Titel: | Betriebsergebnisse der Stahlöfen des Grazer Südbahn-Walzwerkes; von J. Prochaska. |
Fundstelle: | Band 250, Jahrgang 1883, S. 213 |
Download: | XML |
Betriebsergebnisse der Stahlöfen des Grazer
Südbahn-Walzwerkes; von J.
Prochaska.
Mit Abbildungen auf Tafel 16.
Betriebsergebnisse der Stahlöfen des Grazer
Südbahn-Walzwerkes.
In der Oesterreichischen Zeitschrift für Berg- und
Hüttenwesen, 1883 S. 475 theilt Hüttendirektor Julius Prochaska in Graz
Betriebsresultate der von ihm gebauten Siemens-Martin-Stahlöfen (vgl. 1883 249 441) mit.
Diese Oefen zeichnen sich, wie z. Th. auch aus den dem Engineering, 1883
Bd. 36 S. 102 entnommenen Abbildungen Fig. 1 und
2 Taf. 16 hervorgeht, gegenüber älteren Ausführungen durch die
Hinweglassung des Siemens'schen Syphons zur Ansaugung
der Generatorgase, durch die Anordnung horizontaler, vor dem Ofen liegender
Regeneratoren, sowie durch die einfache Mischung von Luft und Gas aus, welche beide
nur je in einem Kanäle zum Ofen aufsteigen und durch kurze, fallende und gegen
einander convergirende Mündungen von vierseitigem Querschnitte direkt auf das
Stahlbad geleitet werden; endlich erhält auch das Gewölbe über dem Herde eine stark
convexe statt der üblichen concaven Form. Solche Oefen sind nun auf dem Grazer Südbahn-Walzwerke seit 5 Jahren im Betriebe
gewesen, so daſs sich wohl aus den erhaltenen Betriebsresultaten ein Vergleich mit
anderen Ofenconstructionen ziehen läſst. Jeder der beiden nach Prochaska's Systeme gebauten Oefen hat einen
Fassungsraum von 12500k. Bei einer jeden Hitze
wird das Bad bis auf 0,12 bis 0,14 Proc. Kohlenstoff entkohlt, worauf dann eine
Rückkohlung durch Ferromangan erfolgt.
Der Ofen Nr. 1 machte in der letzten Betriebsepoche 431 Beschickungen vom 27.
September 1882 bis zum 4. Mai 1883, während der Ofen Nr. 2 539 Beschickungen vom 30.
August 1882 bis zum 2. Juni 1883 erzielte. Die Oefen waren daher über 8 bezieh. 9
Monate unausgesetzt im Betriebe, ohne daſs Ausbesserungen am Ofengemäuer
erforderlich geworden wären. Die einzigen Unterbrechungen des Betriebes wurden durch
das Reinigen der Gasventile bei den Generatoren veranlaſst, was nach ungefähr je
einem Monate erforderlich wurde und 3 bis 6 Stunden dauerte.
Während der erwähnten Ofenbetriebe haben beide Oefen verbraucht:
An weiſsem Roheisen
2452300k
„ grauem „
1358300
–––––––––
zusammen
3810600k
An Alteisen und Bruchstahl
8403630
„ Ferromangan
204460
–––––––––
Im Ganzen an Eisenmaterial
12418690k
An Schmelzkohle (Leobener Mittelkohle)
5060000k
Wärmkohle (Köflacher Lignit)
3023400k
Dabei betrug die Erzeugung beider Oefen an
Stahlblöcken
11714458k
Es wurden daher auf je 100k Stahl verbraucht:
An Roheisen
32,53k
„ Alteisen und Bruchstahl
71,73
„ Ferromangan
1,74
–––––––
Im Ganzen an Eisenmaterial
106,00k
An Schmelzkohle
43,19k
„ Wärmkohle
25,80
Nach Abzug der Stillstände beim Reinigen der Ventile sowie an
Festtagen vertheilt sich dieses Ausbringen von 11714458k Stahlblöcken auf 488 Arbeitstage. Es entfällt daher für jeden Ofen und
für je 24 Stunden ein durchschnittliches Ausbringen von rund 24000k.
Diese Ofenconstruction wurde auch von der Gesellschaft John
Cockerill angenommen, auf deren Werke in Seraing Direktor Prochaska im Laufe dieses Sommers einen Ofen von
15000k Einsatz gebaut hat.
Zwei andere Stahlöfen von nur 5500k Einsatz, welche
vertikale Regeneratoren besitzen, dabei aber mit der gleichen Gas- und Luftführung,
sowie mit derselben Gewölbeanordnung versehen sind wie die vorhin beschriebenen zwei
gröſseren Oefen, wiesen einen viel höheren Kohlenverbrauch auf. Einer derselben, der
Ofen Nr. 3, war vom 24. März bis zum 22. December 1882 unausgesetzt im Betriebe und
erzielte 583 Beschickungen ohne jegliche Ausbesserung. Der Ofen Nr. 4 bestand vom
24. September 1882 bis zum 24. März 1883 497 Hitzen, ohne daſs eine Nachbesserung
erforderlich gewesen wäre. Das Ausbringen dieser beiden Oefen betrug während der
angegebenen Zeit von 360 Arbeitstagen 5400204k
Stahlblöcke, daher auf jeden Ofen und 24 Stunden berechnet 15000k Stahl im Mittel. Der Kohlenverbrauch stellte
sich dabei für je 100k Ausbringen auf 68k Schmelzkohle und 20k Wärmkohle.
Es wurde in der Hütte auch ziemlich viel Stahlguſs
hergestellt, als Kreuzungen, sodann Kuppelungsgetriebe, Walzen, Abstreifmeiſsel,
Walzentische, Thüren u. dgl. für den Walzwerk- und Stahlofenbetrieb. Hier war vor
Allem auf dichten Guſs und eine reine glatte Oberfläche Bedacht zu nehmen. Zur
Erreichung der ersteren Eigenschaft erwies sich der Zusatz eines Tiegels
geschmolzenen Ferromangansilicides zu dem in der Guſspfanne befindlichen Stahle als
vortheilhaft. Die Menge des Zusatzes richtete sich nach der dem Stahle zu
ertheilenden Härte. In den meisten Fällen genügte ein Gehalt von 0,30 bis 0,40 Proc.
Silicium, bei 0,60 bis 1,00 Proc. Mangan und 0,40 bis 0,60 Proc. Kohlenstoff.
Schwieriger war die zweite Bedingung eines vollkommenen Stahlgusses, die reine
glatte Oberfläche, zu erzielen. Als bestes Formmaterial ergab sich nach vielen
Versuchen ganz reiner feuerfester Quarzsand, welchem die nöthige Bindekraft durch
eine Beimengung von ungefähr 12 Proc. Schwarzmehl (Kleie) ertheilt wurde. Diese
Mischung läſst sich sehr gut formen und brennen, wobei das Mehl verkohlt, und die so
entstehende poröse Form läſst die aus dem Stahle sich noch entbindenden Gase leicht
ausströmen. Gegen das Anbrennen wird die fertige Form mit in Leimwasser angerührtem
Kieselguhr leicht
überstrichen, welcher Ueberzug sich als viel besser und feuerfester bewiesen hat als
Graphit.
Tafeln
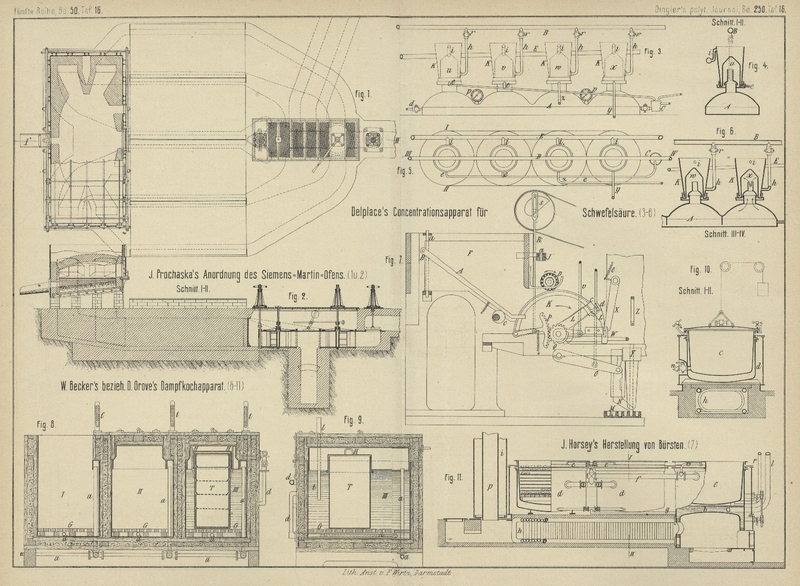