Titel: | Neuerungen in der Tiefbohrtechnik; von E. Grad in Darmstadt. |
Autor: | E. Grad |
Fundstelle: | Band 271, Jahrgang 1889, S. 289 |
Download: | XML |
Neuerungen in der Tiefbohrtechnik; von E. Grad in
Darmstadt.
Mit Abbildungen auf Tafel
14.
Gad, Neuerungen in der Tiefbohrtechnik.
Auf der im September 1888 in Wien abgehaltenen Bohrtechnikerversammlung war wohl eine
der wichtigsten zur Besprechung gelangten Fragen, die nach der für das galizische
Oelgelände geeignetsten Bohrmethode. Zunächst erhielt die Ablehnung der
Diamantbohrung allgemeine Zustimmung, weil das im Ganzen milde Gebirge diese
besondere Kraftleistung nicht verlangt, und die wirthschaftliche Lage der
Bohrunternehmer die Vermeidung der mit derselben verbundenen Mehrkosten erheischt.
Zur engeren Wahl blieb das kanadische Bohrverfahren einerseits, das Fauck'sche Freifall-Bohrsystem andererseits. Als
Ergebniſs der Besprechungen läſst sich feststellen, daſs die kanadische Methode bis
zu 300m Tiefe ihre Schuldigkeit im milden Gebirge
durchaus thut, daſs aber für gröſsere Tiefen, und bei härterem Gesteine, das Fauck'sche System eine entschiedene Ueberlegenheit
gewinnt, ohne indeſs im Wirkungsbereiche des kanadischen Verfahrens irgendwie gegen
dasselbe zurückzustehen. Wohlbemerkt ist dabei die Verwendung des neuesten
Bohrgeräthes von Fauch zu verstehen, wie es von der
Firma Ed. Hasenörl in Wien vollständig mit allen
Verbesserungen angefertigt wird. Das Geschäftsprogramm von 1889 dieser Fabrik gibt
über alle Einzelnheiten der Vorrichtungen, sowie über deren Beschaffungskosten
genauen Aufschluſs. Die Hauptsachen sind folgende:
Bohrmeiſsel (Fig. 1 und 2) werden in genau
abgepaſsten Nummern von 61 bis 680mm
Schneidebreite aus bestem, zähen und gut härtbaren Guſsstahle genau nach der Form
geschmiedet. Die Seitenschneiden sind nach der Kreislinie des Bohrloches gekrümmt.
Der starke Bund a dient einem bequemen Unterfassen bei
etwaigen Meiſselbrüchen. Die Verbindung des Meiſsels mit dem oberen Theile des
Abfallstückes findet mittels des patentirten Doppelkeilverschlusses b statt. Die an Bund und Hülsen angebrachten Marken
müssen über einander gestellt werden, und lassen sich dann allein die beiden kleinen
zugehörigen Keile eintreiben, was am besten wechselseitig durch kupferne Hämmer
erfolgt, bis das volle Aufliegen Bund gegen Bund erreicht ist. Das Lösen der
Verbindung geschieht sehr rasch mittels eigener Nasenkeile, welche in die sogen.
Auskeillöcher a (Fig. 3) eingetrieben
werden.
Die Bohrstange (Fig. 3) hat den Zweck, das
Gewicht des Abfallstückes zu erhöhen und so die Wirkung des Aufschlages zu
verstärken. Die Herstellung geschieht in genau zu dem sonstigen Bohrgeräthe
abgepaſsten Nummern aus weichem, zähem Bessemerstahle oder Schmiedeeisen. Zur
Verbindung dient der Doppelkeilverschluſs.
Der Nachnahmebohrer (Fig. 4, 5 und 6) wird unter Umständen
zwischen Meiſsel und Bohrstange eingefügt, falls eine Erweiterung des Bohrloches, z.B. zur
Erleichterung der Verrohrung, geschehen soll. Der Körper ist aus bestem
Feinkorneisen geschmiedet, trägt oben einen Zapfen a,
unten eine Hülse b, beides für
Doppelkeilschloſs-Verbindung, während in der Mitte zwei Schneidebacken c aus Prima-Tiegelguſsstahl angebracht sind, welche
leicht mit anderen Gröſsen auszuwechseln gehen. Die Druckvorrichtung zum Festhalten
der Schneidebacken liegt geschützt im Inneren des Apparates und ist aus Fig. 6
ersichtlich. Zum Einlassen in das Bohrloch werden die Schneidebacken mit einem
Drahte d (Fig. 5), der über die
Meiſselschneide führt, zusammen gebunden. Beim Aufschlagen auf die Bohrsohle
zerreifst der Meiſsel den Draht, und die Schneiden treten unter der Verrohrung aus
einander.
Das Freifall-Instrument (Fig. 7) ist ein
verbessertes Fabian'sches Freifallstück. Das
schmiedeeiserne Abfallstück a wird mit der Hülse b, in derem ausgebohrten Inneren es seine Führung
findet, durch den sogen. Fangkeil c verbunden, welcher
in den beiden diametral gegenüberstehenden Längsschlitzen d der Hülse auf und nieder gleitet. Festgehalten ist dieser Fangkeil c (Fig. 8) durch einen
zweiten darunter liegenden Keil c1, welcher seinerseits durch einen eingetriebenen
conischen Stift r2
befestigt wird. Durch ein eigens hierfür in die Hülse gebohrtes Loch wird dieser
Stift eingebracht und durch die Hülse selbst am Herausfallen verhindert. Am unteren
Ende besitzt das Abfallstück Bund e und Zapfen f zum Anschluſs an die Bohrstange mittels des
Doppelkeilverschlusses, sowie einen Fangbund g zum
Erfassen im Falle eingetretenen Bruches.
Die Hülse, aus allerbestem Feinkorneisen und auſserordentlich stark im Fleische
ausgeschmiedet, besitzt oben Schraubenzapfen h und Bund
i zur Verschraubung mit dem Gestänge mittels eines
Verbindungs-Mutterstückes. Die Schlitze d sind oben zu
Keilsitzen k erweitert, deren Sitzflächen als
wesentliche Neuerung durch eingelegte und auswechselbare Stahlsegmente l (auch Fig. 9) gebildet sind.
Unten erweitern sich die Schlitze, ebenfalls in verbesserter Weise, zum sogen.
Sicherheitsschloſs m. Beim Einlassen des Bohrzeuges in
das Bohrloch ruht der Fangkeil in diesem Sicherheitsschlosse und stöſst beim
etwaigen Aufsitzen des Meiſsels unterwegs an die obere Auskehlung an, wodurch
verhindert wird, daſs sich das Abfallstück auf den Keilsitzen oben fängt und dann
bei plötzlichem Abfalle Schaden anrichtet.
Der selbsthätige Freifallbohrer (Fig. 10) ist besonders
für Durchmesser von 300 bis 1000mm und Bohrtiefen
über 300m bestimmt. Dieses Instrument besteht aus
Meiſsel a, Nachnahmebohrer und Schwerstange in einem
Stücke b, Freifall-Instrument c und Rahmen d. Das Freifall-Instrument hat
statt eines festen Fangkeiles deren zwei, von denen der untere f zur Führung und zum Einhängen in das Sicherheitsschloſs bestimmt und
unbeweglich ist, während der obere g, der eigentliche
Fangkeil, ein in Stahllagern drehbarer Flügelkeil ist. Das Fangen des Abfallstückes
findet in der
bekannten Weise statt, das selbsthätige Abwerfen dagegen durch den Druck der
schiefen unteren Fläche der Schiene h gegen den
Fangkeil. Die obere Fortsetzung der Hülse des Freifall-Instrumentes bildet eine
längere Stange i von quadratischem Querschnitte, die in
dem Oberstücke d1 des
Rahmens ihre Führung findet, denselben auch beim Umsetzen mitnimmt und oben die
Schraube k zur Verbindung mit dem Gestänge trägt.
Während der Abfall stattfindet, hebt das Instrument den Rahmen, welcher aus 4
Rundeisenstangen e und den Verbindungsstücken d und d1 besteht, etwas in die Höhe, während welcher Zeit
das Umsetzen erfolgt.
Das Bohrgestänge (Fig. 11) setzt sich aus
Quadrateisenstäben von 5m Länge zusammen, die aus
bestem Schmiedeeisen gefertigt sind. Die Verbindung der Stücke findet durch stark
conische Gewindezapfen a und gleiche Mutterschrauben
b statt, wobei bekanntlich im Vergleiche zu cylindrischen Verschraubungen erheblich an Zeit gespart
wird. Unterhalb des Gewindezapfens dient der obere Bund c für den Aufzugskloben (Gestängestuhl), der untere Bund d für das Untergreifen der Gabel (Schlüssel). Die
Seitenlänge von 20mm reicht völlig aus, um selbst
auf bedeutenden Tiefen Festigkeit zu gewähren und Prellung, sowie Umsetzung auf das
Freifall-Instrument zu übertragen. Ueberall dort, wo das Gestänge mit Kloben oder
Gabel angefaſst werden muſs, ist sein Querschnitt verstärkt. Für ausnahmsweise
Tiefen ist ein Gestänge von 23mm Seitenlänge des
Querschnittes zu wählen.
Die Bohrtransmission (Fig. 12 und 13) ist nach
folgenden Gesichtspunkten angeordnet:
1) Gute Schwengelprellung als Hauptbedingung für rationelle Freifallbohrung.
2) Möglichst hoher Hub, von 1 bis 1m,5, ohne
Verwendung von Bohrcylindern.
3) Hohe Lage des Schwengelkopfes, um den Bohrschacht entbehrlich zu machen.
4) Rücklegbarer Schwengelkopf, ohne Rückbewegung des ganzen Schwengels.
5) Anordnung der Theile so, daſs alle Bohrarbeiten (Bohren, Einlassen, Ausziehen,
Löffeln) nach einander durch den Bohrmeister von einem bequemen Standpunkte aus
bewirkt werden können.
6) Verwendung einer einfachen Dampfmaschine, ohne Umsteuerung, für alle
Verrichtungen.
Diesen Ansprüchen ist durch folgende Anordnungen genügt: Die Riemenscheibe a empfängt die Bewegung von der Dampfmaschine und
erhält die Hauptwelle b, auf der sie aufgekeilt ist, in
fortwährender Umdrehung in der angedeuteten Richtung. Von dieser Welle wird durch
Anziehen der verschiedenen Handhebel die Kraft entweder zum Bohren, oder zum
Aufholen, Einlassen und Löffeln entnommen.
Soll gebohrt werden, so wird mittels Handhebels das auf
der Welle mittels Nuth und Feder verschiebbare Zahnrad c zum Eingriffe mit dem Holzkämme tragenden Rade d gebracht. Das letztere dient zugleich als Kurbelscheibe und hat vier in
verschiedenen Abständen von der Achse befindliche Löcher, so daſs der Hub des
Bohrschwengels je nach Belieben von 1 bis 0m,5
verändert werden kann. Die Uebertragung auf den Schwengel e (Fig.
12) geschieht durch die eiserne Pleuelstange f (Fig.
12), deren Angriffspunkt an demselben jedoch nicht starr ist, sondern
durch ein in einem Rahmen g (Fig. 12) verschiebbares
Lager gebildet wird. Der Schwengel besteht aus zwei starken zusammengefügten I-Eisen, welche, da keine Zurückschiebung nöthig ist, bei
h (Fig. 12) fest gelagert
sind. Durch ein am rückwärtigen Theile des Schwengels aufgebrachtes und beliebig
verschiebbares Gegengewicht i nun wird das Bohrzeug
nicht allein abbalancirt, sondern durch das überwuchtende Gegengewicht selbst in die
Höhe gedrückt und bewirkt, daſs das Schwanzende des Schwengels mit Gewalt auf den
Prellstock k schlägt, wodurch die wirksame Prellung
erfolgt. In diesem Augenblicke jedoch hat die Pleuelstange noch nicht den tiefsten
Punkt erreicht, sondern macht, Dank dem beweglichen Lager, noch einen kleinen todten
Gang, wodurch eben vermieden wird, daſs sich die Erschütterung der Prellung auf die
Pleuelstange und weiterhin fortpflanzt. Die über den Schwengelkopf l gelegte Bohrkette m
(Fig. 12)
ist auf der Trommel n (Fig. 13) befestigt und
kann mittels der aus Wurmrad o und Schnecke p (Fig. 13) bestehenden
selbstsperrenden Nachlaſsvorrichtung durch Umdrehung des Handrades q während des Bohrens allmählich nachgelassen werden.
Die Kreissegmentform des Schwengelkopfes bewirkt, daſs die Bohrkette stets genau in
der Mitte des Bohrloches verbleibt. Soll dasselbe für die Nebenarbeiten frei gemacht
werden, so ist der Bolzen r herauszuziehen, das
Kreissegment einfach zurückzulegen, und dann der Bolzen wieder vorzustecken.
Um aufzuholen wird mittels des Förderhebels die lose auf
der Hauptwelle b sitzende Hülse s (Fig.
13), auf der das Zahnrad t und die mit dem
Frictionsconus versehene Bremse u aufgekeilt sind,
gegen die fest auf der Achse sitzende Frictionshülse v
angedrückt, und dadurch die Förderseiltrommel w in dem
Sinne des Pfeiles bewegt. Erfahrungsmäſsig werden damit 2 Stück Gestänge, d.h. der
gewöhnliche Stangenzug von 10m Länge, in 10 bis 20
Secunden gezogen.
Um das Bohrzeug einzulassen wird der Rückgangshebel
angezogen. Derselbe hebt das bewegliche Lager x (Fig. 12) der
kurzen Welle g (Fig. 12), die das mit dem
groſsen Zahnrade z in Eingriff befindliche Zahnrad t (Fig. 13) und das Keilrad
u (Fig. 13) trägt, wodurch
letzteres an die Keilrillen der Frictionshülse v (Fig. 13)
angedrückt und die Fördertrommel w entgegengesetzt dem
Sinne des Pfeiles bewegt wird. Das Einlassen geschieht mit noch gröſserer
Geschwindigkeit als das
Aufholen, und kann das Bohrzeug durch die Bremse a1 (Fig. 13) jeden Augenblick
abgebremst werden.
Die Bewegung der Löffelseiltrommel b1 endlich erfolgt durch Niederdrücken des
Löffelhebels, wodurch das mit dem Hebel c1 (Fig. 12) verbundene
bewegliche Lager d1
(Fig. 13)
der Löffeltrommelwelle gesenkt und Keilrad e1 gegen das auf der Hauptwelle sitzende Keilrad f1 (Fig. 13) gedrückt wird.
Beim Einlassen des Schlammlöffels, sowie beim Spiel desselben, dient diese Friction
zugleich als Bremse.
Die Bohrtransmission wird in drei Gröſsen, und zwar für Tiefen bis 300m, für solche von 300 bis 500m, und von 500 bis 1000m vorräthig gehalten. Eine vollständige
Bohrvorrichtung mit Bohrzeug und Dampfmaschine, jedoch ohne Bohrthurm, mittlerer
Gröſse, stellt sich auf rund 12000 M.
Für Bohrtiefen bis 300m kann die Bohrung mit
Handbetrieb vor sich gehen. Zum Abbohren von etwa 200m hat Fauck eine vereinfachte transportable
Handbohrungseinrichtung mit 1m,25 Schwengelhub und
mit einem beweglichen Bohrgerüste anstatt eines Bohrthurmes construirt, welches
alles in allem etwa 4500 M. kostet.
In Verbindung mit dem Fauck'schen Bohrsysteme wird die
Verrohrung mit patentgeschweiſsten Bohrröhren in ganz zu Tage reichenden
Röhrentouren vorausgesetzt. Die überflüssige Verrohrung soll nach Beendigung der
Bohrarbeit entfernt werden, sei es, um nur die doppelte Verrohrung zu beseitigen,
sei es, um durch Abschneiden der Röhren an standfesten Schichten gewissermaſsen eine
verlorene Verrohrung herzustellen.
Dazu dient das Fauck'sche Kohrabschneid-Instrument (Fig. 14). Der schneidende
Theil ist das Stahlrad a, welches mittels eines
Stahlbolzens, um den es leicht drehbar ist, in dem Schiebergleitstücke b befestigt ist. Dieses findet im Körper des
Unterstückes c seine Führung. Drei starke Bolzen d verbinden dieses Unterstück unverrückbar mit dem
Oberstücke e. An das Gewinde f des Oberstückes wird ein Röhrengestänge (gewöhnliche Gas- oder
Brunnenröhren) geschraubt, mittels dessen das Instrument eine fortdauernde Umdrehung
erhält. Ein Zuggestänge (gewöhnliche Rundeisenstangen) reicht im Anschlusse an die
Stange g durch das Röhrengestänge zu Tage und dient
dazu, den Keil h von Zeit zu Zeit hochzuziehen und
dadurch das Gleitstück mit dem Stahlrade vorzuschieben. Das Hochziehen geschieht
durch Drehung eines Schlüssels an dem am oberen Ende des Zuggestänges
angeschweiſsten Stücke mit Flachgewinde. Wenn der Vorschub des Gleitstückes nicht
mehr ausreicht, werden zur weiteren Verstärkung des Umfanges des Unterkörpers dem
Gleitstücke gegenüber die Stahlsegmente i mit zwei
Druckwalzen k aufgeschraubt. Zum Auseinandernehmen des
Instrumentes muſs die Schraube l etwas gelüftet
werden.
Daſs das Fauck'sche Bohrsystem ein für die Verhältnisse
der galizischen Oelfelder durchaus geeignetes ist, geht aus den 100 und mehr Bohrungen hervor, die
in den letzten 3 Jahren daselbst bereits nach demselben ausgeführt sind. Vor allen
Dingen muſs die verhältniſsmäſsige Billigkeit der Arbeit, trotz, oder vielleicht
gerade wegen der Verwendung nur des trefflichsten Materials für alles Geräth
hervorgehoben werden. Es ist die weitere Verbreitung dieses Apparates in allen den
galizischen Formationen ähnlichen Geländen zu empfehlen.
Nächst den groſsen Fauck'schen Tiefbohreinrichtungen
sind von neueren Erzeugnissen der Hasenörl'schen Fabrik
noch besonders zwei kleinere Apparate zu erwähnen.
Der eine ist eine neue Wasserspül-Bohrvorrichtung nach Fauvelle, für Tiefen bis 200m und
Durchmesser von 10 bis 18cm. Der zweite besteht
aus einem transportablen Bohrtriangel von Eisenröhren für kleine Spül- und
Trockenbohrungen. Zwei von den Füſsen werden unten durch eine feste Spreizstange,
oben an der Spitze, mit dazwischen gelegtem Haspel, zu einem starren Dreieck
vereint, während der dritte Fuſs in einem Charnier gegen die beiden anderen drehbar
bleibt.
Ueber eine interessante Verwendung der Bohrung zum Einbau von Pfählen berichtete
Ingenieur Herr Béla Zsigmondy, wie er sie selbst beim
Donau-Brückenbau bei Krems ausgeführt hatte. An der Stelle des dritten Pfeilers war
man auf ein Felsbett von Gneiſs gestoſsen, woselbst der Strom mit 3m Geschwindigkeit die Rammarbeit vom schwimmenden
Gerüste sehr erschwert haben würde. Mit einem Blechrohre von 40cm lichten Durchmesser als Bohrtäucher durchfuhr
man das Gerölle und den Donauschotter. Dann wurde mit einem Flügelmeiſsel die
Bohrsohle geebnet und womöglich noch 20 bis 30m
tiefer abgebohrt, unter Einführung eines engeren Rohres von 35cm lichter Weite zur Absperrung von Sand und
Schotter. Darauf fand ganz regelrechte Tiefbohrung von 1 bis 1m,5 mit Handschwengel und Freifall statt, wobei
ein besonders construirter Handbagger den gewöhnlichen Schlammlöffel vertrat. Nach
Erreichung der wünschenswerthen Tiefe führte man die Pfeiler durch die Bohrröhren
ein und legte sie mit grobkörnigem Donaukies fest, worauf das Herausziehen der
Röhren behufs weiterer Verwendung erfolgte. Auf diese Weise waren damals schon 52
von den erforderlichen 72 Pfeilern eingebracht worden.
Von den Fragen, welche die Bohrtechniker-Versammlung weiterhin beschäftigten, waren
besonders noch zwei von hervorragender Bedeutung.
Die erste betraf die etwaige Anwendung von Torpedos zum Ergiebigmachen stiller
Oelbrunnen. Anbetracht der Thatsache, daſs in der Pennsylvanischen Oelregion das
Torpediren der Oelbrunnen die Regel ist, muſs es auffallen, daſs in den
mitteleuropäischen Oelfeldern, wo oft die Verhältnisse den amerikanischen gleichen,
dieses alt erprobte Hilfsmittel noch keinen rechten Eingang gefunden hat. Ein
maſsgebender Versuch ist
neuerdings gemacht. Herr Fauck hat am 26. September
1888 auf dem Fauck- und Diener'schen Werke in Polana durch den Sprengtechniker Herrn Tirmann von der Aktiengesellschaft Dynamit Nobel eine Versuchssprengung ausführen lassen.
Das betreffende Bohrloch, Nr. 18, war 320m tief,
bis 207m mit 18cm-Röhren verrohrt, welche bei 17m vom
Tagkranze begannen. Bei 270m Teufe war
ursprünglich der gröſste Oelzufluſs von 10 Faſs im Tage gewesen, nachträglich aber
auf 2 bis 3 Faſs im Tage herabgesunken. An dieser Stelle, über welcher noch 120m Wasser stand, wurde die Sprengung angesetzt. Der
Versuchstorpedo enthielt 50k Dynamit Nr. 1. Die
Zündung geschah elektrisch. Die Wirkung war, daſs die tägliche Ausbeute von 2 auf 30
Faſs stieg. Wir wollen hoffen, daſs dieser schöne Erfolg für Europa gleich Epoche
machend wirkt, wie das wirksame Ansprengen der „Woodin Well“ 1866/67 durch
den amerikanischen Colonel Roberts dazumal für die
Pennsylvanier.
Bei der zweiten Frage springt der materielle Vortheil nicht gleich so in die Augen.
Es handelt sich dabei um den Wunsch, über die auszuführenden Bohrungen recht genaue
Bohrregister, Profilaufnahmen und dergleichen Nachrichten zu erhalten, welche es der
Wissenschaft besser als bisher ermöglichen, der Praxis in die Hand zu arbeiten. Mit
der Zeit würde sich eine bessere Gepflogenheit hierin, gerade für die Herren
Praktiker, gut bezahlt machen.
Wir verlassen nunmehr die III. Bohrtechniker-Versammlung, welche zu Pfingsten, den 9.
Juni 1889, in Budapest in der IV. eine Nachfolgerin erhalten soll.
Wenn es sich bei den besprochenen Einrichtungen von Fauck um Geräthschaften handelt, welche ihre Existenzberechtigung bereits
erstritten haben, kommen wir jetzt zu einer Erfindung, welche ihre Sporen erst
verdienen soll. Es ist dies ein selbsthätiger Tiefbohrapparat für Kurbelbetrieb und
Wasserspülung, erfunden von Herrn Em. Przibilla in Köln
a. Rh. und in allen industriellen Staaten patentirt.
Der Schwerpunkt der ganzen Einrichtung liegt durchaus in dem „Bohrautomaten“, wie der Erfinder die in Fig. 15 bis
24
dargestellten Theile nennt, und welche in 10 Nummern für Rohre von 83 bis 305mm lichter Weite hergestellt werden sollen.
Der an das hohle Bohrgestänge angeschraubte Kopf a
bildet mit der Stange a1 zusammen ein solides massives Stück, und gleitet letzteres in der Hülse
b auf und nieder. Zwischen den Kopf a und die Hülse b ist eine
Feder d eingelegt. In der Stange a1 ist ein Keil c befestigt, welcher sich mit derselben in zwei
Schlitzen e der Hülse b
bewegt.
Der Keil c ist an seinen unteren Flächen abgeschrägt und
tritt durch die Wirkung der entsprechend abgeschrägten unteren Endflächen der
Schlitze e bei seiner tiefsten Stellung in die
seitlichen Aussparungen e1 der Schlitze ein. Auſserdem bewegt sich der Keil c mit seinen beiden über den Umfang der Hülse b hinausreichenden
Enden noch in zwei ferneren Ausschnitten l eines über
die Hülse b gestülpten Rohres i (Fig.
23 und 24). Die in die Ausschnitte l eingreifenden
Enden des Keiles c sind oben gleichfalls abgeschrägt,
da auch das obere Ende der Schlitze e in gleicher Weise
abgeschrägt angeordnet ist.
Ein zweiter, in dem unteren massiven Theile der Hülse b
befestigter Keil g, der rechtwinklig zu dem Keile c steht und gleichfalls durch die Röhre i hindurchgeht, gleitet senkrecht in zwei anderen
Schlitzen n der letzteren auf und nieder. Das Rohr i ist in Fig. 23 und 24 noch
besonders gezeichnet, um die Lage und Form der Schlitze zu zeigen. Unten ist dieses
Rohr ausgeschnitten, um für die Bewegung des breiteren Meiſselblattes Raum zu
lassen, sobald letzteres von der Sohle aufgehoben wird, während das Rohr i auf der Bohrlochssohle stehen bleibt.
In die Hülse b ist unten die Stange f, und in die Muffe f1 dieser Stange der Meiſsel m eingeschraubt.
Die Stange f ist durch einen Bolzen mit der Hülse b und der Meifsel durch eine über seine Verschraubung
gestülpte Büchse h so mit f1 verbunden, daſs eine Lösung dieser
Theile im Bohrloche fast unmöglich, über Tage aber durch leichten Hammerschlag
erreichbar wird. Zu diesem Behufe wird f1, sowie der Meiſselbund m1 mit einem sechskantigen, unten weiteren
Prisma versehen und die Büchse h genau darauf passend
so angeordnet, daſs sie f1 und m1
zugleich umfaſst und in ihrer gegenseitigen Lage festhält.
Mit dem Kopfe a ist endlich das Führungsrohr k verschraubt, welches den ganzen Apparat umschliefst
und mit seiner oberen Verlängerung k1 noch einige Meter über diesen Kopf
hinaufreicht.
Die Wirkungsweise ist folgende:
Aus dem Zustande der Ruhe (Fig. 16), also der Keil
c mit dem oberen Ende des Schlitzes e nahezu in Berührung und die Feder d ausgelöst, beginnt die Abwärtsbewegung. Zunächst
drückt das Gestänge mittels des Kopfes a die Feder d zusammen, und der Keil c
an der Stange a1 klinkt
dieselbe am Ende des durch den Balancirhub begrenzten Weges in die Aussparung e1 (Fig. 15) ein. Vorerst
bleibt der Meiſsel auf dem Boden stehen, während das Gestänge durch das Einklinken
des Keiles c eine Rechtsdrehung von der Breite des
Ausschnittes e1 macht.
Bei dem nun beginnenden Anhübe, wobei der eingeklinkte Keil c die Hülse b, Stange f und Meiſsel m mitnimmt, bleibt das Rohr i so lange auf der Rohrsohle stehen, bis die in dessen
Ausschnitten l sich bewegenden Enden des Keiles c mit ihren abgeschrägten oberen Flächen gegen die
ebenso abgeschrägten Endflächen der Ausschnitte l
stoſsen. Das Rohr i wird dadurch etwas angehoben,
gleitet aber in Folge der oben schiefen Endflächen seiner Schlitze l auf dem Keile c ab und
fällt wieder mit einer kleinen Rechtsdrehung zu Boden, wobei es die Hülse b, wegen Verbindung durch den Keil g, und mit der Hülse auch den nun schwebenden Meiſseltheil in der
Breite des Schlitzes e bezieh. der gleichbreiten
Einklinkung e1 mit
herum nimmt. Bei der Rechtsdrehung der Hülse b gleitet
aber auch die Aussparung e1 so weit nach rechts, daſs der stehen bleibende Keil in den langen
Schlitz e tritt, wodurch die Hülse ihren Halt verliert
und abfällt. Zugleich entspannt sich auch die Feder und treibt mit aller Spannkraft
den mit der Hülse b verbundenen Meiſsel auf die
Bohrsohle.
Es ergibt sich mithin bei jedem Kurbelhube ein kräftiger Schlag unter regelmäſsigem
Meiſselumsatze.
Das Wasser zum Spülen tritt aus dem hohlen Gestänge in den mit einer Bohrung
versehenen Kopf a und durch dessen Seitenschlitze a0 in das Innere des
Apparates, von wo es erst am Meiſselblatte bezieh. auf der Bohrlochsohle wieder
austreten kann, alsdann aber zwischen Bohrlochwand und Rohr k bezieh. k1
wieder aufsteigt. Die Verlängerung des Rohres k durch
das Stück k1 über dem
Kopfe a ist erforderlich, um eine Erweiterung des
Raumes für die Wasserspülung nicht zu dicht über dem Apparate eintreten zu lassen.
Die durch den gröſseren Querschnitt veranlaſste Verringerung der Spülkraft bewirkt
Niederschlag von Bohrschmant, welcher in dem Rohrtheile k1 als Probe gesammelt werden kann. Auch
zur Aufnahme von Nachfall und anderen schädlichen Gegenständen wird sich dieser Raum
nützlich erweisen. Der Röhrenzug k und k1 soll zugleich für
eine glatte Ausführung des Bohrloches sorgen und „Füchse“ verhüten.
Das Gestänge besteht aus dünnen Eisenröhren, deren Gewicht durch Holzumhüllung in dem
nassen Bohrloche zum gröſsten Theile aufzuheben
ist. Die geringe Hubhöhe des Meiſsels von nur 20cm
ermöglicht schnellfolgende und gerade Stöſse – bis zu 120 in der Minute –, die durch
Federkraft gleiche Energie wie sonst durch Belastung erhalten.
Daſs dieser neue Apparat in der Theorie ungemein viel verspricht, ist keine Frage; es
handelt sich nur darum, ob die Praxis unsere Hoffnung bestätigen wird. Daſs sich
diese Wasserspülmethode für galizische Erdölbohrungen besonders gut eignen soll, wie
der Erfinder behauptet, will ich nicht von vornherein bestreiten, möchte nur zu
bedenken geben, daſs der unermeſsliche Oelzustrom im Kaukasus ein nasses Bohrloch
wohl leicht bewältigen kann, während man bei dem mäſsigen Oeldrucke in den
pennsylvanischen Brunnen längst die „trockene“ Bohrung zur Regel erhoben hat.
Der galizische Bohrunternehmer würde wohl vor Annahme einer Wasserspülmethode die
Frage zu erwägen haben, ob sich die Verhältnisse seines Terrains mehr jenen von
Baku, oder doch nicht etwa mehr denen von Oilcity nähern.
Auf dem Felde der Diamantbohrmaschinen haben zwei groſse amerikanische Firmen
Apparate von verbesserten Formen gebracht, welche indeſs grundsätzliche Abänderungen
gegen frühere Constructionen nicht aufweisen.
Die eine dieser Maschinen, und zwar die von der M. C. Bullock
Manufacturing Comp. hergestellte, zeigt nur Veränderungen in der Stellung
des Dampfcylinders, sowie in der Anordnung des Rädergetriebes.
Die zweite, von der American Diamond Rock Boring Comp.
gelieferte Maschinerie ist einmal auf einem Fahrzeuge, ein anderes Mal auf einer
festen Unterlage angeordnet und charakterisirt sich in beiden sonst gleichen
Einrichtungen dadurch, daſs das Rädergetriebe als Vorschubmechanismus aufgegeben und
durch hydraulische Cylinder ersetzt ist.
Eine durchgreifende Aenderung hat aber eine dritte amerikanische
Bohrmaschinen-Gesellschaft getroffen, und zwar die der American Well Works, Aurora, Illinois, welche zum ersten Male wieder seit
längerer Zeit auf amerikanischem Boden einen Mechanismus hergestellt hat, mit
welchem ein leichter Wechsel der Stoſsbohrmethoden einerseits und der
Drehbohrmethoden andererseits stattfinden kann. Bekanntlich sind derartige
Vorrichtungen auf Grund der Erfindungen von Köbrich, Olaf
Terp u.a. diesseits des Ozeans längst im Gebrauche, während sich drüben
diese einzelnen Systeme grundsätzlich wider einander abgegrenzt gehalten haben.
Der sinnreichste Theil dieser sehr erfindungsreichen neuen Maschinerie ist der
Vorschubcylinder (Fig. 25), welcher für den Fall der Drehbohrung mit Spülung zur Regelung
des Vorschubes für das Hohlgestänge bestimmt ist.
Der Cylinder wird im Gebrauchsfalle mittels des Bügels a
an einen Flaschenzug gehängt, welcher seinerseits die Befestigung in der Spitze des
Bohrthurmes erhält. Das untere Ausfluſsrohr b des
Cylinders wird mittels eines Wirbelstückes mit dem Hohlgestänge verbunden, und
enthält dieses Wirbelstück ein Ventil, durch welches man genau den Zufluſs des
Wassers aus dem Cylinder in das Hohlgestänge regeln kann. In den unteren Theil des
Cylinders führt das Einflufsrohr c das mittels einer
Dampfpumpe eingepreſste Wasser ein, welches den Cylinder von unten bis oben füllt
und im Steigen den Kolben d mit der hohlen Kolbenstange
e hebt, sofern nämlich dies Wasser durch das Ventil
abgeschlossen bleibt. Je nach Maſsgabe der Oeffnung des Ventiles findet ein
entsprechendes Maſs Wasser Ausfluſs durch die Oeffnungen f des Kolbenrohres und von dort in das wirbelnd angeschlossene
Hohlgestänge, welch letzteres mithin mit dem Gewichte
auf die Bohrsohle drückt, welches ihm seitens des hebenden Wasserdruckes übrig
gelassen wird. Beim Beginne der Bohrung wird es meist erforderlich sein, die Last
des noch kurzen Gestänges durch angebrachte Gewichte zu verstärken, zumal es rathsam
ist, gewissermaſsen einen Ueberschuſs von todter Last auf der Bohrsohle vorräthig zu
halten, diesen aber im richtigen Verhältnisse durch die Wirkung des
Vorschubcylinders aufzuheben. Es ist ersichtlich, daſs in dem Falle, wenn
angehäuftes Bohrmaterial auf der Bohrsohle den Wasserausfluſs aus dem Bohrgestänge
hemmen sollte, das im
Gestänge gestaute Wasser einen erhöhten Druck auf den Kolben im Vorschubcylinder
üben muſs, was ein Anheben des Gestänges zur Folge hat, bis der Ausfluſsweg für das
um so kräftiger herausdrängende Spülwasser frei wird. Zu vermeiden bleibt, durch
vollen Schluſs des Ventiles die Spülung ganz zu unterbrechen, weil sich dann der
Bohrschlamm leicht verdichten und das Bohrzeug festklemmen kann.
Diese Vorschubvorrichtung gestattet, eine Strecke von fast der lichten Höhe des
Bohrthurmes ohne wesentliche Unterbrechung abzubohren, nur beschränkt durch die
niedrige Drehvorrichtung auf dem Erdboden einerseits und die Länge des bis an die
Spitze des Bohrthurmes gezogenen Cylinders andererseits. Sobald der Kolben im
Vorschubcylinder dem Boden desselben nahe kommt, ist nur der Cylinder selbst am
Kolben des Flaschenzuges herunterzulassen, was während des Fortganges der Arbeit
geschehen kann. Nähert sich schlieſslich der Cylinder zu sehr der Drehvorrichtung,
so wird er im Ganzen hochgezogen. Zur Förderung des Bohrkernes, sowie zur Einfügung
eines neuen Gestängetheiles ist allerdings Unterbrechung der Spülung geboten, welche
durch Schluſs des Ventiles erfolgt. Vor Unterbrechung der Spülung behufs
Einschraubung eines neuen Gestängetheiles wird meist der Bohrschmant noch einmal
künstlich aufgerührt, um das schnelle Setzen zu verhindern, und das Einschrauben
selbst mit groſser Geschwindigkeit ausgeführt.
Derselben Gesellschaft ist es gelungen, ein sehr sinnreiches Verfahren bei
Brunnenbohrungen nach Wasser in Ausführung zu bringen. Es sind nämlich Verrohrungen
mit einem stählernen Treibschuhe mittels der Drehvorrichtung unter Spülung direkt
durch lose Alluvialschichten und Triebsand eingedreht worden. Dabei wurde die Stärke
der Spülung so abgepaſst, daſs der Bohrschmant auſsen zwischen Rohrwand und
Bohrlochswand haften blieb und, insofern er aus Lehm, Thon und anderen zähen
Ablagerungen bestand, sich zu einer festen Wand verdichtete, welche die Klüftungen
des Bohrloches verstopfte und jeden Nachfall verhinderte. In sandigen Schichten
wurde der mangelnde Bindestoff durch Einfüllen von Lehm u.s.w., mit dem Spülwasser
zugleich, in das Innere der Verrohrung eingebracht und dadurch die Standfestigkeit
des Triebsandes auſserhalb erreicht. Je nach der Natur der Schichten eignen sich zu
deren Verdichtung verschiedene Mittel, so z.B. für weichen Lehm, Moorboden u. dgl.:
Sand, Sägemehl, Kalk, Cement; für Muttererde: Getreide und andere Samen, Stroh,
Häcksel u.s.w. Ein Auf- und Abbewegen der Verrohrung, das sich mit der Drehung
derselben vereinigen läſst, erleichtert das Austreten der Kernreste, sowie der etwa
eingefüllten Stoffe. Unter Umständen soll sich solche künstliche Wand derart
erhärten, daſs die nachträgliche Entfernung der Verrohrung möglich wird.
Zuerst ist eine derartige Bohrung in „Sulphur Mine“ in Louisiana in den
lehmigen und sandigen Alluvialschichten der Mississippi-Niederung 100 bis 200m tief mit 12cm
starken Röhren geglückt. Es sind dann in New Orleans mehrere andere nachgefolgt, und
zwar durch zähe und lose Schichten hindurch, wie sie für Tiefbohrungen kaum
schlimmer gedacht werden können. An einer Stelle ist es dort gelungen, eine 17cm,5 starke Verrohrung von 7500k Gewicht mittels einer Maschine von 6
152m,7 tief in 48 Stunden durchzutreiben,
wobei die Schwierigkeiten mit der Tiefe nicht wesentlich wuchsen, und ein weiterer
Fortgang nur wegen Mangels an passenden Röhren unterblieb. Es ist keine Frage, daſs
man alles daran setzen muſs, um möglichst schnell durch solche klebrigen und
haltlosen Schichten durchzukommen.
Eine Frage, welche innig mit der Diamantbohrung zusammenhängt, ist neuerdings in den
Vordergrund des Interesses getreten. Es ist dies das Bestreben, die durch die
Diamantbohrkrone geschnittenen Kerne über Tage in ihrer richtigen Stellung zu
Orientiren, um das Streichen und Fallen der durchsunkenen Schichten danach ermessen
zu können. Ich habe in D. p. J. 1888 270 163 über das Instrument des Engländers Herrn Percy Fry Kendall berichtet, welches mir diese Aufgabe
am einfachsten und vollkommensten zu lösen scheint; doch möchte ich nicht versäumen,
auf zwei sehr beachtenswerthe Erfindungen deutscher Landsleute in dieser Richtung
aufmerksam zu machen.
Das erste dieser Instrumente ist von Köbrich nach einer
Idee von Wolf construirt und bereits mehrfach mit
vollem Erfolge benutzt. Die Beschreibung durch Herrn Köbrich findet sich in der Zeitschrift für Berg-,
Hütten- und Salinenwesen im preuſsischen Staate, 1888 S. 255.
Das Wesen des Apparates besteht darin, daſs sich unterhalb einer Rutschschere ein scharfer Meiſsel befindet, über derselben in einem geschützten Lager ein Kompaſs.
Meiſselschneide und Mittagslinie des Kompaſs liegen in einer Senkrechtebene. Mittels
der Rutschschere wird nun mit dem Meiſsel ein scharfer Schlag auf den oben
geglätteten Kern im Bohrloche gegeben und abgewartet, bis ein mit dem Kompaſs in
Verbindung gebrachtes Uhrwerk denselben arretirt haben muſs. Alsdann holt man den
Apparat, dann den noch abzulösenden Bohrkern auf, und es erhellt, daſs die
Abweichung der arretirten Magnetnadel von der Mittagslinie ebenfalls die Abweichung
des Einstriches im Kerne von derselben Linie angeben muſs.
Der zweite Apparat wird vom Herrn Ingenieur Lubisch
angegeben. Er besteht sehr einfach aus einer glatten, unten etwas zugeschärften
Muffe, von etwas gröſserem Durchmesser als der erbohrte Kern, in deren Inneres ein
Stahlstift von etwas gröſserer Länge, als der Unterschied zwischen den Durchmessern
von Muffe und Bohrkern beträgt, hineinragt. Beim Ueberstülpen dieser Muffe über den
auf der Bohrsohle aufstehenden Kern ritzt alsdann der Stahlstift einen senkrechten
Strich in den Rand desselben. Durch sorgfältiges Zusammenschrauben des Gestänges,
wobei die Verbindungsstellen mit feinen übergerissenen Strichen bezeichnet werden, und möglichst
gerades Einlassen desselben strebt man dahin, den Stahlstift möglichst in derselben
Senkrechtebene zu erhalten. Nach dem Heben des Bohrkernes kann dann dem eingeritzten
Striche am Rande dieselbe Orientirung gegeben werden, wie sie der Stahlstift beim
Einlassen gehabt hat. Bei geringeren Tiefen arbeitet dieses Instrument ganz
zufriedenstellend. Grundbedingung ist, daſs Reinheit der Bohrsohle und Glätte des
Bohrkernes das Ueberstülpen der Muffe über den letzteren gestatten.
Von ausgeführten Tiefbohrungen ist die auf Place Hébert in Paris vollendete
artesische Brunnenbohrung die bedeutendste. Diesseitige Angaben finden sich darüber
in D. p. J. 1888 270
252.
In Bezug auf Verwendbarkeit von Diamantbohrmaschinen sind zwei lehrreiche Beispiele
anzuführen, welche beweisen, daſs auch in unseren Gebirgen diese wirksamste aller
Bohrvorrichtungen als ultima ratio die wesentlichsten Dienste leisten kann.
Von zwei Bohrlöchern, welche 1887 bei Kiedrich im Rheingau nach Mineralquellen
abgeteuft waren, hatte bei dem einen der Stoſsbohrer in Tiefe von 68m,5 eine steil einfallende Quarzschicht nicht zu
durchbrechen vermocht, war vielmehr stets seitlich abgelenkt und abgeschliffen
worden. Es wurde dann im August 1888 die Hilfe der Diamantbohrung in Anspruch
genommen, welche der Ingenieur Hugo Lubisch mit einer
englischen Diamantbohrmaschine leistete. Herr Lubisch
bohrte das ganze Bohrloch mit einem langen, genau passenden Kernrohre nach und
brachte Kerne von mondsichelförmigem Durchschnitte zu Tage, wodurch sich die
Abweichung des früheren Bohrloches von 19mm auf
1m ergab.
Auch die Bohrung des Herrn Fabrikanten A. Neubecker in
Offenbach a. M., welche im Februar 1888 auf 275m
Tiefe eine reiche Lithionquelle angeschlagen hat, ist mit Meiſsel und Wasserspülung
ohne Freifall begonnen und langsam fortgeführt worden, bis das erreichte feste
Gestein des Rothliegenden die Benutzung der Diamantbohrmaschine nahe legte, welche
wohl allein das schwierige Gebirge bewältigen konnte.
Viele Fragen betreffs der Diamantbohrmethode wird übrigens der demnächst erscheinende
III. Band der Tecklenburg'schen Tiefbohrkunde, welcher
dieses Feld behandelt, lösen und dadurch den Stand der Tiefbohrtechnik wiederum um
einen wesentlichen Schritt fördern.
Tafeln
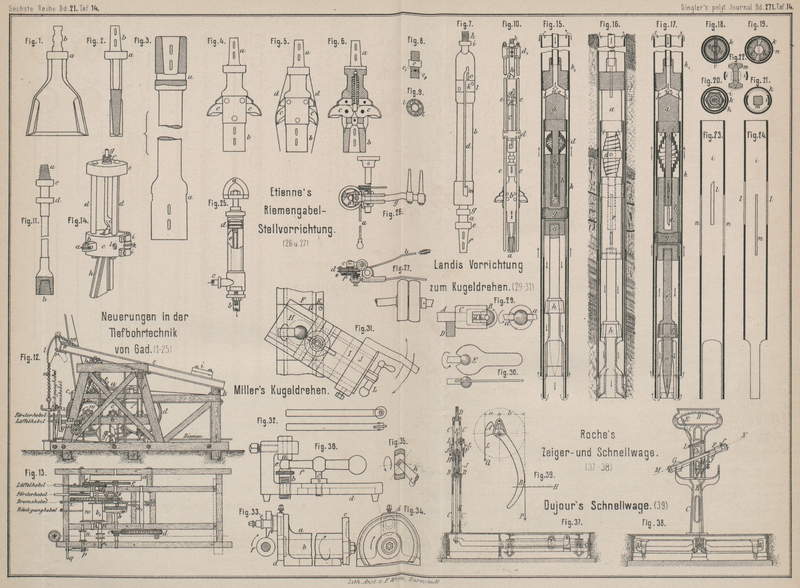