Titel: | Ueber die Herstellung von Zellstoff für Papier. |
Fundstelle: | Band 258, Jahrgang 1885, S. 312 |
Download: | XML |
Ueber die Herstellung von Zellstoff für
Papier.
(Patentklasse 55. Fortsetzung des Berichtes Bd.
255 S. 111.)
Mit Abbildungen auf Tafel
21.
Ueber die Herstellung von Zellstoff für Papier.
A.
Behr in Cöthen (* D. R. P. Zusatz Nr. 31548 vom 15. November 1884) hat seine Anlage zur Gewinnung von Zellstoff und Glykose aus Holz
(vgl. 1885 255 * 111), bei welcher Oel zum Ausziehen der
Inkrusten benutzt wird, erweitert und anders angeordnet. Wie aus Fig. 1 Taf. 21
zu entnehmen, sind an Stelle des einen Cylinders mehrere durch die verschiedenen
Leitungen in Batterieform zusammengeschaltete Extractionscylinder H vorhanden, in welche durch die Löcher in den Domen
a das zu behandelnde Holz eingebracht und aus denen
das fertige Material durch seitliche Mannlöcher b
entnommen wird. Die Cylinder erhalten oben und unten Doppelböden m und n, welche durch
Rohre f unter einander in Verbindung stehen, und in
einiger Entfernung davon Siebböden c und d, von denen die oberen theilweise aufklappbar
eingerichtet sind, um das Holz durch dieselben in den Raum zwischen den beiden
Siebböden zu bringen. Die Zuleitung von Dampf oder Kühlwasser in die Doppelböden m und n erfolgt durch die
Rohre e und g und die Zu-
und Ableitung für das Innere der Cylinder H durch die
Rohre h und i.
Nachdem die Cylinder H etwa auf ⅔ ihrer Höhe mit Holz
gefüllt sind, erfolgt die Zuleitung von Oel aus dem Behälter G mittels der Pumpe P1 durch die Rohrleitung h. An den Glasrohren l ersieht man dabei den
Flüssigkeitstand in den Cylindern. Der zur Heizung der Cylinder benutzte Dampf
tritt, nachdem er zuvor durch die Heizschlange des Oelkessels K gegangen, aus der Leitung o in die Doppelböden des ersten Cylinders und dann durch die
Zwischenleitungen p immer zu dem nächsten Cylinder. Die
Doppelböden aller Cylinder stehen durch die Leitung q
mit einem Dampfwasserableiter in Verbindung.
Hiernach wird der erste Cylinder der höchsten Hitze ausgesetzt,
welche sich nach der Spannung des Dampfes in der Heizschlange des Kessels K richtet. Jeder Cylinder H ist mit je zwei Manometern und Sicherheitsventilen ausgerüstet, je eines
für die Spannung in den Heizräumen m und n und für das Innere des betreffenden Cylinders.
Ist der Inhalt des ersten Cylinders H
genügend ausgezogen, so leitet man die sich im Kessel K
entwickelnden Oeldämpfe durch das Steigrohr r und das
Rohr h in das Innere dieses Cylinders; hierbei wird der
Hahn des Rohres i so weit geöffnet, daſs durch h mehr Oeldampf hinzutritt, als heiſse Flüssigkeit
durch i abgeleitet wird. Es hat dieser Vorgang den
Zweck, jedes Theilchen des Holzes durch Oeldampf auszudrücken. Das Durchpressen des
Oeldampfes geschieht so lange, bis eine am Boden des Cylinders mittels des
Probekühlers N genommene Probe vollständig wasserhell
ist.
Die gefärbte Harz-, Wachs- oder Fettlösung flieſst durch das Rohr
s nach dem Behälter J,
auf welchem Wege sie noch den Kühler K2 durchläuft. Die Kühlung in demselben ist nur eine
oberflächliche; es soll hier nur der Dampf niedergeschlagen werden und muſs die
Flüssigkeit noch heiſs nach dem Behälter J gelangen,
aus welchem dieselbe, falls sie stark mit Harz, Wachs oder Fett versetzt ist,
mittels der Pumpe P2
durch das Rohr t nach dem Kessel K geschafft wird, in welchem alsdann wieder eine
erneute Verdampfung des Oeles durch die Heizschlange bewirkt wird.
Die aus J entweichende Luft geht
durch den Kühler C, in welchem der der Luft noch
beigemengte Oeldampf verflüssigt wird und nach J
zurückfällt, nach dem Oelbehälter G und gelangt von
hier aus durch das Luftfilter Z, frei von jeder
Oelbeimengung, ins Freie. Das Luftfilter Z besteht aus
einem kleinen, auf G befestigten Blechcylinder, welcher
unten mit einer Siebplatte versehen ist, auf welcher Holzkohlenstückchen lagern, die
den übrigen Raum des Cylinders völlig ausfüllen und vermöge ihrer Porosität die etwa
der Luft noch beigemengten Oeltheilchen aufsaugen.
Sobald die Flüssigkeit aus dem ersten Cylinder H farblos abflieſst, derselbe somit nur reines Oel
enthält, wird der Zufluſs von Oeldampf aus dem Rohre r
bezieh. dem Kessel K durch das Rohr h abgesperrt und das im Cylinder H vorhandene Oel, nachdem dasselbe durch den Kühler K2 gegangen ist, durch
das Rohr u nach dem Oelbehälter G geleitet. Die Heizung des ersten Cylinders H mit dem unmittelbar aus der Schlange von K
kommenden Dampfe wird inzwischen fortgesetzt, um hierdurch möglichst viel Oel aus
den Poren der Holzsubstanz zu verdrängen; wird mittels des Probekühlers N gefunden, daſs durch diese Heizung kein Oel mehr aus
dem Holze abgesondert wird, so wird durch das Rohr v
und das Rohr h Kesseldampf auf das auszuziehende Holz
geleitet, welcher die letzten in demselben noch vorhandenen Oeltheilchen
mitreiſst.
Auch bei diesem Vorgange kann man noch einen Theil des Oeles
wasserfrei erhalten und nach dem Behälter G leiten; man
muſs aber hierzu aus dem oberhalb des Probekühlers N am
Cylinder angebrachten Hahne w öfter abgekühlte Proben
entnehmen; färbt sich hierbei die Flüssigkeit weiſslich, so wird sofort das Rohr u geschlossen und gelangt die Flüssigkeit nun durch das
Rohr x nach dem Behälter L. Die sich in demselben ansammelnde ölig-wässerige Flüssigkeit muſs auf
eine Temperatur von 90° gebracht werden, bei welcher sich Oel und Wasser scharf
abscheiden, und kann alsdann das Oel durch die Hähne y
und das Rohr z nach dem Oelbehälter G geleitet werden, wobei dasselbe vorher noch den
Kühler R durchläuft. Die Kühlung in R ist derart einzurichten, daſs die Flüssigkeit eine
Temperatur von ungefähr 90° erhält; ist dies nicht gut zu ermöglichen, so wird in
die Schlange von L entweder Wasser, oder Dampf
eingeleitet, um je nach den Umständen eine Verminderung oder Erhöhung der
Flüssigkeitstemperatur bis auf die verlangten 90° zu bewirken.
Ist auf diese Weise alles Oel aus dem im Cylinder H befindlichen Holze entfernt, so wird, falls die
Inkrusten derselben nur lose gebunden sind, der Cylinder mit Wasser gefüllt, welches
eine geringe Menge Schwefelsäure enthält.
Hierauf wird durch Einleiten von Dampf in den Heizraum des
betreffenden Cylinders die Flüssigkeit zum Kochen gebracht. Erweist sich das Kochen
als zu schwach, so wird dasselbe auf die früher (1885 255
* 113) angegebene Weise mittels Glycosekocher vorgenommen und kann für diesen Fall
die Entleerung des Cylinders H durch das seitliche
Mannloch b stattfinden, wobei vorher ein Abkühlen der
Masse in der Weise stattfinden muſs, daſs man nach Entfernung des heiſsen Wassers
durch g nach q und
Absperrung der Dampfzuleitung durch die Rohre z, o und
e langsam kaltes Wasser in den Heizraum des
Cylinders H leitet.
Der Dampf wird nunmehr aus dem Rohre o durch das Rohr e unmittelbar in den zweiten
Cylinder H geleitet und gelangt aus diesem nach dem
dritten Cylinder H. Falls alsdann der Inhalt der beiden
anderen Cylinder weniger ausgezogen ist, wird der Dampf aus dem dritten Cylinder
durch das Rohr y nach dem zweiten und ersten Cylinder
H geleitet und gelangt aus dem letzteren Cylinder
nach dem Kesselhause.
Gelangen Pflanzenstoffe zur Verarbeitung, die groſse Mengen Substanz enthalten,
welche in dem ausziehenden Oele löslich ist, so würde durch die abzudampfenden
Harzlösungen der Betrieb sehr bald gestört werden; für solche Fälle ist es
angebracht, die Lösung, wenn sie anfängt, dick zu werden, durch das Rohr V nach dem Reinigungsapparate M überzuführen, in welchem ohne Störung durch die Heizschlange das Oel von
der Lösung geschieden werden kann. Das gereinigte Oel gelangt alsdann in Form von
Oeldampf durch das Rohr x1 nach dem Oelbehälter G, wobei es von dem
Kühler Q entsprechend abgekühlt wird. Wird einmal von
den Extractionscylindern H nicht aller im Kessel K erzeugter Oeldampf gebraucht, so wird der
überschüssig entwickelte Dampf durch das Rohr r und den
Kühler Q nach dem Behälter G zurückgeleitet.
Bei der von H. Sellnick in Leipzig (* D. R. P. Nr. 28590 vom 17. Februar 1884) angegebenen
Einrichtung zur Gewinnung von Faserstoffen zur Papierfabrikation wird das vorher
entsprechend zerkleinerte Bolz oder Stroh u. dgl. in Körben C
(Fig. 2
und 3 Taf. 21)
aus durchlochtem Eisenbleche erst ausgelaugt und dann unter freier Luft gekocht. Die Späne werden in die Körbe C fest eingestampft und dann diese mittels Laufkrahn in die
Auslaugebottiche A gestellt und 24 Stunden darin
gelassen. Die Körbe stehen allseitig, auch am Boden, etwa 50mm von der Bottichwandung ab und in ihrer Mitte
ist ein ebenfalls durchlochter Rohreinsatz d, der das
Zutreten der Lauge in das Innere befördert; beim späteren Auskochen ermöglicht
dieses Rohr ein besseres Kreisen des Wassers und auch bereits während des
Einweichens wird dasselbe dazu benutzt, die Materialien immer mit frischen
Laugeschichten in Berührung zu bringen. Zu diesem Behufe wird von Zeit zu Zeit vom
Arbeiter ein Kolben m in das Rohr d gestoſsen.
Nach der 24stündigen Auslaugung werden die Körbe aus den Bottichen herausgehoben und
durch Hängenlassen abgetropft; sodann kommen dieselben eitrige Minuten in einen
Bottich mit warmem Wasser, um von der äuſserlich noch anhaftenden Lauge befreit zu
werden. Dieses Wasser, welches öfters gebraucht werden kann, wird schlieſslich zur
Herstellung frischer Lauge verwendet. Die Späne saugen etwa den sechsten Raumtheil der Lauge an.
Die Bottiche werden um den Betrag dieser in den Spänen aufgenommenen Lauge wieder
mit frischer Lauge angefüllt, welche, in einem höher stehenden Bottiche bereit
gehalten, denselben durch eiserne Röhren zuflieſst.
Der Kochkessel B (Fig. 3 Taf. 21), in
welchen die Körbe dann eingesetzt werden, wird durch eine Dampfschlange F geheizt und ist, nur um den Wrasen abzuhalten, mit
einem durch ein Gegengewicht ausgeglichenen Deckel abgeschlossen. Jedoch kann
erforderlichen Falles der Deckel auch festgeschraubt und unter Druck gekocht werden,
was aber Sellnick vermeiden will, da die Papierstoffe
dann an Farbe und Ausbeute leiden. Der Kochkessel wird nur mit Wasser gefüllt und
dieses mit der hinzutretenden Wärme soll genügen, die Lösung der Inkrusten mittels
der vorher eingelaugten Alkalien zu bewerkstelligen. Die ausgekochte Flüssigkeit
wird von Zeit zu Zeit durch den Hahn H abgezogen und
die Späne in Stampfwerken oder Kollergängen behandelt, wobei stetig zu- und
abflieſsendes Wasser die Ausspülung der gelösten Inkrusten besorgt.
Th. Graham Young in Durris und J. Pettigrew in Dinside, Schottland (Nordamerikanisches Patent Nr. 322822,
vgl. Papierzeitung, 1885 S. 1664) wollen zur
Zellstoffgewinnung aus Holz, Stroh u. dgl. diese Stoffe
mit Lösungen von Salpetrig säure oder Salpetersäure
längere oder kürzere Zeit in einem offenen Kessel kochen. Die Dauer des Kochens ist
verschieden, z.B. bei Fichtenholz und einer Lösung von 1,1 sp. G. etwa 40 Minuten.
Nach dem Kochen wird die Lösung abgelassen und die in den Stoffen noch verbliebene
Säure durch Auswaschen entfernt, worauf die Stoffe dann nochmals mit Alkalien (bei
Holz z.B. 5 Procent vom Gewichte des rohen Holzes) etwa 30 Minuten lang gekocht
werden. Die verwendeten Alkalien sollen auf gewöhnlichem Wege wiedergewonnen und die
beim ersten Kochen aufsteigenden salpetersäurigen Gase in einen Thurm geleitet
werden, um sie dort niederzuschlagen. Die Säurelösungen können mehrere Male zum
Kochen gebraucht und dann abgedampft werden., um die im Rückstande sich vorfindende
Oxalsäure und salpetrige Säure wiederzugewinnen.
J. Chaudet schlägt in der Revue
industrielle, 1883 * S. 425 zum Kochen der zur Zellstofferzeugung benutzten
Stoffe eine schwache Lauge von kaustischer Soda vor und
soll das Kochen unter beständigem Umrühren 6 Stunden lang anhalten. In demselben Kessel hätte dann das Abdampfen der Lauge
stattzufinden, wobei die Inkrusten eine schmierige seifenartige Masse bilden sollen,
welche durch Auswaschen leicht zu entfernen ist, um den reinen Zellstoff
zurückzulassen.
Der hierzu benutzte Kochapparat ist in Fig. 7 und 8 Taf. 21 skizzirt. Ein
rechteckiger, mit halbrundem Boden versehener Kessel ist drehbar in einem Gestelle
gelagert. Durch den einen hohlen Drehzapfen C reicht
die durch eine Stopfbüchse abgedichtete Welle w, welche
innerhalb des Kessels die Rührflügel R trägt und deren
Ende in einer Anbohrung des anderen Drehzapfens C1 steckt, Auſsen trägt die Welle w ein
Schneckenrad e, in welches eine durch die
Riemenscheiben S angetriebene Schnecke f greift, wodurch die Rührflügel in langsame Drehung
versetzt werden. Der Kessel erhält eine innere Bekleidung B aus gegen Säuren widerstandsfähigerem Materiale, welche am Boden etwas
absteht und dort einen Hohlraum A bildet. Der Deckel
D des Kessels ist mit Handgriffen h zum leichten Abheben versehen und erhält ein
Sicherheitsventil v und den Rohransatz a. Der Dampf zum Kochen wird durch den Zapfen C1 und das von diesem
abzweigende Rohr g in den Kessel eingeführt. Beim
Abdampfen wird dieses Rohr abgesperrt und dann der Dampf durch das Rohr d in den Raum A geleitet.
Das sich in demselben niederschlagende Wasser flieſst durch b ab. Das Abdampfen soll auch unter Luftleere
erfolgen, wozu der Rohransatz a mit einer Luftpumpe
verbunden werden kann. Um den Kessel beim Entleeren zu drehen, trägt der Zapfen C einen Arm c, welcher
durch einen Bolzen t mit dem Rade e gekuppelt wird.
Die bei Sulfitkochern entstehenden Gase, die durch
Aufnahme von Sauerstoff aus dem Dampfe, Wasser und Holze Schwefelsäure bilden
können, welche den Zellstoff schwärzt, werden bisher gewöhnlich mit dem Dampfe von
Zeit zu Zeit abgeblasen. Um nun hierbei die Gase nicht verloren gehen zu lassen,
verbinden Ch. S. Wheelwright in Providence und
G. E.
Marshall in Turners Falls, Nordamerika (* D. R. P. Nr. 32528 vom 17.
September 1884) den Dampfraum des Kochers A
(Fig. 10
Taf. 21) mit einem Kühler H, dessen Thätigkeit durch
einen Dampfwasserableiter geregelt wird, indem die durch das Rohr h abziehenden Dämpfe in der Kühlschlange
niedergeschlagen werden und diese mit dem Ableiter unmittelbar verbunden ist. Wenn
die Zersetzung des Holzes beendet ist, werden Dampf und Gase vollends abgeblasen
und, um die darin enthaltenen Chemikalien wieder zu gewinnen, nach einem besonderen
Kühler K (Fig. 9 Taf. 21) geleitet,
aus welchem die flüssige Säure in einen Behälter M
gelangt, wo sie mit einer entsprechenden Base vereinigt und dabei durch einen
drehenden Rechen umgerührt wird. (Vgl. Aussig 1885 257
40.)
Das Wesentlichste des genannten Patentes bildet jedoch die neue Construction eines
Kochers, welcher wie der ältere Marshall'sche Kocher (1884 251 * 214) einen Dampfmantel besitzt.
Derselbe ist, wie der Kocher selbst, aus mehreren hohlen
Ringstücken zusammengesetzt. Die Ringstücke werden aus zwei durch Steh
bolzen unter einander abgesteifte Blechcylinder, die durch guſseiserne Flanschen
oben und unten mit einander verbunden sind, gebildet. Mit diesen Flanschen werden
die einzelnen Ringstücke unter einander verschraubt und die Platten des inneren
Bleibeleges an den Flanschen umgebogen und gleich zwischen denselben mit
zusammengepreſst, wie dies oben an dem dargestellten Kocher Fig. 10 ersichtlich ist,
oder die einzelnen Bleicylinder werden an den Flanschenstellen zusammengelöthet. In die einzelnen
Hohlringe wird Dampf durch das Rohr E eingeleitet und
stehen dieselben durch ein gemeinschaftliches Rohr F
mit einem Manometer f in Verbindung. Der Kocher erhält
einen Siebboden B, unter welchem mit einer
Vertheilungsdüse das Dampfrohr D mündet, und einen
Dampfdom C, welcher, um ein Mitreiſsen von
Holztheilchen in denselben zu verhindern, mit einem Siebe vom Kochraume getrennt
ist. Aus dem Dampfdome C führt das Rohr h für den beständigen Abzug von Dampf und Gasen und das
Rohr I für den Abzug am Ende des Kochens nach den
entsprechenden Kühlern H und K. Um die Lauge während des Kochens beständig in Wallung zu halten und ein
Absetzen der in der Lauge gelösten Stoffe zu verhindern, wird die Flüssigkeit aus
dem Kocher am Boden durch das Rohr n1 von einem Dampfstrahlgebläse N angesaugt und nach oben gedrückt, wo sie in dem Rohre
n wieder in den Kocher tritt. Zum Ein- und Ablassen
der Lauge dient das mit einem Absperrschieber versehene Rohr G. Um nun ein Absetzen von Stoffen in diesem Rohre bis zum Absperrschieber
hin zu verhindern, wird die Rohrmündung durch einen besonderen Spund g verschlossen.
D. O. Francke in Mölndal, Schweden (Nordamerikanisches
Patent Nr. 304092, vgl. Papierzeitung, 1885 S. 1132)
hat das Patent auf seinen wagerechten, während des Betriebes sich drehenden Kocher (vgl. 1883 249 24 bezieh. 1884 252 326) endlich erhalten
und ist hiernach in Fig. 6 Taf. 21 die Einrichtung desselben ersichtlich gemacht. Der
cylindrische, an seinen Enden stumpf zugespitzte Stahlblechkessel ruht auf Rollen
R und ist mit einem Zahnkranze z versehen, in welchen die beliebig angetriebene
Schnecke s greift. Von beiden Enden treten in den
Kessel durchlochte Rohre D, durch welche der zum Kochen
nöthige Dampf zugeleitet wird. Die innere Blei Verkleidung besteht aus
zusammengelötheten Platten und wird der so hergestellte innere Bleicylinder an der
Kesselwandung durch Ringe H anliegend erhalten. Die
Ringe H sind an einer Stelle aufgeschnitten, um sie
durch Keile K aus einander treiben zu können. Zum
Befahren des Kessels ist derselbe mit einem Mannloche E
versehen. Um Undichtheiten in der Bleiverkleidung von auſsen bemerken zu können, ist
durch die Stahlblechwandung eine groſse Anzahl Hähne h
geschraubt, welche während des Betriebes stets offen sind. Tritt nun an einer Stelle
die Kochlauge hinter die Bleiverkleidung, so tropft dieselbe durch den
nächstliegenden Hahn h aus. Man schlieſst dann diesen
Hahn, bis man die Ausbesserung ausführen kann. Erwähnt mag noch werden, daſs die
Kochflüssigkeit mit Stoff etwa ⅔ des Inhaltes beträgt und daſs nach einer Kochung
der Kocher durch das Condensationswasser gänzlich gefüllt wird. Nach dem Einbringen
der ersten Lauge findet während der Arbeit kein Nachfüllen statt.
Bei einer in der Papier Zeitung, 1885 S. 1506
beschriebenen amerikanischen Ausführung eines Sulfitkochers ist der Kessel, wie auch die Bleiverkleidung in zwei Längshälften getheilt. Die beiden Kesselhälften
b und b1 werden, wie in Fig. 4 und 5 Taf. 21 veranschaulicht
ist, mit guſseisernen Flanschen a durch Schrauben
verbunden und die Längskanten der Blei Verkleidung c
einfach umgebogen und zwischen den Flanschen a mit
festgeklemmt. Die Flächen des Bleibleches, welche dabei auf einander zu liegen
kommen, werden mit Riefen versehen, die in einander passen, um eine gute Dichtung zu
erhalten. Auſserdem wird noch eine besondere Dichtung durch Asbestschnüre d o. dgl. hergestellt. Der obere Theil des Kessels ist
zu einem Dampfdome zusammengezogen und der untere Theil endet mit einer Verengung,
damit der dort befindliche falsche Boden kleiner wird und die Auskleidung besser
Stand hält. Am unteren Ende des Kessels liegt die Bleiverkleidung nicht dicht auf
dem Eisenbleche, sondern bleibt etwas davon entfernt, damit sich etwaige durch die
Blei Verkleidung dringende Flüssigkeit unten sammeln und von dort abgelassen werden
kann. Würde diese Flüssigkeit zwischen dem Blei- und Eisenbleche bleiben, so könnte
sie sich beim Wiederanheizen in Dampf verwandeln und das Bleiblech nach innen
aufblähen. Der Kocher soll durch seine Längstheilung weniger Flanschenlänge, also
auch geringere Gefahr des Undichtwerdens bieten als die in Ringstücken
zusammengesetzten und sich auch billiger herstellen lassen.
Th. Routledge, der Erfinder des Espartozellstoffes, soll
nach der Papierzeitung, 1885 S. 1629 den sonderbaren
Vorschlag gemacht haben, Sulfitkocher ganz aus Blei
herzustellen. In welcher Weise die erforderliche Widerstandsfähigkeit dabei erzielt
wird, ist nicht angegeben.
Die Bleiverkleidung der Sulfitkocher besitzt einen Nachtheil wegen der groſsen
Ausdehnungscoefficienten des Bleies und einer bleibenden Ausdehnung bei wiederholtem
Erwärmen und Abkühlen. Zudem haben Blei und Eisen verschiedene
Ausdehnungscoefficienten, in Folge dessen sich der Bleimantel leicht loslöst, Blasen
erhält, welche schlieſslich aufbrechen. Um diesem Uebelstande vorzubeugen, stellt
John
Makin in Bellfield bei Rochdale (*
D. R. P. Nr. 33381 vom 14. Mai 1885) das Futter für
Sulfitkocher u. dgl. aus Bleiblech mit einer Zwischenlage
aus härterem und weniger ausdehnungsfähigem Metalle her. Diese Zwischenlage
hält durch ihre feste Verbindung mit dem Bleie die Verkleidung in sicherer Anlage an
der Kocher wand ung. Die feste Verbindung mit dem Bleie wird erreicht, indem die
Zwischenlage, z.B. Eisenblech, durchlocht und von beiden Seiten mit Blei umgössen
wird, und bildet somit das Eisenblech ein Gerippe für die Verkleidung. In besonderen
Fällen wird eine gelochte Eisenplatte nur auf einer Seite mit Blei vergossen oder
belegt, wobei die Löcher durch hydraulischen Druck auf den Bleibelag oder sonstwie,
z.B. mittels Löthrohres, fest ausgefüllt werden. (Vgl. Suckow 1885 256 142.)
Zum Reinigen des Zellstoffes von unaufgeschlossenen
Holzfasern, Asttheilen, Gyps, schwefligsaurem Kalk oder anderen schwer- und unlöslichen Beimengungen hat
A.
Leonhardt in Oedekoven bei Bonn (*
D. R. P. Nr. 33283 vom 30. Mai 1884) ein Verfahren
angegeben, bei welchem der Zellstoff stark mit Wasser versetzt und dann durch lange
Kanäle und Siebe geführt wird, um eine Ausscheidung der Verunreinigungen zu
erzielen. (Vgl. Hartig 1885 256 436.)
Bei Sulfitzellstoff wird derselbe mit
ungefähr dem 1500fachen seines Gewichtes mit Wasser versetzt und in wagerechten,
ziemlich breiten Kanälen fortgeleitet, deren Boden (nach Art der sogen. Sandfange)
mit der Strömungsrichtung entgegenstehenden Vorsprüngen versehen ist. An den
Vorsprüngen befinden sich Kästen, welche von Zeit zu Zeit herausgenommen und von den
niedergefallenen gröberen Unreinigkeiten entleert werden können. In einem gröſseren
Bottiche findet dann ein noch vollkommeneres Absetzen statt. Aus diesem Bottiche
wird die Flüssigkeit durch eine Schöpfvorrichtung auf ein höher liegendes Schwimmsieb (vgl. C.
Hoffmann 1884 251 * 531) gehoben, wo weitere
Verunreinigungen abgesondert werden. Die freie Durchfluſsfläche des Siebes wird
dabei auf stündlich 100k Zellstoff zu 0qm,2 gerechnet, Von dem Schwimmsiebe gelangt die
Flüssigkeit in einen besonderen Stoffabsonderer,
welcher aus einem schräg liegenden Trommelsiebe besteht, dessen
Umfangsgeschwindigkeit so bemessen wird, daſs das Wasser durch die Centrifugalkraft
ausgeschleudert wird, die Fasern jedoch an der inneren Siebfläche hängen bleiben
sollen. Im höchsten Punkte sollen dann bei der Drehung die Fasern abfallen und durch
die schräge Lage der Trommel nach und nach aus derselben befördert werden. Das
ausgeschleuderte Wasser flieſst zu weiterer Zellstoffverdünnung in den Anfangskanal
zurück. – Namentlich in Bezug auf den vorgeschlagenen Stoffabsonderer dürfte der
Erfolg des ganzen Verfahrens zweifelhaft sein.
Tafeln
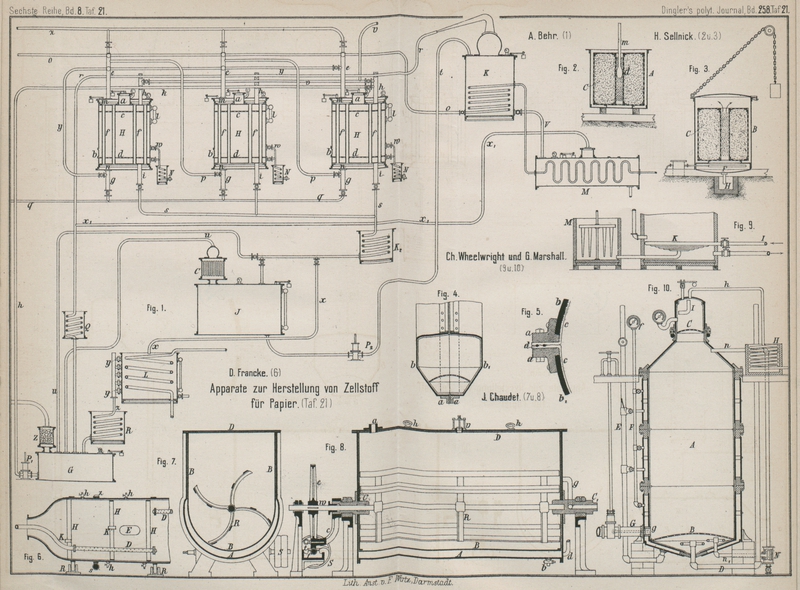