Titel: | Ueber die Herstellung von Leuchtgas. |
Fundstelle: | Band 261, Jahrgang 1886, S. 435 |
Download: | XML |
Ueber die Herstellung von Leuchtgas.
(Patentkl. 26. Fortsetzung des Berichtes Bd. 257
S. 466 und Bd. 259 S. 88.)
Mit Abbildungen auf Tafel
28.
Ueber die Herstellung von Leuchtgas.
Als Sicherheitsvorrichtung zur geschlossenen Speisung von
Oelgasretorten verwendet H. Hirzel in
Plagwitz-Leipzig (* D. R. P. Nr. 34204 vom 24. Februar 1885) ein Metallgehäuse,
welches nach Fig.
1 Taf. 28 durch eine Scheidewand b in zwei
Kammern getheilt ist; das Oel flieſst bei f in die
durch eine angeschraubte Glasplatte e geschlossene
vordere Kammer c, steigt, weil die Scheidewand b nicht ganz bis zum Boden reicht, in der Kammer d bis zur Höhe des Abfluſsrohres g und flieſst bei geöffnetem Hahne h in die Retorte ab.
An bereits bestehenden Zulaufrohren bringt man einen Glascylinder a (Fig. 2 Taf. 28) an,
welcher oben und unten durch zwei zusammen geschraubte, je mit einer Verschraubung
in der Mitte versehene Metallplatten dicht geschlossen ist. Diese Vorrichtung kann
auf jedem Heber nach Entfernung des Trichters aufgeschraubt werden und wird
andererseits mit der Oelzuleitung f verbunden.
Bei Anwendung dieser Sicherheitsvorrichtungen kann nun das Abgangsrohr vom Heber zur
Retorte oder der Gasabzug verstopft sein und der Druck in der Retorte noch so hoch
steigen, es kann doch kein Ueberflieſsen oder Emporspritzen des Oeles
stattfinden.
W. de St Martin in Brüssel (* D. R. P. Nr. 36134 vom 17.
September 1885) will ein zur Heizung oder Beleuchtung dienendes Gas aus Mineralöl und Wasserdampf herstellen. Der in der
Patentschrift beschriebene Apparat erscheint für diesen Zweck aber durchaus
ungeeignet.
L. Fuchs in Beraun, Oesterreich (* D. R. P. Nr. 35924
vom 17. September 1885) verwendet zur Herstellung von
Leuchtgas aus leichtflüchtigen Kohlenwasserstoffen eine besondere
Vorrichtung, welche einen ununterbrochenen Strom Preſsluft liefern soll. Diese Vorrichtung enthält drei Glocken c, b und d (Fig. 9 Taf.
28), wovon die mittlere am Boden befestigt ist. Das Ventil a der äuſseren Glocke c öffnet sich nach
innen, während das Rohr e mit einem sich in die Glocke
d öffnenden Ventile v
versehen ist. Durch das Rohr t wird die innere Glocke
in angegebener Höhe mit Wasser gefüllt; das Rohr l
dient zur Druckausgleichung.
Wird die äuſsere Glocke c mittels des angedeuteten
Windewerkes gehoben, so öffnet sich das Ventil a und es
tritt Luft in die Glocke c ein; beim folgenden Sinken
derselben durch Wirkung einer entsprechenden Belastung wird diese Luft gepreſst und
tritt durch das Rohr e und Ventil v in die Glocke d, welche,
wenn die Hähne p und q
geschlossen sind, bis an den Deckel der Glocke b
gehoben wird. Die Gewichte beider Glocken sind im Verhältnisse ihrer Querschnitte so
gewählt, daſs sie einander wechselseitig ausgleichen. Wird dann der Hahn p oder q geöffnet, so
strömt unter Einwirkung des von der Glocke d ausgeübten
Druckes Luft durch das Rohr f in den Carburator H und in Folge der dadurch veranlaſsten Verminderung
der Luftspannung sinkt die Glocke d, öffnet sich aber
auch das Ventil v, die Glocke d steigt also wieder in ihre höchste Stellung und so geht es fort, bis die
Glocke c ganz gesunken ist, worauf auch die Glocke d ununterbrochen sinkt.
Der flüchtige Kohlenwasserstoff gelangt durch das Rohr g
in die obere Abtheilung des cylindrischen Gefäſses H
und durch die Ueberlaufrohre n und h schlieſslich in den Behälter J. Querwände u (vgl. Fig. 8) zwingen die durch
Hahn p zutretende Luft in der Pfeilrichtung dem Oele
entgegen nach oben zu steigen, um durch Rohr k mit
brennbaren Dämpfen gesättigt zu entweichen.
Wenn die ablaufende Flüssigkeit im Behälter J einen
bestimmten Stand erreicht hat, hebt der Schwimmer s das
Ventil x, so daſs die durch das Rohr w eintretende gespannte Luft die Flüssigkeit durch Rohr
j wieder in den Behälter G hebt. Die kurze Drehachse des Hebels y
reicht durch eine Stopfbüchse aus dem Behälter J und
trägt dort nach den Hähnen des Behälters G reichende
Zugstangen, so daſs, wenn das Ventil x geöffnet wird,
die Hähne der Rohre g und z geschlossen werden und umgekehrt.
J. Hanlon in New-York (* D. R. P. Nr. 34075 vom 21.
Januar 1885) will Leuchtgas aus Mineralöl und
Wasserdampf für Fabriken, Leuchtthürme u. dgl. in einem angeblich leicht zu
handhabenden Apparate herstellen. Wie aus Fig. 5 bis 7 Taf. 28 zu
entnehmen, ist der das Heizgas liefernde Generator A
nebst dem Retortenraume B aus feuerfesten Steinen aufgebaut und auſsen mit
Kesselblech umgeben. Die stehenden Retorten R werden
mit Holzkohle gefüllt, die gemauerten und mit Blechmantel versehenen Cylinder H und H1 sind mit Steinen gitterförmig ausgesetzt.
Ist bei Inbetriebsetzung des Apparates im Generator A
ein genügendes Feuer vorhanden, so werden die Schieber Q und Q1
(Fig. 6),
sowie die Stopfen S bezieh. S1 auf den Rauchrohren M bezieh. M1 geöffnet. Nun wird durch das Rohr x Luft in den Generator A
eingeblasen; das erzeugte Generatorgas geht durch den Retortenraum B, verbrennt hier theilweise mit der durch die Rohre
K zugeführten Luft, um schlieſslich in den
Ueberhitzern H und H1 mit der durch Rohre L
zugeführten Luft völlig zu verbrennen, während die Verbrennungsgase durch die Rohre
M und M1 entweichen. Ist die erforderliche Hitze erreicht,
so werden die Schieber P und P1 und Q und
Q1 sowie die
Stöpsel S und S1 mittels Hebeln so gestellt, daſs der Schieber P im Rohre N das Leuchtgas
nach dem Ueberhitzer H leitet. Der Schieber Q, der Stöpsel S und der
Schieber P1 sind
geschlossen; der Schieberei läſst nun Heizgas nach H1 strömen und der Stöpsel S1 des Ueberhitzers H1 ist offen; hierbei
ist das Luftventil l geschlossen und Luftventil l1 offen. Gleichzeitig
wird in den Röhren i überhitzter Wasserdampf oben in
die Retorten R geleitet, so daſs das hier gebildete
Wassergas in die Abtheilung e tritt, hier mit dem durch
Rohr o (Fig. 5) zugeführten
Mineralöle zusammentrifft und mit diesen Dämpfen gemischt durch Rohr N in den Ueberhitzer H
tritt, um bleibendes Leuchtgas zu bilden, welches durch Rohr T und Wasserverschluſs V zum Gasometer geht.
Hat sich die Kammer H abgekühlt, so stellt man die
Schieber um, so daſs das Gasgemisch durch den inzwischen geheizten Ueberhitzer H1 geht, das Heizgas
aber durch 27, um diesen Raum wieder auf die erforderliche Temperatur zu
bringen.
Ch. Tellier in Paris (* D. R. P. Nr. 36133 vom 26. Juli
1885) legt Gewicht darauf, daſs bei der Herstellung
brennbarer Gase aus festem Brennmateriale die bei der Entgasung gebildeten
Gase durch glühende Kohle streichen. Bei dem in Fig. 12 und 13 Taf. 28
dargestellten Apparate rutschen die durch das Hebewerk M in den Trichter N gehobenen Kohlen in dem
Rohre a nach unten, werden durch den Kolben c absetzend vorgeschoben und dann durch den Kolben T im Rohre G nach oben
gedrückt. Beim Zurückgehen des Kolbens E werden zwei
Platten r von beiden Seiten durch Vermittelung des
Triebwerkes in dem Rohre G quer vorgeschoben, so daſs
die Kohle nicht zurückfallen kann. Die Verbrennung der Kohle wird dadurch
unterhalten, daſs durch die Rohre H Luft eingeblasen
wird, oder daſs die gebildeten Gase durch Rohre F, W, J
abgesaugt werden, so daſs die Luft folgt. Die nicht verbrannten Theile werden durch
Schieber n in das Rohr O
gestoſsen und fallen nach unten in Wasser. Der im Wassermantel P entwickelte Dampf tritt durch Rohr p in das Wasser der Abtheilung Q, dann durch
Rohr q in den Mantel s und
durch Rohre S in die Kohle. Zur Vorwärmung der Luft
wird diese durch Rohre z in die vier weiten Rohre W geführt, um dem durch die in diesen angebrachten
engen Rohre nach unten geführten Gase die Wärme zu entziehen.
M. Hempel in Breslau (* D. R. P. Nr. 34418 vom 19. Mai
1885) will bei Retortenöfen sowohl die sogen. Primär-,
d. i. die Vergasungsluft, als die Secundär- oder Verbrennungsluft vorwärmen. Die erstere, für die
Vergasung bestimmte Luft tritt vorn bei 1 (Fig. 3 und 4 Taf. 28) in
zwei Kanäle ein, geht nach hinten durch die Kanäle 2
und 3 und gelangt bei 4 in
den Feuerraum. Die eigentliche Verbrennungsluft tritt hinten bei I ein, geht in den Kanälen III nach vorn und trifft bei VI auf die
Generatorgase.
In der Vorderwand des Ofens ist unter der Feuerthür c
ein Wasserbehälter d derart eingesetzt, daſs das von
auſsen durch das Röhrchen e zugeführte Wasser zunächst
an dieser Stelle auf den Schlitzstein f seine kühlende
Wirkung ausübt. In Folge des beständigen Ueberlaufens des Behälters d werden die Kanten des Feuerschlitzes genäſst und
gekühlt. Das hier nicht verdampfte Wasser nimmt der unter der Herdsohle angelegte
Wasserkasten g auf. Die weitere Verdampfung dieses
Wassers erfolgt durch die Wärme, welche von der Herdsohle nach unten ausgestrahlt
und die dem Ofen in dem Wasserdampfe wieder zugeführt wird. Der Abschluſs der
Auſsenluft ist derart bewirkt, daſs die im Uebrigen dicht schlieſsende Thür h zum Entschlacken und Entaschen der Feuerung unten in
das Wasser eintaucht und hierdurch ein Wasserabschluſs gebildet wird.
Die Herdsohle ist aus eisernen Platten und Stäben gebildet, welche durch Chamotte
abgedeckt sind. Zur Reinigung der Feuerung liegen in der Sohle guſseiserne Röhren
i, die nach ihrer Entfernung in der ganzen Länge
der Sohle Schlitze hinterlassen, durch welche man mit entsprechenden hakenförmig
gebogenen Eisen das Brennmaterial durchstoſsen, auflockern und die sich bildende
Asche daraus entfernen kann, damit die allgemeine Reinigung der Feuerung nur selten
erforderlich wird. Um diese Rohre vor zu rascher
Abnutzung zu bewahren, erhalten dieselben am vorderen Ende passende Oeffnungen, so
daſs das aus dem Behälter d abflieſsende Wasser auch theilweise in das Innere der Rohre gelangt.
Besser ist die Wärmeausnutzung in dem Retortenofen von
Stedman-Stanley (vgl. Revue
industrielle, 1886 * S. 144). Die Verbrennungsgase gehen von a bis e (Fig. 10 und 11 Taf. 28)
bezieh. von A bis E nach
unten. Die Vergasungsluft tritt beiderseitig bei 1 ein
und von Kanal b bei r in
die glühende Kokesschicht. Die bei I eintretende
Verbrennungsluft trifft vom Kanäle VI aus auf die
Generatorgase.
Bei dem von J. Mc Nair in Renfrew (Englisches Patent
1885 Nr. 6059)
angegebenen Retortenofen ist die Wärmeausnutzung der
abziehenden Verbrennungsgase mangelhaft.
W. Hollweck macht im Journal für
Gasbeleuchtung, 1886 S. 409 Mittheilungen über die Münchener Generatoröfen (vgl. 1883 248 * 25.
1885 258 28). Auf der neuen Filiale der Münchener
Gasanstalt sind 6 Oefen mit je 8 Retorten im Betriebe. Ein Ofen hat etwa 1000
Betriebstage und liefert täglich im Durchschnitte für jede Retorte 255cbm Gas. Der erste geöffnete Ofen zeigte nur die
gewöhnlichen Beschädigungen und Abnutzungen der Retorten in Folge des Einbringens
und Ausziehens der Ladungen. Diese mechanische Beanspruchung des Materials ist keine
geringe, denn sie entspricht für jede Retorte bei genannten Oefen mit 1000 Tagen dem
6000 maligen Einbringen von je 138k Kohle und dem
ebenso oftmaligen Ausziehen von je etwa 83k Koke.
Die Dauer des Graphitausbrennens wechselt von 5 bis 30 Stunden, die Zwischenzeit von
einem Ausbrennen zum anderen ist anfänglich eine längere, 60 bis 65 Tage etwa; sie
verkürzt sich aber auffallend mit der rauher werdenden Innenfläche der Retorten auf
durchschnittlich 50 Tage und es ist auch im Allgemeinen ersichtlich, daſs gerade die
am meisten der Stichflamme ausgesetzten Retorten die meisten Ausbrennungen und
Ausbesserungen erfordern.
Das Ableuchten der Ofen wände und das Ueber tünchen derselben geschieht als laufende
Arbeit einmal in der Woche durch den Ofenmaurer, welcher auch regelmäſsig einmal in
der Woche die Brennerschlitze und den Heizgaskanal nachzusehen bezieh. von Flugasche
zu säubern hat. Auſser dieser letzteren Arbeit traf auf die Regenerationen keine
andere Ausbesserung als das Reinigen des ersten und zweiten Rauchkanales von
Flugasche, gerade nach einer Betriebsdauer von 2 Jahren. An den Generatoren trifft,
abgesehen von dem regelmäſsig jede Woche durch den Heizer vorzunehmenden Ableuchten
und Ueberwaschen der Auſsenwände: für je 60 Tage eine kleine Ausbesserung des
Pflasters um den Füllschacht herum und für je 400 Tage eine Neulegung dieses
Pflasters, ebenso für 450 Tage eine Neueinmauerung des Mundstückes im Aschenraume,
sowie ein neuer Füllschachtdeckel, auſserdem für 1 Generator und 1 Jahr eine
Erneuerung von ⅔ der Stäbe zum vorläufigen Roste, welcher beim Putzen eingeschoben
wird, um den glühenden Brennstoff zu tragen, während die Asche unten abgezogen
wird.
Ein Mann besorgt in einer Arbeitsschicht das Ausziehen der Asche für 6 Generatoren,
die Reinhaltung des entsprechenden Raumes und die völlige Instandhaltung der
Generatoren; während der Nachtzeit ist zur Bedienung der Generatoren Niemand
anwesend, da die Füllung der Schachte beim Ziehen der Retorten durch die
Retortenarbeiter geschieht. Nach O. Hofer (Gastechniker, 1885 Nr. 9) bewähren sich die Münchener
Generatoröfen auch in Franzstadt, nachdem die Zuführungen für die Vergasungsluft auf 430qc Gesammtquerschnitt vergröſsert sind. Bei 10,5
Proc. Unterfeuerung liefert die Retorte täglich 283cbm Gas.
Tafeln
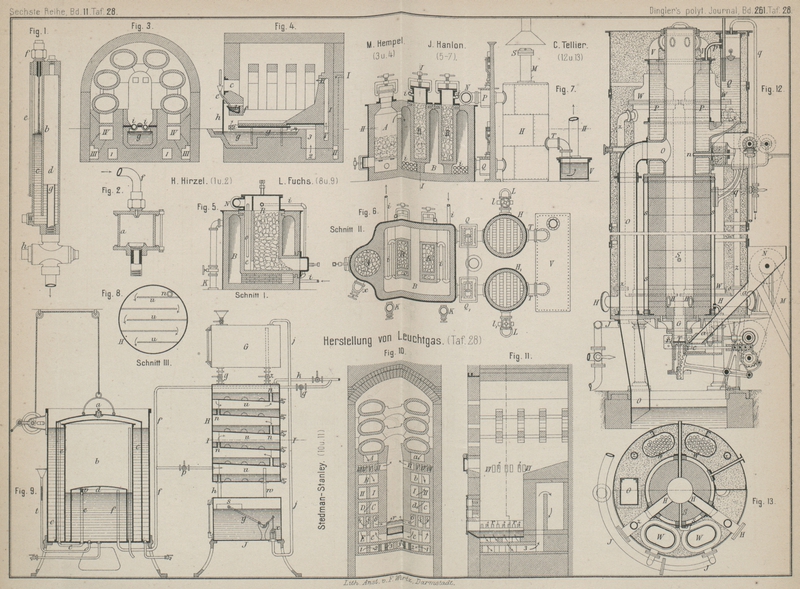