Titel: | Ueber Neuerungen im Hüttenwesen. |
Fundstelle: | Band 258, Jahrgang 1885, S. 163 |
Download: | XML |
Ueber Neuerungen im Hüttenwesen.
(Patentklasse 40. Fortsetzung des Berichtes S. 31
d. Bd.)
Mit Abbildungen auf Tafel
12.
Ueber Neuerungen im Hüttenwesen.
Th. R. Jordan in London (* D. R. P. Nr. 31900 vom 3.
Februar 1884 vgl. auch D. p. J. 1885 257 * 286) will zur Gewinnung von
Gold und Silber mittels Amalgamation die fein gepulverten trockenen Erze
durch Quecksilber treiben. In dem Troge A (Fig. 1 und 2 Taf. 12) wird
mittels Riemenscheiben d das mit Einfülltrichter t versehene Rohr b in
Umdrehung gesetzt; letzteres geht am unteren Ende in die zwei Scheiben e aus, zwischen welchen passend gekrümmte
Ausfluſsrinnen c (vgl. eine dieser Formen in
Fig. 2) zu dem
Zwecke sich befinden, um das Erzmehl in das Quecksilber zu treiben. Die mit Flügeln
g versehene Trommel f
wird durch Riemenscheibe h und Schneckengetriebe z in entgegengesetzter Richtung zum Rohre b bewegt. Durch das Rohr i
wird ein Luftstrom über das Quecksilber hingeführt, Auf der gegenüber liegenden
Seite und in der gleichen Ebene mit i liegt ein Rohr
j, durch welches die von der Oberfläche des
Quecksilbers abgeblasenen Rückstände nach dem Concentrator k getrieben werden. Letzterer besteht aus Schmiedeisen und ist in seinem
unteren Theile durch Scheidewände in eine Anzahl von Kammern getheilt. Die
Scheidewände bestehen je aus einer festen und einer mit Längsschlitz versehenen
Platte l, welche mittels Schrauben an ersterer der Höhe
nach verstellbar befestigt werden kann.
Bei Anwendung des Apparates wird der Erzstaub durch den Trichter t in das Rohr b eingeführt
und von der Flügelscheibe e in das Quecksilber
getrieben. Das in dem Quecksilber aufsteigende Erzpulver wird von den Flügeln g entsprechend aufgehalten. Sobald der Staub an die
Oberfläche des Quecksilbers gelangt, geräth er unter den Einfluſs des durch i eingeblasenen Windes, wird durch das Rohr j und über die Abtheilungen des Concentrators k getrieben, in welchem er sich je nach dem
specifischen Gewichte seiner Theilchen niederschlägt; die leichtesten, also
werthlosen derselben aber werden durch m
ausgeblasen.
Nach dem von J. Shedlock in New-Barnett (* D. R. P. Nr. 32123 vom 25. November 1884) angegebenen
Verfahren zur Behandlung von Erzen behufs Gewinnung der
Metalle aus denselben werden die gepulverten Erze
(insb. Eisenerze) mit Kohle gemischt durch eine Schicht
geschmolzenes Metall gepreſst. Der Ofenraum A
(Fig. 3
und 4 Taf. 12)
zur Aufnahme des Metallbades hat einen von hinten nach vorn geneigten Boden und der
gröſsere Theil desselben ist mit einer Platte m
überdeckt, welche von hinten nach vorn schräg ansteigt und vorn eine Oeffnung a läſst. Die Hitze zur Aufrechterhaltung der geeigneten
Temperatur des Metallbades liefert die Feuerung B,
deren Verbrennungsgase zuerst die Gasgeneratoren H und
Ueberhitzer I umspielen und sodann in Zügen C um das Metallbad gehen, um schlieſslich durch den
Schornstein S zu entweichen. Der durch Rohre J und die Ueberhitzer ziehende Dampf tritt durch die
Kammer K in die mit Kohle gefüllten Generatoren H, während das gebildete Wassergas durch Kanäle e in das Metallbad A
gelangt. Das mit Kohle gemischte Erzpulver wird durch die Schnecke im Trichter F in das Metallbad gepreſst. Die aus den Erzen
abgeschiedenen Metalle sollen sich mit dem Metallbade verbinden, während die
Schlacke durch P abgeschöpft wird und die Gase durch
Kanal O zu den Flugstaubkammern entweichen. Der Abfluſs
der Metalle aus dem Herde A erfolgt durch den Kanal v, dessen innere Mündung so tief unterhalb des Spiegels
des geschmolzenen Metalles liegt, daſs keine Schlacken in den Behälter R mit hinüberflieſsen können.
Wenn die Metalle im Herde A durch Ausscheidung der
oxydirbaren Metalle gereinigt werden sollen, so werden die Generatoren mit
feuerbeständigem Material gefüllt, die Röhren J und
Ueberhitzer I dienen zur Einführung von atmosphärischer
Luft, welche in erhitztem Zustande durch die Kanäle e
in den Herd A übertritt, hier die unedlen Metalle
oxydirt und die flüchtigen Bestandtheile nach den Condensationskammern treibt. Das
reine Metall aber wird durch den Kanal W
abgelassen.
Bei der Anlage zur Vermeidung von Rauch bei Zinköfen von
R. Lorenz in Beuthen (* D. R. P. Zusatz Nr. 32856
vom 23. Oktober 1884, vgl. 1881 242 * 432) ist, wie aus
Fig. 7 und
8 Taf. 12
zu ersehen, über den Vorlagen der Zinkdestillirröhren ein an der Längsseite des
Ofens sich hinziehender Kanal a angeordnet. Die damit
verbundenen senkrechten Kanäle b münden in
Condensationskammern d, welche unten im Bodenmauerwerk
des Ofens ausgespart sind und durch Zwischenmauern mit Oeffnungen die niedergehenden
Zinkdämpfe, den Staub und Rauch nöthigen, einen längeren Weg zu machen, ehe sie
durch den mit der letzten Kammertheilung verbundenen Kanal e in den unter allen Oefen herführenden gemeinschaftlichen Abzug f für Feuergase nach der Esse geleitet werden. Vorher
haben Staub und alle sonstigen lästigen Beimengungen in den Condensationskammern d Gelegenheit gehabt, sich niederzuschlagen und
anzuhäufen, von wo sie von Zeit zu Zeit entleert werden können.
Die aus dem Ofen entweichenden Feuergase gehen durch die Kanäle h nieder und münden in der Nähe der aus den
Condensationskammern d kommenden Dämpfe ebenfalls in
den gemeinschaftlichen Kanal f, wo sie sich mischen,
angeblich gegenseitig entzünden und verzehren. Mittels der Schieber c kann man den Abzug der Dämpfe und Gase derart regeln,
daſs die Hüttenhalle und deren Umgebung stets fast frei von Rauch, Dampf und Staub
bleiben. Selbst die aus dem Inneren der Muffeln entweichenden letzten Dämpfe können
durch die Abzugsröhren k, welche in den Kanal a einmünden, abgeführt werden. Besonders wichtig beim
Entleeren der Muffeln soll der Schieber s sein.
Zur Herstellung von reinem Zink durch Elektrolyse macht
R. P. Herrmann in Berlin (D. R. P. Zusatz Nr. 33107
vom 14. September 1884, vgl. 1884 253 32) den kaum neu zu
nennenden Vorschlag, Rohzink als Anode in das Bad eines Zinkdoppelsalzes zu hängen
unter Verwendung von Zinkblech als Kathode. (Vgl. S. 34 d. Bd.)
Zur Herstellung von Metallen schlagend, und A. Cowles in Cleveland, Ohio (Nordamerikanisches Patent
Nr. 319795 und 324658, vgl. auch D. R. P. Nr. 33672 vom 10. Juni 1885) vor, durch
die mit Kohle gemischten Erze einen elektrischen Strom zu leiten, welcher einen
Theil der Reductionsarbeit und die erforderliche Wärme geben soll. Zur Herstellung
von Legirungen kann eines der Metalle als Anode
eingeführt werden. Der Vorschlag ist kaum neu zu nennen (vgl. W. Siemens 1882 246 *
462).
Um ferner Aluminium nach Cowles (Nordamerikanisches Patent Nr. 324659) herzustellen, soll Thonerde
mit Kohlenpulver gemischt durch den elektrischen Strom reducirt werden unter Zusatz
eines Metalles, welches nachher durch Amalgamation wieder zu entfernen ist. Die
Ausführbarkeit dieses Vorschlages muſs Referent bezweifeln.
Nach J. Boguski in Warschau (Englisches Patent 1884 Nr.
3090) sollen zur Herstellung von Aluminiumbronze
Aluminiumverbindungen, z.B. Kryolith, unter Anwendung einer Kupferanode
elektrolytisch zerlegt werden. Der Vorschlag ist nicht neu (vgl. Muspratt's Chemie, 3. Aufl. Bd. 1 S. 574).
F. J. Seymour (Scientific American Supplement, 1885 S.
7824) will zur Herstellung von Aluminium 100 Th.
Zinkerze, 50 Th. Kaolin, 125 Th. Anthracit, 15 Th. Perlasche und 10 Th. Kochsalz in
Retorten aus Graphit erhitzen (vgl. 1884 254 387).
L.
Henne in Halle (* D. R. P. Nr. 32644 vom 14. Oktober 1884) will zur Herstellung von Aluminium Thonerde oder Schmirgel durch
Kalium oder Natrium reduciren, welche durch Glühen der Carbonate mit Kohle erzeugt
werden. Zu diesem Zwecke wird der viereckige Tiegel bis zu den Ansätzen a mit der Mischung des betreffenden Carbonates und
Kohle gefüllt. Auf die Ansätze a wird der mit Chamotte
gefütterte Teller b gesetzt, auf welchen die Thonerde
zu liegen kommt. Nachdem der Deckel aufgesetzt und zur Dichtung mit Lehm verstrichen
ist, setzt man das Gefäſs der Weiſsglühhitze genügende Zeit je nach seiner Gröſse
aus. Das sich entwickelnde Reductionsgas streicht durch den Zwischenraum, welcher
zwischen dem Teller b und der Innenwand bleibt, in die
Höhe und erreicht hier die glühende Thonerde, die dadurch in das entsprechende Oxyd
und Aluminium zerfällt, von welchem das Metall später durch Schlemmen o. dgl.
getrennt wird.
Textabbildung Bd. 258, S. 166Zur Gewinnung von Magnesium will Gerhard in Wolverhampton (Englisches Patent 1884 Nr.
16651) eine Lösung von 228 Th. Magnesiumsulfat und 132 Th. Ammoniumsulfat in 35000
Th. Wasser auf 65 bis 100° erwärmt durch den elektrischen Strom zersetzen. Magnesiumbronze soll erhalten werden, wenn man dem Bade
noch 550 Th. Cyankalium und 550 Th. Ammoniumcarbonat zusetzt und eine Kupferanode
verwendet. Ob sich aus wässerigen Lösungen vortheilhaft Magnesium herstellen läſst,
ist sehr zu bezweifeln (vgl. F. Fischer 1882 246 28).
P. Higgs stellt im Engineer, 1885 Bd. 60 S. 155, die bekannten Erfahrungen über die Raffinirung von Kupfer und Blei mittels Elektricität
kurz zusammen (vgl. S. 33 d. Bd.).
Die Beseitigung des Hüttenrauches soll nach A. O.
Walker in Chester (D. R. P. Nr. 32861 vom 27. Februar 1885) durch Elektricität erreicht werden. Zu diesem Zwecke
bringt er in dem Rauchkanale oder der Staubkammer zwei Stangen in Form eines Kreuzes an, welche
mit Spitzen versehen sind. Dieser Leiter wird sehr sorgfältig isolirt, was in
vortheilhafter Weise dadurch geschehen kann, daſs man ihn am Ende einer wagerechten
Metallstange befestigt, welche durch die Wand des Rauchrohres hindurchgeht. Man kann
ein Thonrohr in die Wand des Rauchrohres einschieben und die Stange durch das Rohr
hindurch führen, jedoch so, daſs sie mit demselben nicht in Berührung steht.
Auſserhalb des Rauchrohres kann die Stange auf Glasfüſsen weiter geführt werden,
welche in Glasgefäſse eintreten, ohne jedoch deren Hals zu berühren. Die Glasgefäſse
enthalten eine geringe Menge concentrirter Schwefelsäure. Diese Stange ist mit einem
Pole einer Reibungs- oder Influenz-Elektrisirmaschine verbunden, welche
hochgespannte Elektricität liefert; der andere Pol der Maschine ist mit der
Auſsenseite des Rauchrohres oder mit der Erde verbunden. Doch kann man statt dieser
Maschine auch andere bekannte Quellen hochgespannter Elektricität benutzen. Das
Ganze ist so angeordnet, daſs eine beständige Entladung der Elektricität an den
Spitzen, welche sich an der Oberfläche des Leiters befinden, in die Luft
stattfindet.
Nach W. M. Hutchings (Berg- und Hüttenmännische Zeitung,
1885 S. 253) zeigte O. J. Lodge in Liverpool in einem
Vortrage, daſs Staub und Rauch sehr rasch
niedergeschlagen werden, wenn man elektrische
Funken hindurchschlagen läſst. Dadurch wurde Walker
veranlaſst, auf seiner Bleihütte zu Bagillt in Flintshire entsprechende Versuche
auszuführen. Lieſs man die Funken einer Influenzmaschine durch einen mit Bleirauch
gefüllten Kanal schlagen, so setzte sich der Rauch sehr rasch ab. Lieſs man den
Rauch mit voller Geschwindigkeit einen kleinen Kanal durchströmen und an die Luft
austreten, so sah man beim Ausgange die Wirkung der Elektricität ebenso auffallend,
indem der austretende Flugstaub flockig wurde und bei ruhiger Luft sich schnell zu
Boden senkte. Unterbrach man plötzlich den Rauchstrom, so sah man, wie der Rauch,
welcher an den Metallspitzen vorbeigeströmt war, sich in weiterer Entfernung von
denselben rasch absetzte, indem er fast ganz aus Flocken bestand. Es kommt nur
darauf an, daſs die Isolation bis mitten im Kanäle gut ist und daſs man eine
genügende Anzahl von Metallspitzen thunlichst gleichmäſsig über den
Kanaldurchschnitt verbreitet. Die Spitzen sowie die dieselben tragenden
Metallstangen besetzen sich stark mit Flugstaub. Dies scheint aber gar keine
nachtheilige Wirkung zu haben oder höchstens erst nach längerer Zeit- sollte sich
die Nothwendigkeit zeigen, so kann sehr leicht die Einrichtung so getroffen werden,
daſs der in dem Kanäle hängende Theil des Apparates in wenigen Minuten herausgehoben
und abgebürstet werden kann.
Es werden jetzt zwei gröſsere Elektrisirmaschinen eigens ausgeführt, welche mittels
einer kleinen Dampfmaschine von 1e getrieben
werden sollen. Diese Maschinen sind stärkere Inductionsmaschinen nach Wimshurst's System und haben Glasscheiben von 1m,52 Durchmesser. Diese Maschine ist von dem
Feuchtigkeitszustande der Luft fast ganz unabhängig. Der Rauch im Hauptkanale soll
hinter einander und nach Zwischenräumen von einigen Meter zwei oder auch drei Reihen
von Metallspitzen treffen, so daſs die starke Einwirkung von der ersten Reihe noch
von den folgenden unterstützt und fortgesetzt werden soll, worauf der stark flockige
Flugstaub sich im Kanäle recht bald absetzen wird. (Vgl. Schlösser und A. Ernst 1885 257 * 287.)
E. H. Cook in Bristol (Englisches Patent 1884 Nr. 7731)
will zum Niederschlagen des Hüttenrauches in die
Abzugskanäle Schwefelwasserstoff einleiten, oder in
dieselben mit Sodarückständen getränkte Tücher
aufhängen, oder aber den Rauch über feuchte Sodarückstände leiten, aus denen durch
Einwirkung der Kohlensäure Schwefelwasserstoff entwickelt wird. Der Nachbarschaft
wird damit wenig gedient sein.
Nach einer Angabe im Génie civil, 1885 Bd. 7 S. 217 ist
es vortheilhaft, Bleierze mit geschmolzenem Roheisen zu
reduciren. Zu diesem Zwecke soll der Bleiglanz aus
dem Röstofen in eine kleine Bessemerbirne gebracht, dann aus einem Kupolofen 50 bis
80 Procent des Minerales an geschmolzenem Roheisen eingelassen werden. Die Reduction
soll sehr rasch beendigt sein, ohne daſs erhebliche Mengen Bleirauch entweichen.
J. W. Simpson in Newark (Nordamerikanisches Patent Nr.
323222). will die Erze mit einer Lösung von Cyankalium,
kohlensaurem Ammonium und Chlornatrium behandeln und aus der Lösung Gold, Silber und Kupfer
fällen.
Bei der Gewinnung von Gold und Silber durch Amalgamation
will F. Hollick in New-York (Nordamerikanisches Patent
Nr. 314578) statt Quecksilber eine schmelzende Legirung von Blei, Zinn, Zink,
Wismuth und Quecksilber verwenden.
Nach J. Simpson und E. W. Parnell in
Liverpool (D. R. P. Nr. 33097 vom 30.
December 1884) werden Schwefelantimon, Gold und
Silber haltige Erze gepulvert in eine heiſse Lösung von Schwefelnatrium
oder Schwefelcalcium eingetragen. Die Sulfantimoniatlösung wird von dem
Niederschlage getrennt und das Schwefelantimon durch Zusatz von Säure gefällt. Statt
dessen kann man das Erz auch mit einer kalten Lösung von Schwefelammonium ausziehen
und dieses dann abdestilliren. Um das etwa mit in Lösung gegangene Gold zu erhalten,
werden aus der Sulfantimoniatlösung zunächst nur etwa 2 Proc. Schwefelantimon
gefällt, welche das gesammte Gold enthalten. Der Erzrückstand wird zur Gewinnung des
übrigen Goldes und des Silbers in passender Weise weiter behandelt.
W. Hampe (Chemikerzeitung, 1885 S. 1334) hat zur Bestimmung des Schwefels 3 Mansfelder Kupfer folgender
Zusammensetzung untersucht:
I
II
III
Kupfer
98,9048
99,5200
99,6125
Silber
0,0287
0,0280
0,0292
Blei
0,0208
0,0232
0,0200
Arsen
0,0223
0,0228
0,0172
Antimon
0,0059
0,0031
0,0023
Nickel
0,2200
0,2142
0,2112
Eisen
0,0029
0,0039
0,0039
Sauerstoff
0,7464
0,1546
0,0752
Schwefel
0,0036
0,0021
0,0024
–––––––
–––––––
–––––––
99,9627
99,9719
99,9739.
I übergares Kupfer, nach 9stündigem Einschmelzen und
4stündigem Oxydiren; II dicht gepoltes Raffinad, nach 1½stündigem Dichtpolen; III
zähe gepoltes Raffinad, nach 1 stündigem Zähepolen.
Je 50g Feilspäne wurden mit
einer Lösung von 350g CuCl2.2NH4C1.2H2O, 200cc
Salzsäure und 1l Wasser bei mäſsiger Wärme gelöst,
dann wurde filtrirt. Der geringe schwarze Rückstand enthielt 0,0022 bezieh. 0,0007
und 0,0014 Proc. Schwefel. Diese Ergebnisse stellen es auſser Zweifel, daſs Kupfer
trotz eines Sauerstoffgehaltes auch noch Halb-Schwefelkupfer enthalten kann;
besonders auffallend ist dies bei dem hohen Sauerstoffgehalte von 0,7464 Proc. des
übergaren Kupfers. Da in allen Fällen der als Halb-Schwefelkupfer gefundene
Schwefelgehalt geringer ist als die nach der Chlormethode gefundenen Gehalte, so
erscheint es wahrscheinlich, daſs die Kupfer neben Halb-Schwefelkupfer auch noch
eingeschlossene Schwefligsäure enthalten.
Versuche von Föhr (Berg- und Hüttenmännische Zeitung,
1885 S. 382) bestätigen, daſs das Silberfeintreiben
vortheilhafter ist als Abtreiben und Feinbrennen. Auf der Victor-Friedrichshütte bei
Harzgerode werden die Erze von Neudorf verhüttet, welche aus Silber haltigem
Bleiglanz mit wenig Fahlerz, Bournonit, Zinkblende und Kiesen bestehen. Das
beibrechende Gangmaterial besteht aus Spatheisenstein, Fluſsspath, Quarz und
Thonschiefer. Der Durchschnittsgehalt der Erze beträgt etwa 40 Proc. Blei, 0,6 bis
0,7 Proc. Silber und 0,1 Proc. Kupfer. Die Erze werden zum Theile ungeröstet als
sogen. „Rohschmelzer“ verschmolzen, zum gröſsten Theile jedoch geröstet einer
vereinigten Röstreductions- und Niederschlagsarbeit unterworfen. Das Werkblei wird
durch Zink entsilbert, der Zinkschaum nach der Flach'schen Methode mit sauren und an Eisen reichen Zuschlägen verschmolzen
und das dabei erhaltene Reichblei in Posten von 10000k in deutschen Treiböfen feingetrieben. Früher wurde das Reichblei bis
etwa 940 im Treibofen gebracht und dann in Testen unter der Muffel in Barren von
etwa 18k feingebrannt.
Beim Feintreiben von 20000k Reichblei mit 116k,44 Silber wurden erhalten:
111,24k
Silber mit 998 auf 1000 fein
=
111,02k fein.
400,0
grober Abstrich mit 10 Ag
=
0,40
2450,0
Antimonabstrich mit 0,5 Ag
=
0,12
2500,0
Herd mit 9,0 Ag
=
2,25
4000,0
Schuppenglätte mit 1,0 Ag
=
0,40
1500,0
gemahlene Glätte mit 1,3 Ag
=
0,20
11000,0
unreine Brockenglätte mit 1,6 Ag
=
1,76
500,0
Endglätte mit 4,0 Ag
=
0,20
–––––––
––––––––
23461,24k
116,35k fein.
Das Silberfeintreiben wird auf der Victor-Friedrichshütte in zwei deutschen Treiböfen
von 2m,10 Durchmesser ausgeführt. Auf den Herd
werden erst 7500k Reichwerke gebracht, bei
möglichst niedriger Temperatur eingeschmolzen, der Kupfer haltige und an Silber
reiche grobe Abstrich entfernt, stärker gefeuert, der geschmolzene Antimonabstrich
abgezogen und dann bis zu reiner Glättebildung getrieben. Hierauf wird die
Glättegasse zugedämmt, die Feuerung zurückgehen gelassen, noch 2500k Reichblei nachgetragen, wieder der grobe und der
Hartbleiabstrich getrennt entfernt und bis zum Blicke getrieben. Dann wird stärker
gefeuert und schwächer geblasen und nach einigen Minuten etwas Herd auf die
Metallfläche gestreut, wodurch diese sich rasch reinigt. Das Silber kann so leicht
auf 998 fein gebracht werden; auſserdem bewirkt das Aufstreuen von Herd eine starke
Strömung im Silberbade, so daſs die Legirung innig gemischt wird und der Kuchen
später beim Zerschlagen überall dieselbe Feine zeigt. Vor dem Herdaufstreuen wird
das Gebläse abgestellt, welches überhaupt nun nicht mehr in Thätigkeit kommt. Ebenso
läſst man nun das Feuer zurückgehen. Der Silberkuchen erkaltet langsam bei
geschlossener Haube, oder wird durch Wasser gekühlt und geht in Stücke geschlagen in
den Handel. Für ein Treiben von 10000k Werke
werden etwa 1 Raummeter Holz und 1600 bis 1700 Reisig wellen verbraucht; die
Herdmasse besteht aus 3. Th. gemahlenem Kalkstein, 1 Th. feinem Thon und 2 Th.
ausgelaugter Holzasche.
Um den Einfluſs des Härtens und Hämmerns auf Guſsstahl
festzustellen, hat Osmond (Comptes rendus, 1885 Bd. 100
S. 1228) je 1g,5 besonders weichen Guſsstahl (I),
mittelharten (II) und für Werkzeuge bestimmten Guſsstahl (III), sowie schwedisches
weiſses Eisen (IV) in 500cc einer gesättigten
Lösung von Kupferoxydammoniak gelöst und die bei der Reaction CuCl2 + Fe = FeCl2 + Cu
auftretende Wärmeentwickelung bestimmt. Die Temperaturzunahme betrug je nach der
Behandlung der Proben (das Weiſseisen wurde in Schalen abgeschreckt):
Temperaturzunahme
Probe
Kohlenstoff-gehalt
Nach-gelassen
Hart-geschlagen
Ab-geschreckt
I
0,17
2,151
2,247
–
II
0,54
2,111
2,207
2,222
III
1,17
1,895
2,018
2,056
IV
4,10
1,419
–
1,632
Osmond glaubt das Eisen trete in
zwei Abarten einer krystallinischen (α) und einer
amorphen (β) auf; erstere soll beim Erhitzen auf
Rothglut und langsamen Abkühlen entstehen und durch bleibende Formänderung bei
niederer Temperatur sowie durch plötzliche Abkühlung, jedoch nur in Gegenwart von
Kohlenstoff, Mangan und Wolfram, in die β-Abart
übergehen. (Vgl. Troost und Hautefeuille 1875 218 274. Tresca 1884 251 * 97.)
Um den Verbindungszustand des Kohlenstoffes im Stahl
festzustellen, hat F. Abel nach Engineering, 1885 Bd. 39 S. 200 verschiedene Proben Cementstahl und
Guſsstahl, gehärtet und angelassen, mit einer Lösung von Kaliumbichromat und
Schwefelsäure behandelt und das ungelöst bleibende Eisencarbid bestimmt. Aus
ungeschmolzenem Cementstahle blieben z.B. angelassen 13,5 Proc., gehärtet nur 0,98
Proc. Carbid zurück, aus Guſsstahl 5 bis 6 Proc. Das aus blau und strohgelb
angelassenem Stahle ausgeschiedene Kohlenstoffeisen, sowie das aus geglühtem und
langsam erkaltetem Stahle entspricht der Formel Fe3C. Beim Härten des Stahles hindert die plötzliche Abkühlung die Bildung der
Verbindung.
Nach Th. Turner (Chemical News, 1885 Bd. 52 S. 5) erhöht ein Siliciumgehalt des Guſseisens bis zu 2,5
Proc. die Festigkeit desselben, begünstigt die
Abscheidung des Kohlenstoffes als Graphit und die Bildung glatter und schöner Güsse. Ein gröſserer Siliciumgehalt macht das Eisen
brüchig.
A. Ledebur bespricht in Stahl
und Eisen, 1885 * S. 121 das Kupolofenschmelzen in
alter und neuer Zeit.
Noch im Anfange des 18. Jahrhunderts wurde selten umgeschmolzenes
Eisen verwendet, welches in Tiegeln geschmolzen wurde. Reaumur (1722) bemerkte, daſs das Eisen voraussichtlich auch in
unmittelbarer Berührung mit brennenden Kohlen zum Schmelzen gebracht werden könne.
Etwa um dieselbe Zeit fingen Hausirer an, in tragbaren Oefen Eisen zu schmelzen, um
Töpfe daraus zu gieſsen. Der erste feststehende Schachtofen scheint 1790 in England
von Wilkinson ausgeführt worden zu sein. Die Höhe
dieser Oefen betrug 1,5 bis 2m,5, ihr Grundriſs
war kreisförmig oder häufig länglich und durch zwei oder drei Düsen wurde der Wind
zugeführt. Häufig gab man dem Ofenschachte Trichterform, d.h. lieſs denselben nach
oben sich erweitern, so daſs eine sehr weite Gicht entstand. Um die Gicht vor
vermeintlichen Wärme-Verlusten und die Arbeiter vor der strahlenden Hitze der
Gichtflamme zu schützen, überdeckte man die Gicht vermuthlich mit einer gemauerten
Kuppel „cupola“, in deren Scheitel die
Austrittsöffnung für die Gase angebracht war, und benannte alsdann hiernach den
ganzen Ofen.
In Oberschlesien wurde der Kupolofenbetrieb in den letzten Jahren
des vorigen Jahrhunderts eingeführt. Vermuthlich war es Gleiwitz, welches mit der
Einführung des Kokeshochofenbetriebes auch die neuen Oefen zum Umschmelzen des
Roheisens zuerst in Anwendung brachte; in Rheinland-Westfalen ging die Antonienhütte
den übrigen Werken voran. Bereits 1804 war dort ein Kupolöfen, welcher mit
Holzkohlen geheizt wurde, mit befriedigendem Erfolge in Benutzung. In den zwanziger
Jahren waren die Kupolöfen ganz allgemein verbreitet.
Die Leistungsfähigkeit der früheren Kupolöfen war sehr gering, der
Brennstoffverbrauch sehr hoch. Bei dem erwähnten Kupolöfen der Antonienhütte setzte
man auf 50 Pfund Kokes 65 Pfund Roheisen und war recht befriedigt von diesem
Ergebnisse; 30 Jahre später, in den 40er Jahren, betrug nach Karstens Angabe der Kokesverbrauch für 100 Pfund
umzuschmelzendes Roheisen durchschnittlich 47,6 Pfund ohne die Füllkokes. In den
50er und selbst noch in den 60er Jahren waren Kupolöfen, welche mehr als 30 Pfund
Kokes für 100 Pfund Roheisen gebrauchten, durchaus keine Seltenheit. Dies erklärt
sich daraus, daſs in Folge starker Windpressung und enger Düsen die Kohle nur zu
Kohlenoxyd verbrannt wurde. Allerdings wurde in Folge dessen das Eisen beim
Einschmelzen wenig oder gar nicht geändert. Erst allmählich machte man die
Beobachtung, daſs gröſsere Einströmungsquerschnitte und geringere Windpressung
günstig für die Ersparung von Brennstoff sei. Dem entsprechend fand Ebelmen (1842 85 39) in den
40er Jahren das Verhältniſs CO2 : CO noch zu 0,83,
während F. Fischer (1879 231
38) bei neueren Kupolöfen durchschnittlich 2,5 nachwies. Ebelmen fand einen Brennstoffverbrauch von 18 bis 20k, Fischer von 7k Kokes auf 100k
Eisen. Da Holzkohle leichter Kohlenoxyd bildet, so stellt sich dichter Kokes
vortheilhafter.
Je reichlichere Kohlensäurebildung in einem Kupolöfen stattfindet, mit je weniger
Brennstoffaufwand man also das Schmelzen durchzuführen im Stande ist, desto stärker
wird die Oxydationswirkung des Ofens auf das schmelzende und niedersickernde
Roheisen ausfallen, desto mehr wird die Beschaffenheit desselben verändert werden.
Schmilzt man, wie gewöhnlich, graues Roheisen, so verliert dasselbe einen Theil
seines Siliciumgehaltes und wird bei jedem Umschmelzen härter, weiſser. Die
Anwendung dieser Kupolöfen mit äuſserst geringem Brennstoffverbrauche und stark
oxydirender Gasatmosphäre ist daher überhaupt erst möglich geworden, seitdem man
gelernt hat, Roheisensorten im Hochofen darzustellen, welche einen Ueberschuſs des
beim Umschmelzen theilweise austretenden Siliciums enthalten. Liegt die Aufgabe vor,
die Zusammensetzung des zum Umschmelzen bestimmten Roheisens möglichst unverändert
zu erhalten, wie z.B. in vielen Bessemerhütten, so wählt man auch jetzt noch einen
höheren Brennstoffsatz und erzeugt dadurch eine an Kohlenoxyd reichere
Gasatmosphäre.
Wesentlich ist ferner der Einfluſs der Schlacke, welche ihrerseits wiederum abhängig
ist von dem Aschengehalte des Brennstoffes, der Zusammensetzung der Asche und der
Menge und Zusammensetzung des Zuschlagkalksteines. Auch die Menge des dem Roheisen
anhaftenden Sandes sowie die Menge und Zusammensetzung der aus dem Roheisen durch
Oxydation ausscheidenden Stoffe kommt hierbei in Betracht. Die Kokes, welche fast
regelmäſsig den Brennstoff des Kupolofenbetriebes bilden, pflegen 8 bis 12 Proc.
Asche zu enthalten. Gewöhnlich liefern sie, zumal wenn denselben noch Kieselsäure
aus dem am Roheisen haftenden Sande zugeführt wird, eine ziemlich dickflüssige
Schlacke, welche an den Ofenwänden sich ansetzt und schwer aus dem Ofen zu entfernen
ist. Schon im Anfange dieses Jahrhunderts pflegte man deshalb den Gichten etwas
Kalkstein zuzusetzen. Die Schlacke wird dadurch leichtflüssiger, bildet über dem
Roheisen eine schützende Decke und läſst sich ohne Schwierigkeit durch Abstechen aus
dem Ofen entfernen. Der Kalk hat aber noch die Aufgabe, den Schwefel aus den Kokes,
welcher nicht als Schwefligsäure entweicht (vgl. 1879 231
39) aufzunehmen, damit er nicht das Eisen verdirbt. Dies bestätigen die
Schlackenuntersuchungen von F. Fischer und folgende
drei Analysen von Ledebur:
I
II
III
Kieselsäure
60,05
46,70
37,05
Thonerde
18,00
9,30
11,08
Eisenoxydul
4,61
7,36
1,59
Manganoxydul
8,29
2,79
14,09
Kalk
6,29
31,44
29,64
Magnesia
0,25
0,15
0,79
Kali
–
0,72
–
Schwefel
0,33
0,40
1,58
Calcium
0,41
0,50
1,98.
I Kupolofenschlacke früherer Zeit. II Schlacke eines
versuchsweise mit Zusatz von Steinkohle und viel Kalk betriebenen Krigar'schen Ofens. III Schlacke von weiſsem Roheisen
für den basischen Bessemerprozeſs.
Bei einer an Kalk und Mangan reichen Schlacke kann auch das Eisen Schwefel abgeben;
das Eisen III enthielt z.B. vor dem Schmelzen 0,42, nach dem Schmelzen nur noch 0,09
Proc. Schwefel. Der Kalkzuschlag sollte so bemessen werden, daſs die gebildete
Schlacke 20 bis 30 Proc. Kalk enthält.
Der Eisengehalt der Kupolofenschlacke stammt theils aus der Asche, theils aus dem
Roheisen; letzteres wird um so stärker oxydirt, je weniger Kohlenoxyd gebildet wird,
je besser also der Brennstoff ausgenutzt wird, wie dies z.B. die Schlacken der
Hannoverschen Kupolöfen zeigen. Je hoher aber der Mangangehalt des eingesetzten
Roheisens ist, desto stärker wird dieser selbst durch die Oxydationswirkung
betroffen, desto mehr werden nicht allein das Eisen, sondern sogar das Silicium vor
der Oxydation geschützt. Ein an Mangan reiches Roheisen wird deshalb stets eine an
Eisen ärmere Schlacke liefern als ein wenig Mangan enthaltendes Eisen; dieser
Umstand erklärt neben höheren Brennstoffverbrauch den niedrigen Eisengehalt der
beiden an Mangan reicheren Schlacken Nr. I und III. Bei dem Schmelzen in Ofen Nr.
III enthielt das Roheisen vor dem Schmelzen 2,48 Proc. Mangan, nach dem Schmelzen
nur 1,32 Proc.
Daſs eine Schlacke, welche 15 oder mehr Proc. Eisenoxydul enthält, bei längerer
Berührung mit dem geschmolzenen Eisen selbst noch oxydirend auf dasselbe einwirken,
insbesondere auch den Siliciumgehalt des grauen, für die Gieſserei bestimmten
Roheisens abmindern könne, unterliegt wohl keinem Zweifel. Auch in dieser Beziehung
wirkt ein reichlicher Kalksteinzuschlag günstig, indem er den Eisenoxydulgehalt der
Schlacke verdünnt und somit die Einwirkung desselben auf den Siliciumgehalt des
Roheisens abschwächt.
Wenn man die Beschaffenheit des in einem Kupolofen geschmolzenen Eisens von
verschiedenen Abstichen mit einander vergleicht, so wird man, besonders wenn graues
Roheisen für die Gieſserei geschmolzen wurde, nicht selten deutliche Abweichungen
wahrnehmen können. Insbesondere häufig zeigt sich, daſs das Eisen des ersten
Abstiches härter, zum Weiſswerden geneigter ist als das später erfolgende.
Die Unterschiede in dem Verhalten des zuerst und des später abgestochenen Eisens
werden geringer ausfallen, wenn man, wie es in den meisten für Darstellung
gewöhnlicher Handelsguſsware betriebenen Gieſsereien üblich ist, einen
Roheiseneinsatz wählt, dessen Silicium- und Kohlenstoffgehalt gröſser ist, als es
zur Erzielung der höchsten Festigkeit wünschenswerth sein würde. Man kann alsdann
mit geringerem Brennstoffaufwande, also in stärker oxydirender Atmosphäre, schmelzen
und erhält immer noch ein leicht bearbeitbares graues Guſseisen, welches auch in
dünneren Querschnitten mit Graphitausscheidung erstarrt. Ist zu Anfang des
Schmelzens die Oxydationswirkung sehr stark, so wird das Silicium besonders
verbrennen und das zuerst folgende Eisen in Folge des geringeren Siliciumgehaltes
weniger zur Graphitausscheidung neigen als das spätere. Daſs das erste Eisen
zuweilen reicher an Kohlenstoff ist, erklärt sich aus dem zum Anblasen des Ofens
erforderlichen reichen Aufwände von Füllkokes, durch welche das schmelzende Eisen
hindurchsickert. Die ausgedehnte Berührung mit den Kokes befördert die Aufnahme von
Kohlenstoff; später verringert sich das Verhältniſs zwischen Brennstoff und Eisen,
die Kohlenstoffanreicherung im Eisen hört auf.
Immerhin bleiben für den Kupolofen noch manche Fragen zu erledigen, wie Ledebur bemerkt. Häufigere Untersuchungen der
chemischen Veränderungen, welche das Eisen im Kupolofen erfährt, der Schlacken und
der entweichenden Gichtgase würden nicht allein wissenschaftlichen Werth besitzen,
sondern auch dem Praktiker manchen nützlichen Fingerzeig zu geben im Stande
sein.
Ledebur berichtet ferner (daselbst S. 370) über das Verhallen des Mangans beim Tiegelschmelzen. In der
Guſsstahlfabrik zu Dohlen wurden verschiedene Einsätze mit und ohne Mangan
verschmolzen. Die verwendeten Rohstoffe hatten folgende Zusammensetzung:
C
Si
Mn
Rohstahl von Schmalkalden
1,08
0,15
0,35
Rohstahl aus den Alpen
0,66
0,00
0,09
Manganeisen
6,61
0,69
72,76
Hieraus und aus den gegenseitigen Gewichtsverhältnissen dieser Materialien in den
Einsätzen wurde die Zusammensetzung der letzteren berechnet, während die
Zusammensetzung der geschmolzenen Erzeugnisse durch unmittelbare Untersuchung
gefunden wurde. Es ergab sich hierbei folgendes:
C
Si
Mn
I)
Einsatz aus 25 Th. Alpiner und 5 Th.
Schmalkaldener Rohstahl
0,73
0,02
0,13
Schmelzerzeugniſs
0,75
0,08
0,18
II)
Einsatz aus 24 Th. Alpiner, 4 Th.
Schmalkaldener Rohstahl nebst 1 Th. Manganeisen
0,92
0,04
2,63
Schmelzerzeugniſs
2,81
0,37
1,32
III)
Einsatz aus 20 Th. Schmalkaldener und 10 Th.
Alpiner Rohstahl
0,94
0,10
0,26
Schmelzerzeugniſs
0,74
0,10
0,26
IV)
Einsatz aus 19 Th. Schmalkaldener, 9 Th.
Alpiner Rohstahl nebst 1 Th. Manganeisen
1,14
0,12
2,76
Schmelzerzeugniſs
2,86
0,47
1,53
Während also bei den beiden an Mangan armen Einsätzen I und III keine oder eine nur
sehr unwesentliche Anreicherung des Kohlenstoff- und Siliciumgehaltes eintritt,
zeigt sich beim Schmelzen der zwei an Mangan reichen Einsätze II und IV
übereinstimmend eine Zunahme des Kohlenstoffgehaltes von etwa 1,8 Proc. und des
Siliciumgehaltes von 0,3 Proc. Die Zunahme ist so bedeutend, daſs thatsächlich
Roheisen entstand; ein Versuch, die Könige zu schmieden, miſslang. Mangan befördert
somit die Aufnahme von Kohlenstoff und Silicium durch den Stahl. Gibt man aber einen
Braunsteinzusatz zu dem gewöhnlichen Einsatze, so kann Silicium nicht eher reducirt
und vom Stahle aufgenommen werden, bis der gröſste Theil des Mangans aus dem
zugesetzten Braunstein reducirt worden ist; hierin unterscheidet sich die Wirkung
eines Braunsteinzusatzes sehr wesentlich von derjenigen eines Zusatzes an
metallischem Mangan. Bei Braunsteinzusatz erfolgt ein Mangan haltiger, aber Silicium
armer Stahl- bei Manganzusatz ein zwar ebenfalls Mangan haltiger, aber zugleich auch
an Silicium und Kohlenstoff reicherer Stahl als im ersteren Falle. In den meisten
Fällen dürfte also ein Braunsteinzuschlag vor dem Manganzusatze den Vorzug
verdienen.
B. Platz bespricht in Stahl und
Eisen, 1885 S. 471 die chemischen Vorgänge beim
Glühen und Tempern von Roheisen. Wenn Roheisen längere Zeit einer starken
Glühhitze ausgesetzt wird, so erleidet es eine Entkohlung, auf welchem Vorgang
bekanntlich die Tunner'sche Glühstahlbereitung beruht.
Dabei vollzieht sich ein Feinprozeſs, durch welchen Silicium verschlackt wird und
aussaigert. Nachfolgende Analysen zeigen, daſs auch Phosphor vor der vollständigen
Oxydation des Eisens der Aussaigerung unterliegt, wenn die Temperatur der Glühhitze
hoch genug ist, um ein Ausschmelzen des sich bildenden Eisenpyrophosphates bewirken
zu können. Diese Thatsache berechtigt zu der Annahme, daſs es möglich sein müſste,
nach dem Tunner'schen Glühstahlverfahren ein stark
Phosphor haltiges Roheisen zu entphosphoren, wenn man das oxydische Product nach dem
Glühen einem geeigneten Schweifsprozesse unterzieht. Freilich dürfte ein solches
Verfahren heute kaum praktisch verwerthbar sein, da auch die Tunner'sche Herstellungsweise nur kurze Zeit ein kümmerliches Dasein
gefristet hat.
Am oberen Theile einer Kokesofenthür war das Eisen auſsen unversehrt, in der Mitte
stark verbrannt, die innere Seite war von einer dicken Glühspanlage bedeckt, welche
von unebener Oberfläche war und sich anscheinend im geschmolzenen Zustande befunden
haben muſste. Das verbrannte Eisen enthielt 81,25 Proc. Eisen, der Glühspan 60,84
Proc. Deren Zusammensetzung, auf den Eisengehalt des gesunden Eisens berechnet,
lieferte:
Gesund
Verbrannt
Glühspan
Eisen
90,82
–
–
Silicium
2,57
2,09
5,79
Mangan
0,88
0,86
1,16
Phosphor
1,71
1,17
4,19.
Danach zeigt das verbrannte Eisen eine Abnahme, der Glühspan
eine bedeutende Zunahme des Gehaltes an Silicium, Mangan und Phosphor.
Wahrscheinlich war der verbrannte Theil ungleichartig zusammengesetzt und zwar
derart, daſs nach dem Glühspane zu eine allmähliche Abminderung des Gehaltes der in
Frage stehenden Bestandtheile stattfand.
Die Innenseite eines Temperglühtopfes bedeckte eine
dünne Lage Glühspan, die Auſsenseite dagegen eine stärkere, welche rissig,
aufgebläht und stellenweise abgeblättert war. Der Kern war gleichmäſsig verbrannt,
von stumpfgrauer Farbe und dichtem, feinkörnigem Bruche. Es enthielt:
Glühspan
Kern
wirklich
umgerechnet
Eisen
86,94
66,85
–
Silicium
2,06
2,72
3,54
Phosphor
0,28
0,52
0,68.
Ein Glühcylinder war am Muffenrande noch gesund, mitten
geborsten. Die Analyse ergab:
Gesund
Verbrannt
Glühspan
umgerechnet
Eisen
91,54
–
–
Silicium
1,84
1,73
1,36
Phosphor
0,85
0,45
0,12
Mangan
0,73
0,68
0,79.
Es scheint, daſs das Eisensilicat leichter schmelzbar ist als das Phosphat, daſs aber
letzteres von einer gewissen Temperaturgrenze an leichtflüssiger ist.
Ein Stück von einem Glühgefäſse zeigte im Bruche vier
Schichten: einen stumpfgrauen Theil mit eingesprengten weiſsen Blättchen aus
verbranntem Eisen (I), einen 4mm breiten Streifen
von weiſsem grobkrystallinischem Eisen (II), dann einen dunkelgrauen Theil,
verbrannt (III) und schlieſslich Glühspan (IV). Die Bestandtheile der letzeren, auf
den Eisengehalt von I bezogen, ergaben folgende Zahlen:
I
II
III
IV
Eisen
88,31
–
–
–
Silicium
2,70
0,15
1,83
3,41
Phosphor
0,96
0,98
0,58
–
Mangan
0,68
0,05
–
–
Die Glühhitze war somit hoch genug, das Eisensilicat in Fluſs
zu bringen, hat aber die zum Ausschmelzen des Phosphates erforderliche Höhe nicht
erreicht. Der Phosphor war in allen Proben als Phosphorsäure zugegen.
Beim Glühen von Roheisen in einer oxydirenden Atmosphäre verbrennen somit Silicium
und Phosphor nicht gleichzeitig mit Eisen und entsprechend ihrem Mengenverhältnisse
zu demselben, sondern ihre Oxydation ist längst beendet, wenn das Eisen erst
theilweise verbrannt ist; unter Umständen beträgt hierbei die Menge des verbrannten
Eisens nur so viel, als zur Bildung der Verbindungen von FeO oder Fe2O3 mit Kieselsäure
und Phosphorsäure erforderlich ist. Ob die Oxydation in einer bestimmten Reihenfolge
und ob sie vor der des gebundenen Kohlenstoffes
erfolgt, mag dahingestellt bleiben. Bei genügender Temperatursteigerung saigern die
entstandenen Eisensilicate und Phosphate aus dem Roheisen aus.
Diese Wahrnehmungen erklären auch das Zerspringen und die rasche Abnutzung von Heizkörpern. Bei den Oxydationsvorgängen
in Roheisen entsteht nicht bloſs durch Sauerstoffaufnahme seitens des Siliciums und
Phosphors eine bedeutende Raumvergröſserung und dadurch eine Spannung in den
Massetheilchen des Eisens, sondern vor Allem bewirkt das Aussaigern der
Oxydverbindungen eine Lockerung des Gefüges, welche bei eintretenden
Temperaturschwanklingen und Erschütterungen leicht ein Bersten der Gefäſse
herbeiführen kann. Ferner vermögen die Verbrennungsgase in die entstandenen
Hohlräume und Saigerkanäle unbehinderter einzudringen und ihre zerstörenden
Oxydationswirkungen auf das noch gut gebliebene Eisen um so rascher zu vollenden. Es
treten jedoch diese chemischen Vorgänge erst dann ein, wenn der betreffende
Gegenstand einige Zeit im Gebrauche befindlich, also den Heizgasen ausgesetzt
gewesen war. Diese Erklärungen stimmen auch mit den Erfahrungen der Praxis überein,
da diese festgestellt hat, daſs ein möglichst niedriger Phosphor- und ein mäſsiger
Siliciumgehalt auf die Dauerhaftigkeit von Winderhitzungsröhren von günstigstem
Einflüsse sind. Hiernach sollte man für Heizkörper ein Roheisen verwenden, welches
möglichst wenig Phosphor und Mangan und nur so viel Silicium enthält, als zur
Ausscheidung von Graphit, dem besten Schutzmittel des Eisens, erforderlich ist.
Um festzustellen, ob bei der Herstellung von schmiedbarem
Guſs durch oxydirendes Glühen in Metalloxyden, statt in atmosphärischer
Luft, dieselben chemischen Einflüsse obwalten, und von dem Gesichtspunkte ausgehend,
daſs solches Eisen durch Ausschmieden in Weiſsglühhitze von den allenfalls
entstandenen Silicium- und Phosphorverschlackungen befreit werden müſste, wurde
weiſses, in der Mitte schwach melirtes Roheisen in 2cm dicken Würfeln in einen guſseisernen Tiegel mit Eisenoxyd (purple ore) eingepreſst, hierauf der Tiegel in
feuerfeste Masse eingeschlagen und in einen Brennofen mit 10tägigem Gange für
feuerfeste Steine
eingesetzt. Nach Ablauf der 10 Tage wurde der Tiegel herausgenommen, seines Inhaltes
entleert, neuerdings mit denselben Eisenstücken, aber mit frischem Eisenoxyd
beschickt und abermals in den Brennofen eingesetzt. Dies wurde noch ein 3. Mal
vorgenommen, wobei die Ofenhitze so hoch stieg, daſs der guſseiserne Tiegel eine
starke Formveränderung erlitt. Das in dieser Weise hergestellte schmiedbare
Guſseisen war im Bruche durchaus weiſs und von grobkrystallinischer Structur, ferner
sehr weich und in der Hitze gut schmiedbar, jedoch stark kaltbrüchig. Geschmiedet
und ausgehämmert zeigte es den dichten, feinkörnigen Bruch von Werkzeugstahl. Vor
und nach dem Glühen hatte es folgende Zusammensetzung:
Vor
Nach
Eisen
–
97,808
Silicium
0,917
0,940
Phosphor
0,355
0,361
Mangan
0,803
0,819
Kohlenstoff
2,826
Spur.
Phosphor und Silicium haben also nicht abgenommen, sind
vielmehr noch vollkommen unoxydirt vorhanden, so daſs sich bei der Herstellung von
schmiedbarem Guſs die Oxydation nur auf den Kohlenstoff bezieht.
A. Friedmann (daselbst S. 529) hat im Eisenwerke
Reschitza 10mm starke Puddelbleche mit Blasenbildungen untersucht. Eine beim Fertigwalzen des
Bleches entstandene Blase enthielt 180cc Gase
folgender Zusammensetzung:
Kohlensäure
20,85 Proc.
Kohlenoxyd
70,42
Sauerstoff
0,85
Es gelang nicht, das Gas ganz luftfrei aufzufangen, daher der
geringe Sauerstoffgehalt; auf Luft berechnet ist dies 4,05 Proc. Es bliebe noch als
Differenz 4,68 Proc., welche aus Stickstoff oder Wasserstoff oder dem Gemenge beider
bestehen konnte und nicht näher untersucht wurde. In der Blase fanden sich lichtere
schuppenartige Gebilde folgender Zusammensetzung (I):
I
II
Kieselsäure, lösl. in Salzsäure
0,45
0,50
Desgl., unlöslich
73,25
63,80
Kalk
2,05
1,10
Magnesia
0,84
1,49
Manganoxydul
0,77
0,76
Eisenoxyd und Thonerde
23,20
33,65
––––––
––––––
100,56
101,30.
Unter II ist ein ähnlicher Ansatz einer zweiten Blase
untersucht. Das Zustellungsmaterial des Puddelofens hatte etwa 66 bis 70 Proc.
Kieselsäure.
Nach H. v. Jüptner (Chemikerzeitung, 1885 S. 448) floſs
aus der Lürmann'schen Schlackenform eines Hochofens eine dünnflüssige, auſser dem Ofen unter
Entwicklung eines dichten, erstickenden Qualms erstarrende Masse aus von folgender
Zusammensetzung:
In Wasserunlöslich
KohleSchlacke
1,37 Proc.6,39
In Wasserlöslich
SchwefelkaliumKohlensaures
KaliumCyankaliumCyansaures
KaliumRhodankaliumKaliummetasilicat
2,9936,5249,58 1,15Spur 1,75
Die Beschickung bestand aus gleichen Raumtheilen Kokes und
Holzkohle, gerösteten Spatheisensteinen mit 10 Proc. Puddelschlacken und 20 Proc.
Kalkstein. Der Ofen zeigte starken Gargang bei 400° Windtemperatur und einer
Erzeugung von 22 bis 23t Roheisen (mit 2,75 Proc.
Silicium und 5,75 Proc. Mangan).
Zur Siliciumbestimmung in Eisen wird die Probe mit
rauchender Schwefelsäure übergössen und etwa eine Messerspitze voll Kaliumchlorat
zugesetzt. Nach ungefähr ½ Stunde ist die Auflösung vollendet. Nun wird bei nicht zu
groſser Hitze auf der mit Asbestpappe bekleideten Herdplatte zur Trockne gebracht,
mit etwas rauchender Salzsäure angewärmt, verdünnt und filtrirt. Soll die
Rohkieselsäure gereinigt werden, so wird das sammt Inhalt im nassen Zustande
veraschte Filter mit rauchender Salzsäure gekocht.
L. Blum (daselbst S. 1373) wägt zur Bestimmung des Siliciums in Eisen 5g Roheisen in einer Erlenmeyer'schen Kochflasche ab, gibt ungefähr 100cc Wasser hinzu und dann weiter unter Bewegung des
Flascheninhaltes 150cc Bromsalzsäure. Es erfolgt
sogleich eine stürmische Einwirkung, wobei sich die Flüssigkeit stark erhitzt, so
daſs in wenigen Augenblicken die Auflösung erfolgt. Man kocht hierauf einige Minuten
zur Austreibung des überschüssigen Broms, spült die Lösung in eine geräumige
Abdampfschale, fügt ungefähr 10g Chlorammonium in
Lösung hinzu und dampft auf dem Wasserbade zur Trockne ein. Nach dem Eindampfen
läſst man erkalten, nimmt den Rückstand mit concentrirter Salzsäure auf, verdünnt
mit Wasser und filtrirt. Die noch an der Abdampfschale haftenden Theilchen spült man
mit Wasser auf das Filter, wäscht dieses einige Male mit Wasser aus und dann auf
einander folgend einmal mit Bromsalzsäure, zweimal mit warmem Wasser, wieder einmal
mit Bromsalzsäure und dann mit warmem Wasser bis zur vollständigen Verjagung der
letzten Reste von Bromsalzsäure. Den noch feuchten Niederschlag bringt man sammt
Filter in ein Platinschiffchen und glüht in der Muffel bis zur vollständigen
Verbrennung des Graphits.
Zur Reinigung von geschmolzenem Eisen will W. Griffith in Pittsburg (Nordamerikanisches Patent Nr.
289085 bis 289089) ein Gemenge aus schwefelsaurem Kupfer und Chlorkalium, oder
Ammoniumnitrat und Mangansulfat, oder Soda und Blutlaugensalz, oder Potasche und
Salpeter eintragen.
J. E. Atwood will zu gleichem Zwecke, wie in D. p. J. 1885 257 243 schon
erwähnt, Bleiamalgam einrühren, während H. Pundy in Brooklyn (Nordamerikanisches Patent Nr.
322558) das Eisen in einem mit Mennige, Zinnober und Sand gefütterten Tiegel
schmelzen will.
Zur Bestimmung der Phosphorsäure in den basischen
Entphosphorungsschlacken werden nach C. Brunnemann
(Chemikerzeitung, 1885 S. 1335) 10g
Schlacke in einem Becherglase mit 10cc
Schwefelsäure, 50cc Salzsäure und 20cc Salpetersäure etwa ½ Stunde lang gekocht. Die
erkaltete Lösung, in welcher sich neben Kieselsäure, Kohle und Graphit auch mehr
oder weniger groſse Mengen Gyps ungelöst befinden, wird in einen Literkolben
gespült, mit etwas Salzsäure versetzt, um den Gyps beim nachherigen Verdünnen mit
Wasser in Lösung zu bringen, und dann bis zur Marke aufgefüllt. Nach mehrmaligem
Umschütteln läſst man absetzen und dampft dann 50 oder 100cc der darüber stehenden klaren Flüssigkeit in
einer Porzellanschale so lange ein, bis die noch vorhandene Salzsäure und
Salpetersäure fast abgeraucht ist, neutralisirt dann die freie Schwefelsäure mit
verdünnter Ammonlösung (1 : 5), indem man letztere mit Hilfe einer Spritzflasche an
den Rändern der Schale heruntertropfen läſst, dampft bis zur Trockne auf dem
Wasserbade ein und erhitzt nachher noch ½ Stunde bei 110° im Luftbade, um die
gelöste Kieselsäure in eine unlösliche Form überzuführen. Der Rückstand wird dann
mit Salpetersäure aufgenommen, filtrirt und die Phosphorsäure mit Molybdän
gefällt.
Tafeln
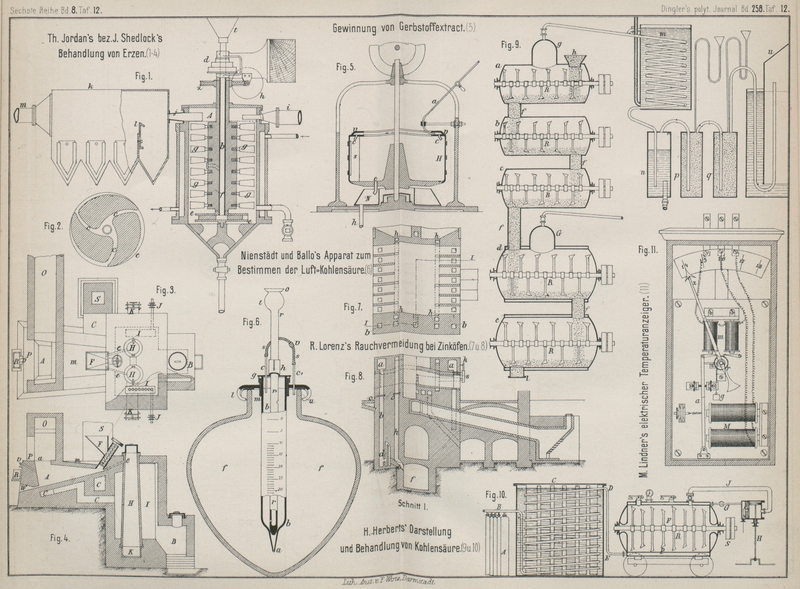