Titel: | Ueber Neuerungen im Eisenhüttenwesen. |
Fundstelle: | Band 264, Jahrgang 1887, S. 278 |
Download: | XML |
Ueber Neuerungen im Eisenhüttenwesen.
(Patentklasse 18. Fortsetzung des Berichtes S. 216
d. Bd.)
Mit Abbildungen im Texte und auf Tafel 14.
Ueber Neuerungen im Eisenhüttenwesen.
Der Hochofen-Prozeſs. (Schluſs.)
C. Stone, Ingenieur der New-Jersey Zinc-Company behandelt im Engineering
and Mining Journal, 1886 Bd. 42 S. 208Vgl. auch Berg- und Hüttenmännische Zeitung,
1886 S. 497 ff.die Darstellung von
Spiegeleisen aus Franklinit-Rückständen (vgl. 1883 248 523.):
Fig. 1., Bd. 264, S. 278
Fig. 2., Bd. 264, S. 278
Fig. 3., Bd. 264, S. 278
Fig. 4., Bd. 264, S. 278
Die New-Jersey Zink-Gesellschaft war die erste, welche in ihrem im
J. 1885 erbauten Ofen Spiegeleisen aus Franklinit-Rückständen darstellte, um daraus
schmiedbares Eisen zu erzeugen; da aber beim Puddeln zu viel Abgang entstand, so
entschloſs man sich, das Roheisen zu verkaufen; letzteres verschaffte sich dann
allmählichen Eingang durch seinen hohen Mangangehalt.
Im J. 1884 wurde ein neuer Ofen A
(Textfig. 1 und 2)
erbaut, welcher als der beste gegenüber allen bisherigen zu betrachten ist. Die
gegenwärtige Anlage besteht aus zwei Oefen, dem Ofen A,
10m,69 hoch auf 2m,44 Kohlensack-weite, sowie dem Ofen B (Textfig. 3 und 4),
10m,48 hoch auf 2m,44 Kohlensackweite. Der Wind wird für jeden Ofen in einem 21 rohrigen
Cowper'schen Ofen erhitzt, welcher mit besonderen
Thüren für die Reinigung versehen ist; beim Ofen B
stehen zwei alte Wasseralfinger-Apparate zum Ersatz. Die drei vorhandenen
Gebläsemaschinen sind für den jetzigen Betrieb unzureichend und wird von der
Dickson-Maschinenbau-Gesellschaft eine Maschine mit einem Dampfcylinder von 710mm, einem Windcylinder von 1m,524 Durchmesser und einem Hube von 910mm mit 50 Umdrehungen gebaut. Die Kessel sind
ausreichend für die Oefen und werden mit deren Dampf auch die Gebläse für die
Zinköfen, sowie die Erwärmung der Gieſsereitrockenöfen betrieben.
Die verwendeten Erze sind ein Gemenge von Willemit, Franklinit,
Zinkit und Calcit von Sterling und Franklin, Sussex County (New-Jersey). Die
gattirten Erze werden je nach Bedarf mit Kalkstein gemengt und in Röstöfen oxydirt,
in denen das Zink verflüchtigt wird, um gesammelt und als Oxyd verkauft zu werden.
Das Erz wird in den Röstöfen mit einer groſsen Menge von Anthracitförderkohle und
Kohlenstaub der Haldenplätze gemengt, welche sehr hohen Aschengehalt haben, wie
folgende Analyse zeigt:
Feuchtigkeit
4,08 Proc.
Flüchtige Stoffe
6,03
Fester Kohlenstoff
66,64
Asche
23,25
Die Kohlenasche verbleibt natürlich in den Rückständen, welche sie
rauher macht und mit Kieselerde und Thonerde verunreinigt.
Die gesinterten Rückstände kommen aus den Röstöfen theils in
flachen Kuchen, 5cm stark und 10 bis 25cm im Durchmesser, theils in Brocken von
Pulverform bis zu 5cm Korngröſse. Ehe sie zum
Hochofen gelangen, werden sie gesiebt und der Siebdurchfall weggeworfen. Das grobe
Röstgut hat folgende Zusammensetzung:
I
II
III
SiO2
19,97
23,47
21,29
Fe2O3
33,21
33,84
31,06
Al2O3
2,25
8,24
5,98
MnO
17,83
15,66
21,03
ZnO
10,74
4,98
7,84
CaO
11,96
11,04
7,60
MgO
2,30
1,84
4,01
P
0,037
–
–
Fe
23,25
23,69
21,74
Mn
13,82
12,13
16,29.
Das Röstgut ist mithin ein mageres und kieseliges Erz, enthält
jedoch genug Kalk, Magnesia und Thonerde als Fluſsmittel für die Kieselsäure. Die
Thonerde ist kein erwünschter Bestandtheil; ebenso gehört das Zink (6 Proc.) zu den
schädlichen Begleitern. Bei regelmäſsigem Ofengange wird es gänzlich ausgetrieben;
ein Theil desselben setzt sich in der Gicht als ein harter dichter Ring an, ein
anderer wird in den Gaskanälen, Condensatoren, Oefen und Kesselzügen als loses
Pulver gesammelt und ein groſser Theil geht in die Luft.
Geht der Ofen nicht gut, besonders wenn er auf längere Zeit
geschlossen werden muſs, dann wird das Zink bis nahe vor die Düsen mitgeführt und
verdichtet sich in der Beschickung zu einer teigigen unschmelzbaren Masse, welche
öfters das Entleeren des Ofens erforderlich macht; bei solcher Gelegenheit fand man
in Höhe der Düsen Kokes, welche völlig mit Zink durchsetzt waren. Auſserdem
durchdringt das Zink das Gemäuer auf 15 bis 20cm
Tiefe und macht es mürbe. Die Ziegel im oberen Theile des Ofens B enthielten nach einer 15 monatlichen Betriebsdauer
1,14 Proc. Zinkoxyd und 0,055 Proc. Manganoxyd und waren auf 20cm vom inneren Rande aus blau gefärbt.
Die verwendete Kohle ist Lehigh-Nuſskohle; sie hat gewöhnlich
einen Aschengehalt von 11 bis 12,25 Proc.
Als Kalkzuschlag wurden früher Austernschalen und etwas irischer
Kalk verwendet, später ein dolomitischer Mergel von Sing-Sing, New-York; gegenwärtig
dient ein Dolomit aus der Nachbarschaft von High Bridge (New-Jersey) und nur
gelegentlich der Stein von Sing-Sing als Zuschlag; letzterer wird ausschlieſslich
bei den Röstöfen verwendet.
Die ersten Hochöfen waren klein, wurden langsam niedergeschmolzen
und waren beständigen Störungen unterworfen, indem sie entweder ausbrachen, oder
erkalteten. Es war nichts Ungewöhnliches, daſs man 2 oder 3 Tage, ohne Eisen zu
bekommen, schmolz. Der Brennstoffverbrauch betrug bis 3t,25 auf 1t Eisen, wovon 3 bis 6t täglich gemacht wurden. Der Wind wurde auf ungefähr 189° erhitzt und
hatte 0at,3 Pressung. Die älteren Oefen arbeiteten
mit offener Gicht, waren klein und von schlechten Maſsverhältnissen, erforderten
viel Arbeit und Brennstoff, um eine geringe Menge von Spiegeleisen niedriger Güte zu
erzeugen. Die durchschnittliche Dauer einer Zustellung betrug 15 Monate.
Die neuen Oefen mit geschlossener Gicht sind gröſser als die alten
und arbeiten vortheilhafter. Der im Oktober 1883 zugestellte Hochofen B (Fig. 3) ist 9m,14 bis zum Scheitel des Chamottefutters hoch bei
1m,82 Durchmesser an der Gicht, 2m,44 an der East, 1m,52 zwischen den Düsen und 1m,35 auf
dem Herdboden. Die Glocke hat 1m,0 im Durchmesser.
Der Ofen besitzt 5 Düsen von 70mm und eine Düse
über dem Abstichloche von 50mm Durchmesser und ist
mit wassergekühlten Platten an den Düsen, Abstichloch und Schlackentrift und einer
Form von Schmiedeisen versehen, welche durch Wasserröhren von den Düsen bis zum
Mantel gekühlt wird. Unter den Düsen liegt abermals eine wassergekühlte Form. Die
Wände von den Düsen ab bis zur Gicht sind nur 35cm
dick. Die erste Betriebsdauer war 453 Tage. In dieser Zeit war der Ofen 6 Tage 15¾
Stunden der Reinigung wegen geschlossen. Die durchschnittliche Eisenerzeugung war
täglich 8460k, im Durchschnitte mit 20,74 Proc.
Mangan. 0,05 Procent des Eisens war Brucheisen, 0,66 Proc. war 10 bis 12 procentiges
Spiegeleisen, 9,46 Proc. waren 17 bis 19 procentiges Spiegeleisen und 89,83 Proc. 20
procentiges Spiegeleisen. Die verbrauchte Kohle war 0t,04 Dampferkohle und 2t,637 Kleinkohle
auf 1t Eisen. Die gewöhnliche Gicht hatte 450k Kohle, 550k
Erz und 130k Kalkstein.
Der Zinkgehalt des Erzes macht eine besondere Construction der
Gicht und die Anlage von Staubfängern nothwendig und verursacht Zeitverluste durch
das Reinigen derselben sowie der Oefen und Kesselzüge. Im offenen Ofen wird das Zink
selten hart an den Wänden; in den gröſseren geschlossenen Oefen ist es härter als
Stein und fast so schwer wie Eisen. Man erhält in den neuen Oefen nicht so viel
Zinkrauch auf 1t Eisen, aber er ist viel reicher
an Zink. Der Rauch ist von wechselndem Gehalte in den verschiedenen Theilen der
Kanäle und Staubkammern; am reichsten ist er an den Brennern der Winderhitzungsöfen,
wo er oft als metallisches Zink mit 83 Proc. Zinkgehalt herabschmilzt. Der Zinkrauch
wird auf Rohzink verarbeitet und liefert ein Metall von groſser Reinheit, völlig
frei von Arsen, Antimon sowie Blei und nur mit wenigen Hundertsteln Procent
Eisen.
Die zur Zeit gebräuchlichen Staubfänger bestehen aus einem
niedrigen guſseisernen Kasten, 1m,22 Quadrat und
0m,01 innen hoch, mit einer Reinigungsthür
versehen und sind durch 5 Rohre aus Eisenblech von 33cm Durchmesser mit einem zweiten, nur 61cm hohen Kasten verbunden, auf dessen oberer Seite vier quadratische
Reinigungsthüren angebracht sind. Die Thüren sind so aufgehängt, daſs sie, wenn sie
durch Gasdruck auffliegen, von selbst wieder zufallen. Je zwei Staubfänger gehören
zu einem Ofen. Auſserdem ist mit dem Ofen A ein
rechteckiger eiserner Thurm verbunden von 9m,75
Höhe, 1m,21 auf 1m,83 im Querschnitt, mit geneigten Blechen versehen, welche fast durch die
ganze Breite reichen und mit Explosionsthüren an jedem Bleche. Man muſs bei diesen
Staubfängern reichlich Explosionsthüren vorsehen und sie derart anbringen, daſs
keine gröſsere Gasmenge in gerader Richtung auf einmal explodiren kann.
Die gewöhnliche Schlacke nähert sich einem Singulosilicat; eine
genaue Bestimmung der passendsten Zusammensetzung ist schwer zu treffen. Die
Annahme, daſs, je mehr Kalk und Magnesia sie enthält, desto weniger Mangan darin
sei, trifft bei geringem Thonerdegehalte zu. Man hat zur Darstellung einer Schlacke
gerathen, in welcher der Sauerstoff der Basen, mit Ausschluſs von MnO, demjenigen
der Kieselsäure gleich kommt oder denselben übertrifft; dies geht an, wenn der
Thonerdegehalt gering gehalten werden kann, sonst ist es vorzuziehen, weniger Kalk
zu haben. Leider enthält die Schlacke gewöhnlich so viel Thonerde, daſs man sie
nicht gut so basisch, wie es wünschenswerth, machen kann. Gute Schlacken haben eine
flache oder erhabene Oberfläche, sind von grüner oder brauner Farbe, sind heiſs sehr
flüssig und im kalten Zustande brüchig. Arme Schlacken haben eine flache oder
concave Oberfläche, sind
dunkelgrün, zeigen dunkle Streifen und sind erkaltet gewöhnlich dicht und von
glasigem Bruche.
Die Oefen gehen am besten, wenn sie auf ihre volle
Leistungsfähigkeit betrieben werden, mit der schwersten Beschickung, welche die
Zusammensetzung des Röstgutes gestattet.
Beim Spiegeleisen unterscheidet man 5 Sorten: Brucheisen, d. i.
alles Eisen, welches weniger als 10 Proc. Mangan enthält; dann 10 bis 12, 13 bis 16,
17 bis 19 bezieh. 20 und mehr Proc. Mangan enthaltendes Product. Um sich einer
genauen Sortirung zu versichern, ist es nothwendig, jeden Abstich analysiren zu
lassen. Der Mangangehalt der Eisensorten hat allmählich zugenommen, so daſs sie
jetzt meistens über 20 Proc. Mangan enthalten:
Eisen
93,364
83,250
–
–
Mangan
3,204
11,596
19,760
21,98
Phosphor
–
0,196
0,086
0,068
Silicium
0,640
0,367
0,660
0,88
Zink
–
–
–
–
Schwefel
–
–
–
–
Kohlenstoff
2,250
4,362
–
–
An diesen Bericht knüpft Kosmann in
der Berg- und Hüttenmännischen Zeitung, 1886 S. 505
einige Betrachtungen über Oberschlesien, wo die Aufstapelung groſser Halden von den
Rückständen der Zinkdestillation schon in den 50 er
Jahren zu Versuchen geleitet hat, dieselben zu verschmelzen. Leider sind die
damaligen Schmelzversuche so miſslich ausgefallen, daſs sie, wie es den Anschein
hat, ein für alle Mal von einer Wiederaufnahme derselben abgeschreckt haben. Und
doch müſste den oberschlesischen Hüttenleuten die Verschmelzung dieser Rückstände um
so eher geläufig werden, als auf den dortigen Hochöfen rohe Eisenerze verschmolzen
werden, deren Zinkgehalt viel höher ist als derjenige in den abgerösteten
Franklinitrückständen, und in eben dem Maſse die Schwierigkeiten, mit welchen die
Entwickelung und das Auffangen der Zinkdämpfe verbunden sind, mit aller durch die
Erfahrung gewordenen Sicherheit ihre Bekämpfung finden. Auf der anderen Seite sind
die Rückstände von der Zinkdestillation bei weitem nicht so Zink haltig wie die
Franklinitrückstände und ist daher nicht abzusehen, weshalb die Verschmelzung
derselben im Hochofen nicht mit demselben Erfolge gelingen sollte wie in
Amerika.
Daſs der Eisengehalt der zur Verhüttung gelangenden Zinkerze ein
ganz bedeutender ist, ergibt sich schon daraus, daſs bisweilen auf der Sohle der
Muffeln sich geschmolzenes Roheisen vorfindet, und auch der Mangangehalt kann nicht
unbedeutend sein, da überall Anzeichen vorhanden sind, daſs, namentlich bei den
Lagern des weiſsen Galmei, neben dem Zinkcarbonat auch Mangansuperoxyd (Polianit,
Pyrolusit und Manganocker) zur Abscheidung und zur Ablagerung gekommen sind. Die zur
Zeit vorhandenen Rückstandshalden werden sich allerdings zu solcher Verschmelzung
schwerlich eignen: sie sind mit den Räumaschen der Feuerungen, mit den Brocken
zerstörter Muffeln und Thonvorlagen, mit den Kalkschlämmen von der
Röstgasentsäuerung oder durch unmittelbares Hineinpumpen der Kalkmilch aus dem
Entsäuerungsverfahren verunreinigt; aber die laufende Zinkproduction erübrigt
tagtäglich derartige Mengen von Muffelrückständen, daſs dieselben auf etwa 25
Procent der zur Zeit in die Hochöfen gelangenden metallischen Schmelzmaterialien
veranschlagt werden können.
In der Revue universelle, 1886 Bd. 19 S. 332 bringt J. Wolters beachtenswerthe Angaben über den Einfluſs eines Walz-Schlackenzusatzes im Hochofenmöller
auf die Reinheit des daraus erzeugten Roheisens.Vgl. auch Oesterreichische Zeitschrift für Berg- und
Hüttenwesen, 1886 S. 685.
Unter Walzschlacke wird ein Gemisch von 50 Proc.
Puddelofenschlacke Und 50 Proc. Schweiſsofenschlacke verstanden. Das zu verwendende
Erz ist Minette und oolithisches Erz von Luxemburg. Ein Zusatz an Schlacke im Völler
von 25 bis 30 Proc. darf nicht überstiegen werden, da sonst der Gehalt an Schwefel und Phosphor im
Roheisen zu sehr zunimmt. Eine Anzahl Analysen gibt Aufschluſs über die
Phosphorzunahme bei verschiedenen Beschickungen. Aus denselben geht hervor, daſs,
wenn alle anderen Erzeugungsumstände die gleichen bleiben, das Roheisen um so mehr
Schwefel und Phosphor aufnimmt, einer je reicheren Möllerung an Schlacke es
entstammt. Nichts desto weniger steigt oft die Zunahme des Schwefel- und
Phosphorgehaltes im Roheisen langsamer, als der Zunahme von Schlacke im Möller
entsprechen würde; man erzeugt mit einer Möllerung von 40 Minette und 60 Schlacke
ein Roheisen von 0,05 Proc. Silicium, 0,77 Proc. Schwefel, 3,23 Proc. Phosphor.
Hat man nur die Walzarbeit vor Augen, so kann man einen ziemlichen
Phosphorgehalt zulassen, wenn sonst auf die Güte wenig Rücksicht genommen wird. Was
den Schwefelgehalt betrifft, so werden dadurch beim Walzen Risse erzeugt, sobald
derselbe zu hoch ist. Aus diesen Gründen wird der Zusatz von Schlacke im Möller eine
gewisse Grenze nicht überschreiten dürfen. Setzt man diesen Schlackenzusatz im
Möller mit 25 bis 30 Proc. fest und strebt man ferner einen kalten Hochofengang an,
so kann man ein Roheisen folgender Zusammensetzung erhalten: 0,20 bis 0,30 Proc.
Silicium, 0,60 bis 0,70 Proc. Schwefel, 2,00 bis 2,50 Proc. Phosphor.
Der Schwefel- und Phosphorgehalt der Puddel- und
Schweiſsofenschlacken wechselt auf den verschiedenen belgischen Werken sehr:
Puddelofenschlacke
Schweiſsofenschlacke
Si
8,64
bis
14,20 Proc.
20,20
bis
27,80 Proc.
S
0,10
„
0,62
0,09
„
0,93
P
3,15
„
8,07
1,00
„
2,87
Die an Phosphor und Schwefel reichsten Schlacken
stammen von der Trägerfabrikation.
In Folgendem sind die (bereits S. 188 d. Bd. angeführten) Analysen
einiger Roh-, Halb- und Fertigproducte (Träger) wiedergegeben:
Roheisen
Luppeneisen
Fertigproduct
Nr. 1:
Si
0,21 Proc.
0,20 Proc.
0,17 Proc.
S
0,82
0,58
0,07
P
1,79
0,97
0,78
Nr. 2:
Si
?
0,08
Spur
S
0,53
0,10
0,07
P
2,40
1,10
0,36
Nr. 3:
Si
0,35
?
0,14
S
0,53
0,04
0,02
P
2,04
0,34
0,31
Wie ersichtlich, ist die Ausscheidung von Silicium
gering; die Roheisensorten selbst enthielten aber auch nur geringe Mengen. Die
Ausscheidung des Phosphors und Schwefels erreichte 77 bis 92 Procent der im Roheisen
enthalten gewesenen Mengen.
Manche sind der Ansicht, daſs bei einer Möllerung von 60 bis 65
Proc. Erzen und 35 bis 40 Proc. Schlacke ein zur Trägerfabrikation vorzügliches
Roheisen erhalten werden könne, wenn auf eine Singulosilicatschlacke hingearbeitet
werde. Andere hingegen meinen, daſs in diesem Falle immer schlechtes, bei späterer
Verarbeitung viel Abfall gebendes Roheisen entsteht.
Setzt man z.B. 40 Proc. Schlacke dem Möller zu und nimmt man
Rücksicht auf Brennstoffersparniſs, so wird die an Kalk verhältniſsmäſsig reiche
Schlacke ein wenig Kohlenstoff und Silicium (bis 0,1 Proc.) enthaltendes Roheisen
ergeben, der Schwefelgehalt wird trotz der groſsen Kalkmenge der Schlacke hoch sein,
der Phosphorgehalt jedoch niedrig, weil bei sehr kaltem Gange die Hochofenschlacke
Theile dieses Metalloides aufnimmt. Der geringe Kohlenstoffgehalt wird beim
Verpuddeln veranlassen, daſs die Ausscheidung der fremden Stoffe von sehr kurzer
Dauer sein wird. Andererseits wird der geringe Kohlenstoffgehalt wenig Wärme
erzeugen können, desgleichen das Silicium, welches auch in geringen Mengen vorhanden
ist; man kann sogar annehmen, daſs man Hauptmengen dieser Körper im Luppeneisen
wiederfinden wird, so daſs durch Verbrennung der im Roheisen enthaltenen fremden
Bestandtheile gar keine Wärme erzeugt werden wird. Auch wenn das Roheisen viel Phosphor enthält,
wird dieser doch nicht durch seine Verbrennung die in Folge des geringen
Kohlenstoff- und Siliciumgehaltes mangelnde Wärme ersetzen können. Der Puddler kennt
diese Roheisensorte als wenig Schlacke gebende. Man erhält auf diese Art statt einer
heiſsen, weiſsglühenden, mit gut schweiſsbarer Schlacke vermengten Luppe eine
Eisenmasse, der die Hitze mangelt und welche kalte Schlacke enthält, d.h. Schlacke,
die zu basisch ist und in Folge dessen bald fest wird. Unter dem Hammer läſst sich
die Masse schwer schweiſsen und die Schlacke schwierig entfernen, der Abfall wird
groſs, im Bruche läſst das Luppeneisen schwarze Theilchen erkennen und wird es wenig
Schwierigkeiten machen, Schlackentheile, welche weder Hammer noch Walzwerk entfernen
können, wahrzunehmen. Das Metall ist somit trocken, kurz, brüchig und schlecht
schmiedbar. Während der Vollendungsarbeit wird das Luppeneisen ebenfalls schlecht
schweiſsen, die Schlacke den verlangten Fluſs, um aus dem Packet austreten zu
können, nicht besitzen und das Endproduct reiſsen, so daſs viel Ausschuſs und lange
Enden die Folge sein werden.
Ist der Hochofengang weniger kalt, so steigt der Brennstoffaufwand
und hiermit der Gehalt von Kohlenstoff und Silicium im Roheisen, während der
Schwefelgehalt sinkt. Was den Phosphorgehalt des Roheisens anbelangt, so wird
derselbe nicht selten auf 3 Proc. und darüber steigen. Die Puddel-, Hammer- und
Walzarbeit geht besser von statten als im vorigen Falle, der Abbrand wird geringer
werden, derjenige im Schweiſsofen zunehmen.
Aus diesen beiden Fällen ist zu ersehen, daſs durch höheren
Schlackenzusatz die Herstellung eines wohlfeileren Productes insofern theuer erkauft
wird, als die Uebelstände bei den späteren Arbeiten sehr vertheuernd auf das
Endproduct wirken werden; deshalb sei wiederholt, daſs die Grenze des
Schlackenzusatzes im Möller 25 bis 30 Proc. nicht übersteigen darf.
Einem Berichte von T. Egleston (übersetzt von Ed. Sauvage in den Annales des
Mines, 1886 Bd. 9 S. 313) sind folgende Mittheilungen über die Inbetriebsetzung von Anthracit-Hochöfen in den
Vereinigten Staaten Nordamerikas entnommen: Man läſst gewöhnlich den neu
zugestellten Ofen bei offenem Gestelle einige Wochen durch Luftzug trocknen; dann
schlägt man bei offenem Gestelle im Vorherd einen ungefähr 1qm groſsen Rost, überdeckt diesen mittels eines
Gewölbes und bringt vor letzteren eine Scheidewand dergestalt an, daſs der Zug unter
der Scheidewand durch in den Ofenschacht führt. Bei geschlossener Brust muſs man
äuſserhalb des Gestelles eine Feuerung anlegen. In beiden Fällen schlieſst man alle
übrigen Oeffnungen im Gestelle und unterhält dann auf dem Roste so lange ein
Kohlenfeuer, bis sich keine Feuchtigkeitsniederschläge an den kälteren Ofentheilen
mehr zeigen. Die Dauer dieser Trocknung schwankt je nach Umständen 6 bis 60 Tage.
Unterdessen bringt man die Formen ein, untersucht, ob die Wasserkühlung derselben
und des Gestelles richtig arbeitet und setzt zuletzt, nachdem man sich auch von dem
guten Gange der Gebläsemaschine überzeugt hat, auch die Düsen ein. Dann bedeckt man
die Ofensohle 15cm mit Holzasche, Holzkohlen- oder
Anthracitklein, damit sich die später erzeugten flüssigen Schlacken nicht auf der
Sohle festbrennen. Hierauf setzt man zwei Schichten Scheitholz von 1m,20 bis 1m,35
Länge und bedeckt dieses mit trockenem Reisig und Hobelspänen. Man hat gefunden,
daſs diese Holzmengen gerade genügen, um einen regelmäſsigen Niedergang der darauf
folgenden Gichten zu erzielen und ohne Schwierigkeiten zu erhalten. Hierauf öffnet
man die Gicht, welche bis hierher zum Theile mit Blechen bedeckt war, und ordnet einen
Tonnenaufzug an, um 10 bis 20t, selbst bis 30t Anthracit einzufüllen. Derselbe darf nicht
gelagert haben, da sich sonst Schwierigkeiten bei der gleichmäſsigen Entzündung und
Verbrennung ergeben: zu demselben Zwecke muſs auch die Kohle gleichmäſsig über das
Holz ausgebreitet werden und darf dieselbe Stücke von 15cm Gröſse nicht übersteigen. Auf die Kohle kommen ⅝ ihres Gewichtes
faustgroſser Hochofenschlacken, welche bei der Herstellung von grauem Roheisen
fallen und sehr basisch sein müssen, um die saure Brennmaterialasche zu
verschlacken.
Auf die Schlacke folgen Gichten von Kohle, Schlacke, Kalk und Erz im Verhältnisse von
4 : 2 : 1 : 2 für die einzelnen Bestandtheile, jede Einheit zu 203k angenommen. Auf 4 bis 5 Gichten setzt man solche
mit immer wachsendem Erz- und Kalkgehalt, bis gewöhnliche Gichten, wie sie im
laufenden Betriebe vorkommen, erreicht sind, mit z.B. 2 Th. Anthracit, 1 Th. Kalk, 2
Th. Erz. Die Gichten müssen genau wagerecht liegen und dürfen auch zwischen den
einzelnen Kohle-, Zuschlag- und Erzstücken keine kleineren Stückchen liegen, um den
Zug nicht zu stören. Die Füllung des Hochofens dauert je nach der Gröſse 4 bis 6
Tage. Man muſs dann die Füllung sofort anzünden, weil sonst dieselbe sackt und die
Zwischenräume sich versetzen.
Die Entzündung der Holzschichten geschieht durch in den Vorherd gelegte brennende
Hobelspäne, oder mittels durch die Düsen in das Innere des Ofens eingeführter
glühender Eisenstangen. Dabei müssen alle Düsen offen sein, da sonst der Zug
ungleichförmig wirkt und auch die Verbrennung ungleichförmig stattfindet. Erscheinen
am Schlackenloche nach 6 bis 10 Stunden brennende Holzkohlen, so schlieſst man den
Vorherd fest mit Kohlenklein, welches man mit Erde und schweren Eisenplatten
überdeckt. Es findet dann ein lebhafter, bei richtiger Füllung gleichmäſsiger Zug
durch alle Düsen statt. 16 bis 20 Stunden nach dem Anzünden erscheinen brennende
Kohlen vor den Düsen, worauf man letztere sofort verschlieſst. Sind alle Düsen
gleichmäſsig hell, so öffnet man sie während einer Stunde und läſst dann schwach
gepreſsten Wind in den Ofen treten. Vorher muſs man natürlich die Kessel heizen und
die Winderhitzer durch Kohlenfeuer anwärmen. Beim Anlassen des Windes müssen die
Gichtgase brennbar sein, um die Heizung der Winderhitzer zu übernehmen. Unterdessen
begichtet man den Ofen in gewöhnlicher Weise und läſst die Schlacke ab, wenn sie
fast die Düsen erreicht. Endlich erscheint das Eisen am Abstichloche; dasselbe
erreicht die regelrechte Menge nach 2 bis 5 Wochen. Verfährt man in der
vorbeschriebenen Weise, so soll, nach zahlreichen Beispielen zu urtheilen, ein
Miſserfolg fast ausgeschlossen sein.
In Stahl und Eisen, 1887 * S. 303 ist
von J. H. C. Steffen in Luxemburg der Entwurf einer
neuen beachtenswerthen Hochofenanlage mitgetheilt. Der
Hochofen ist auf 115 bis 120t Tagesleistung
berechnet, hat etwa 390cbm Rauminhalt bei 21m Nutzhöhe und 70 bis 75° Rastwinkel. Als
Eigenthümlichkeiten sind zu erwähnen, daſs Herd und Gestell nach oben
sich erweitern und nach der Sohle in kreisrundem Einschnitte zulaufend
gebaut sind; der Querschnitt hat Kleeblattform.
Daselbst * S. 310 veröffentlicht Prof. A. Ledebur eine
Studie über die Entwickelung der inneren Form der
Eisenhochöfen.
Carl Pieper in Berlin (* D. R. P. Nr. 37101 vom 10.
Februar 1886) bringt einen eigenthümlichen Winderhitzer
in Vorschlag, welcher nach Fig. 10 bis 12 Taf. 14
einem Rippenheizkörper ähnelt, durch den die
Hochofengase hindurchstreichen, während der Wind die Heizkörper umspült; letztere
sind nach dem Entwürfe in 3 Gruppen unterhalb eines Kanales b angeordnet, mit welchem sie durch Stutzen d
in Verbindung stehen. Jede Gruppe wird aus 14 Heizkörpern c gebildet, deren Inneres oben mit den Stutzen d und unten mit den Ringkasten f in
Verbindung steht. Die Hochofengase treten bei a in den
Apparat ein, verbreiten sich im Raume b und ziehen dann
durch die Stutzen d in die einzelnen Heizkörper, um von
hier durch den Ringkanal f und das seitliche
Austrittsrohr f1 den
Apparat zu verlassen. Der Wind dagegen tritt durch die Kanäle g in den die Heizkörper enthaltenden Raum und verläſst
denselben, nachdem er sich an den Heizkörpern vorgewärmt hat, bei i. Die Heizkörper besitzen Rippen, welche nicht
senkrecht zu den Flächen der ersteren stehen, sondern nach der Richtung der
Windströmung geneigt sind, um eine bessere Aufnahme der Wärme zu erzielen. Fig. 12 laſst
erkennen, wie die Heizkörper zu einander angeordnet sind.
In dem deutschen Patente * Nr. 33417 vom 3. April 1885, 2. Zusatz zu * D. R. P. Nr.
31116 vom 17. August 1884 (vgl. 1885 257 * 236 und 1886
259 363) gibt Fritz W.
Lürmann in Osnabrück fernere Anordnungen für Lufterhitzer an, um die Verbrennungsluft auf noch höhere Temperatur, als
dies durch die früheren Einrichtungen möglich war, zu bringen und um die Luft in noch dünneren
Schichten mit dem Gas zusammentreten zu
lassen. Es soll dies dadurch erreicht werden, daſs man die Wandungen des
Feuerungsraumes aus metallenen Doppelwänden herstellt, durch welche die
Verbrennungsluft behufs Vorwärmung strömt, um durch möglichst dünne, durch
Metallwände gebildete Schlitze mit den ebenfalls sehr dünn gehaltenen Gasströmen
zusammenzutreten.
In der Zeitschrift deutscher Ingenieure, 1885 S. 652
bespricht Lürmann die in D. p.
J. 1884 251 356 erwähnten Ionischen Winderhitzer mit Vorwärmung der Verbrennungsluft und der
Gase. Am Schlusse führt Verfasser diejenigen Fälle an, in welchen die
Erhitzer angewendet werden können.
Heinrich Macco in Siegen (* D. R. P. Nr. 38285 vom 27.
Februar 1886, Zusatz zu * Nr. 33329, vgl. 1886 259 * 362)
hat seinen Winderhitzer dahin abgeändert, daſs der
Füllraum mit Ausnahme der Eintritt- und der Austrittstelle für die Gase durch
mehrere in der Stromrichtung der letzteren liegende Wände in einzelne von einander
unabhängige Kammern geschieden wird, so daſs die Gase in mehreren besonderen Strömen
den Füllraum durchziehen und denselben besser ausnutzen.
Um beim Verhütten Zink haltiger Erze den sich in den Winderhitzern ablagernden Gichtstaub zu entfernen,
schlägt Carl Boehm in Laurahütte (* D. R. P. Nr. 33105
vom 3. April 1885) vor, den Gichtstaub durch besondere für diesen Fall zu öffnende
Ventile abzublasen. Dabei werden die Gasventile und das Warmwindventil geschlossen,
jedoch die Abblaseventile geöffnet. Läſst man dann den kalten Wind in voller Stärke
durch den Apparat gehen, so soll derselbe den Gichtstaub von den Mauern lösen und
durch die am Boden liegenden Abblaseöffnungen entfernen.
Berichtigung: S. 220 d. Bd. Z. 3 v. u. lies „Toldl“ statt „Todt“.
Tafeln
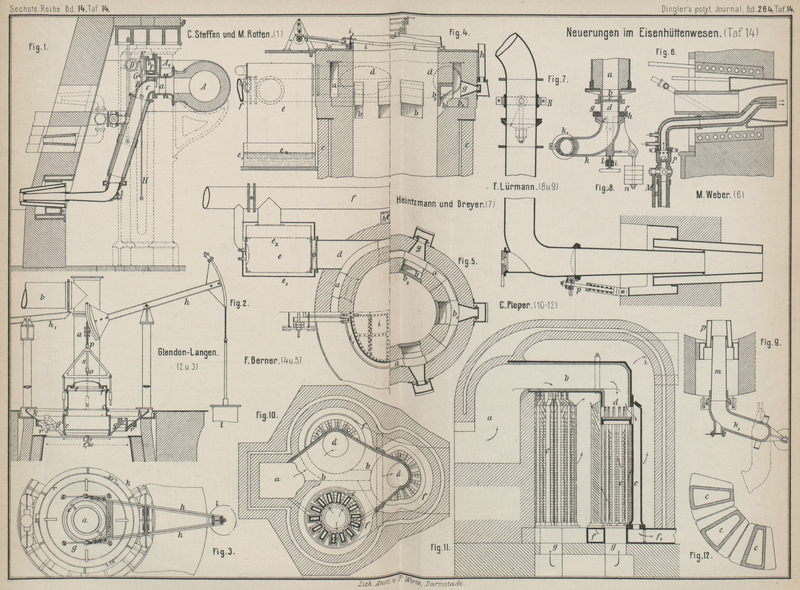