Titel: | Ueber Neuerungen im Eisenhüttenwesen. |
Autor: | St. |
Fundstelle: | Band 249, Jahrgang 1883, S. 440 |
Download: | XML |
Ueber Neuerungen im Eisenhüttenwesen.
(Patentklasse 18. Fortsetzung des Berichtes Bd.
248 S. 498.)
Mit Abbildungen im Texte und auf Tafel 31.
Ueber Neuerungen im Eisenhüttenwesen.
Zum Feinen und Frischen des Roheisens bedient sich Cam. Lévêque in Pouzin, Frankreich (* D. R. P. Nr.
22410 vom 8. November 1882) eines kleinen, auf Rädern ruhenden Herdes von
ringförmigem oder rechteckigem Querschnitte, in welchen am Boden Winddüsen
hineinreichen und dessen Decke aus einem aus einander nehmbaren Gewölbe besteht, in
welchem sich Rauchabzugsröhren befinden. Das Roheisen wird aus dem Hochofen in den
Apparat abgestochen; sodann werden die Winddüsen durch eine biegsame Rohrleitung mit
dem Windrohre verbunden und wird so lange Wind durch das Metallbad geblasen, bis der
gewünschte Grad der Reinheit erreicht ist. Man sticht dasselbe dann ab und läſst es
in die Gieſsbetten laufen. Den Apparat kann man hiernach leicht auf Schienengeleisen
entfernen und durch einen frisch zugestellten ersetzen.
Herrn. Wedding macht in Stahl
und Eisen, 1883 S. 334 einen Vorschlag zur Gewinnung eines Materials für den Flammofen-Fluſseisen-Prozeſs aus Roheisen
mittleren Phosphorgeholtes ohne eine Oxydationsarbeit. Da gegenwärtig in
Deutschland Roheisenmarken von weniger als 0,1 Proc. Phosphor für den sauren, solche
von mehr als 1,5 Proc. Phosphor für den basischen Bessemerbetrieb gesucht sind, die
dazwischen liegenden Marken aber schwer Abgang finden, so schlägt Wedding vor, diese Eisensorten in flüssigem Zustande
längere Zeit stehen zu lassen und, nachdem eine Trennung des reineren von dem
unreineren Eisen stattgefunden hat, ersteres, welches oben steht, abzuzapfen.
Verfasser denkt sich die Ausführung des Verfahrens etwa folgendermaſsen.
Der in einer fahrbaren Pfanne, wie sie z.B. für den direkten Bessemerprozeſs
verwendet wird, gesammelte Hochofenabstich bleibt unter Luftabschluſs möglichst
lange stehen. Die oberen zwei Drittel gelangen dann noch flüssig in den tiefsten
Herd eines stufenförmig angelegten 3herdigen basischen Martinofens, in welchem sich
bereits ein aus dem Prozesse herrührendes Eisenbad befindet. Jeder Herd hat seine
eigenen Gas- und Verbrennungsluft-Kanäle, so daſs seine Temperatur beliebig gestellt
werden kann. Das auf hohe Temperatur erhitzte Eisen steht hinreichende Zeit still,
sondert sich dabei und wird dann abgekühlt. Die sich auf der von Schlacke befreiten
Oberfläche bildenden Krystallhäute werden in den nächst höheren Herd übergeschöpft,
wo sie wieder eingeschmolzen und der gleichen Operation ausgesetzt werden. Die in
dem obersten Herde gebildeten Krystalle gehen direkt in einen gewöhnlichen
Fluſseisenflammofen; die Eisenmutterlauge aus dem obersten Herde dagegen nimmt ihren
Rückweg allmählich bis zum tiefsten Herde, aus welchem sie abgestochen wird und
vielleicht als Material für den basischen Bessemerprozeſs oder als Gieſsereiroheisen
verwerthbar scheint. Wedding fordert die deutschen
Eisenindustriellen auf, das Verfahren im Groſsen zu versuchen, da Versuche im
Kleinen unausführbar sind.
Die Oesterreichische Zeitschrift für Berg- und
Hüttenwesen, 1883 S. 201 ff. bringt einen Auszug aus dem Berichte des
schwedischen Ingenieurs Erik G. von Odelsterna, welcher
in Oesterreich, Deutschland, Frankreich und England 27 Siemens-Martin- Werke besuchte.Die interessante Anlage (mit zwei Oefen zu 12t,5 Fassungsvermögen) der Südbahn bei Graz nach Plänen des
Direktors Prochaska ist im Engineering, 1883 Bd. 35 S. 102 näher
abgebildet.
Zur Erzeugung des Martin-Metalles werden fast nur Siemens-Oefen angewendet. (Pernot benutzt auf seinem Werke in St. Chamond die nach ihm benannten
Oefen; diese geben aber ein weniger gleichförmiges Product und sind in der
Unterhaltung kostspieliger, wenn sie auch schneller arbeiten.) Das Fassungsvermögen
der Siemens-Oefen schwankt zwischen 2 und 25t; am besten hat sich ein solches von 8t bewährt. Der Fassungsraum des Herdes wird 12 bis
30 Proc. gröſser gemacht als die Post selbst. Die Länge des Herdes soll so gewählt
werden, daſs die Gase Zeit zur vollständigen Verbrennung im Ofen haben und sich die
Flamme nicht bis über die Fuchsbrücke erstreckt. Die Tiefe des Bades richtet sich
nach dem Mischungsverhältnisse von Abfalleisen und Roheisen, in so fern als dadurch
eine geringere oder stärkere Oxydation des Bades bedingt wird; sie schwankt von 25
bis 90cm. Bei der Benutzung von Erzen als Zuschlag
macht man die Oberfläche des Herdes so groſs wie möglich. In der Schlackenlinie
bedeckt man die feuerfesten Steine des Ofens mit einer 5 bis 6cm starken Sandschicht.
Der Ofenboden besteht aus 3 Eisenplatten, wovon die mittlere horizontal, die beiden
Seitenplatten etwas geneigt liegen. Auf diese kommt eine Lage auf die Längskante
gestellter Dinasziegel und hierauf der aus Quarzsand bestehende eigentliche Boden,
welcher entweder aufgestampft, oder aufgeschmolzen (bezieh. aufgesintert) wird. An
der schwächsten Stelle, d. i. an der Abstichöffnung, soll der Boden wenigstens 50cm stark sein. Die Feuerbrücken, welche am besten
ebenfalls von frei liegenden Platten getragen werden, um ein Durchfressen des
Stahles sofort bemerken zu können, müssen so lang hergestellt werden, daſs alle von
der Flamme mitgerissenen Schlackentheile auf ihnen niederfallen und wieder in den
Herd zurücklaufen können. Die Anordnung der Gaskanäle ist eine sehr verschiedene; es
mischen sich Gas und Luft entweder in den Kanälen selbst, oder im Ofeninneren. Am
besten sollen die Feuerbrücken sein, bei denen die 5 oder 7 Kanäle in gleicher Höhe
liegen; dabei nimmt man für die Luft immer einen Kanal mehr als für das Gas.
Gewöhnlich sind die Oefen als Zugöfen ausgeführt; dabei gilt als Regel, daſs der
Querschnitt aller Gasöffnungen um ⅓ gröſser als die offene Rostfläche und die
Luftöffnungen um die Hälfte gröſser als erstere zu machen sind. (In Schweden werden
die Oefen durch Gebläseluft gespeist.) Die Regeneratorkammern sind meist unter den
Oefen angebracht. Mit Ausnahme von Witkowitz, welches nur die Luft vorwärmt,
besitzen die übrigen Werke Regeneratoren für Luft und Gas.
Statt der in der Mitte tief herabhängenden Ofengewölbe werden stellenweise auch
Kuppelgewölbe angewendet, von denen der Herdraum, die Feuerbrücken und Regeneratoren
je eines besitzen. Sie sollen haltbarer sein als erstere und so dünn als möglich
hergestellt werden. Die Seitenwände besitzen 1 bis 3 Oeffnungen zum Beschicken und
Instandhalten des Herdes und sind gewöhnlich 1 bis 2 Ziegellängen dick.
Das deutsche Patent Nr. 21220 vom 28. März 1882 von Ch. W.
Siemens in London (vgl. 1881 242 * 123. 1880 235 * 369) betrifft die Herstellung von Ausbauchungen im Inneren von Drehöfen behufs Klumpen-
bezieh. Luppenbildung. Die Ausbauchungen können durch Einbettung von Kühlröhren und
Kühlkegeln in das Herdmaterial hergestellt werden. Auf diesen gekühlten Stellen
setzen sich dann Schlacken und andere schmelzende Materialien ab. Die Röhren können
parallel der Drehachse liegen und mit oder ohne Ausbiegungen versehen sein. Den in
das Herdmaterial eingebetteten Kegeln kann das Wasser frei zuflieſsen und an den
Wänden des Ofens abtropfen, oder es kann den Kegeln unter Druck zu- und abgeführt
werden. Die Verbindung der Wasserkühlröhren mit der Hauptwasserleitung findet in der
Achse des Ofens in bekannter Weise statt.
Nach dem englischen Patente (Nr. 3545 vom J. 1882) von J.
Gjers in Middlesborough können die bekannten Durchweichungsgruben (vgl. 1882 246 * 508. 1883
247 429. 248 173. * D. R.
P. Kl. 31 Nr. 21716 vom 9. Mai 1882) auch auf fahrbaren
Wagen angeordnet werden. Wie Fig. 6 Taf.
31 erkennen läſst, befinden sich die zur Aufnahme je eines Blockes bestimmten
Schächte in einem Mauerkörper aus feuerfestem Materiale, welcher von einem
schmiedeisernen Mantel eingeschlossen ist. Um eine Ausdehnung des Mauerköpers zu
gestatten, ist zwischen ihm und dem Mantel ein Hohlraum gelassen, welcher mit irgend
einem die Wärme schlecht leitenden Materiale ausgefüllt ist. Der Mantel ruht auf
einem fahrbaren Wagengestelle. Der Boden der Blockschächte wird mit Sand bedeckt und
die oberen Oeffnungen derselben werden mit feuersicheren Deckeln in bekannter Weise
geschlossen. In einem Mauerkörper können je nach der Gröſse ein oder mehrere (bis zu
8) Guſsblöcke untergebracht werden.
Man kann die Blockschächte auch horizontal in feststehenden Mauerkörpern anbringen (vgl. Fig. 8 Taf.
31). Die Einbringung der Guſsblöcke erfolgt dann gerade wie bei den Schweiſsöfen. In
diesem Falle sind die seitlichen Oeffnungen durch nach unten herabklappbare Thüren
abschlieſsbar. Derartige Gruben kann man für einen fortgesetzten Betrieb dadurch
einrichten, daſs man am Boden derselben, senkrecht zur Längsachse, Laufrollen
anordnet, welche alle durch eine Treib welle und entsprechende Kegelgetriebe in
gleicher Richtung umgedreht werden (vgl. Fig. 7).
Denkt man sich einen solchen Durchweichungskanal zwischen der Gieſsgrube und dem
Walzwerke einer Bessemeranlage eingeschaltet, so würde sich der Betrieb derselben
ungefähr folgendermaſsen gestalten: Nachdem die Blöcke gegossen und genügend
erkaltet sind, um sie aus den Formen entfernen zu können, werden sie mittels eines
Krahnes durch eine Endöffnung des Durchweichungskanales in letzteren hineingelassen
und auf die Rollen gelegt; diese befördern dann die Blöcke je nach ihrer
Geschwindigkeit in entsprechender Zeit bis zum anderen Ende des Kanales. Hier werden
die Blöcke durch einen zweiten Krahn herausgehoben und direkt dem Walzwerke
übergeben. Man sieht, daſs man die Dauer des Aufenthaltes der Blöcke in dem
Wärmekanale beliebig verändern kann, und man muſs zur Erzielung einer gleichmäſsigen
Temperaturvertheilung nur mit folgenden Gröſsen rechnen: Länge des Kanales,
Umdrehungsgeschwindigkeit der Laufrollen und die Schnelligkeit bei der Herstellung
der Blöcke. Ist letztere groſs, so muſs der Kanal lang und die
Umdrehungsgeschwindigkeit der Rollen auch groſs sein.
Nach dem Engineering and Mining Journal, 1883 Bd. 35 S.
90 ist in Amerika ein Verfahren bekannt geworden, welches der Gjers'schen Wärme-Ausgleichung den Rang ablaufen soll. Es wird in dem Bessemerwerke
der Pittsburg Steel Casting Company ausgeführt, welches
von W. Hainsworth gebaut ist. Dort wird weniger Gewicht
auf eine Massenherstellung einer Sorte von Stahl (z.B. Schienen) gelegt, als auf die
Herstellung von Stahl in verschiedenen Qualitäten und Formen. Die Birne hat deshalb
nur ein Fassungsvermögen von 5t. Um eine innige
Mischung des Spiegeleisens mit dem Stahle in der Birne zu erzielen, wird nach Beendigung des Blasens
eine Rührkrücke in die Birne eingeführt. Nachdem die Blöcke gegossen sind, werden
sie, bis sie zwischen die Walzen kommen, in einer aufrechten Stellung gehalten. Nach Hainsworth's Ansicht soll hierdurch eine Bildung von Hohlräumen im Blocke
vermieden werden. In dieser Stellung werden die Blöcke in mit feuerfesten Steinen
ausgemauerte Gruben gebracht, welche etwa 1m,83
tief, am Boden 1m,06 und oben 0m,91 im Quadrate haben. 5 solcher Gruben liegen
neben einander und stehen an beiden Seiten mit 2 Siemens'schen Regeneratoren in Verbindung, welche von 2 Generatoren
gespeist werden. In jede der 5 Gruben werden, nachdem sie mit einer nicht
oxydirenden Gasatmosphäre gefüllt und auf etwa 1100° erhitzt sind, 4 Blöcke in
aufrechter Stellung von 1 bis 1t,5 Gewicht und in
dunkel- bis mittelroth warmem Zustande eingesetzt. Nach einigen Minuten sind die
Blöcke auſsen fast gelbwarm geworden, während der Kern derselben fest ist und
ungefähr dieselbe Temperatur angenommen hat wie die Oberfläche, so daſs der Block in
dem für die Streckung günstigsten Zustande zwischen die Walzen gelangen kann. Nach
Hainsworth's Ansicht ist es nur so möglich, einen
groſsen Block in einer Hitze zu einer Schiene mit dünnerem Fuſse auszuwalzen. An
Brennmaterial soll die Anlage, wenn sie einmal in Betrieb ist, nicht mehr als 50k auf 1t Stahl
gebrauchen, weil die Ofenklappen während des Einsatzes geschlossen werden können und
den Gruben nur das nöthige Gas zur Bildung einer nicht oxydirenden Luft zugeführt zu
werden braucht. 5 Gruben sollen die Leistung eines Werkes mit 3 Birnen vollauf
bewältigen können. In dem genannten Werke genügt 1 Grube für 60t Stahl, welche in 8 Stunden hergestellt
werden.
Was an dieser Sache ist, kann man nicht recht übersehen. Das geniale Gepräge, welches
die Gjers'sche Erfindung trägt, indem sie gar keines Brennstoffes bedarf, besitzt jene nicht; es
ist aber doch noch fraglich, ob die Verbindung der Wärmegruben mit Feuerungen, wenn
auch nicht gerade Regeneratorfeuerungen, sich bei weiteren Versuchen nicht als
praktischer erweist. (Vgl. Tunner 1882 246 512.)
E. F. Göransson in Stockholm (* D. R. P. Nr. 22172 vom
31. Oktober 1882) kühlt den Gebläsewind, bevor er
denselben in die Verbrennungsöfen einführt, durch den Oberflächen-Condensatoren
gleichende Apparate ab. Hauptzweck des Verfahrens soll eine Erhöhung des
Sauerstoffgehaltes in der dichteren kalten Luft sein. Erfinder verspricht sich
besonders gute Resultate bei der Anwendung seines Verfahrens auf den
Bessemerprozeſs.
J. Mannstaed in Kalk bei Köln (* D. R. P. Nr. 22277 vom
4. Juli 1882) legt den Vorwärmer seines Puddelofens neben die Generatorfeuerung auf die Seite
der Arbeitsöffnungen, so daſs ein Theil der im Generator erzeugten Gase durch den
Vorwärmer streichen muſs, ehe er in den Ofenherd gelangt. Nähere Angaben über die
Einrichtung der Feuerung sind in der Patentschrift nicht gemacht.
Im Iron, 1883 Bd. 21 S. 494 wird über einen rotirenden Puddelofen berichtet, welcher als
Brennmaterial Erdöl verwendet und von G. Duryee aus
New-York construirt ist. Der rotirende Ofenkörper, welcher von einem Eisenmantel mit
feuerfester Ausmauerung gebildet wird, besitzt zwei gröſsere Abtheilungen A und B (Fig. 1 Taf.
31) zur Bildung der Luppen und einen langen Kanal C
behufs Reduction und Kohlung der mit Fluſsmitteln vermischten Erze. Die ganze Länge
dieser 3 Theile beträgt 36m,5. Der Ofenkörper ruht
auf Rollen und erhält seine Drehung in bekannter Weise. In dem vorderen Theile
mündet der schräge Kanal D, welcher den Rostraum E mit A verbindet. In E münden das Erdölzuführungsrohr F, die Begichtungsvorrichtung G zur Einleitung von Kohlenstoff und die beiden Winddüsen H und J, welche von dem in
dem Rauchabzugskanale des Ofens liegenden Rohre K aus
gespeist werden. Das Rohr N dient zur Ansaugung des
Erdöles durch das Rohr M. P bezeichnet die
Entleerungsöffnung des Ofens, welche durch die mit Wasser gekühlte Thüre Q geschlossen werden kann, O den Beschickungstrichter, durch welchen die Erze, mit fein zertheiltem
Kohlenstoffe (z.B. Ruſs) und Fluſsmitteln vermischt, dem Ofen zugeführt werden
sollen. Die Erze werden reducirt, die Verunreinigungen verschlackt und das reducirte
und gleichzeitig gekohlte Eisen in den Abtheilungen A
und B durch den überschüssigen Sauerstoff der
Erdölflamme auf den gewünschten Kohlenstoffgehalt gebracht. Der Rost in dem Räume
E dient zur Unterhaltung der Flamme.
Zur Gewinnung des Phosphors aus Phosphor haltigen
Metallschlacken schlägt G. Rocour in Lüttich
(D. R. P. Nr. 21240 vom 28. Januar 1882) folgendes Verfahren vor: Die Phosphor
haltigen Schlacken werden zuerst einem reducirenden Schmelzen in einem Schachtofen
unterworfen. Behufs vollständiger Zersetzung des phosphorsauren Kalkes empfiehlt
sich ein Kieselsäuregehalt der Schlacke von 30 bis 40 Proc. Ist dieser nicht schon
an und für sich vorhanden, wie dies bei den basischen Schlacken des
Bessemerprozesses gewöhnlich der Fall sein dürfte, so schlägt man entsprechende
Mengen Puddelofenschlacken zu. Um die Reduction der Phosphorsäure und der
Metalloxyde zu begünstigen, müssen die Schlacken in möglichst kleinen Stücken
aufgegeben und muſs die Temperatur des Schachtofens möglichst hoch gehalten werden.
Das Product dieses Schmelzens ist je nach Umständen eine stark Phosphor haltige
Phosphormetall-Legirung, welche am besten in Wasser abgestochen wird. Die so
erhaltenen Granalien werden sodann unter Druck- und Temperaturerhöhung in
widerstandsfähigen Behältern mit Schwefelsäure oder Salzsäure behandelt, wobei eine
Zersetzung der Phosphormetalle unter Entwickelung von Wasserstoff und
Phosphorwasserstoff stattfindet, welche Gase durch ein Rohr nach einer Anzahl von
Brennern geleitet werden, um einen kleinen Flammofen zu erwärmen. Die Wasserstoff-
und Phosphorwasserstoffgase bilden bei ihrer Verbrennung Wasserdampf und
Phosphorsäure, welche
nach einem Condensationsapparate geleitet werden. Hier sammelt sich die
Phosphorsäure als wässerige Lösung an, welche abgezapft und durch Eindampfen
concentrirt werden kann. Bei der Zersetzung der Phosphormetalle durch die Säuren
bildet sich eine Lösung von Eisen- und Manganchlorür oder Eisen- und Manganvitriol,
welche mehr oder weniger rein ist und Phosphor als saures Phosphat in mehr oder
weniger groſser Menge enthält. Ist die Lösung durch Salzsäure hergestellt worden, so
kann man die gleichzeitige oder getrennte Ausfällung des Eisens und Mangans als Oxyd
direkt durch Hinzufügung von Kalk im Ueberschusse oder aber durch eine titrirte
Menge kohlensauren Kalkes nach bekannten Verfahren bewirken. Statt des Kalkes kann
man auch fein pulverisirte Schlacken des basischen Frischprozesses, welche einen
Ueberschuſs an Kalk enthalten, benutzen. In diesem Falle treten die Eisen- und
Manganoxyde und die Phosphorsäuren dieser Schlacken zu dem Oxyde und phosphorsauren
Eisenniederschlage hinzu und vermindern so die Kosten der Concentration eines
entsprechenden Phosphormetalles. Die Phosphorsäure schlägt sich als basisch
phosphorsaures Eisen neben Eisenoxyd nieder. Um beide Producte zu trennen, mischt
man den Niederschlag mit schwefelsaurem Kali und calcinirt. Es bildet sich dann
phosphorsaures Kali, welches sich in Wasser löst. Setzt man hierzu Kalk, so bildet
sich phosphorsaurer Kalk.
Textabbildung Bd. 249, S. 446
Nach dem Engineering and Mining Journal, 1883 Bd. 35 S.
190 hat man in einer amerikanischen chemischen Fabrik Krigar'sche Kupolöfen mit einem fahrbaren Sammelherde gebaut. Dieselben
dienen hauptsächlich zur Verschmelzung der Röstrückstände von Eisen und Kupfer
haltigen Pyritabbränden. Der Anwendung der Kupolöfen zu anderen Zwecken, als der
Umschmelzung von Roh- und Guſseisen, steht nichts entgegen. Der Sammelherd ist in
einen cubischen Kasten aus Schmiedeisen eingebaut und besitzt einen Abstich und ein
Schlackenloch. Die Verbindung des Kastens mit dem Ofenmantel wird, wie nebenstehend
veranschaulicht ist, durch an beiden Theilen befestigte gekühlte Ringe
bewerkstelligt, welche, nachdem sie an einander geschoben und verbunden sind,
verschmiert werden.
Eine von G. Winter in Laufach (* D. R. P. Nr. 22436 vom
1. August 1882) angegebene Vorrichtung bezweckt eine Vorwärmung der Böden von Kupolöfen, um auch den ersten Abstich sofort für
die feinsten Güsse verwenden zu können. Zu diesem Zwecke werden dicht über dem
Ofenboden in den Mantel sechs radiale Oeffnungen a
(Fig. 2 Taf. 31) und an der Gichtöffnung ein guſseiserner Schieber c angeordnet. Das Anfeuern des Ofens geschieht wie
gewöhnlich. Ist derselbe in gehöriger Glut, so rückt man den Schieber c in den Ofen hinein und schlieſst die seitlichen Fugen
durch Lehmverschläge. Läſst man nun das Gebläse mit voller Kraft arbeiten, so
werden die Verbrennungsgase gezwungen, durch die Oeffnungen a auszutreten. Der Boden wird hierdurch schnell vorgewärmt und kann, wenn
dies geschehen, der Schieber c zurückgezogen werden, um
dann den Betrieb des Ofens in bekannter Weise weiterzuführen.
Um eine noch schnellere und vollständigere Reduction des
Eisenerzes bei Herstellung des Eisens auf direktem Wege zu erzielen, formt
Ph. S. Justice in London (* D. R. P. Nr. 22013 vom
9. September 1882, vgl. 1881 242 290 u. 1882 246 144) die einzelnen Kuchen, welche aus einer Mischung
von Erz, Kohle und Fluſsmitteln bestehen, in der in Fig. 5 Taf.
31 dargestellten Weise, so daſs 2 Paar gegenüber liegende Flächen durch Kanäle mit
einander verbunden sind, welche zwischen sich Wände von 25 bis 38mm Stärke stehen lassen. Die Kuchen sind 40 bis
45cm hoch und 20 bis 21cm breit. Die Rinnen am Boden der Kuchen dienen
zum Einführen derselben in den Ofen mittels Gabeln. Die Kuchen werden in
hydraulischen Pressen hergestellt.
F. R. Asthöwer und Comp. in Annen (* D. R. P. Nr. 22260
vom 4. November 1882) lieſsen sich eine Wendevorrichtung für
Walzwerke mit hinter statt neben einander liegenden horizontalen
Walzenpaaren patentiren. Dieselbe besteht aus zwei kleinen vertikalen, hinter dem
Walzenpaare auf einer Schiene c (Fig. 9 bis
11 Taf. 31) angeordneten Walzen a und a1 bezieh. b und b1 deren Mantelflächen bei rectangulärem Kaliber der
Walzen einfach conisch, bei Ovalkalibern geschweift conisch ausgebildet sind. Der
Stab wird dem ersten Walzenpaar in bekannter Weise zugeführt und gelangt aus diesem
sofort zwischen die Wendewalzen. Diese geben den Stab, um seine Längsachse gedreht,
an einen vor dem nächsten Walzenpaare stehenden Trichter e ab, dessen Mündung dem Querschnitte des Stabes entspricht. Durch den
Trichter gelangt der Stab sodann zwischen das zweite Walzenpaar. Da von den beiden
Wendewalzen die eine ihre Spitze nach unten, die andere dieselbe nach oben kehrt, so
ist die Conicität der Walzen und ihre Entfernung von dem Hauptwalzenpaare bestimmend
für das Maſs der Drehung des durch die Wendewalzen gehenden Stabes. Geht der Stab
von einem Ovalkaliber in ein Vierkant- oder ein Rundkaliber des nächsten
Walzenpaares über, so muſs eine Verdrehung um einen rechten Winkel erfolgen.
Zur Einstellung der Walzen von Blech- und
Universaleisen-Straſsen ordnet R. M. Daelen
(Stahl und Eisen, 1883 S. 335) eine
Zwillingsdampfmaschine direkt auf einer der Einstellschrauben an. Die oberen Enden
der Einstellschrauben A (Fig. 3 und
4 Taf. 31) sind ausgehöhlt und tragen mittels conischer Zapfen ein Bett
F. In diesem ist die horizontale, über einer
Schraube doppelt gekröpfte Welle E gelagert. Ueber der
betreffenden Schraube ist auf dem Bette F eine
Zwillingsmaschine angebracht, deren Kolbenstangen an die Kurbeln der Welle E angreifen. Die oscillirenden Cylinder der Maschine
sind mit einer der bekannten Hahnsteuerungen versehen, welche den Anforderungen eines
nur zeitweisen Betriebes vollauf entspricht. Die Umsteuerung der Drehungsrichtung
geschieht durch den Muschelschieber G, welcher mittels
eines Handhebels bewegt wird und abwechselnd die Rohre J und K mit dem Dampfzufluſs- und
Abfluſsrohre in Verbindung setzt, während in der mittleren Stellung die Absperrung
erfolgt. Die Dampfrohre sind mit Stopfbüchsen versehen, um die auf- und
niedergehende Bewegung und beim Auswechseln der Walzen das Abheben der Maschine mit
dem Bette F und der Welle E zu gestatten. Auf letzterer sitzen auf derselben Seite der
Einstellschrauben zwei Kegelräder, die in entsprechende Räder der Schrauben
eingreifen. Um die Stellung der beiden Schrauben zu einander und damit die Lage der
Oberwalze zur Horizontalen leicht regeln zu können, ist das eine Kegelrad mit einer
Bremskuppelung und die Welle E mit einem Handrade
versehen, so daſs man nach Lösung der ersteren die Welle E ohne Mitwirkung der Maschine drehen kann. Die Geschwindigkeit der
Maschine kann ohne Bedenken bis auf 360 Umdrehungen in der Minute steigen, so daſs
bei einer Räderübersetzung von 1 : 3 die Einstellschrauben 120 Umdrehungen machen
und bei einer Steigung der Schrauben von 20mm die
Oberwalze um 40mm in der Sekunde gehoben oder
gesenkt werden kann. Um dem Arbeiter, welcher das Einstellen der Oberwalze bewirkt,
den Stand der Walze direkt anzuzeigen, ist es zweckmäſsig, an der Walze einen Zeiger
anzubringen, welcher auf einer am Walzenständer befestigten Skala einspielt.
Bei Panzerblechstraſsen, bei welchen der Hub der
Oberwalze bis zu 800mm beträgt, gleicht man jetzt
vielfach das Gewicht der Oberwalze statt durch Hebelgewichte durch hydraulischen
Druck aus, indem unter die Walze angreifende hydraulische Kolben unter der Pressung
einer bestimmten Wassersäule stehen.
Die New-Yorker Eisen- und Metallbörse schlägt im Iron
Age folgende Classification von gebrauchtem altem
Eisen vor: Nr. 1 soll bestehen aus allem bearbeiteten Eisen, Bleche
ausgenommen, diese nur, wenn besonders geschnitten und frei von Winkeln und Nieten;
Eisen von ¼ Zoll engl. und mehr, rund oder 4 kantig, aber nicht, wenn es solche
auſsergewöhnlichen Maſse oder Profile hat, welche nicht auf übliche Methode
hergestellt werden können, – frei von Schienen, Schienenenden, Nägeln, Ambossen,
Hacken, Schaufeln, Gasröhren, Kaminröhren, Ofenröhren, Dünnblech, Reifeisen, Draht
und ähnlichem leichtem Eisen, Guſs-, schmiedbarem Guſs-, galvanisirtem, verzinntem
oder verkupfertem Eisen, Zink, Stahl oder anderen fremden Substanzen, ebenso von
verbranntem oder sehr stark verrostetem Eisen. – Nr. 2 kann bestehen aus schweren
Stücken, wie groſse Anker, Schiffsarmaturplatten, Schiffsknie, Kurbelwellen, schwere
Radwellen, Träger, Winkel oder nicht auf gewöhnliche Methode hergestellte,
auſsergewöhnliche Abmessungen besitzende Gegenstände. – Nr. 3 kann bestehen aus
bearbeitetem Eisen, welches nicht unter Nr. 1 und 2 gebracht werden kann, aber frei sein muſs von
Ambossen, Schienen, Schienenenden, Guſs-, schmiedbarem Guſs-, galvanisirtem,
verzinntem oder verkupfertem Eisen, Zink, Stahl oder anderen Substanzen.
Nach einem im Iron, 1882 Bd. 20 S. 533 abgedruckten
Berichte des Direktoriums der American Iron and Steel
Association vom 25. Juli 1882 hat sich die Zahl und
Leistung der amerikanischen Bessemerwerke gegen das J. 1880 ganz bedeutend
vergröſsert.Die Tonnen sind in englischen Einheiten ausgedrückt (vgl. 1882 246 394), trotzdem aber kurz mit „t“
bezeichnet.Red.
Während am 15. März 1880 11 Bessemerwerke mit 22 Birnen von
zusammen 138t Inhalt in Betrieb waren und
dieselben im Durchschnitte jährlich 1250000 Nettotonnen, jede Birne dagegen 56818t Stahl erzeugten, war am 15. Juli 1882 die Zahl
der Bessemerwerke auf 14, die der Birnen auf 36, der Inhalt der letzteren auf 254t, die durchschnittliche jährliche Erzeugung der
Werke auf 2150000t und die einer Birne auf
59722t gestiegen. Man sieht aus diesen Zahlen,
daſs der Gesammtinhalt der Birnen im gleichen Verhältnisse mit deren Zahl gewachsen,
daſs dagegen die jährliche Leistung einer Birne nicht viel höher gestiegen ist,
trotzdem die Gesammtleistung aller Werke fast die doppelte Höhe erreicht hat. Es mag
dies darin seinen Grund haben, daſs das Product aus der Zahl der Birnen eines Werkes
und dem Inhalte einer Birne keinen Maſsstab für die Leistung eines Werkes gibt. Es
erzeugen z.B. drei 10t-Birnen nicht doppelt so
viel wie zwei 7t Birnen, weil in dem Werke mit 3
Birnen an einer Grube jede derselben längere Zeit auſser Thätigkeit bleibt als dort,
wo 2 Birnen sind. In Folge dessen wird sich auch die Zahl der Hitzen in beiden
Werken gleich bleiben. Als Beispiel hierfür dienen englische Werke mit 4 Birnen an
einer Grube, welche nicht mehr Stahl erzeugen als amerikanische Werke mit 2
Birnen.
Die groſse Productionserhöhung der Werke um 72 Proc. wirft aber
die Frage auf, ob dieselbe berechtigt und ob in der Zukunft ein genügender Absatz
für den hergestellten Stahl vorhanden ist. Eine Erniedrigung des Verkaufspreises des
Stahles um 25 Proc. läſst darauf schlieſsen, daſs es den Werken schon schwerer wird,
ihr Fabrikat unterzubringen. So betrug der Preis für 1t Stahlschienen im Januar 1882 in Philadelphia 243 M., im Oktober dagegen
nur 189 M. Trotzdem kauften die Abnehmer nicht sofort, theils weil sich eine Abnahme
im Bahnbaue bemerkbar machte, theils weil sie ungern abschlössen, während die Preise
im Sinken begriffen waren. Und während es vor einigen Jahren der Stolz der Werke
war, sagen zu können, sie hätten schon ihre Production auf 1 bis 1½ Jahre hinaus
verkauft, müssen sie jetzt suchen, Aufträge zu erhalten, um im Betriebe bleiben zu
können. Es wird ihnen deshalb für die Zukunft nichts Anderes übrig bleiben, als ihre
Production einzuschränken oder neue Absatzgebiete zu suchen. Da aber eine
Einschränkung der Leistung gleichbedeutend ist mit geringerem Verdienste, nicht
allein wegen der weniger erzeugten Tonnen Stahl, sondern auch wegen der sich auf
weniger Tonnen Stahl vertheilenden, auf gleicher Höhe bleibenden Generalunkosten, so
werden sich die Werke nur schwer dazu verstehen, sondern Gelegenheit suchen, ihr
Absatzgebiet zu erweitern. Daſs die Werke schon solche Gelegenheit gefunden haben,
geht aus den Verkaufspreisen der Fluſsstahlschienen und von Stabeisen hervor.
Während im Juli 1880 1t Stahl mehr als 50 M.
theurer war als 1t Eisen, kostete im Oktober 1882
1t Stabeisen 235 M., 1t Stahlschienen dagegen 189 M. Es ist also jetzt
der Stahl billiger als je zuvor und wenn je, so ist jetzt der Zeitpunkt gekommen, um
Eisen durch Stahl zu ersetzen. Dazu gehört aber vor Allem, daſs sich die
Bessemerwerke darauf einrichten, neben Stahlschienen auch Profilstahl in ebenso
vollendeter Güte wie erstere und billiger als gepuddeltes Baueisen herzustellen;
dies konnten sie aber bis jetzt nicht, trotzdem die Stahlblöcke billiger als die
Eisenluppen standen, theils weil die Walzenstraſsen nicht stark genug waren, theils
weil die Arbeiter das Walzen von Stahl nicht kannten, oder endlich, weil die
Einrichtungen nicht für eine Massenproduction genügten. Neben Profilstahl müssen
sich die Bessemerwerke noch auf die Herstellung von Blechen, Achsen, Wellen,
Kleineisenzeug werfen, von welcher Form es auch immer, ob gestanzt, gepreſst oder
geschmiedet, sei. Daſs dies aber möglich ist, beweist die massenhafte Herstellung
von Stahlzaundraht, welcher ebenso billig, ja noch billiger als Eisendraht
hergestellt werden kann, wenn er in groſsen Massen in einer Sorte verlangt wird.
Handeln die Werke hiernach, so ist es nur eine Frage der Zeit, wann das Eisen
vollständig vom Stahle verdrängt sein wird.
Letzteren Rath können die deutschen Stahlwerke ebenso beherzigen wie die
amerikanischen; auch in Deutschland findet eine Ueberproduction von Bessemerstahl
statt, welcher nach irgend einer Seite Luft geschafft werden muſs, wenn nicht eine
zeitweise Einstellung des Betriebes vieler Werke eintreten soll.
St.
Tafeln
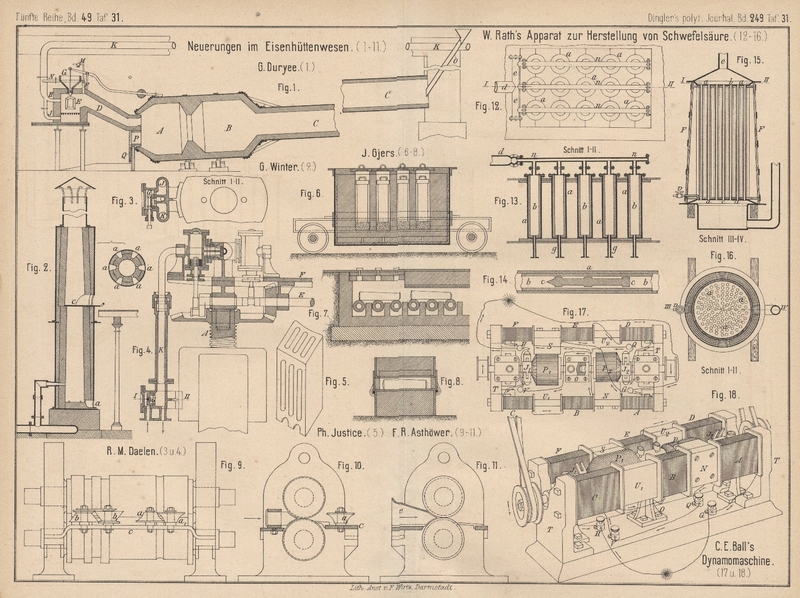