Titel: | Ueber Neuerungen im Eisenhüttenwesen. |
Fundstelle: | Band 255, Jahrgang 1885, S. 375 |
Download: | XML |
Ueber Neuerungen im Eisenhüttenwesen.
(Patentklasse 18. Fortsetzung des Berichtes S. 29
d. Bd.)
Mit Abbildungen im Texte und auf Tafel 27.
Ueber Neuerungen im Eisenhüttenwesen.
Auf der letzten Herbstversammlung zu Chester des Iron and
Steel Institute hielt J. Riley aus Glasgow
einen bemerkenswerthen Vortrag: über neuere Fortschritte im
Herdschmelzprozesse, welcher u.a. im Engineering, 1884 Bd. 38 * S. 316 abgedruckt ist.
Während Mitte der Siebenziger Jahre in den Siemens-Martin'schen Werken lediglich Eisenbahnschienen erzeugt wurden,
ging man allmählich dazu über, auch Qualitätseisen, Bleche, Winkeleisen u.s.w. zum
Baue von Schiffen, Brücken und Kesseln sowie Eisen zur Herstellung des Weiſsbleches,
wozu bis dahin nur bestes Holzkohleneisen verwendet wurde, zu erschmelzen. Dieses
Eisen gelangte bald zu einem solchen Absatze, daſs die Herstellung der
Eisenbahnschienen von den Werken gänzlich eingestellt wurde. Hiermit wuchs auch der Wunsch, Oefen
von gröſserer Fassung als bisher zu verwenden, und so kam man zu Oefen bis zu 12t Inhalt mit einem wöchentlichen Ausbringen von
150 bis 200t Blöcken. Durch das Heruntergehen der
Preise wurde man jedoch zur fortwährenden Erprobung neuer Vorschläge gezwungen,
welche Ersparnisse theils am Materiale, theils an Löhnen durch allerlei
Veränderungen im Betriebe, bezweckten. Bei Gelegenheit des Umbaues der durch die Steel Company of Scotland angekauften Blochairn-Werke
versuchte Riley es mit dem Pernot'schen Ofen (vgl. 1875 217 * 426). Es
wurden 2 derartige 20t-Oefen angelegt und darin
der basische Prozeſs vorgenommen, jedoch mit wenig Erfolg. Dasselbe gilt von mit
basischem Futter ausgekleideten Siemens-Martin'schen
Oefen; man konnte das Futter an der Trennungsfuge zwischen dem basischen und saueren
Mauerwerke nicht erhalten. Endlich baute man 12 Siemens'sche 15t-Oefen. Dabei stellten
sich aber Betriebsschwierigkeiten ein. Man suchte zur Hebung derselben die Blöcke in
einer Hitze zu hämmern; aber vergeblich. Entweder
war der Kern zu weich, so daſs das Metall bei jedem Hammerschlage herausspritzte,
oder die Auſsenseite war so kalt und hart, daſs der Block Risse bekam und ein
fehlerhaftes Blech ergab. Es hatte dies besonders darin seinen Grund, daſs man
meistentheils verhindert war, die Blöcke in noch warmem Zustande in die Wärmöfen zu
bringen. Umstände halber war man nämlich gezwungen, alle 12 Oefen gleichzeitig in
der Sonntag-Nacht zu beschicken. Die Folge davon war, daſs auch alle Oefen
gleichzeitig beendete Abstiche ergaben. Dann waren nicht Wärmöfen genug vorhanden,
um alle Blöcke bewältigen zu können. Man half sich einigermaſsen durch bewegliche
Durchweichungskästen von B. E. Cammel und J. Duffield (vgl. 1881 239
139), welche zwischen den Oefen und den Hämmern hin und her liefen.
Durch alle diese Umstände wurde man zum Umbaue der ganzen Anlage gedrängt und hat
diese nun die in Fig. 7 bis 9 Taf. 27 veranschaulichte
Einrichtung, bei welcher die Hämmer ganz durch Walzen ersetzt sind. In den
Zeichnungen gibt Fig. 7 und 8 den Längenschnitt
bezieh. Grundriſs durch das Werk und Fig. 9 den Querschnitt
durch die Gieſsgrube, parallel der Ofenreihe aus 12 Siemens-Martin'schen Oefen O; letztere
besitzen bis auf den äuſsersten rechten Ofen, welcher 25t Inhalt hat, einen Fassungsraum von 15t. Vor diesen Oefen O liegen 2 Geleise. Auf dem
ersten Geleise a läuft eine kleine Locomotive, der ein
Wagen mit einer Pfanne für Stahl bezieh. einer Form für Schlacken angehängt ist.
Zwischen dem 5. und 6. Ofen ist unmittelbar über dem Geleise a ein eigenartiger hydraulischer Krahn b von
20t Tragkraft angebracht, welchem gerade
gegenüber ein 20t-Gieſskrahn c von gewöhnlicher Bauart, jedoch ohne Einrichtung zum
Heben liegt. Der Gieſskrahn ist nur mit einer hydraulischen Vorrichtung versehen, um
denselben um seine Achse drehen zu können, und besitzt auſserdem an einer Seite
einen Cylinder mit
Tauchkolben, um die Gieſspfanne nach jedem Gusse zur Entfernung aller Schlacke und
zur leichten Umwechselung des Ausgusses kippen zu können. Dieser Krahn ist im
Mittelpunkte einer halbkreisförmigen Gieſsgrube d von
12m,2 (40 Fuſs engl.) Durchmesser und 914mm Tiefe aufgestellt. An passenden Punkten rund um
die Gieſsgrube sind 3 Blockkrahne e angeordnet, deren
jeder 5t zu heben vermag und einen Kreis von 12m Halbmesser beschreibt. Zwischen den Krahnen
liegen zwei Sätze Gjers'scher Durchweichungsgruben f von je 6 Zellen, welche theilweise für Blöcke von
1t,5, theilweise für solche von 3t eingerichtet sind (vgl. 1883 249 * 442. 1884 252 *
251).
Die zwei äuſseren Krahnen setzen die Formen in die Gieſsgrube, streifen dieselben
hernach von den Blöcken ab und legen diese in die Durchweichungsgruben, während der
Mittelkrahn die Blöcke von dort wieder wegnimmt und sie in senkrechter Lage auf den
Kippwagen g legt, welcher sich vor den Zuführungsrollen
h des Blockwalzwerkes i befindet und der mit Cylinder und Kolben versehen ist, um das Umwerfen
der Blöcke herbeizuführen. Indem der Kolben einen Hebel des Wagens faſst, dreht er
denselben um, so daſs der Block leicht und ohne Stoſs auf die Zuführungsrollen zur
Walzenstraſse fällt.
Die Blockstraſse hat hohle Stahlwalzen von 810mm
Durchmesser; das Gewicht der oberen Walze, welche um 356mm verstellbar ist, wird durch hydraulische, unter der Grundplatte
gelegene Cylinder ausgeglichen. Statt die Stellschrauben in gewöhnlicher Weise zu
drehen, erhalten ihre drehbar eingerichteten Lager den Antrieb von einer kleinen
Zwillingsmaschine mittels Schneckenradübersetzung. Zwischen den Zuführungsrollen
sind Hebel zur Handhabung der Blöcke angeordnet, um letztere nach Belieben flach
oder hochkantig vor die Kaliber legen zu können; die Bewegung der Hebelarme
geschieht durch unter den Rollen angebrachte hydraulische Cylinder.
Die Blockstraſse steht unter der Aufsicht eines Mannes, welchem 2 Jungen helfen, von
denen der eine die Stellvorrichtung der Walzen und der andere die Dreh- und
Zuführungsvorrichtungen unter sich hat. Der Antrieb der Straſse geschieht durch eine
Zwillingsmaschine von 914mm Cylinderdurchmesser
und 1219mm Hub und einem Uebersetzungsverhältniſs
von 1 : 2¾. Der Dampfdruck beträgt 6at bei ¾
Füllung. Die Walzen machen 28 Umdrehungen in der Minute und haben eine
Umfangsgeschwindigkeit von ungefähr 1m in der
Secunde.
Eine hydraulische Schere k ist im Baue begriffen, um mit
einem Drucke von 1000t Blöcke von 610mm auf 203mm
Seitenlänge zu zerschneiden. Dieselbe findet hinter der Walzenstraſse Aufstellung
und ist mit Zuführungsrollen versehen, welche die Blöcke von der Walzenstraſse durch
die Schere auf Wagen bringen sollen, die dann zu den Wärmöfen gerollt werden.
Der Betrieb der Anlage ist folgender: Die Schmelzöfen werden in der Sonntag-Nacht in schneller
Aufeinanderfolge beschickt und, sobald der erste davon (etwa nach 12 Stunden) zum
Abstiche fertig ist, fährt die Locomotive den Wagen mit der Pfanne vor den Ofen,
worauf das Bad abgestochen wird. Man läſst hierbei allen Stahl nebst Schlacke in die
Pfanne eintreten, da die Schlacke in die auf dem gleichen Wagen befindliche Form
überlaufen kann- man rettet dadurch den Stahl, den man gewöhnlich noch unten in den
Schlackenläufen vor den Oefen findet, und erhält von Eisen freie Schlacke, so daſs
man der Notwendigkeit, sie aus einander zu brechen, enthoben ist. Nachdem die Pfanne
unter den Krahn b gefahren worden ist, wird dieselbe
emporgehoben, bis zwei Knaggen, die zu beiden Seiten ihrer Gieſsmündung liegen, in
Berührung mit entsprechenden Ansätzen kommen, welche am Krahne b befestigt und so angebracht sind, daſs sie die
Ausguſsöffnung der Pfanne in der gleichen wagerechten Ebene halten, bis ihr ganzer
Inhalt in die zweite Gieſspfanne gegossen ist. Nachdem der Gieſskrahn c in seine Pfanne den ganzen Inhalt der ersten Pfanne
aufgenommen hat, wird derselbe rund über die Formen der Gieſsgrube bewegt und der
Guſs in gewöhnlicher Weise vorgenommen. Das Umgieſsen des Stahles dient
hauptsächlich zur Entgasung und es entfällt dadurch gleichzeitig die Notwendigkeit,
den Gieſskrahn heben zu müssen. Eine schädliche Abkühlung des Stahles hat sich dabei
nicht herausgestellt, trotzdem die Temperatur desselben eine viel geringere ist als
die des Bessemermetalles. Der Rückstand soll sich sogar nach dem neueren Verfahren
vermindert haben. Die Zeit, welche für den Abstich des Ofens, den Umguſs des Stahles
in die zweite Pfanne und für das Vergieſsen in die Formen nöthig ist, beträgt 14 bis
15 Minuten, eine kürzere Zeit, als bei dem früheren Verfahren erforderlich war.
Nachdem die Formen nach dem Gieſsen ungefähr 20 Minuten gestanden haben, werden sie
abgehoben und die Blöcke in die Durchweichungsgruben gestellt, um daselbst ungefähr
55 Minuten zu verbleiben; von dort werden die Blöcke nach dem Walzwerke geschafft
und auf den erforderlichen Querschnitt ausgewalzt, worauf die Schienen passend
zerschnitten und nach den Wärmöfen der Blechstraſsen gebracht werden.
Die bis hierher beschriebenen Arbeiten nehmen im Ganzen 95 Minuten in Anspruch. Die
Anlage hat sich vollkommen bewährt; der ganze Betrieb steht mehr unter Aufsicht und
erfolgen die einzelnen Handhabungen regelmäſsiger. Die Arbeitslöhne sind erheblich
verringert, Brennmaterial wird gespart, der Abbrand hat sich von 2¾ Proc. auf fast
Null ermäſsigt. In den Durchweichungsgruben beträgt derselbe z.B. nur 0,02 Proc. und
dabei werden bessere Blöcke erzielt.
Nach einem von Thomas Gillot vor der American Institution of Civil Engineers gehaltenen
Vortrage: Ueber den basischen Herdschmelzprozeſs werden
nach dem Engineering and Mining Journal, 1884 Bd. 38 *
S. 266Vgl. auch Stahl und Eisen, 1885 * S.
91.
die zu diesem Verfahren
bestimmten Siemens'schen Oefen in folgender Weise
hergerichtet: Die feuerfeste Masse, aus welcher der Herd der Oefen hergestellt wird,
besteht aus 58 Th. Kalk, 24 Th. Magnesia, 8 Th. Kieselsäure, 10 Th. Thonerde und
Eisenoxyd. Diese Materialien werden bei hoher Weiſsglut gebrannt, zerkleinert und in
einer Kollermühle mit heiſsem Theere gemischt. Die Masse wird dann sofort mittels
rothwarmer Keulen auf der eisernen Bodenplatte des Herdes aufgestampft, wobei
hölzerne Pflöcke für die Herstellung des Abstiches und der beiden Schlackenlöcher
eingesetzt werden. Zwischen der basischen Masse und dem sauren Mauerwerke wird eine
Isolirschicht von Magnesia und Bauxit angebracht. Der Ofen wird nun 72 Stunden
gefeuert, so daſs derselbe auf gute Schmelztemperatur kommt, und dann frisch
gebrannter Dolomit im Herde auf dem Boden und an den Wänden ausgebreitet. Dem
Dolomite mischt man nicht mehr als 10 Proc. feuerfeste Steine bei, um einen
derartigen Flüssigkeitsgrad zu erhalten, daſs sich die Herdmassen mit einander
verbinden. Nach dieser Zurichtung wird der Ofen zuerst mit einer Lage frisch
gebrannten Kalksteines beschickt, hierauf das Roheisen und dann die Eisen- und
Stahlabfälle eingelegt. Der Kalkzuschlag, welcher sofort aufgegeben wird, beträgt
1/20 bis 1/10 des
Roheisengewichtes.
In 3 oder 4 Stunden ist von den kalt eingebrachten Massen das Roheisen geschmolzen,
so daſs schon ein Bad entsteht und etwas sehr flüssige Schlacke abgestochen werden
kann. In weiteren 3 Stunden haben sich die Eisenabfälle im Roheisen gelöst, so daſs
weitere Schlackenmengen abgelassen werden können. Ist die Schlacke zu dünnflüssig,
so setzt man Kalkstein oder Eisenerz zu, je nachdem die Menge des Roheisens zum
Abfalleisen groſs oder klein ist. Nachdem die Kochperiode beendet und das Bad gut
durchgerührt ist, wird mit einem Gieſslöffel eine Probe genommen und in eine Form
von etwa 6cm Durchmesser gegossen. Nach dem
Erkalten wird der kleine Block auf 1cm Dicke glatt
geschlagen, abgekühlt und in bekannter Weise gebogen und gebrochen. Hat das
Metallbad die gewünschte Zusammensetzung, so gieſst man die Schlacke vollends ab,
was, da sie in dieser Periode gewöhnlich zu strengflüssig ist, durch die mittlere
etwa 10cm tiefer liegende Arbeitsthür geschehen
muſs. Sodann werden 5 Proc. Hämatit-Roheisen aufgegeben, wonach das Bad etwa 15
Minuten mehr oder weniger heftig aufkocht. Sind dann wiederum 15 bis 30 Minuten
vergangen, während welcher Zeit sich das Bad beruhigt hat, so zieht man alle
Schlacke bis auf die zur Bedeckung des Metalles in der Gieſspfanne nothwendige Menge
ab und nun erfolgt der Abstich. Hiernach ist eine sofortige Reinigung des Abstiches
von Schlacke erforderlich; man bringt deshalb zur Erleichterung dieser Arbeit
gegenüber dem Stichloche eine Thür an. Sodann stellt man den Boden mittels Kalkstein
unter Anlassen der Feuerung wieder her, beseitigt unter Umständen Ansätze mit Hilfe
von Brecheisen, oder
wendet zu demselben Zwecke Fluſsmittel an. Nach 1 bis 4 Stunden kann dann der
nächste Einsatz beginnen.
Um basisches Futter gegen mechanische Einflüsse
widerstandsfähiger zu machen, mischt W. F. Batho in
Westminster (* D. R. P. Nr. 29488 vom 5. Juni 1884) dasselbe mit 10 Proc. Eisen-
oder Stahldrahtabschnitten in gebogener oder gewundener Form. Entweder wird der
Draht in Wellen- oder in Spiralfeder form an dem Mantel der Birne befestigt, oder in
das Futter des Herdes werden von einander unabhängige oder in einander gedrehte
Schraubenfedern eingestampft, oder aber es werden willkürlich durch einander
geworfene oder parallel zu einander angeordnete Drahtstückchen in das Futter gelegt.
Hauptsache bleibt die Beimischung von Eisen- oder Stahldraht oder Spänen zu dem
basischen Futtermateriale von Stahl- oder Eisenöfen mit offenem Herde behufs
Erzielung gröſserer Dauerhaftigkeit des Futters.
Um in einer Bessemerbirne sauren oder basischen
Fluſsstahl, Guſsstahl oder gefeintes Roheisen herzustellen, gibt Ph. Lamberty in Ehrang (* D. R. P. Nr. 29571 vom 30.
April 1884) derselben eine besondere Einrichtung. Der Tragkranz wird als
Windbehälter hohl eingerichtet, so daſs der Gebläsewind durch einen der Hohlzapfen
in den Behälter und von da durch schräg nach unten gerichtete Düsen seitlich in das
Metallbad gelangen kann. In Folge der geringeren Druckhöhe sind also geringere
Windpressungen erforderlich. Die Düsen sind entweder nur auf einem Theile des
Umfanges, oder auf dem ganzen Umfange vertheilt. Auſserdem sind die Düsen nicht auf
die Mittelachse, sondern auf einen um dieselbe beschriebenen Kreis gerichtet, so
daſs der Wind das Metallbad in eine kreisende Bewegung versetzt. Eine genauere
Angabe der Benutzung der Birne ist in der Patentschrift nicht angegeben.
Um je nach Bedarf die Eisendarstellung nach dem Windfrisch- oder nach dem
Herdschmelzverfahren einrichten zu können, hat T.
Williamson in Pollokshields (Englisches Patent 1884 Nr. 6082) eine Bessemerbirne mit Siemens'schen Wärmespeichern in
Verbindung gebracht. Wie aus Fig. 10 Taf. 27 zu
entnehmen ist, besitzt die Birne sehr weite hohle Tragzapfen g und eine verschlieſsbare Mundöffnung. Die Zapfen münden in je einen
Kanal, in welchen die Gas- und Luftzüge zweier Siemens'schen Wärmespeicher auslaufen. Soll nun gebessemert werden, so läſst
man das Gebläse an, so daſs die Luft das Metall durchdringt und durch die
Wärmespeicher oder durch den Birnenhals abzieht. Bei dieser Benutzung steht die
Birne senkrecht. Will man dagegen den Apparat zum Herdschmelzprozesse anwenden, so
legt man die Birne wagerecht, was, da die Tragezapfen auf Rollen laufen, möglich
ist, und läſst heiſse Gase und Luft aus den Wärmespeichern über das Metallbad
streichen. Die Fuge zwischen den Tragzapfen und den Kanälen nach den Wärmespeichern
ist durch Wasserkasten gekühlt. – In der Grundidee erinnert diese Einrichtung an David und Manhés drehbaren
Schmelzofen (vgl. 1884 254 * 481).
C. Thompson in Sunderland (Englisches Patent 1884 Nr.
10292 und 10574) stellt den Querschnitt der Kanäle der Bessemerdüsen entweder ganz flach her, so
daſs die Luft das Bad in flachen Strömen durchdringt, oder er erweitert die Kanäle
nach hinten bedeutend, um die Reibung der Luft an den Kanalwandungen möglichst zu
verringern. Diese Düseneinrichtung soll sich in Oesterreich bei der sogen. Kleinbessemerei sehr gut bewähren.
Das Bessemer- und Thomasverfahren für Kleinbetrieb (vgl.
1884 252 * 243) hat in den letzten Monaten immer weitere
Beachtung gefunden.
Unter dem Titel „Krahn für Bessemerbirnen“ hat Alfred
Trappen in Wetter a. d. Ruhr ein deutsches Reichspatent * Nr. 29158 vom 1.
April 1884 erhalten, welches für Einrichtung solcher Kleinbetriebsanlagen von Werth
erscheint, wenn auch in Einzelheiten der Construction beim Gebrauche einige
Verbesserungen nöthig befunden werden dürften. Der Verfasser spricht sich über den
Gegenstand in Stahl und Eisen, 1884 S. 524 eingehender
aus.
Trappen sah bereits im J. 1878 auf
dem kgl. Ungarischen Hüttenwerke Rohnitz eine kleine Birne mit höchstens 300k Einsatz in Betrieb, in welcher unter Leitung des
Oberbergrathes Moschitz die verschiedenen Eisensorten
Ungarns geprüft wurden. Im J. 1879/80 wurden auf der Franz-Josefs-Hütte in
Oestr.-Schlesien unter Leitung des Hüttenmeisters Oelwein in einer kleinen Birne Sätze von 1500k bereits basisch mit Erfolg durchgeführt und ergaben ein ausgezeichnetes
Product. Avesta in Schweden liefert bereits, wie bekannt, mit Erfolg seit Jahren in
kleinen Birnen dargestellte marktfähige Waare, welche den Wettbewerb mit groſsen
Bessemerhütten aushalten kann. Prävali in Kärnten beabsichtigt, dies zu thun,
namentlich in kleinen Birnen feinere Qualitäten herzustellen, trotzdem zwei groſse
Bessemerbirnen zur Verfügung stehen; die beiden letzten Versuche haben eigentlich
nur wissenschaftlichen Zwecken gedient. Alle aber haben den Beweis geliefert, daſs
der Bessemerprozeſs sowohl sauer, als basisch in kleinen Birnen anstandslos
durchgeführt werden kann.
Wohl kein Hüttenprozeſs hat in den wenigen Jahren seines Bestehens
so bedeutende Fortschritte gemacht, als der Thomasprozeſs in Deutschland und
Oesterreich; mit gröſster Sicherheit wird ein Material erblasen, welches für die
Verwendung zu Draht, Feinblech u. dgl. kaum noch etwas zu wünschen übrig läſst und
das sich mit jedem Tage ein gröſseres Absatzgebiet erobert. Einzelne Gegenden
Deutschlands und Oesterreichs, welche ein ausgezeichnetes Roheisen erblasen und
dasselbe in Puddelöfen, oder gar noch im Frischherde in vorzügliches Schmiedeisen
umwandeln und vielfach zur Herstellung feiner Eisensorten, für Feinblech u.a.,
verwenden, sind bereits durch den Thomasprozeſs schwer bedroht. Aehnliches mag für
andere Länder gelten. Für solche Gegenden also würde der Klein-Bessemerprozeß jedenfalls eine nicht zu unterschätzende Bedeutung
gewinnen können, um so mehr, wenn in diesen Gegenden auch noch vielfach billige
Wasserkräfte zur Verfügung stehen, um die nöthigen Maschinen damit treiben zu
können.
Es erscheint somit wohl begründet, wenn dem Klein-Bessemerprozesse
in neuester Zeit eine gröſsere Aufmerksamkeit zugewendet worden ist und Veranlassung
zu vielfachen Versuchen und Einrichtungen genommen wurde. Seit Jahren fortwährend
mit dem Gegenstande beschäftigt und namentlich auch dem Klein-Bessemerprozesse ganze
Aufmerksamkeit zuwendend, hat Verfasser sich bestrebt, für denselben eine möglichst
einfache und bequeme Einrichtung zu finden, welche auf S. 382 dargestellt ist.
Die kleine Birne ist mittels einer starken stählernen Flansche an
dem Ausleger eines Krahnes beliebiger Construction befestigt und kann so bis
unmittelbar vor das Abstichloch eines kleinen Hochofens oder Schmelzofens gebracht werden. Somit
sind zunächst längere Zuführungsrinnen für das geschmolzene Eisen nicht
erforderlich; das flüssige Eisen gelangt auf kürzestem Wege in die Birne, Material-
und Wärmeverluste werden möglichst vermieden, was bei kleinen Einsätzen wohl
beachtet werden dürfte, und auch die Zeit des Einfüllens ist auf die kürzeste
herabgemindert.
Textabbildung Bd. 255, S. 382
Die Birne ist an dem äuſsersten Ende der stählernen Welle
angeheftet, welche zur Wendung derselben mittels Schneckengetriebe und Handrad
dient. Biese Welle besitzt an dem der Birne nächstliegenden Ende nur ein Unterlager;
die Schalen des Lagers auf der anderen Seite sind äuſserlich cylinderisch und leicht
drehbar in ihrem Lagerkörper. Die Luft wird durch ein Hohlstück der Welle, welches
mit einem Stopfbüchsengehäuse umgeben ist und mittels eines Schlauches mit dem
Absperrventile in Verbindung steht., eingeführt. Denkt man sich die Birne an eine
Centesimalkrahnwage angehängt, so wird sich dieselbe bei geringem Sinken des Krahnes
frei aus letzterem herausheben und es wird möglich, das Taragewicht einschlieſslich
der geringen Reibung im Lager am Ende der Welle und in den Zähnen des
Schneckengetriebes ziemlich genau zu ermitteln und durch Auflegen ferneren Gewichtes
das Gewicht des in die Birne eingeführten Roheisens festzustellen. Die Wage ist
unmittelbar vor dem Abstichloche des Ofens anzubringen. Durch Anheben des Krahnes
löst sich die Birne leicht von der Wage ab und kann nunmehr der Krahn bequem um 180°
oder nach Erforderniſs mehr oder weniger gedreht, die Birne vor einen passenden
Kamin oder ganz auſser den Bereich des Arbeitsraumes gebracht werden. Es wird
nunmehr Luft eingelassen, die Birne gewendet und das Frischen des Roheisens
vorgenommen.
Nach Vollendung des Frischens würde bei basischem Prozesse
zunächst die Schlacke in ein bereit stehendes Gefäſs abgegossen, alsdann das
erforderliche Ferromangan oder Spiegeleisen in möglichst zertheilter Form und, wenn
nöthig, vorgewärmt eingebracht. Dann würde bei beiden Fällen das gewonnene Metall
unmittelbar in die bereit stehenden Schalen eingegossen. Alle diese Arbeiten sind
mittels des Krahnes mit der gröſsten Leichtigkeit auszuführen. Der ferneren
Behandlung der Guſsschalen und Blöcke mittels des kleinen Blockkrahnes braucht keine
Erwähnung zu geschehen.
Für jeden Krahn mögen nach Erforderniſs 2 bis 3 Birnen vorhanden
sein, welche mittels eines leichten Wagens abgenommen, auf letzterem ausgebessert
und wieder warm geblasen, endlich im warmen Zustande wieder angeheftet werden, so
daſs die Hitzen ohne viel Unterbrechung auf einander folgen können.
Der ganze Vorgang vollzieht sich somit unmittelbar über der
Hüttensohle, ein einfacher Schuppen genügt für die Hütte, die Birne kann in
bequemster Weise bedient und ausgebessert werden. Es würden somit alle Bedingungen
vorhanden sein, welche die Arbeiten zu möglichst bequemen gestalten und die
Zeitdauer für eine Hitze möglichst abkürzen würden, so daſs es wohl gerechtfertigt
erscheint, die Dauer einer Hitze zu ½ Stunde oder die Zahl der Posten in 24 Stunden
auf etwa 50 anzunehmen.
Das Abstichloch kleiner Hochöfen liegt meistens sehr nahe über der
Hüttensohle; in diesen Fällen würde eine Gieſsgrube von etwa 500 bis 600mm Tiefe nicht zu umgehen sein. In Fällen, in
denen das Roheisen in Kupol- oder Flammöfen umgeschmolzen wird, liegt das
Abstichloch so hoch, daſs keinerlei Vertiefungen in der Hüttensohle nöthig sind.
Muſs das Roheisen umgeschmolzen werden, so würden örtliche Verhältnisse die Art des
Umschmelzofens, ob Kupol- oder Flammofen bestimmen; bei basischem Prozesse dürfte
ein Siemens'scher Ofen empfohlen werden, um dem Eisen
einen hohen Grad von Wärme zu ertheilen.
Die Birne ist vorläufig für einen Einsatz von 750k angenommen; daraus würden sich erfahrungsmäſsig
600k fertige Blöcke ergeben. Die
Leitungsfähigkeit für 1 Birne würde mithin für 24 Stunden zu 30000k anzunehmen sein. Sollte dieselbe nicht genügen,
so würde nichts im Wege stehen, auf der anderen Seite des Ofens eine zweite Birne
aufzustellen und unter Benutzung desselben Gebläses, Schmelzofens, Blockkrahnes
u.s.w. die Leistung zu verdoppeln. Da die Hitze kaum 12 Minuten beanspruchen kann,
so wird dieselbe Gebläsemaschine ununterbrochen im Gange bleiben und ohne
Vergröſserung recht gut 4 Hitzen in der Stunde blasen können.
Für die Bedienung einer Birne würden mit dem Schmelzarbeiter und
Maschinisten etwa 6 Mann in der Schicht zu rechnen sein.
Die erforderliche Windmenge wird laut Versuchen minutlich 40,
höchstens 50cbm von 1at
Spannung betragen. Die für die Anlage geplante eincylindrige Gebläsemaschine würde
einen Durchmesser des Dampfcylinders von 786mm des
Gebläsecylinders von 900mm, einen Hub von 786mm erhalten und in der Minute 50 Umdrehungen
machen. Die Gebläsemaschine könnte gleichzeitig in Fällen, in denen in Kupolöfen
umgeschmolzen werden soll, das erforderliche Roots-Gebläse und auſserdem die
Accumulatorpumpe betreiben. Um den verschiedenen Inanspruchnahmen folgen zu können,
ist die Maschine als Präcisionsmaschine mit Ventilsteuerung und Regulator gedacht.
Die Füllung wird eine sehr geringe sein, so daſs ein Dampfkessel von 70 bis 75qm Heizfläche genügen wird. Ein Accumulator für
20at Druck ist zur Beschleunigung der Arbeit
erforderlich. Wenn wünschenswerth, würde ein Martinofen oder gar ein Puddelofen so
aufgestellt werden können, daſs das Metall aus der Birne in diese Oefen eingegossen
und darin weiter behandelt werden könnte.
Die Kosten für den Birnenkrahn, 1 Birne, 1 Wagen, 1
Gebläsemaschine, 1 Accumulator, 1 Blockkrahn, 1 Centesimalkrahnwage, 1
Accumulatorpumpe stellen sich beiläufig auf 42000 M., für den Dampfkessel auf 7250
M. In manchen Fällen würden durch Nutzbarmachung vorhandener Wasserkraft die Kosten
noch bedeutend herabzumindern sein. Das Gebäude würde das denkbar einfachste sein
können.
Später (daselbst 1885 * S. 26) macht A. Trappen noch den
Vorschlag, die Abstiche gröſserer Hochöfen in Flammöfen
abzulassen, das Roheisen dort warm zu halten und dann allmählich in der
Bessemerbirne zu behandeln.
Darauf erwidert a. a. O. S. 109 H. Macco in Siegen,
welcher die Verbreitung des Avestaer Stahlprozesses in die Hand genommen hat, daſs
diese Art des Warmhaltens gröſserer Abstiche schon früher in Erwägung gezogen worden
und der Vorschlag in der angegebenen Form wohl auch nicht anwendbar ist. Es dürfte
aber möglich sein, ohne diesen Flammofen zu arbeiten, sobald man den Abstich 20 bis
25cm über dem Bodenstein des Hochofens
anbringt und dafür sorgt, daſs im gewöhnlichen Betriebe die Schlacke nie so tief
fällt, um das Abstichloch zu erreichen. Entschieden wendet sich Macco gegen die Bestrebungen, den Kleinbessemerbetrieb
für Groſsbetrieb, also auf die Benutzung groſser Hochöfen auszudehnen.
Ueber die Bedeutung der Kleinbessemerei für die alpine
Eisenindustrie hat Wilh. Hupfeld auf dem
Montistentage in Steyr im September v. J. Vortrag gehalten und in der Oesterreichischen Zeitschrift für Berg- und
Hüttenwesen, 1885 S. 1 ff. eine sehr lehrreiche Abhandlung
veröffentlicht.
Nachdem Verfasser den jahrelangen Kampf um die Herrschaft zwischen
Fluſseisen und Schweiſseisen beleuchtet hat, kommt er zum Schlüsse, daſs die Rettung
der Industrie der Alpenländer in dem täglich schärfer auftretenden Wettbewerbe mit
dem in der Birne erzeugten Thomasfluſseisen dadurch anzustreben sei, daſs man
zunächst dem jetzt dargestellten Bessemereisen die demselben eigenthümliche Härte
und die darin auftretenden Spannungen durch entsprechende Behandlung benehmen müsse.
Dies könne sowohl durch rationelles Ausglühen geschehen, als auch durch möglichste
Ausscheidung des Siliciumgehaltes, durch den allein sich Bessemereisen von
Martineisen und Thomaseisen unterscheide. Für alle Walzproducte, welche einer
späteren Verarbeitung nicht unterliegen, also für Schienen u. dgl., sei ein mäſsiger
Siliciumgehalt bis zu 0,5 Proc. absolut unschädlich, wenn ein gleich hoher
Mangangehalt vorhanden sei; für alle Artikel dagegen, welche Kohlenstoffhärte
benöthigen, oder nach dem Walzen einer weitgehenden Bearbeitung in und auſser dem
Feuer unterliegen, müsse das Silicium so viel wie möglich entfernt werden. Obschon
dies auch in groſsen
Birnen möglich ist und Fluſseisen mit 0,12 bis 0,20 Proc. Kohlenstoff, 0,03 bis 0,06
Proc. Silicium, 0,25 bis 0,4 Proc. Mangan, 0,035 bis 0,05 Proc. Phosphor, 0,01 bis
0,03 Proc. Schwefel mit vollster Sicherheit erzeugt wird, was sich in Prävali z.B.
seit 10 Jahren auch als vorzügliches Kessel-material bewährt hat, erscheint doch
eine Methode, welche eine noch weitergehende Entsilicirung des Bessemerfluſseisens
ermöglichen würde, von hohem Werthe. Nachdem Fr. Müller
(vgl. 1884 251 83, ferner Stahl
und Eisen, 1884 S. 69) darüber aufgeklärt hat, daſs das Metallbad nur bei
hoher Temperatur aus an Kieselsäure reicher
Schlacke das Silicium wieder aufnimmt, beschränkt sich die Aufgabe darauf, überhaupt
mit geringerer Temperatur zu arbeiten. Nach der Ansicht
Hupfeld's bietet die Verarbeitung kleinerer Roheisensätze in entsprechend kleineren Apparaten unter unmittelbarem Abgüsse der
Blöcke aus der Birne ein Mittel, um dem für die Wettbewerber des Thomasfluſseisens
gewünschten Ziele näher zu kommen.
Es wird dieses Prinzip einerseits durch die Engländer Clapp und Griffith in
stehender Birne (vgl. 1883 247 * 331) und andererseits im
bekannten Avestaer Verfahren (vgl. 1884 252 * 243)
angewendet.
Zu den vom Verfasser in Prävali angestellten Versuchen hatten die
günstigen Erfolge des Betriebes in Avesta die Anregung gegeben. Die Vorversuche
wurden in einer kleinen Birne von denselben Abmessungen wie der in Avesta in Betrieb
befindliche vorgenommen; dieselbe wurde in eine groſse Birne nach Abnahme ihrer
Haube und des Untertheiles eingebaut. Trotz der mangelhaften Einrichtung, namentlich
trotz der langen Fülldauer, verlief der Satz genügend heiſs und das Gieſsen sehr
gut, das Material war wesentlich weicher als sonstiger Bessemerstahl.
Man schritt hierauf zur Aufstellung einer kleinen Birne. Auf einem
gemauerten Sockel wurde ein guſseiserner, in zwei Lagerständern drehbarer Mittelring
festgeschraubt, in welchem die Birne mit einem Winkelringe und Keilen befestigt
wurde. Die Windzuführung geschieht wie üblich durch eine Hohlachse; der Wind wird
auf 70m Entfernung durch 500mm weite Blechröhren zugeleitet. Die Bewegung
erfolgt durch 2 Mann an einem Handrade, welches mit Getriebe von 1 : 5 in ein auf
der Achse aufgekeiltes Zahnrad eingreift. Die Birne steht auf der Hüttensohle; zum
Gusse dient eine Grube, in welcher die Guſsschalen auf Wagen laufen. Zur Füllung der
Birne und zu den Arbeiten mit den Schalen und den Blöcken wird ein gewöhnlicher
Gieſsereidrehkrahn gebraucht.
Wider Erwarten verlief zuerst der stetige Betrieb, bei welchem
alle 50 Minuten abgestochen wurde, sehr unbefriedigend. Trotzdem das Roheisen 2,5
Proc. Silicium und 5,5 Proc. Mangan enthielt, verlief die Hitze bei einer Dauer bis
zu 35 Minuten zu kalt. Es wurde dies auf die Beschaffenheit des Roheisens geschoben,
zu dessen Erblasung damals nur sehr mangelhafte Holzkohlen zur Verfügung standen und
das in dem 2m weiten Hochofengestelle eine nur
geringe Höhe einnahm. Als man dann dazu überging, nur einen kleinen Einsatz mit
jedem groſsen zu Verblasen, indem man jeweilig 700 bis 750k Roheisen der groſsen Pfanne entnahm, erhielt man
gute Posten. Im December v. J. fiel in Folge der Anlieferung besserer Kohle ein sehr
schönes graues Roheisen, mit welchem der stetige Betrieb mit bestem Erfolge
aufgenommen wurde. Der Ofen wurde in einstündigen Zwischenzeiten für 14 bis 18 auf
einander folgende Hitzen abgestochen; eine Unterbrechung trat auch dann nur wegen
Platzmangel für die Blöcke o. dgl. ein.
Nach diesen Betriebsergebnissen betrachtet Hupfeld es als feststehend, daſs man kleinere Hochöfen anstandslos alle
Stunden abstechen kann, mithin im Stande ist, ihre ganze Erzeugung in einer kleinen
Birne zu verarbeiten, wenn man regelmäſsig ein sehr hitziges gares Roheisen zur
Verfügung hat. Daſs ein solches Eisen Grundbedingung für das Gelingen des Verfahrens
ist, kann gar keinem Zweifel unterworfen sein, denn jeder Uebergang ins Mattere
hatte einen starken Auswurf zur Folge. Direkter Betrieb, d.h. wenn man das Roheisen
unmittelbar in die Birne laufen lassen kann, wird sich wahrscheinlich noch günstiger
gestalten, aber selten ausführbar sein. Jedenfalls sind Abkühlungen durch lange
Rinnen u. dgl. zu vermeiden.
Für Holzkohlenöfen ist die Erzeugung eines gleichmäſsig hitzigen
und garen grauen Roheisens nicht leicht durchführbar; für gröſsere Oefen von 30t Leistung in 24 Stunden ab ist es unmöglich,
Posten von 800 bis 1000k abzustechen, so daſs Hupfeld die Anbringung eines Zwischenapparates, in
welchem das Roheisen anzusammeln und nach Bedarf zu überhitzen wäre, in Erwägung
gezogen hat. Er ist mit Trappen (vgl. oben S. 384) der
Ansicht, daſs ein Gasflammofen hierzu am besten geeignet ist.
Die bisher erblasenen Posten verliefen günstig mit wenigen
Ausnahmen, wo das Roheisen zu kalt war. Nach 1 bis 2 Minuten, manchmal sofort,
stellt sich lange Flamme ein, welche unter starker Rauchentwicklung bis zum Schlüsse
anhält. Zur Beurtheilung des Endes werden Schlacken und Metallproben genommen. Vor
dem Gieſsen, aber nach dem Ferromanganzusatze, welcher zwischen 0,25 bis 1 Proc.
schwankt, wird das Bad bei Bedarf durch kalte Eisenabfälle abgekühlt, die bei
unmittelbarem Gusse bis zu 10 Procent des Einsatzes betragen. Es wird dabei die oben
mehr erkaltete Schlackendecke in der Birne zurückgelassen und das Metall in sehr
dünnem Strahle langsam ausgegossen.
Die Qualität dieses Bessemerstahles ist nach den bisherigen
Erfahrungen eine bessere als die des gewöhnlichen Verfahrens. Die Zähigkeit ist
entschieden gröſser als bei Schweiſseisen, die Schweiſsbarkeit vollkommen
befriedigend, die Dehnbarkeit eine sehr hohe. 60 auf einander folgende
Siebener-Posten ergaben im Durchschnitte 0,0281 Proc. Silicium und zwar 11 Posten
(oder 18 Proc.) unter 0,02, 29 (48,6 Proc.) von 0,02 bis 0,03, 11 (18 Proc.) von
0,03 bis 0,04, 7 (11,6 Proc.) von 0,04 bis 0,05 und 2 (3,8 Proc.) von 0,05 bis 0,055
Proc. Silicium und ferner im allgemeinen Durchschnitte 0,1166 Proc. Kohlenstoff, und
zwar 16 (26,6 Proc.) unter und von 0,10 Proc., 23 (38,3 Proc.) mit 0,11 und 0,12, 19
(31,6 Proc.) mit 0,13 bis 0,14 bis 0,15, 2 (3,5 Proc.) mit 0,16 Proc. Kohlenstoff,
während die in derselben Zeit in der groſsen Birne erblasenen Siebener-Posten einen
Durchschnitt ergaben von 0,055 Proc. Silicium und 0,126 Proc. Kohlenstoff.
Während also nach Hupfeld
hinsichtlich der Ueberlegenheit der Güte im Kleinbetriebe kein Zweifel zu bestehen
scheint, herrscht weniger Klarheit über den wirtschaftlichen Vortheil desselben.
Nach J. v. Ehrenwerth (vgl. 1884 252 248) wäre für die Alpenländer die Kleinbessemerei das billigste
Verfahren, namentlich billiger als das bisher übliche Bessemern. Verfasser
bezweifelt dies; während er die Gesammtkosten einer Groſsbessemerei für eine
Erzeugung von 15000t Blöcken, entsprechend der
Leistung zweier alpinen Holzkohlen-Hochöfen, mit 500000 M. in Rechnung setzt, so
daſs die 50000 M. Zinsen, welche diesem Betriebe zur Last fallen, auf 100k 33,3 Pf. ausmachen, bringt er die
Kleinbessemerei mit 90000 M. in den Anschlag, so daſs hier auf 100k nur 6 Pf. Zinsen entfallen. Das Verhältniſs des
Kleinbetriebes gegenüber dem Groſsbetriebe wird sich nach Hupfeld etwa folgendermaſsen gestalten:
Löhne auf 100k
+ 10 Pf.
Feuerfestes Material
+ 20
Roheisen (Mehraufwand)
+ 24
Verlust an Blockschöpfen
+ 20
Zinsen und Tilgung
– 33,3 Pf.
––––––––––––––––
+ 74 Pf.
– 33,3 Pf.,
d.h. es ergibt sich nach Abzug des Zinsenunterschiedes
also ein Ueberschuſs von rund 50 Pf. auf 100k zu
Ungunsten des Kleinbetriebes. Dieser Unterschied wird sich natürlich nach örtlichen
Verhältnissen ändern, aber nie verschwinden, so daſs es aussichtslos erscheint, in
den Alpenländern das neue Verfahren in Wettbetrieb mit den
bestehenden Bessemerhütten einführen zu wollen zur Erzeugung von Schienen,
grober Zeugwaare, Schiffsblechen u. dgl.; die Frage kann nur sein, ob man mit dem
Schweiſseisen und dem Martinfluſseisen bezieh. dem Thomaseisen wettarbeiten kann.
Von Wichtigkeit ist hierbei der Punkt, ob man die Blöcke roh verkaufen oder selbst
weiter verarbeiten will. Der Blockverkauf würde, weil man dann auf kleine Blöcke
hinarbeiten muſs, den direkten Birnenguſs ausschlieſsen. Hupfeld erachtet den vorgewalzten Block als die zweckmäſsigste
Handelsform, da die Umformung des Groſsblockes in eine solche Form unter Verwendung eines
kräftigen Walzwerkes und unter Ausnutzung der ursprünglichen Wärme billig geschehen
kann.
Die anzusaugende Windmenge berechnet Verfasser auf 45qm in der Minute; dieselbe ist auf ⅔ bis 1at zu pressen. Auch die Alpenländer müssen
demgemäſs bei etwaiger Anlage einer Kleinbessemerei bei vorhandenen Hochöfen fast
überall auf Dampf kraft rechnen, da verfügbare Wasserkräfte von 80 bis 100e, wenigstens nicht bei den steirischen und
kärntnerischen Hochöfen, vorhanden sind. Hupfeld
empfiehlt unter allen Umständen die Anlage eines für die angegebene Pressung
gebauten Gebläses, um nach Bedarf sowohl mit dem Avesta-Verfahren, als auch nach der
Methode von Clapp und Griffith arbeiten zu können.
Zur Kleinbessemerei liefert – jedoch ohne Bezugnahme auf
die jüngsten Erfahrungen Hupfeld's – einen weiteren
Beitrag P. v. Tunner in der oben genannten Oesterreichischen Zeitschrift, 1885 S. 41 ff.
Mit Bezug auf die Mittheilungen von Hupfeld, J. v. Ehrenwerth, Truppen und Macco
gesteht Verfasser offen, daſs ihm die Ursachen, weshalb die Kleinbessemerei ein
vorzüglicheres Product als das Bessemern in groſsen Birnen liefere und insbesondere
zur Darstellung eines sehr weichen, faserigen Eisens
geeignet sein sollte, nicht faſslich sind; es kann nach seiner Ansicht eine
Verkleinerung der Sätze wohl bei der Herdfrischerei und im gewöhnlichen
Fuddelprozesse von verbesserndem Einflüsse auf ihre Güte sein, aber niemals in der
Bessemerbirne, weil die Durcharbeitung, welche im ersten Falle von Hand geschieht
und der Verbesserung fähig ist, im zweiten Falle in der vollkommensten Weise von dem
gepreſsten Winde besorgt wird. Der Vortheil, welchen die bei dem Avesta-Prozesse
erzielte Verminderung der Abkühlung in Folge des unmittelbaren Vergieſsens aus der
Birne bietet, wird reichlich aufgehoben bei den gröſseren Posten durch den
vergleichsweise geringeren Verlust an Wärme durch Ausstrahlung. Die
Schlackenvermengung mit dem Metalle, welche zwar nach der herrschenden Meinung
gerade die Bildung eines faserigen Eisens herbeiführen soll, sieht Tunner unter allen Umständen für einen Nachtheil an;
abgesehen davon, erblickt er keine besondere Schwierigkeit darin, auch bei dem
Vergieſsen gröſserer Posten theilweise die Schlacke mit dem Metalle in die Schalen
gelangen zu lassen.
Daſs im Groſsen und Ganzen das Bessemerverfahren den Herdfrisch-
und Puddelprozeſs immer mehr verdrängen werde, steht für Tunner seit Jahren auſser Zweifel, weil er überzeugt ist, daſs ersteres
billigere und zugleich bessere Qualität liefere; daſs aber gerade die
Kleinbessemerei dazu geeignet sein soll, die Herdfrischerei zu verdrängen, kann
seines Erachtens wohl nur insofern Geltung haben, als die Kleinbessemerei,
namentlich in Bezirken mit vielen kleinen, auf die Verwendung von Pflanzenbrennstoff
begründeten Eisenwerken, wegen ihrer geringeren Anlags- und Betriebskosten, leichter
in Anwendung gebracht werden kann als das Bessemern mit gröſseren Einsätzen. Im
übrigen wird jedoch der Bessemerprozeſs um so vortheilhafter betrieben werden
können, mit je gröſseren Posten, bis zu 10 und 15t, bei ununterbrochenem Betriebe gearbeitet wird.
Tunner hält dafür, daſs der noch
vielfach verbreitete Zweifel rücksichtlich der Qualität des Bessemermetalles – auch
für dessen Verwendung zu Schiffs-, Kessel- und Feinblechen, Drähten u. dgl. –
täglich mehr beseitigt werde. Wenn Verfasser nun der Kleinbessemerei nicht den
Vorzug einzuräumen vermag, welcher dieser Arbeit von anderen Seiten mit Bezug auf
die besondere, gute weiche Qualität zuerkannt wird, so gibt er doch die groſse
Wichtigkeit zu, welche das Verfahren vorzugsweise für die alpinen Verhältnisse hat.
Die Einführung der Kleinbessemerei daselbst setzt voraus, daſs das Roheisen dem
Hochofen unmittelbar entnommen werde. Will man stetigen Betrieb mit Anwendung von
Durchweichungsgruben einleiten, so muſs man auf ungefähr jede halbe Stunde einen
Satz rechnen, dessen Gewicht füglich nicht unter 500k angenommen werden kann. Es entspricht dies einer täglichen
Roheisenerblasung von 24t, eine Menge, welche von
vielen alpinen Hochöfen überschritten wircj. und Einsätze von 1000 bis 1500k ermöglicht. Je kleiner das Satzgewicht gewählt
wird, um so hitziger muſs das Roheisen sein; es darf aber andererseits nicht zu viel
Silicium enthalten und muſs deshalb mit einer sehr basischen Schlacke erblasen
werden. Dies würde 25 bis 30 Procent mehr Brennstoff als die landesübliche
Darstellung von halbirtem Roheisen erforderlich machen; würde man das Roheisen im
Kupolofen umschmelzen, so würde sich auch dort der Brennstoffbedarf um 15 bis 20
Proc. höher stellen als bei der gewöhnlichen Umschmelzerei. Mit der Kleinheit der
Einsätze wachsen im Allgemeinen die Schwierigkeiten- erst bei 1000 bis 1500k kommt man auf einen dem gewöhnlichen Bessemern
ähnlichen sicheren Betrieb.
Verfasser drückt seine Meinung dahin aus, daſs die Kleinbessemerei
nicht in Anbetracht einer damit vermeintlich zu erzielenden vorzüglichen weichen
Qualität, sondern vielmehr in der Rücksicht unsere
volle Beachtung und Förderung verdient, daſs mit diesem Verfahren bei
verhältniſsmäſsig kleinen Eisenwerken und mit geringen Kosten der an und für sich so
wichtige Bessemerprozeſs und zwar mit stetigem und
dadurch billigerem Betriebe eingerichtet werden kann.
Unter stetigem Betriebe ist hier verstanden, daſs die Oefen, Maschinen und Arbeiter
mit thunlichst geringen Unterbrechungen vollauf beschäftigt sind und das einmal
erhitzte Material unter möglichst geringen Verlusten an Hitze rasch seiner
Vollendung zugeführt wird, um Brennstoffbedarf, Metallverlust und Allgemeinkosten
nach Möglichkeit zu verringern. Die Durchweichungsgruben sind stets vortheilhaft,
auch wenn die aus denselben kommenden Blöcke nicht mehr genügend Hitze besitzen, da
sie in diesem Falle in kürzerer Zeit und gleichförmiger erhitzt werden können.
Zum Schlüsse erwähnt Tanner noch den
Trappen'schen Vorschlag, betreffend die
Einschaltung eines Flammofens zwischen Hochofen und Birne (vgl. S. 384 d. Bd.), und
meint, daſs auf diesem Wege ein stets hitziges Roheisen für die Birne wohl erzeugt
werden könnte- doch scheitere der Vorschlag an den Kosten, welche durch Unterhaltung
der Flammöfen entstehen würden, zumal die Einstellung eines stets bereiten zweiten
Ersatzofens für nothwendig bezeichnet wird. Unter diesen Umständen müſste es denn
doch besser sein, mit gröſseren Einsätzen zu arbeiten, welche unmittelbar vom
Hochofen entnommen werden, und zugleich den Hochofen in einem entsprechenden
hitzigen Gange zu erhalten.
(Schluſs folgt.)
Tafeln
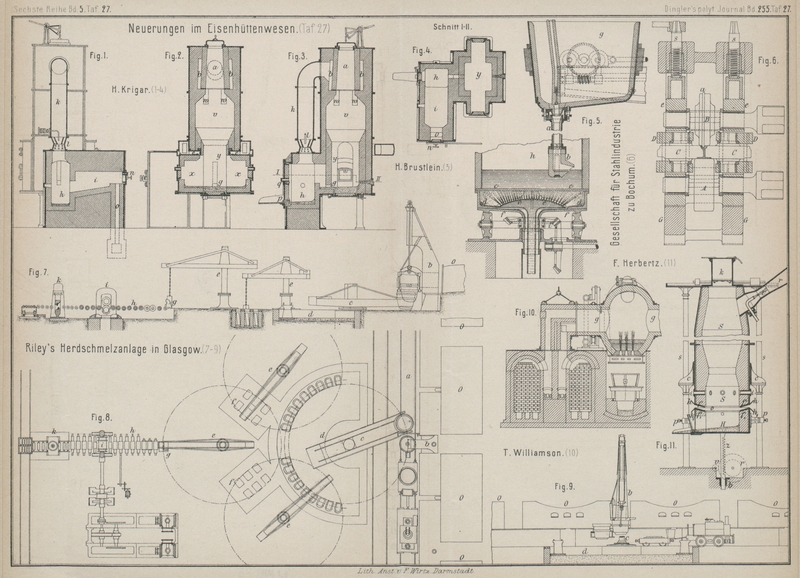