Titel: | Ueber Neuerungen im Eisenhüttenwesen. |
Fundstelle: | Band 257, Jahrgang 1885, S. 235 |
Download: | XML |
Ueber Neuerungen im Eisenhüttenwesen.
(Patentklasse 18. Fortsetzung des Berichtes Bd.
255 S. 421.)
Mit Abbildungen auf Tafel
17.
Ueber Neuerungen im Eisenhüttenwesen.
In der Zeitschrift des Vereins deutscher Ingenieure,
1885 * S. 245 ist ein Vortrag von Weinlig über den Einfluſs der Hochofen-Abmessungen sowie der Gas fange auf
die Betriebsergebnisse der Hochöfen im Allgemeinen sowie der Siegener
Hochöfen im Besonderen veröffentlicht.
Von jeher hat man danach gestrebt, das Ausbringen der
Kokes-Hochöfen bei gleichzeitiger Verminderung des Kokesverbrauches zu vergröſsern,
und ist dies bis zu einer bestimmten Grenze durch die Vergröſserung des Hochofens
erreicht, dann aber auch durch Anwendung besserer Kokes und hoch erhitzten Windes.
Der Inhalt der Hochöfen ist in Folge dessen von 80 bis 100cbm auf 300 bis 500cbm, in England sogar auf über 1000cbm
gestiegen. Je länger die Beschickung der Einwirkung reducirender Gase ausgesetzt
ist, desto besser ist die Ausnutzung derselben, desto mehr Reduction durch
Kohlenoxyd findet statt, desto weniger Brennmaterial auf 1t erzeugten Eisens wird verbraucht; andererseits
aber wird das Ausbringen bei gleicher Windzufuhr und gleichem verhältniſsmäſsigen
Kokesverbrauche ein vergröſsertes werden, welche ein kleinerer Ofen auch, aber nur
durch vermehrte Windzufuhr und Mehrverbrauch an Brennmaterial erreichen würde. Die
groſsen englischen Hochöfen beweisen indessen, daſs die Vergröſserung nicht im
geraden Verhältnisse zum Ausbringen steht.
Mit dieser bedeutenden Raumvergröſserung wachsen naturgemäſs die
Anforderungen an die Gichtaufzüge und die Gebläsemaschinen. Der Inhalt und die Höhe
des Hochofens hängt wesentlich ab von der Natur der Kokes und der Erze. Nach den
bisherigen Erfahrungen scheint die Grenze des Ofeninhaltes nach oben 400cbm zu sein. Die Natur des zu erblasenden Eisens
hängt weniger von dem Inhalte der Oefen ab als von der Durchgangszeit der Gichten,
durch deren Aenderung man die Art des Roheisens beeinflussen kann.
Ueber die zweckmäſsigste Form der Hochöfen gehen die Ansichten der
Techniker weit aus einander, so daſs im Siegerland kaum zwei Hochöfen vorhanden
sind, welche sich einander gleichen. Durch die heutige Form der Hochöfen –
Erweiterung des Gichtdurchmessers nach dem Kohlensacke und Wiederverengung nach dem
Gestelle zu – will man die Schmelzmaterialien nach der Ofenmitte hin auflockern und
den Niedergang derselben verlangsamen. Da sich aber die Schmelzmaterialien von der
Gicht bis zum Kohlensacke nur unmerklich in ihrem Volumen verändern, so stände der
Anordnung cylindrischer Schächte nichts entgegen. Trotzdem sind dieselben nicht
beliebt. Den Kohlensackdurchmesser soll man nicht über 6m wählen, wegen der erforderlichen gleichmäßigen Vorbereitung der Erze durch die reducirenden Gase. Der
Durchmesser der Gicht richtet sich nach der Construction des Gasfanges. Eine in der
Achse des Hochofens lockere Beschickung erreicht man am besten durch ein Mittelrohr und eine Langen'sche Glocke bei nicht zu weiter Gicht.
Erachtet man aber die Schüttung des Parry'schen
Trichters als die zweckmäſsigste, dann wähle man eine enge Gicht. Die Gase sind
immer in der Mitte abzuziehen. Offene Gichten sind unzweckmäſsig. Aus dem
Durchmesser des Kohlensackes und des Gestelles und der Höhe des Kohlensackes über
dem Bodenstein ergibt sich der Rastwinkel. Derselbe war früher 60 bis 65°; er
beträgt heute 70 bis 80°. Flache Rasten stehen einer Vergröſserung des Ausbringens
entgegen. Der Durchmesser des Gestelles sollte nicht über 2m steigen; nur bei hoch erhitztem Winde (800°)
darf das Gestell vergröſsert werden.
Die von W. J. Taylor in Chester (New-Jersey) mit einem
cylindrischen Hochofen vorgenommenen Versuche (vgl.
Engineering and Mining Journal, 1884 Bd. 38 * S.
187) sind leider miſslungen. Der Erfolg spricht weder für, noch gegen die
cylindrische Form, weil mit dem Ofen noch ganz andere als auf die Form bezügliche
Versuche gemacht worden sind, welche einen Schluſs auf die Zweckmäſsigkeit der
ersteren nicht gestatten. (Vgl. auch Lürmann's Kritik
in der Zeitschrift des Vereins deutscher Ingenieure,
1885 * S. 373.)
Der Vorschlag der Société des Aciéries de Longwy in
Longwy (D. R. P. Nr. 30545 vom 14. Mai 1884) befaſst sich mit der Herstellung von Mangan haltigen Kokes. Dieselben sollen
besonders zur Erzeugung von Bessemer-Roheisen mit möglichst geringem Schwefelgehalte
und 1,5 bis 2 Proc. Mangan, wie es sich besonders für den basischen Prozeſs eignet,
dienen. Gibt man das Mangan in den Erzen auf, so wird dasselbe zum gröſsten Theile
verschlackt. Mischt man aber das Manganerz mit den Kokes, so verbindet es sich
unmittelbar mit dem Schwefel derselben und geht als Schwefelmangan in die Schlacke,
während der übrige Theil des Mangans reducirt in das Eisen übergeht. Zur Herstellung
der Mangankokes werden Kohle und Manganerze, unter Umständen auch noch andere
Zuschläge, in Pulverform vermischt und verkokt. Nach Versuchen mit derartigen
Mangankokes sollen dieselben mehr als die Hälfte Mangan, welches sonst in den Erzen
enthalten sein müſste, um ein Roheisen mit bestimmtem Mangangehalte zu erblasen,
ersparen.
Zur Entphosphorung und Entschwefelung des Roheisens
füllt C. H. W. Hoepfner in Berlin (D. R. P. Nr. 30123
vom 1. Januar 1884) einen Schachtofen, dessen Futter sauer oder basisch sein kann,
locker mit Bruchstücken von Kalkstein oder an Kalk reichen Ziegeln, denen Stücke von
Eisen- und Manganoxyd beigemischt werden können. Am unteren Ende des Ofens ist ein
Abstich und eine Winddüse vorhanden. Nachdem der Inhalt des Ofens durch stark
erhitzte Luft zum Weiſsglühen gebracht ist, läſst man das flüssige, Silicium,
Kohlenstoff und Phosphor enthaltende Roheisen ununterbrochen von oben in den
Schachtofen hineinflieſsen. Dabei sollen Silicium, Kohlenstoff und zuletzt Phosphor
und Schwefel durch die Oxyde des Eisens und Mangans bezieh. den Gebläsewind oxydirt
und die Phosphorsäure durch den Kalk sofort gebunden werden. Diese Schlacke bleibt
an den Steinen haften, während das schwerere entphosphorte Eisen durch die Schlacken
hindurch flieſst und sich am Boden ansammelt, von wo es abgelassen wird. Bei
Anwendung von viel Eisenstein oder Braunstein in der Kalkfüllung soll man das
Einblasen von Luft während des Eingieſsens des Roheisens ganz entbehren können.
Statt des Schachtofens wird auch die mit einem Abstiche versehene Bessemerbirne
vorgeschlagen. Nach früheren Versuchen hat das Verfahren wenig Aussicht auf
Verwerthung.
Zur schnelleren und vollkommeneren Verbrennung von
Gasen, deren Temperatur geringer, als zur Entzündung nothwendig ist, gibt
F. W. Lürmann in Osnabrück (* D. R. P. Nr. 31116
vom 17. August 1884) eine Einrichtung an, welche sich besonders bei Winderhitzern und Dampfkesselfeuerungen
anwenden läſst. In Fig. 6 Taf. 17
ist der untere Theil eines Röhren-Winderhitzers dargestellt. Die Gase treten durch
das Rohr G, den Kasten G1 und enge Schlitze in den Vorraum V und verbrennen hier, nachdem sie sich mit
atmosphärischer Luft, welche zwischen den Gasschlitzen eintritt, gemischt haben.
Dabei werden das Gas und die Luft durch die von den Mauern des Verbrennungsraumes
V ausgestrahlte Wärme erhitzt. Die Luft tritt durch
die Oeffnungen l, l1
des Ofengemäuers in die den unteren Theil des Flammraumes des Winderhitzers auf 3
Seiten umgebenden Kanäle l2, erhitzt sich hier und gelangt dann in den Kanal l3, welcher sie in den unmittelbar über
dem Verbrennungsraume V liegenden Ofentheil L führt, von wo sie durch enge, zwischen die
Gasschlitze im Verbrennungsraume V ausmündende Kanäle
in letzteren gelangt. Auf diesem Wege wird die Luft durch die ausstrahlende Wärme
des Verbrennungsraumes erhitzt und angeblich in Verbindung mit der vollkommeneren
Mischung mit dem Gase eine bessere Verbrennung als bisher erzielt. Will man auch das
Gas erhitzen, so kann man den Raum L durch eine
Scheidewand in 2 Abtheilungen trennen, zu welchen besondere Gas- und Luftkanäle
gehören. In der Patentschrift ist auch die Anwendung der Einrichtung auf
Winderhitzer mit Steinfüllung und auf Dampfkessel
erläutert.
Für Winderhitzer u. dgl. hat J.
Hanlon in New-York (* D. R. P. Kl. 47 Nr. 31060 vom 18. Juni 1884) einen
Absperrschieber mit Wasserkühlung angegeben, bei
welchen sowohl der hohle Schieberkörper, als auch der von einem besonderen Gehäuse
umschlossene Schieberkasten nach einander von einem laufenden Wasserstrome bespült
wird. Der Hohlraum des Schieberkörpers B (Fig. 9 Taf. 17)
ist durch eine Scheidewand b in zwei Abtheilungen
getrennt, in welche die in der Wandung des Schieberkörpers befestigten Rohre e und f münden. Bei der
Aufwärtsbewegung des Schiebers, welche durch einen einfachen, an der Stange a angreifenden Hebel bewerkstelligt wird, verstellen
sich die Rohre e und f in
Stopfbüchsen des Schieberkastens und erhält dadurch der Schieber seine Geradführung.
Der Schieberkasten ist von einem Blechgehäuse umschlossen und steht auſserhalb
desselben das Rohr e durch einen biegsamen Schlauch mit
der Wasserzuleitung in Verbindung. Das dadurch in die eine Abtheilung des
Schieberhohlraumes zugetretene Kühlwasser flieſst durch eine Oeffnung in der
Scheidewand b in die zweite Abtheilung und aus
derselben in dem Rohre f und einem damit verbundenen
Rohre f1 in den
Behälter, aus welchem es oben bei m abläuft. Unter dem
Schieber B befindet sich in dem Schieberkasten noch ein
hohler Raum d, welcher den sich absetztenden Staub o.
dgl. unter dem Schieber aufnimmt, so daſs beim Schlieſsen desselben die gute
Abdichtung gesichert ist. Der Raum d ist unten mit
einem abnehmbaren Deckel versehen, um den Staub leicht entfernen und die
Dichtflächen des Schiebers reinigen zu können.
An seinem Heiſswindschieber hat F. Burgers in Bulmke (* D. R. P. Kl. 47 Zusatz Nr. 31384 vom 12. September
1884, vgl. 1885 255 * 186) an Stelle der eingelegten elastischen Dichtungsringe die
Schiebersitzbüchsen mit vorstehenden Ringen versehen. Das Schiebergehäuse ist, um
diese Sitzbüchsen dann einbringen zu können, zweitheilig ausgeführt. Die Sitzbüchsen
haben wieder eine Packung aus Asbest erhalten.
Zur Auswechselung ganzer Bessemerbirnen (vgl. Holley 1883 248 501)
schlagen P. C. Gilchrist in Wolverhampton und L. G. Fitzmaurice in Bilstone (Englisches Patent 1884
Nr. 7804) die in Fig. 1 Taf. 17 dargestellte hydraulische
Hebevorrichtung vor, welche unter der Birne im Boden liegt und deren
Kolbenkopf mittels eines Querhauptes E in den Ständern
F geführt wird. Auf dem oberen Ende des Kolbens
ruht drehbar ein Tisch C, welcher ein Stück
Schienengeleise trägt. Um nun die Birne auszuwechseln, hebt man den Tisch, so daſs
ein aufgefahrener Wagen die senkrecht gekippte Birne von unten erfaſst. Sodann hebt
man dieselbe mit dem Wagen, nachdem man die Lagerdeckel der Zapfen abgenommen hat,
so hoch, daſs die Zapfen über den Lagern stehen. Natürlich muſs man vorher das
Windrohr und die Drehachse, welche auſserhalb der
Zapfenlager an die Zapfen angeschlossen sind, abkuppeln. Dann dreht man Birne, Wagen
und Tisch um 45°, so daſs die Zapfen parallel dem Geleise stehen und kann nun den
Kolben anstandslos senken. Auf umgekehrte Weise geschieht das Einlegen einer neuen
Birne. Bei dieser Einrichtung brauchen also die Zapfenlager nur um den Durchmesser
der Birne von einander entfernt zu sein.
Die schon früher angeregte Idee, die Wärme der
Bessemerbirnenflamme zu verwerthen, hat neuerdings Th. Williamson in Wishaw, Schottland (* D. R. P. Nr. 31236 vom 22. August
1884) zu dem Zwecke vorgeschlagen, den Bessemer- mit dem
Herdschmelzprozesse zu vereinigen (vgl. Williamson 1885 255 * 380). Die Bessemerbirne
Fig. 2 bis
5 Taf. 17
hat in der Kippebene den in Fig. 3 dargestellten
Querschnitt. Diese Form bezweckt die Verminderung von Melallverlusten, indem die vom
Winde mitgerissenen Metalltheilchen gegen die Wölbung der Birne stoſsen und wieder
in das Metallbad zurückfallen. Die Einrichtung des Bodens ist die bekannte. Der Hals
der Birne ist sehr eng und wird von einer Klappe, welche durch irgend welche Mittel
festgestellt werden kann, überdeckt. Die Zapfen der Birne sind unverhältniſsmäſsig
groſs, beide hohl, mit feuerfestem Futter bekleidet und laufen nach Art der Hälse
der Drehöfen in Rollenlagern (vgl. Fig. 2). An die Endflächen
der Zapfen schlieſsen sich die leicht entfernbaren Kanaltheile a und c, welche zu den 4
Regeneratorkammern G und L
führen. Zur Dichtung der Fuge zwischen den Zapfenendflächen und dem Kanalkörper a c ist an letzterem ein mit Wasser gekühlter Ring r (vgl. Fig. 4) befestigt, so daſs
ein U-Eisen t die mit einem Winkeleisen versehenen
Zapfenenden umfaſst. Der Zwischenraum kann mit Schlackenwolle gefüllt werden. Die Kippung der Birne
geschieht in bekannter Weise durch ein auf einem Zapfen angeordnetes
Schneckengetriebe, welches durch eine besondere kleine Dampfmaschine (vgl. Fig. 5) o. dgl.
angetrieben wird. Das feste Windrohr w ist mittels
zweier Gelenke d mit dem an der Birne befestigten
Windrohre e verbunden, so daſs der Birne in jeder Lage
Wind zugeführt werden kann.
Beim Betriebe wird nun die Birne behufs Füllung in die punktirte Stellung Fig. 3 gekippt
und dann nach Oeffnung der Klappe die auf einer erhöhten Schienenbahn laufende
Roheisenpfanne über den Rand in die Birne entleert. In letzterer sammelt sich das
Eisen im Bauche an, so daſs es den Boden nicht berührt. Man verschliefst nun die
Klappe, läſst den Wind an und richtet die Birne auf, so daſs die Windstrahlen das
Eisenbad in seiner ganzen Höhe durchströmen. Immerhin hat aber das Bad bei gleich
groſsen Sätzen nicht die Höhe des Bades in gewöhnlichen Birnen, weil das Eisen bei
senkrechter Stellung der Birne den Bauch derselben zum Theile noch ausfüllt. In
Folge dessen können kleinere Gebläsemaschinen zur Verwendung gelangen. Nachdem die
nöthigen Zusätze von Abfalleisen u.s.w. gemacht sind und das Blasen etwa 10 bis 15
Minuten angedauert hat, wobei das Silicium und der Kohlenstoff angeblich genügend
oxydirt worden sind, wird die Birne gekippt, bis das Eisenbad den Boden nicht mehr
berührt. Man stellt dann das Gebläse ab und unterwirft das Bad durch Einlassen von
Gas und Luft in die vorher durch die Bessemerflamme erhitzten Regenerativkammern
einem Herd Schmelzprozesse. Während desselben kann das Bad durch die Klappenöffnung
umgerührt werden (vgl. Fig. 5) und irgendwelche
Zusätze erhalten. Die Ueberführung der Bessemerflamme in die Regeneratorkammern
erfolgt bei den einzelnen Hitzen abwechselnd, so daſs die Flamme bei der einen Hitze
z.B. durch die linken Kammern strömt, während die rechten geschlossen sind. Durch
die geheitzten Kammern ziehen dann beim zweiten Theile des Prozesses Gas und Luft.
Die Abhitze dieser Flamme geht durch die rechten Kammern und ebenso die
Bessemerflamme der nächst folgenden Hitze u.s.w. Hat das Fluſseisen die gewünschte
Zusammensetzung, so werden Gas- und Luftzufuhr abgeschnitten und die Birne so weit
gekippt, daſs das Bad in die Gieſspfanne g abgelassen
werden kann. Die Gieſspfanne g ruht auf einem
Drehkrahne und wird in bekannter Weise in die Formen entleert. Statt eines
Schlackenwagen s kann die Schlacke auch in eine unter
der Birne befindliche Grube ausgegossen werden.
So hübsch die Sache auch erdacht ist, so wenig wahrscheinlich erscheint es, daſs eine
derartige Anlage jemals zur Ausführung kommt; in welchem Verhältnisse stehen denn
die durch die Verbindung der beiden Prozesse erzielten Vortheile zu den Kosten der
Anlage und des Betriebes? Der Erfinder will die Birne sowohl zur Ausführung des
sauren, wie des basischen Verfahrens benutzen.
B. Versen in Dortmund (* D. R. P. Nr. 30634 vom 23.
April 1884) hat verschiedene Maschinen angegeben, um die Böden und das Futter basischer Birnen zu stampfen. Die gestampften Theile
sollen durch eine derartige maschinelle Herstellung
gleichmäſsiger, fester und in Folge dessen haltbarer werden. Die eine der Maschinen
zur Herstellung der Böden besitzt einen Stampftisch, welcher sowohl um eine
senkrechte, als wagerechte Achse gedreht werden kann, um den Stampfer in jeder
Richtung auf die Bodenmasse einwirken lassen zu können. Die Bewegung des Tisches
erfolgt mittels Wasserdruck oder Riemen. Am Rande der Grube, in welcher der Tisch
ruht, steht ein Drehkrahn, an dessen Ausleger radial verschiebbar die Stampfmaschine
– ein kleiner Schnellhammer – angebracht ist, der durch Dampf oder Preſsluft, welche
ja immer im Bessemerwerk vorhanden ist, getrieben wird. Die Steuerung für diesen
Schnellhammer und die für die Vorrichtungen zum Einstellen des Stampftisches, auf
welchem die Bodenform steht, liegt im Bereiche des einen Arbeiters, welcher das Stampfen beaufsichtigt. Nachdem die Böden
fertig gestampft sind, werden die Windkanäle durch gleichzeitiges Einpressen von
ebenso viel Stahlnadeln hergestellt. Die letzteren sitzen an dem Kolben einer
hydraulischen Presse, welche entweder gleich unter dem Stampftische angeordnet, oder
an einem besonderen Orte untergebracht ist. Eine ähnliche Einrichtung besitzt die
Futterstampfmaschine.
Beim Stampfen des Birnenfutters wird in der Längsachse der senkrecht stehenden Birne
eine starke Schraubenspindel befestigt und auf dieser zwei radiale Arme angeordnet,
welche an ihren Enden die beiden Schnellhämmer in Schildzapfen hängend tragen. Die
Arme werden nun langsam im Kreise herumgedreht, so daſs die Schnellhämmer die
plastische Masse zwischen Birnenmantel und einer eingesetzten Lehre feststampfen.
Mit der Drehung der Arme findet aber auch ein langsames Aufsteigen derselben an der
Schraubenspindel statt, so daſs das Futter in dünnen, langsam ansteigenden Lagen
eingestampft wird.
Gegen den Zweck der Maschinen läſst sich nichts einwenden. Es fragt sich nur, ob zur
Erreichung desselben thatsächlich so umständliche Maschinen nothwendig werden, wie
sie gerade dargestellt wurden. (Vgl. Rühle v.
Lilienstern 1879 232 * 140.)
Der basische Bessemerprozeſs verlangt ein Roheisen mit 1
bis 2 Proc. Mangan. Die Minetten von Luxemburg und Elsafs-Lothringen liefern aber
nur ein Roheisen mit 0,4 bis 0,5 Proc. Mangan, weshalb zu diesen Erzen entweder
theure Nassauer oder Siegerländer Manganerze zugesetzt werden müssen, um ein zum
basischen Prozesse geeignetes Roheisen zu erhalten. Der Preis für letzteres wird
aber dadurch nicht unerheblich vertheuert, so daſs das basische Fluſseisen nur
schwer neben dem sauren Verfahren aufkommen kann.
C. Stöckmann in Ruhrort (D. R. P. Nr. 30076 vom 30.
April 1884, abhängig von Nr. 12700, vgl. 1882 244 151)
schlägt deshalb folgendes Verfahren vor: Das flüssige, an Maugan arme Roheisen wird in eine mit Kalkzuschlag
beschickte heiſse basische Birne abgestochen und Wind durchgeblasen. Sobald die
Spektrumslinien schwächer werden, setzt man Ferromangan (Phosphor haltig oder nicht)
zu. Durch letzteres tritt eine Verzögerung in der Verbrennung des Kohlenstoffes ein,
ohne aber die Oxydation des Phosphors zu beeinträchtigen; denn das Mangan oxydirt
durch die eingeblasene Luft zu Manganoxydul und dieses hat das Bestreben, sich zu
verschlacken. Da nun aber das Silicium bereits zu Anfang des Blasens ausgeschieden
worden ist und sich mit dem Kalke verbunden hat, so bleibt nur noch die
Phosphorsäure übrig, mit welcher sich das Manganoxydul nach der Oxydation des
Phosphors verbinden kann. Ein Nachblasen soll hierbei unnöthig sein. Auſserdem soll
man bei diesem Verfahren die Hitze mit dem Spektroskop bis zu Ende verfolgen können,
weil die Linien wegen der Gegenwart des Mangans bis zu Ende sichtbar bleiben.
Das betreffende Patent ist bereits wieder erloschen.
Wahrscheinlich haben Versuche gezeigt, daſs das Vorhandensein des Manganoxyduls die
Oxydation des Phosphors, für die ein triftiger Grund nach den von Stöckmann angegebenen Gesichtspunkten nicht recht
vorliegt, nicht beeinfluſst.
Zur Herstellung schweiſsbaren Fluſseisens und
Fluſsstahles schlägt W. Mathesius in Horde (D.
R. P. Nr. 31628 vom 14. September 1884) folgendes Verfahren ein: Der basische
Bessemerprozeſs wird bis zum Beginne der Entphosphorung wie gewöhnlich geführt; dann
aber werden durch beliebige Vorrichtungen Theer, Erdöl o. dgl. reducirende Stoffe
mit dem Winde in das Eisenbad eingeblasen, um die Entphosphorung in einer Atmosphäre
zu vollenden, welche für den Phosphor in Folge der hohen Temperatur und der sehr
basischen Schlacke eine oxydirende, für die übrigen
Metalle aber eine reducirende sein soll. Auf eine
solche Schluſsfolgerung will Mathesius durch die
Erkenntniſs gekommen sein, daſs in der Mitte des Blasens eine erhebliche
Verminderung des Kalkgehaltes der Schlacken stattfinde, welche nicht anders als
durch eine Reduction des Kalkes zu Calcium zu erklären sei. Untersuchungen von
Schöpfmetall hätten denn auch thatsächlich einen erheblichen Calciumgehalt des
Metalles ergeben. Auſserdem zeigte das Spektrum sehr deutlich die Calciumlinie.
Hieraus schlieſst Mathesius, daſs zu dieser Zeit im
Eisenbade gleichzeitig eine Reduction von CaO zu Calcium und eine Oxydation von
Kohlenstoff zu CO und von Phosphor zu P2O5 stattfände. Der fertige basische Stahl enthält nur
Spuren von Calcium, weshalb also letzteres im weiteren Verlaufe des Prozesses wieder
oxydirt werden müsse, wobei gleichzeitig das Eisen verbrenne. – Sollten die
Schluſsfolgerungen betreffs der gleichzeitig oxydirenden und reducirenden Atmosphäre
nicht auf falschen Analysen beruhen?
In Fig. 10 bis
12 Taf.
17 sind die Herdschmelzöfen mit Wärmespeichern von F. W. Dick und J. Riley in
Glasgow (* D. R. P. Nr. 30899 vom 6. Juli 1884, vgl. 1884 253 * 120)
veranschaulicht. Die Oefen unterscheiden sich bekanntlich von den älteren dadurch, daſs der Ofen
selbst und die 4 Wärmespeicher über der Hüttensohle liegen und von allen Seiten
zugänglich sind. Der Ofen ist kreisförmig. Der gestampfte Herd wird von auf Trägern
ruhenden Eisenplatten unterstützt. Unter dem Herde ist ein freier Raum gelassen, um
Ausbesserungen von unten leicht vornehmen zu können. Im Herde ist ein Abstich mit
der Rinne r sowie ein Schlackenauslauf s angebracht und an den freien Seiten des Herdes sind
in den Herdwänden die Füll- und Arbeitsöffnungen a
angebracht. Auf den Herdwänden ruht das Kugelgewölbe, welches in einen Eisenring
eingebaut ist und vom Herde ohne weiteres abgenommen werden kann. In das
Kugelgewölbe münden die beiden Kanäle c, welche dem
Ofen die heiſse Luft zuführen. Die Wärmespeicher liegen paarweise einander gegenüber
und bestehen aus Blechcylindern, welche mit feuerfesten Steinen ausgefüttert sind,
wie auch der innere freie Raum mit ebensolchen Steinen ausgesetzt ist. In den
Blechcylindern sind Thüren z zur Einbringung der
feuerfesten Materialien und behufs Vornahme von Ausbesserungen angeordnet. Die
Decken der Wärmespeicher sind wie das Gewölbe des Ofens eingerichtet, so daſs auch
sie leicht abgenommen werden können. Am Boden stehen die Wärmespeicher mit den Gas-
und Luftkanälen und dem Essenkanale in Verbindung. Oben münden die zu dem Ofen
führenden Kanäle; G bedeuten die Luft-, L die Gasspeicher. Die Gaskanäle v führen durch die Herdwände in das Innere des Ofens,
so daſs die Luftströme aus den Kanälen c in fast
senkrechter Richtung auf die Gasströme treffen, wodurch eine innige Mischung von Gas
und Luft befördert wird. Der Luftstrom ist ungetheilt, der Gasstrom aber getheilt.
Der Betrieb der Oefen ist der bekannte. – In der Revue
industrielle, 1885 S. 214 sind ganz gleiche Oefen unter der Bezeichnung
„System Batho“ beschrieben.
Die Erzeugung des Fluſseisens in Herdöfen geht
gewöhnlich in der Weise vor sich, daſs nach entsprechender Vorbereitung der
Ofensohle ein Posten Roheisen mit oder ohne Eisenabfälle eingebracht wird, nach
deren Einschmelzung dann soviel weitere Eisenabfälle und Erze zugesetzt werden, bis
entnommene Proben zeigen, daſs das Bad die gewünschten Eigenschaften besitzt. Dann
gibt man die Manganmetalle zu. Man sticht hierauf den ganzen Satz mit der Schlacke ab, bessert die Sohle aus und verschmilzt
einen neuen Posten. Dieses Verfahren ist in vieler Hinsicht unzweckmäſsig, weil es
eine starke Abnutzung des Ofens, erhebliche Metallverluste, Aufwand an Arbeit und
Zeit und auch Verlust an Wärme mit sich bringt. Friedr.
Siemens in Dresden (D. R. P. Nr. 31432 vom 11. November 1884) schlägt
deshalb vor, in dem Ofen fortwährend eine gewisse geschmolzene Metallmenge zu
belassen und hiervon nur von Zeit zu Zeit die erforderlichen Mengen abzustechen,
wonach sofort der neue passend gemischte Satz eingetragen wird. Zu diesem Zwecke
wird über den gewöhnlichen Abstich noch ein zweiter höherer Abstich angeordnet, so
daſs durch diesen die Abzapfung der erforderlichen Metallmenge erfolgen kann,
während der untere Abstich geschlossen bleibt. Man könnte auch allein den unteren
Abstich benutzen; dann aber müſste derselbe, wenn der Herd noch zum Theile gefüllt
ist, geschlossen werden. Ein Abzapfen der Schlacke wäre hierbei nicht möglich; dies
geht aber wohl an bei Benutzung des höheren Abstiches.
Bei Einführung eines solchen Betriebes können die Oefen gröſser als bisher werden, da
nur ein Theil des Ofeninhaltes auf einmal abgestochen wird. Dadurch kann ein groſses
Metallbad auf dem Herde erhalten werden, welches denselben wirksam vor Zerstörung
durch die Schlacken schützt und eine gleichmäſsige Hitze über den ganzen Herd
vertheilt. Dies ermöglicht es, daſs die frisch eingebrachten Sätze schnell und
gleichmäſsig aufgelöst werden, ohne daſs der Abbrand die bisherige Höhe erreicht. Da
bei dem Abstiche nur die oberen Herdwände frei gelegt und dem unmittelbaren
Einflüsse der Hitze und der Schlacke ausgesetzt sind, so braucht man auch nur diese
Theile stark zu kühlen. Wenn Phosphor haltige Erze verarbeitet werden, können diese
Theile aus basischem Materiale bestehen.
Zur Benutzung von Kohlengrufs bei Gasgeneratoren schlägt J.
Mc Farlane in Motherwell, Lanark (Englisches Patent 1884 Nr. 4075) einen
Rost aus einer feuerfesten Platte bestehend vor, bei welchem durch Oeffnungen und
durch seitlich angeordnete Schlitze ein Gemisch von Luft und Dampf eingeblasen
wird.
J. E. Atwood in Brooklyn (D. R. P. Nr. 30951 vom 10.
September 1884) will Eisen durch Zusatz eines
Bleiamalgams reinigen. Wie dasselbe wirken soll, ist in
der Patentschrift nicht angegeben.
C. Bramall in Sheffield (Englisches Patent 1884 Nr. 586)
hat einen Schachtschmelzofen mit 4 Regeneratorkammern
zur Vorwärmung der in den Ofen eingeblasenen Luft und des Gases angegeben. Während
dieselben das eine Paar Regeneratorkammern
durchstreichen und sich in denselben erhitzen, gehen die Gichtgase durch die andere
Kammer ab. Durch Umstellung von Schieberventilen wird dann der umgekehrte Weg
vermittelt.
F. W. Gordon in Pittsburg (Nordamerikanisches Patent Nr.
308665) gibt einen Kupolofen an, welcher mit sehr stark
stechenden Düsen versehen ist; dieselben ragen in das Innere des Ofens hinein und
können durch Zahngetriebe vorgeschoben und zurückgezogen werden, so daſs der Wind
nach Belieben unter die Oberfläche des Bades oder in
die Beschickung geblasen werden kann.
Im Engineering, 1885 Bd. 39 S. 421 ist das Blockwalzwerk der Ebbw Vale
Iron Works beschrieben. Danach hat die liegende Walzenzugmaschine 2
Cylinder und überträgt ihre Bewegung durch eine Räderübersetzung von 1 : 3, durch
Kuppelmuffen und Räder mit Schrauben-Gähnen auf die beiden Walzen. Die Umkehrung der
Dampfmaschine erfolgt
durch eine Wasserkraftmaschine, deren Cylinderdurchmesser 127mm und deren Hub 317mm beträgt. Die Walzen haben einen Durchmesser von 914mm. Vor und hinter den Walzen liegen je 5
Laufrollen, welche von einer besonderen stehenden Zwillingsdampfmaschine ihren
Antrieb erhalten, so daſs die Blöcke allein durch maschinelle Kräfte zwischen die
Walzen geschoben werden. Die Laufrollen haben einen Durchmesser von 406mm und liegen mit den Mittelpunkten 679mm aus einander. Die sie bewegende Maschine hat
Cylinder von 254mm im Durchmesser; der Hub beträgt
355mm. Um die Blöcke auf den Laufrollen von
einem Kaliber zum anderen zu bringen, greifen zwischen die Rollen Daumen, welche auf
einem unter den Rollen quer beweglichen Wagen gelagert sind; letzterer wird von
einer Preſspumpe von 203mm Durchmesser und 1m,878 Hub bewegt. Die Preſscylinder zum Bewegen
der Daumen haben 152mm Durchmesser und 406mm Hub. Das Gewicht der obersten Walze wird
ebenfalls durch zwei unter dem Drucke eines Accumulators stehende Kolben
ausgeglichen. Die beiden Schrauben, welche die obere Walze auf die untere pressen,
haben einen Durchmesser von 254mm und eine
Gangtiefe von 51mm. Dieselben werden von einer
Wasserkraftmaschine mit 228mm Cylinderdurchmesser
und einem Hube von 609mm umgetrieben. Die Maschine
liegt auf der Spitze eines der Walzenständer.
Zum Glühen von groſsen Blechplatten, welche zu
Dampfkesseln verwendet werden sollen, hat W. Boyd von
der Wallsend Slipway Company in der Institution of Naval Architects in London (vgl. Engineering, 1885 Bd. 39 S. 387) den in Fig. 7 und 8 Taf. 17 gezeichneten
Ofen empfohlen. Derselbe ist an beiden Kopfseiten mit Arbeitsöffnungen versehen (der
Grundriſs Fig.
8 gibt nur die Hälfte des Ofens) und liegen an einer Langseite die
Feuerroste, von denen die mittleren schmäler als die an den Enden gelegenen sind.
Gegenüber jedem Roste liegt ein besonderer Fuchskanal mit Schieber und münden alle
Fuchskanäle in einen gemeinschaftlichen, mit dem Schornsteine in Verbindung
stehenden Kanal.
Es kommt bei Kesselblechplatten, namentlich wenn dieselben aus Fluſseisen hergestellt sind, wesentlich darauf an, daſs
die Platten, wenn dieselben vor dem Biegen zum Glühen gebracht werden, eine überall
gleichmäſsige Durchwärmung zeigen, damit die Festigkeit der Platte nach dem Biegen
an allen Stellen gleich ist. Es geht dies aus einem Beispiele hervor, über welches
W. Parker in einem a. a. O. S. 353, ferner in Stahl und Eisen, 1885 S. 255 abgedruckten Vortrage in
der gleichen Gesellschaft berichtet hat.
Ein cylindrischer Kessel von 3m,962 Durchmesser und 4m,877 Länge, welcher
für einen Druck von 10at,5 berechnet war und
dessen Bleche eine reichliche Stärke besaſsen, barst beim Probiren unter dem
hydraulischen Drucke und zwar, als derselbe in langsamer Steigerung auf 17at,9 gebracht wurde. Es zerriſs ein Stoſs
vollständig, während das angrenzende Blech noch in Mitleidenschaft gezogen
wurde.
Das Material bestand durchweg aus Herd-Fluſseisen, das durch eine
englische Firma allerersten Ranges hergestellt worden war. Alle Bleche waren auf dem
Werke der Prüfung unterzogen worden, bei welcher sie den Vorschriften des Lloyd's Register und des Handelsamtes entsprochen
hatten. Aus dem Berichte des Prüfungsbeamten der ersteren Behörde geht hervor, daſs
die Platte, welche zerriſs, bei der Probe eine Zugfestigkeit von 46,5k/qmm bei 20 Proc.
Dehnung auf 200mm Länge ergeben hatte; auſserdem
hatten sich von derselben abgeschnittene Streifen kalt fast doppelt biegen lassen,
so daſs die mechanischen Proben auf ein für den Zweck vorzüglich geeignetes Material
hingedeutet hatten. Die fragliche Platte war sehr groſs und maſs 6096 × 1676 × 31mm,7 bei einem Gewichte von 2845k. Die Platte wurde genau so wie die früheren
behandelt; unter Anwendung aller Vorsicht wurden die Löcher gebohrt, die Platte
erwärmt und in einem kräftigen Walzenpaare auf die erforderliche Biegung
gebracht.
Unter diesen Umständen war man nicht wenig erstaunt, als das
Material bereits bei einem Drucke nachgab, welcher einer absoluten Festigkeit von
10,5k/qmm
entsprach, d. i. noch nicht einem Viertel der Zerreiſsfestigkeit des ursprünglichen
Probestückes. Dazu kam noch die Erscheinung, daſs das Bruchaussehen von einer
Beschaffenheit war, welche nicht auf eine Spur von Zähigkeit oder Dehnungsvermögen
des Materials schlieſsen lieſs.Vgl. auch W. Parker 1881 241 * 1. 242 306. 1884 252 127. H. Jacobi
1883 249 523.
Da die zerrissenen Platten vor ihrer Verarbeitung mehr als die
vierfache Festigkeit als hernach im Kessel gezeigt hatten, so muſste man zunächst
auf den Gedanken kommen, daſs die Platten in irgend einer Weise beschädigt worden
waren, oder daſs bei denselben eine Veränderung in dem Materiale auf dem Wege vom
Stahlwerke bis zur Einsetzung in den Kessel eingetreten war. Man unterzog deshalb
die Prozesse, welche die Platten durchzumachen haben, einer genauen Beobachtung. Ein
Blech wurde in einem gewöhnlichen Ofen erwärmt. Der Ofen hatte einen groſsen Rost am
Ende und zwei kleinere seitlich gelegene Roste. Das Blech war aber bei seiner
Herausnahme weit davon Entfernt, sich in gleichmäſsiger Hitze zu befinden; es besaſs
in der der Thür zunächst gelegenen Stelle noch schwarze Farbe, welche allmählich bis
zum anderen Ende in dunkelroth überging. Dann wurde das Blech umgekehrt in den Ofen
gesteckt, um eine möglichst gleichmäſsige Erwärmung zu erreichen. Ein Ende der
Platte zeigte jedoch augenscheinlich immer noch gröſsere Wärme als das andere, als
die Platte in die Biegemaschine gebracht wurde. Die letztere bestand aus einem Paar
kräftiger, senkrecht angeordneter Walzen, zwischen denen die Platte 6mal durchging.
Während dabei zu Anfang die Farben der Platte von der einen Kante zur anderen von
dunkelroth oder fast schwarz bis ins Blaue spielten, war zu Ende der Arbeit die
Platte an der einen Kante ganz kalt, an der anderen dagegen noch blauwarm.Unter „blauwarm“ ist hier eine Temperatur von annähernd 3100
verstanden; sie wird dadurch zur Erscheinung gebracht, daſs man das erwärmte
Stück anfeilt, worauf die blank gewordene Stelle eine tiefblaue Farbe
annimmt, wenn die angegebene Temperatur erreicht wird.
Man kam auf die Vermuthung, daſs durch die ungleichförmige
Erwärmung in der Platte ungewöhnliche Spannungen entstanden und daſs dieselben durch
das Walzen der Platte bei einem gefährlichen Hitzegrade verstärkt worden waren, da
bekanntlich Fluſseisen brüchig wird, wenn man es in blauwarmer Hitze verarbeitet. Im
Allgemeinen wird es für richtig gehalten, dieses Material entweder in kaltem, oder
in rothwarmem Zustande, niemals aber zwischen diesen beiden Grenzen zu verarbeiten.
Fluſseisenbleche – namentlich groſse – erleiden zweifellos bei solcher Behandlung
Schäden; über die Stärke und Ausdehnung der dadurch bewirkten Spannungen weiſs man
jedoch nichts Bestimmtes. Von der in Rede stehenden zerrissenen Platte wurden
Probestäbe sowohl dicht an der Bruchstelle, als an entfernteren Stellen entnommen,
welche bei der in einer der Prüfungsanstalten des Lloyd
vorgenommenen Zerreiſsung folgende Ziffern ergaben:
Probestäbe
k/qmm
% Dehnung
S. I X.
50,6
27,34
S. C H I.
52,0
26 59
S. 2
51,8
21,27
S. C H 2 X.
49,4
23,4
S. XX.
46,8
21,8
S. IXX.
46,5
26,6
S. XXX.
48,0
28,1
S. IXXX.
47,7
27,34.
Die Probestäbe maſsen 25mm,4 und 32mm,0 im Querschnitte bei
200mm Länge.
Es ist ersichtlich, daſs die Zerreiſsfestigkeit der Platte an den
verschiedenen Stellen zwischen 46k,5 und 52k,0 und die Dehnung zwischen 21,8 und 28,1 Proc.
schwankte. Ein Unterschied von 5,6 in der Festigkeitszahl ist aber für eine Platte
aus so gleichartigem Material wie Fluſseisen ein höchst unbefriedigendes
Ergebniſs.
Von der Platte wurden ferner Proben genommen und an fünf
bedeutende und von einander unabhängige Chemiker übermittelt, von welchen folgende
Angaben erhalten wurden:
C
Si
S
P
Mn
1)
0,36
0,015
0,055
0,087
1,050
2)
0,27
0,016
0,044
0,076
0,641
3)
0,33
0,010
0,038
0,065
0,612
4)
0,30
0,018
0,044
0,063
0,648
5)
0,26
0,005
0,038
0,067
0,650.
Am meisten fällt der hohe Kohlenstoffgehalt in die
Augen, welcher für Kesselblech besonders hoch erscheint. Das Material, das man zur
Fabrikation von 13 bis 9mm dicken Blechen zu
benutzen pflegt und welches dieselben mechanischen Proben wie die dickeren Bleche
auszuhalten hat, enthält nicht mehr als 0,15 bis 0,18 Proc. Kohlenstoff und
veranlaſste diese Erscheinung weitere Versuche. Dieselben sollten Aufklärung
verschaffen, inwieweit die Walzarbeit und namentlich solche bei kaltem Materiale, da
die dünnen Bleche stets gegen Ende der Behandlung kalt werden, von Einfluſs auf die
Festigkeit und Dehnbarkeit des Materials ist. Ein Block mit etwa 0,33 Proc.
Kohlenstoff, d. i. annähernd von dem Gehalte des zerrissenen Bleches, wurde in einer
Hitze zu einem Bleche von 13mm ausgewalzt, welches
bei der Zerreiſsprobe eine Festigkeit von 55 bis 63k/qmm bei 21 bis 24 Proc. Dehnung ergab,
während dasselbe Material, wenn dasselbe nur bis zu 32mm Dicke gewalzt worden wäre, erfahrungsgemäſs bloſs 47 bis 53k/qmm Festigkeit
gezeigt haben würde.
Von der Kante der zerrissenen Platte wurden Stücke Zug-, Biege-
und Härteproben unterworfen. Die Festigkeit lag zwischen 52,8 und 53,9k/qmm, die Dehnung
war nur 13 bis 16 Proc.; das Bruchaussehen war krystallinisch und augenscheinlich
spröde. Die Stäbe bogen sich kalt bis zu einem ziemlichen Winkel, brachen aber,
nachdem sie warmroth gemacht und im Wasser abgekühlt worden waren, unter dem Hammer
beim ersten Schlage. Das Material war eben so hoch Kohlenstoff haltig, daſs es
Härtung und damit auch Sprödigkeit annahm.
Weitere Biegeproben wurden sowohl in ausgeglühtem, wie in
unausgeglühtem Zustande angestellt; erstere fielen leidlich gut aus, da Streifen von
6mm,5 Quadrat sich bis zu einem Winkel von 49
bezieh. 61° biegen lieſsen, während die ausgeglühten besser, thatsächlich fast um
180°, gebogen werden konnten. In Wasser gehärtete Streifen brachen dagegen, in
Uebereinstimmung mit den oben angeführten Versuchen, beim ersten Hammerschlage.
Die Versuche weisen darauf hin, daſs die Platte, welche nachgab,
durch die Erwärmung und Abkühlung, welcher sie behufs ihrer Biegung unterworfen
wurde, theilweise Härtung erfahren haben muſs.
Nach Parker's Ansicht muſs ein
Material, welches so hoch Kohlenstoff haltig ist, daſs es Härtung und die oben
beschriebene Kurzbrüchigkeit annimmt, auch dann, wenn es vor der Härtung hohe
Eigenschaften in Bezug auf Festigkeit und Dehnbarkeit besitzt, als ein unzuverlässiges und für den Bau von Schiffskesseln durchaus
ungeeignetes bezeichnet werden. Es scheint fast, als ob durch das Streben nach Einführung von
hoch gespanntem Dampfdruck und in Folge der damit in Verbindung stehenden Verwendung
eines Materials von höherer Festigkeit mit leidlicher Dehnbarkeit die
Schiffbautechniker unabsichtlich dazu gedrängt wurden, ein für ihre Kessel höchst
ungeeignetes und unzuverlässiges Material zu nehmen. Es scheint ferner auch
auſserhalb der Hüttenkreise die Thatsache noch nicht genug gewürdigt zu werden, daſs
mit der Dicke eines Bleches auch dessen Brüchigkeit und Unzuverlässigkeit
steigt.
Sowohl Parker, als auch die
Gesellschaft Lloyd haben stets gegen die Verwendung von
Fluſseisen mit zu hoher Festigkeit Stellung genommen. Die Vorschriften des Lloyd's Register verlangen, daſs Kesselbleche eine
Zugfestigkeit von 41 bis 47k/qmm haben sollen. Das Bestreben ist bei dieser
Vorschrift auf die Verwendung eines weichen Materials gerichtet; es ist jedoch
sowohl von Seiten der Fabrikanten, als der Constructeure der Wunsch gestellt worden,
eine Festigkeit von 50k/qmm zu erlauben.
Der oben beschriebene Vorfall und die damit verbunden gewesenen
Untersuchungen weisen deutlich darauf hin, daſs man die Verwendung eines
unzuverlässigen Materials angestrebt hat, oder sicherlich eines solchen Materials,
welches sich der gefährlichen Grenze unnöthig nähert, eine Gefährdung, die für
Dampfkessel nicht zulässig erscheint. Zur Abstellung dieses täglich sich steigernden
Uebelstandes soll die Festigkeit von dicken
Fluſseisenblechen für Kessel keinesfalls 47k/qmm (30 Tons engl. auf 1 Quadratzoll) überschreiten
und ferner die Verwendung großer Platten möglichst
vermieden werden, damit auf gleichförmige Erwärmung und
Biegung der Platten gröſsere Sorgfalt gelegt werden kann.
Zur Herstellung von Schlackenkies aus Hochofenschlacke
benutzt die Vereinigte Königs- und Laurahütte,
Actiengesellschaft für Bergbau und Hüttenbetrieb in Königshütte (* D. R. P.
Nr. 30643 vom 6. Juni 1884) eine Vorrichtung, bestehend aus einer langen, auf
Leitrollen wagerecht ruhenden Kastenkette (Paternosterwerk), welche an den beiden
Enden durch sechsseitige Wellen in bekannter Weise in Bewegung gesetzt wird. Die
einzelnen Kasten sind flach, so daſs die in dieselben eingelassene flüssige Schlacke
eine nicht zu starke Schicht bildet und dadurch Gelegenheit findet, schnell zu
erstarren. Die Schlacke läuft nun aus dem Hochofen durch eine Rinne, deren Endpunkt
sich über dem einen Wendepunkte der in Bewegung befindlichen Kastenkette befindet,
in die einzelnen Kasten hinein. Die auf jeden Kasten fallende Schlackenmenge kann
durch Veränderung der Geschwindigkeit, mit welcher sich die Kastenkette bewegt,
geregelt werden. Auf dem Wege, den die einzelnen Kasten bis zum zweiten Wendepunkte
zurücklegen, gibt die in denselben befindliche Schlacke ihre Wärme zum gröſsten
Theile an die umgebende Luft ab; diese Abgabe wird noch verstärkt durch gegen die
Auſsenseite der Kasten gespritztes Wasser. Nachdem die Schlacke hierdurch in einen
genügend zähen Zustand übergeführt ist, wird bei der weiteren Fortbewegung ein
starker Wasserstrom von oben auf die Schlacke geleitet, so daſs sie zerspringt und
am Wendepunkte der Kasten aus denselben herausfällt.
Tafeln
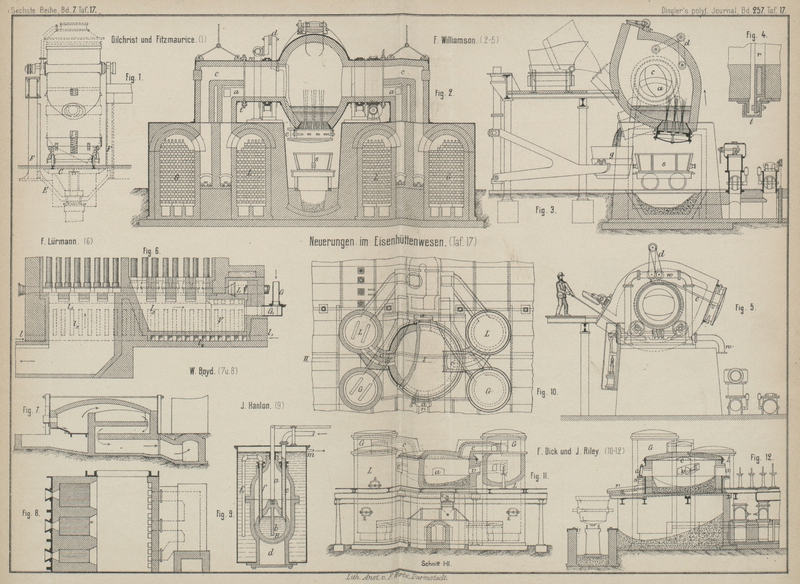