Titel: | Neuerungen in der Gespinnstfabrikation; von Hugo Fischer. |
Fundstelle: | Band 249, Jahrgang 1883, S. 202 |
Download: | XML |
Neuerungen in der Gespinnstfabrikation; von Hugo
Fischer.
Patentklasse 76. Mit Abbildungen auf Tafel 14.
Hugo Fischer, über Neuerungen in der
Gespinnstfabrikation.
Im Anschlüsse an die früheren Berichte (vgl. 1882 243 *
119.* 195) ist im Nachfolgenden versucht, in kurzen einfachen Darstellungen den
wesentlichen Inhalt derjenigen Deutschen Reichspatente wiederzugeben, welche die
Gespinnstfabrikation betreffen und seit der Niederschrift der genannten Referate bis
jetzt durch das Reichspatentamt veröffentlicht wurden. Allerdings war auch hier, wie
früher, eine Auslese zu halten, da nicht alle der ertheilten Patente für die
Besprechung geeignet erschienen. Die folgenden Zeilen sind demnach als Fortsetzung
der früheren Darlegungen zu betrachten. Zur Erleichterung der Uebersicht ist auch
hier die Eintheilung des Stoffes in einzelne Kapitel erfolgt, welche solche
Gegenstände zusammenfassen, die gleiche Arbeitsziele verfolgen. Einzelne
Abweichungen von der früheren Eintheilung wurden durch den Mangel geeigneter
Unterlagen bedingt, da sich die Erfinderthätigkeit nicht gleichmäſsig auf alle
Theile des Spinnereigebietes erstreckte.
1) Vorbereitung vegetabilischer
Faserstoffe.Vgl. Hugo Fischer 1880 238 * 34. Spencer 1881 239 352. Mülhauser Vorschriften 1881 240 361. Holt's Wolf
und Schlagmaschine 1881 241 * 356. Miauton's Carbonisirapparat 1882 244 * 380. Clough's
bezieh. Mehl's Wollwaschmaschine 1882 244 * 432 und 1883 247
* 368. O. Schimmel's bezieh. Polster's Wolltrockenapparate 1883 248 * 357.
Die Gewinnung der spinnbaren Fasern aus den Stengeln des
Hanfes, Flachses und anderer Pflanzen ist durch H.
C. Fricke in Bielefeld (* D. R. P. Nr. 18195 vom 17. November 1881) um ein
neues Arbeitsverfahren und eine auf demselben gegründete Brechmaschine bereichert
worden; – ob zum Vortheile muſs allerdings vorläufig dahingestellt bleiben und wird
erst durch eingehende Versuche zu erweisen sein. Bei der Beurtheilung dürfte
jedenfalls der Umstand, daſs aller Voraussicht nach bei ungenügender Aufmerksamkeit
des Arbeiters die Fasern beträchtlichen Zugspannungen und daher Schädigung ihrer
Festigkeitseigenschaften unterworfen werden können, nicht auſser Acht zu lassen
sein. Nach den Angaben des Erlinders erfolgt die Zerstörung der die Fasern
bedeckenden Holzschicht dadurch, daſs die Stengel an zwei oder mehreren Stellen
ihrer Länge von Zangen erfaſst werden, welche abwechselnd eine auf- und
niedergehende Bewegung erhalten derart, daſs je zwei benachbarte Zangen immer
entgegengesetzte Bewegung besitzen. Hierdurch werden die zwischen den Zangen frei
liegenden Stengeltheile abwechselnd nach entgegengesetzten Richtungen durchgebogen und an den
Zangenwänden gerieben. Die Stengelfaser widersteht dem hierbei auf sie ausgeübten
Zuge; die holzige, scharf getrocknete Umhüllung wird dagegen zerbrochen und
theilweise von der Faser abgestreift.
Die Zangen sind, wie Fig. 1 und
2 Taf. 14 zeigen, von zwei hölzernen Hebeln a und h gebildet, deren Drehpunkte in dem
Gestelltheile c liegen. Den Schluſs der Zangenbacken
und den Druck derselben gegen die Pflanzenstengel bewirken Schrauben federn d, welche an dem kleinen Winkelhebel e hängen. Die Kurbelscheibe f und Treibstangen g vermitteln die
schwingende Bewegung der Backen a, b. Die Lagerung der
Hebel bedingt es, daſs bei der Schwingung die Zangenflächen, welche die Stengel
halten, auf einander gleiten und somit die Holztheile von den Fasern abzureiben
streben. Für das Durchziehen der Stengel zwischen den Zangenbacken rechnet Fricke auf die Trägheit des rasch schwingenden oberen
Backens, welcher, da nicht direkt angetrieben, bei der Rückkehr des unteren Backens
aus seiner höchsten Stellung kurze Zeit in der gehobenen Lage verharrt und somit die
eingeklemmten Stengel freigibt. Zur vollständigen Zangeneröffnung dient der
Fuſstritt h, welcher den Drehzapfen des Winkelhebels
e trägt. Der kurze hakenförmige Arm dieses
letzteren stützt sich während der Arbeit gegen den festen Gestellzapfen i; die Feder d ist dadurch
fest gehalten, wird aber durch Aushängen des Hebels e,
beim Niedertreten des Trittes h und Anheben des freien
Endes von e mit der Fuſsspitze ausgelöst. In diesem
Falle hebt das am Hebel k befestigte Gewicht l den Tritt empor, gleichzeitig mittels des Bügels m den oberen Zangenbacken von dem unteren abhebend.
Erst durch Niedertreten des Trittes findet wieder der Schluſs der Zange und die
Spannung der Feder statt.
Die von J. Roguet in Paris (* D. R. P. Nr. 18358 vom 22.
Oktober 1881) angegebene, in Fig. 3 Taf.
14 dargestellte maschinelle Einrichtung ist die Vereinigung einer Brech- und Schwingmaschine. Die erstere wird aus zwei
Cylinderpaaren a1, a2 und b1, b2 gebildet, denen das
Material auf dem Tische c zugeführt wird. Die
cylindrischen Walzen sind parallel zur Achse gerippt, die unteren von dem Zahnrade
d angetrieben, die oberen durch Federn belastet,
deren Spannung durch Druckschrauben regulirbar ist. Der Austrittstelle des
Walzenpaares b1, b2 gegenüber liegt die
Schwingtrommel S, deren aus polirten Holz- oder
Metallplatten bestehende, parallel zur Drehachse am Trommelumfange befestigte und
durch Kautschukbuffer nachgiebig unterstützte Schwingmesser s dicht an den Walzen und der Innenfläche eines die Trommel concentrisch
umschlieſsenden Rostes r aus polirten Stäben vorüber
streichen. Die Walzen a2, b2
erhalten Pilgerschrittbewegung, welche hier durch ein Ead'sches Getriebe von der Drehung der beiden Achsen e, f abgeleitet ist. Die Achse e trägt ein Excenter, auf dessen Umfang das durch den Arm g an der Achsendrehung gehinderte Rad h drehbar aufgesetzt ist und die Drehung des Excenters auf den
Zahnkranz z1 des Rades
d und somit auch auf die mit dem innen verzahnten
Kranze z2 dieses Rades
in Eingriff stehenden Antriebräder der Walzen a2, b2 überträgt. Dies liefert die Einzugsbewegung dieser
Walzen. Gleichzeitig wird aber auch der Arm g von dem
Excenter i auf der Achse f
der Schwingtrommel in rasche Schwingung versetzt und dadurch dem Rade h eine geringe Vor-und Rückdrehung um seine
geometrische Achse ertheilt, welche sich abwechselnd zu der Hauptdrehung dieses
Rades und folglich auch zur Drehung der Walzen a2, b2 addirt oder subtrahirt. Diese Walzen
erhalten demnach die der Pilgerschrittbewegung eigenthümliche bald vorwärts, bald
rückwärts gerichtete Drehung, was das Brechen und Abstreifen der Holztheile
wesentlich fördert, ohne doch die Lieferungsfähigkeit zu beeinträchtigen.
Eine eigenthümliche Zuführungseinrichtung zeigt die zur Lösung der spinnbaren Fasern aus unreifem Chinagrase, Flachse, Hanfe und
dgl. von der Compagnie industrielle de la Ramie in
Paris (* D. R. P. Nr. 10309 vom 7. Januar 1880) angegebene Maschine, deren
prinzipielle Einrichtung in Fig. 4 und
5 Taf. 14 dargestellt ist. Diese Einrichtung besteht aus einem um Umfange ausgekehlten und um die vertikale Achse a drehbaren Rade b und dem
von der stellbaren Rolle c geleiteten endlosen Seile
d (vgl. auch Berthet
1882 244 * 121). Die Pflanzenstengel werden bei x so zwischen Seil und Scheibenrand eingeführt, daſs
sie etwa in der Mitte ihrer Länge erfaſst und durch Einpressen in die Scheibenkehle
um fast 180° zusammengebogen werden. Die der oberen Scheibenfläche zugekehrten
Fasern legen sich hierbei auf den kleinen Tisch e auf
und werden von diesem den gerippten Walzen f, g
zugeleitet. Diese erfassen die Fasern, brechen die Holztheile und streifen diese, da
die Fasern durch die Scheibe und das Seil gleichzeitig vorwärts gezogen werden, ab,
so daſs die gereinigte Faser bei y aus dem
zangenähnlichen Apparate entfernt werden kann. Für das Reinigen der zweiten
Faserhälfte werden die gereinigten Enden an einem Haken der oberen Scheibenfläche
verschlungen und ebenfalls zwischen die Walzen geführt.
Eine Maschine für die Absonderung der spinnbaren Bastfasern
aus den Stengeln der chinesischen Nessel empfiehlt P. A. Favier in Villefranche (* D. R. P. Nr. 12 785 vom 15. August 1880).
Nach dem der Maschine zu Grunde liegenden Arbeitsverfahren werden die frischen oder
gedörrten Stengel durch einen bis zur Mitte des Stengelquerschnittes reichenden
Schnitt in der Längenrichtung aufgeschlitzt, zu einem ebenen flachen Streifen
gebogen, der innere, jetzt frei liegende Holzkern vielfach gebrochen und von den
Bastfasern abgelöst und schlieſslich diese letzteren durch Reibung von der äuſseren
Rinde befreit. Die in Fig. 8 Taf.
14 in ihrer prinzipiellen Einrichtung zur Darstellung gebrachte Maschine setzt sich
aus zwei Theilen zusammen, der Abschälmaschine A und
der Reibmaschine B. Beide Theile verbindet, wenn es
sich um die Bearbeitung
bereits getrockneter Pflanzenstengel handelt, ein Transporttuch t oder bei der Schälung frischer Stengel eine doppelte
Reihe hohler, mit Dampf geheizter Walzen, welche der entholzte Stengel durchläuft,
um theilweise getrocknet in die Reibmaschine überzutreten.
Vor dem Eintritte in die Walzenpaare a1 bis a4 der Abschälmaschine
durchläuft der Stengel die anfänglich kreisförmig gestaltete, nach dem Ende zu flach
gedrückte Hülse b. Er wird hierbei von dem bis zur
Hülsenachse herabragenden Messer c aufgeschlitzt und
gelangt flach gebogen zwischen die Walzenpaare a.
Starke Zusammenpressung löst hier den Holzkörper theilweise von dem Baste, so daſs
sich nach dem Zerbrechen der Holzschicht mittels des rasch rotirenden Schlägers d die Holztheilchen leicht absondern und zwischen den
Transportwalzen e austreten. Die Reibmaschine, welcher die entholzte Bast- und
Rindenschicht nun zugeführt wird, besteht aus einer Reihe gröſserer Trommeln f mit parallel zur Achse gerippten Mantelflächen. Diese
werden auf der unteren Hälfte ihres Umfanges von einer Reihe parallel zu einander
gelagerten, ebenfalls gerippten, dünneren Walzen g
umschlossen. Die groſsen Walzen werden direkt angetrieben, die kleineren durch den
Eingriff der Riffeln bezieh. durch die Reibung der zwischen den Walzen
durchlaufenden Fasern mitgenommen. Den Uebergang zwischen zwei benachbarten Trommeln
f vermitteln die Leitwalzen h und Windräder i. Die Riffeltheilung der
Walzen nimmt gegen den Austrittspunkt der Maschine hin allmählich ab; sie beträgt
z.B. für Maschinen mit sechs groſsen Walzen von 160mm Durchmesser bei je zwei auf einander folgenden Walzen 3mm, 2mm,5
bezieh. 2mm. Die kleinen Walzen erhalten hierbei
50mm Durchmesser. Für die Bearbeitung frischer
Stengel empfiehlt es sich, die groſsen Walzen mit Dampf zu heizen; auch ist eine
kurze Hin- und Herschiebung dieser Walzen in der Achsenrichtung der Reindarstellung
der Faser förderlich.
2) Entkletten der Wolle.
Die vollkommene Befreiung der Kammwolle von Kletten und anderen gröſseren
Unreinheiten, welche von den Wollhaaren dicht umschlungen werden, gelingt bei den
zur Zeit üblichen, mit den Krempelspeiseapparaten verbundenen
Entklettungseinrichtungen meist nur unbefriedigend. Es ist dies die Folge des
Umstandes, daſs stets nur die eine Seite der die
Klettenwalze bedeckenden Wollschicht, nämlich die äuſsere, der Wirkung des
Klettenschlägers ausgesetzt ist, während die auf den Grund der Walzengarnitur
gedrückten Unreinheiten sich der Schlagwirkung entziehen. Die Firma Klein, Hundt und Comp. in Düsseldorf (* D. R. P. Nr.
11050 vom 31. März 1880) beseitigt diesen Mangel in einfacher Weise durch Anfügung
einer weiteren Klettenwalze mit Schläger zwischen
Trommel und dem das Wollvlieſs an diesen abgebenden Wender. Die Einrichtung ist
durch Fig. 9 Taf. 14 veranschaulicht. Die auf dem Lattentuche a ausgebreitete und von den Einziehwalzen b erfaſste Wolle tritt in den Beschlag der ersten
Klettenwalze k1 ein,
auf welcher die oberhalb der Zahnspitzen liegenden Kletten von dem Schläger s1 in die Mulde m1 abgeworfen werden.
Durch eine zweite Klettenwalze k2 mit kleinerer Umfangsgeschwindigkeit als k1 findet eine Theilung
der Wollschicht in der Dicke statt, derart, daſs die obere Schichthälfte auf diese
Walze übergeht, um hier nochmals der Wirkung des Schlägers s2 unterworfen und dann an die Wenderwalze
w abgegeben zu werden. Die in k1 zurückgebliebene
Vlieſshälfte wird an der Berührungsstelle von k1 und w ebenfalls von letzterer aufgenommen und vereinigt
sich somit wieder mit der über k2 gegangenen Hälfte. Sie bildet aber jetzt nicht
mehr die untere Schicht, sondern steht auf den Spitzen der Kratzenzähne, wird in
dieser Lage auf die neu zugefügte dritte Klettenwalze k3 übertragen und hier von dem rotirenden
Schläger s3 gereinigt.
Die beiden vom Wender w und von der Klettenwalze k3 kommenden
Vlieſsstreifen vereinigen sich sodann auf der Krempeltrommel T.
L. Offermann in Leipzig (*Erl. D. R. P. Nr. 10000 vom 6.
Januar 1880) bemüht sich die bei der Verarbeitung der Kammwolle auf der Krempel
aufgerollten und in Fasern verschiedener Länge zerlegten Ringelkletten dadurch für die Abscheidung aus dem Vlieſse vorzubereiten,
daſs er dieselben zerstückelt und somit die Ablösung
von der Faser bei dem Kämmprozesse erleichtert. Die Einrichtung besteht aus zwei
über einander gelagerten und fest zusammengepreſsten Walzen a und b (Fig. 6 Taf.
14). Die untere Walze b besitzt eine glatt abgedrehte
Mantelfläche, die obere a ist mit ringsum laufenden,
scharfkantigen Rippen versehen. Der Durchmesser des mittleren Walzentheiles ist
wenig kleiner als derjenige der Endscheiben c und d, so daſs die Schneiden der Rippen um einen kleinen
Betrag von der Umfläche der Walze b abstehen. Hierdurch
soll eine Verletzung der stark elastischen, in dünne Schicht zwischen die Walzen
geführten Wollfasern vermieden, dagegen die Zertrümmerung der stärkeren und spröden
Klettenfasern herbeigeführt werden.
Vorzugsweise für die Reinigung des durch Zerfaserung von
wollenen Lumpen erhaltenen Fasergemenges (Kunstwolle) von fremden Festkörpern ist ein von J.
S. Bolette in Pepinster (* D. R. P. Nr. 16537 vom 5. April 1881)
angegebener Krempelspeiseapparat bestimmt. Die Eigenthümlichkeit dieser in ihren
wesentlichen Theilen durch Fig. 7 Taf.
14 wiedergegebenen Einrichtung besteht darin, daſs die Speisung der Krempeltrommel
T periodisch mit kleinen Fasermengen erfolgt, die
ein rotirender oder, wie in der Zeichnung dargestellt, durch ein Kurbelgetriebe
geradlinig hin und her bewegter Kamm k den Speisewalzen
a entnimmt und an die Walze b abgibt. Auf dem Wege von a nach b läuft dieser Kamm an einem rasch rotirenden
Klettenschläger s vorüber, welcher die auf den
Kammzähnen ruhenden Festkörper abschlägt und in die Mulde m wirft. Kurze, hierbei mit fortgeschleuderte Faserenden scheidet ein
durch den Ventilator v erzeugter Luftstrom von den
herabfallenden Unreinheiten und führt sie der Walze c
und der Krempeltrommel T zu. Die Reinigung der Fasern
ist in Folge der von dem Schläger s getroffenen
geringen Fasermenge jedenfalls eine vorzügliche; doch läſst es die periodische
Speisung der Krempel fraglich erscheinen, ob die Leistungsfähigkeit der letzteren
als eine für die Praxis genügende zu betrachten ist.
(Fortsetzung folgt.)
Tafeln
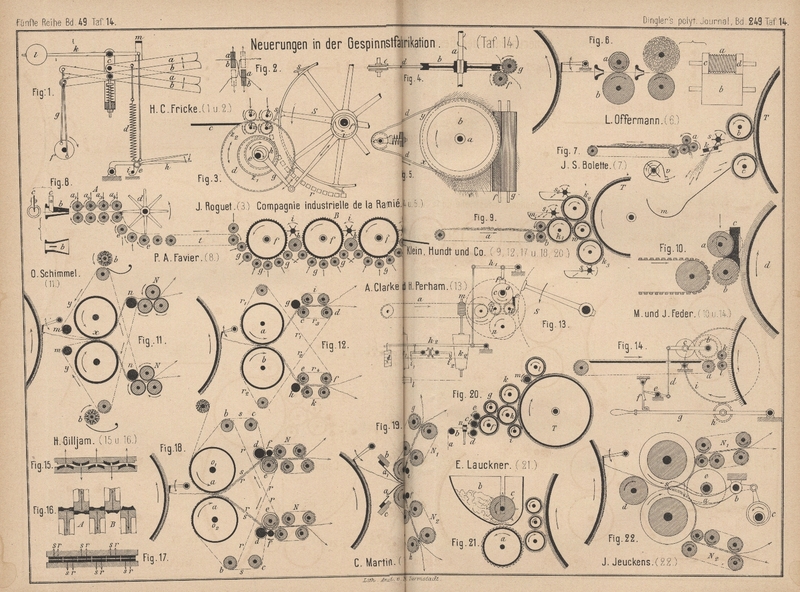