine schnelle Schmelzung herbei. Oberhalb des
Sammelraumes ist in der Decke des Flammofens eine Winddüse F angebracht, welche die Möglichkeit einer Erhitzung oder Feinung des
Eisens im Sammelraume bezweckt. Hauptsache bei den Kupolöfen mit Gasfeuerung bleibt
natürlich die reducirende Flamme, da sonst ein zu groſser Abbrand entstehen
würde.
Um Abfälle von Schmiedeisen und Stahl, z.B. Drehspäne,
dünne Blechschnitzel u.s.w., verwerthen zu können, ohne sie im Kupolofen umzuschmelzen, macht Herm. Reusch in
Dillingen a. d. Saar (* D. R. P. Nr.
18726 vom 30. September 1881) dieselben in einem kleinen Schachte, durch
welchen er eine Flamme streichen läſst, stark rothglühend, bringt sie in starke
rectanguläre eiserne Formen und schlägt sie in diesen unter einem Hammer zusammen.
Der Schachtofen besitzt eine geneigte Sohle, deren Ausziehöffnung direkt über den
eben erwähnten Formen liegt. Auf der entgegengesetzten Seite des Ofens mündet der
Fuchs einer Rostfeuerung in den Ofenschacht ein, welche den Eisenabfällen die
nöthige Wärme zuführt.
St.
Tafeln
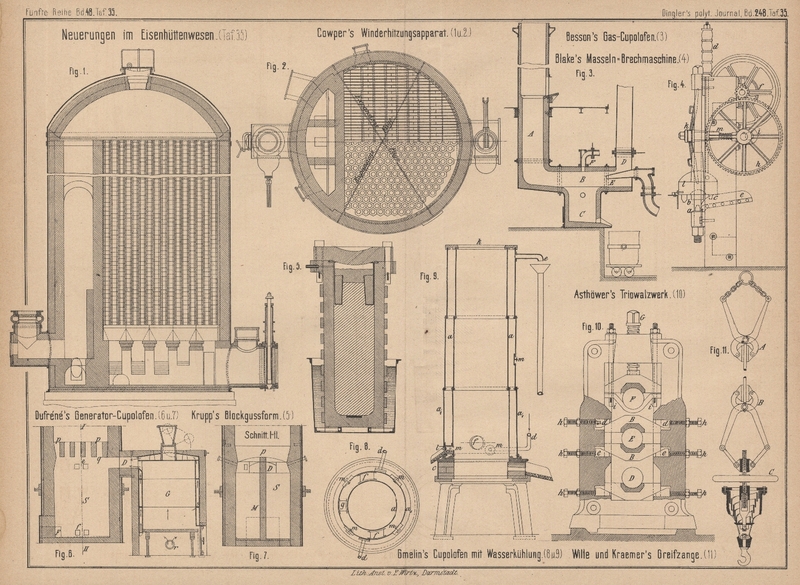