Titel: | Zur Entwickelung der deutschen Koksindustrie. |
Autor: | W. Koort |
Fundstelle: | Band 271, Jahrgang 1889, S. 445 |
Download: | XML |
Zur Entwickelung der deutschen
Koksindustrie.
Mit Abbildungen auf Tafel
24.
Zur Entwickelung der deutschen Koksindustrie.
Die Kokserzeugung in den hervorragendsten Staaten der Erde betrug vor einigen Jahren
nach Angabe von Simmersbach in der Zeitschrift für Berg-, Hütten- und Salinenwesen, 1887
S. 325, mehr als 24 Millionen Tonnen jährlich, welche einen Gesammtwerth von etwa
266 Millionen Mark darstellen. An dieser Production ist Deutschland mit etwa 4⅓
Millionen Tonnen im Werthe von etwa 39 Millionen Mark betheiligt. Nach den
Veröffentlichungen des Kaiserl. statistischen Amtes betrug die Ausfuhr an Koks im
Reiche im J. 1888 9176838 MC. und die Einfuhr 2686352 MC. Solche Ziffern beweisen,
daſs die Kokserzeugung eine Groſsindustrie geworden ist. Sie steht in enger
Beziehung zur Roheisenerzeugung, denn ohne Koks würde es nicht möglich sein, solche
Mengen, nämlich mehr als 100t Roheisen täglich in
einem Hochofen zu erzeugen.
Wenngleich die Anfänge der Steinkohlenverkokung in England zu suchen sind, so ist
doch gerade in unserem Vaterlande dieser Industriezweig durch Einführung besserer
Ofensysteme zur höchsten Blüte gelangt.
Ursprünglich verkokte man Steinkohle unter Luftzutritt in Meilern, später traten an
Stelle der letzteren offene Verkokungsöfen mit rechtwinkeligen Formen, die sogen.
Feld-, Stadel- oder Schaumburger Koksöfen. Die letzteren sind noch nicht vollständig
verschwunden. Man benutzt sie gegenwärtig noch in Schlesien und im Schaumburgischen
(Obernkirchen), weil die hier vorkommende Wälderthonkohle sich stark aufbläht und
daher eine Verkokung in geschlossenen Oefen nicht gestattet. Darauf folgte eine
dritte Art Oefen, die Back-, Rund- oder Bienenkorböfen, bei welchen die Erhitzung
der Kohle im Ofen oben anfängt und die Koksbildung daher von oben nach unten
erfolgt. Dieselben werden wegen des geringen Ausbringens (etwa 55 Proc.), da ja ein
beträchtlicher Theil der Kohle im Ofen verbrennt, und der verhältniſsmäſsig hohen
Betriebskosten bei uns nicht mehr gebaut, wohingegen sich dieselben in England und
den Vereinigten Staaten noch groſser Beliebtheit erfreuen.
Erst seit der Mitte dieses Jahrhunderts gelangten Ofenconstructionen in Aufnahme, bei
welchen die Erhitzung des Verkokungsraumes von auſsen geschieht, so daſs eine
Verbrennung der Kohle im Ofen möglichst vermieden wird. An Stelle der halbkugelförmigen Räume der
Rundöfen traten lange prismatische Verkokungskammern. Man unterscheidet gegenwärtig
Koksöfen mit senkrechter und mit wagerechter Längsrichtung des Verkokungsraumes.
Zu den ersteren gehören der Appolt'sche Ofen und die
neueren Constructionen von Bauer (1888 270 1), welche beispielsweise in Westfalen, Böhmen und in
Frankreich (Creuzot) zur Ausführung gelangt sind.
Zu den Oefen mit horizontalem Verkokungsraume gehören unter anderen die Oefen von Haldy, Smet, François-Rexroth und Coppée. Letzterer vereinigt die schmalen, hohen lichten
Formen des Smet'schen Ofens mit den bereits bei François-Rexroth vorhandenen senkrechten Wandkanälen.
Trotz der guten Erfolge, welche mit dieser Construction erzielt wurden, hat dieselbe
doch weitere Abänderungen erfahren.
Das Verdienst, den Coppée-Ofen in allen seinen Theilen
verbessernd behandelt zu haben, gebührt der Firma Dr. Otto
und Comp. in Dahlhausen an der Ruhr. Zur besseren Verbrennung der Gase
verbindet genannte Firma einige von den senkrechten Wandkanälen mit den unter der
Ofensohle befindlichen heiſsen Luftkühlkanälen und läſst diese vier Kanäle auf der
Höhe der Ofenwand in einen wagerechten Sammelkanal münden, von welchem aus Pfeifen
in jeden senkrechten Wandgaskanal einmünden. Die Verbrennungsluft wird auf diesem
Wege aus den Kühlkanälen bis zur Mischung mit den aus den Retorten in die
senkrechten Wandkanäle austretenden Gasen auf eine sehr hohe Temperatur gebracht.
Auf diese Weise ist es der genannten Firma gelungen, einen Ofen herzustellen,
welcher nach Simmersbach bei 120 Centner Füllung, 70
Proc. Ausbringen, 48stündiger Betriebsdauer und 330 Betriebstagen jährlich eine
Leistung von 775t Koks, also mehr als das Doppelte
der Leistung eines Rundofens ergibt, welcher bei 120 Centner Füllung, dreitägiger
Brennzeit, 55 Proc. Ausbringen und 330 Betriebstagen jährlich etwa 333t Koks liefert. Dieser Otto'sche Ofen ist gegenwärtig in vielen hundert Ausführungen
vorhanden.
Von den bisher genannten Koksofensystemen unterscheidet sich wesentlich der Lürmann-Ofen, bei welchem ununterbrochen eine Mischung
von mageren Kohlen und Fettkohlen oder Steinkohlenpech unter Druck verkokt wird.
Zwar können in allen neueren Koksöfen Mischungen von mageren und fetten Kohlen
verarbeitet werden; kein System soll sich jedoch zur Verarbeitung von sehr mageren
Mischungen so gut eignen wie die Lürmann'schen
Koksöfen. Zwar sind viele von den Lürmann-Oefen nach
kurzem Betriebe wieder abgebrochen worden, was jedoch nicht beweist, daſs die Oefen
nicht im Prinzipe gut und auch dauernd leistungsfähig sind. C. Blauel äuſsert sich auf Grund mehrjähriger Erfahrungen hierüber in Stahl und Eisen, 1889 S. 34, wie folgt:
Zunächst erforderte die nicht einfache Luft- und Gasführung eine ganz
auſsergewöhnliche Aufmerksamkeit auf den Betrieb, aber trotz gröſster Vorsicht wurde man
leicht getäuscht und nahmen die Gase gern nicht die vorgeschriebenen, sondern
Nebenwege. Hierzu fand sich bei den ersten Lürmann-Oefen um so eher Gelegenheit, als die Mauerwerksconstruction zwar das
Aeuſserste in Dünnheit der Wände und Ersparniſs an feuerfestem Materiale leistete,
dafür aber auch der Verband kein ganz genügender war, noch mehr aber, weil an
einigen Punkten die Temperatur so hoch stieg, daſs kein feuerfester Stein
standhielt.
In der ersten Zeit traten deshalb die meisten Betriebsstörungen dadurch ein, daſs die
Gaskanäle zuschmolzen, wenn die Oefen eine kurze Zeit gut gegangen waren. Die Folge
war dann, daſs diese sofort schlecht gingen, und einen Koks sehr geringer Qualität
mit sehr viel Abfall lieferten.
So gehörte ein groſses Maſs von Ausdauer und feste Ueberzeugung von der Güte des
Prinzipes dazu, um bei den langwierigen Kinderkrankheiten der Lürmann-Oefen den Muth und die Lust am Betriebe
derselben nicht zu verlieren.
Meistens sind die Oefen nach mehr oder weniger gründlichen Versuchen aufgegeben und
nur an ein paar Orten durch allmähliche Aenderungen nach den Erfahrungen des
Betriebes dahin gebracht, daſs die Erfolge gute geworden sind, so daſs bei guter
Betriebsleitung fortwährend schöner Koks erzielt wird, ohne daſs die Oefen mehr
leiden als andere Koksöfen.
Es werden jetzt in Lürmann-Oefen ohne Schwierigkeit 40
bis 45 Proc. ganz magere, anthracitartige Kohlen ohne eine Spur von Backfähigkeit
mit 60 bis 55 Proc. guten fetten Kokskohlen bei einem Ausbringen von etwa 80 Proc.
verarbeitet. Der Koks ist sehr fest und dicht, und hat sich auch bei der Verwendung
im Hochofen kein wesentlicher Unterschied gegen gewöhnlichen Koks finden lassen.
Statt fetter Kohlen läſst sich den mageren Kohlen auch Schwarzpech (Steinkohlenpech)
zusetzen, und wird aus etwa 5 Th. Anthracitkohlen und 1 Th. Pech in Lürmann-Oefen ein guter Koks hergestellt. Auſser diesen
Mischungen von ganz fettem und ganz magerem Materiale eignen sich zur Verkokung in
Lürmann-Oefen alle Kohlensorten oder Gemische von
solchen, welche etwas zu mager sind, um ohne Druck und hohe Temperatur ordentlichen
Koks zu geben. Die vor Jahren gemachten, meist nicht erfolgreichen Versuche sind
nicht maſsgebend, da sie geschahen, als die Lürmann-Oefen in den schlimmsten Kinderkrankheiten lagen, welche sich
naturgemäſs bei Verwendung gasreicher, halbmagerer Kohlensorten, deren Verkokung
mehrfach versucht ist, am meisten fühlbar machten.
Obige Mischung von ganz magerer und fetter Kohle, welche zur Verkokung in den Lürmann-Oefen mit Erfolg verwendet ist, gibt im
Laboratorium 85 bis 86 Proc. Koks und 14 bis 15 Proc. Gas, dagegen z.B. halbmagere schlesische Kohle
etwa 65 Proc. Koks und 35 Proc. Gas. Dieser Unterschied ist natürlich zu groſs, als
daſs nicht wesentliche Rücksicht beim Betriebe darauf zu nehmen wäre, und dazu war
man vor mehreren Jahren noch nicht in der Lage. Heute aber halte ich den Betrieb mit
solchen schwachbackenden, gasreichen Kohlen eher für leichter als für schwerer, wie
mit der Mischung aus Anthracit und fetten, starkbackenden Kohlen.
Anlagekosten und Arbeitslöhne stellen sich bei den Lürmann-Koksöfen etwas höher als bei den meisten anderen Arten, dagegen
sind aber die verwendeten Kohlen, wenn man eine Mischung von Anthracit und
Fettkohlen nimmt, billiger, und das Ausbringen ist ein höheres, so daſs sich die
Herstellungskosten des Koks doch ganz wesentlich niedriger stellen als aus
Fettkohlen. Hierüber kann sich Jeder leicht Rechenschaft geben, der berücksichtigt,
daſs z.B. an der Ruhr der Doppelwaggon Anthracitgrus jetzt gegen 30 M. billiger ist
als die gleiche Menge guter, fetter Kokskohlen.
Bei Verwendung mancher halbmagerer Kohlen wird der Nutzen mehr darin liegen, dass man
in den Lürmann-Oefen einen Koks von erheblich besseren
Eigenschaften erzielt als in anderen, während die Herstellungskosten wahrscheinlich
nicht wesentlich niedriger sein werden.
C. Blauel ist zu der Ueberzeugung gekommen, daſs die Lürmann-Oefen trotz aller anfänglichen Miſserfolge noch
eine gute Zukunft haben werden. Je mehr die Fettkohlen abnehmen, desto mehr dürften
die Lürmann-Oefen an Bedeutung gewinnen.
Gegenwärtig stehen zu Kohlscheid bei Aachen 20 Oefen im Betriebe.
Eine besondere Construction erhalten diejenigen Koksöfen, welche auf Gewinnung der
Nebenproducte (Theer, Ammoniak) abzielen. Den Franzosen gebührt das Verdienst, die
Vorgänger auf diesem Gebiete der Technik zu sein, während in Deutschland mit den Hüssener-Carvès-Oefen zu Bulmke bei Gelsenkirchen der
Anfang gemacht wurde zur Begründung einer Groſsindustrie in der angegebenen
Richtung.
Eine bahnbrechende Neuerung brachte indessen erst die Ofenconstruction von Gustav Hoffmann, welcher zum Zwecke der Vorwärmung von
Gas und Verbrennungsluft die gewöhnlichen Coppée-Oefen
mit Siemens'schen Regeneratoren verband. Auch diese
Erfindung ist von der Firma Dr. Otto und Comp. in die
Praxis eingeführt worden, und zwar mit ausgezeichnetem Erfolge, wie dies durch die
zahlreichen Anlagen bekundet wird.
In der Oesterreichischen Zeitschrift für Berg- und
Hüttenwesen, 1888 S. 530 ff., beschreibt W.
Jicinzky eine derartige Einrichtung, wie sie gegenwärtig zur Theer- und
Ammoniakgewinnung gebräuchlich ist.
Die betreffenden Koksöfen haben die Ausdehnungen der gebräuchlichen Otto'schen Koksöfen, nämlich im Lichten 10 × 1,6 × 0m,5, mit einer Füllung von 3500 bis 4000k, bei gröſseren Oefen bis zu 5700k Das Innere des Ofens (Fig. 1 und 2) steht durch die
Gasrohre g und absperrbaren Ventile a mit der Vorlage V in
Verbindung. Letztere geht in eine Röhre GaR (Fig. 6) über,
welche meist 1m tief unter der Erde zu dem zur
Erzeugung von Theer und Ammoniak bestimmten Raume führt. Ableitung und Bewegung der
Gase aus dem Ofen wird durch die Rohre g, V und GaR bis in das Ammoniakhaus durch einen Exhaustor EX (Fig. 5 und 6) vermittelt. Nach dem
Passiren des letzteren werden die vom Ammoniak und Theer befreiten Gase in einem
Gasometer bekannter Construction gesammelt. Von diesem wird ein groſser Theil der
Gase durch ein unterirdisches Rohr, welches in die beiden parallel zur Ofengarnitur
im Niveau der Sohlkanäle S1 und S2
laufenden Rohre g1 und
g2 (Fig. 1 und 2) mündet, in den Koksofen
zurückgeführt. Diese beiden Gasrohre sind mit so vielen durch Hähne oder Ventile
absperrbaren Rohrstutzen h1 und h2
versehen, als es Oefen gibt. Sie haben den Zweck, das zurückgeleitete Gas in diese
Sohlkanäle zu bringen oder einzublasen.
Der Sohlkanal des Ofens ist in der Mitte bei b durch
eine Querwand getheilt; derselbe enthält seitlich gegen die eine Ofen wand so viele
Oeffnungen c1 und c2, als senkrechte
Wandkanäle w1 und w2 in der Seitenwand
des Ofens vorhanden sind, und mit einander in Verbindung stehen.
Alle senkrechten Kanäle w1 und w2
münden in einen oberen ungetheilten Gaskanal O, welcher
längs jeden Ofen Widerlagers hinläuft.
Ferner besitzt die ganze Ofengarnitur die beiden Generatoren R1, und R2 je 2m hoch und
1m breit, welche parallel zu den Gasröhren g1 und g2 liegen und durch
Oeffnungen d1 und d2 mit den Sohlkanälen
S1 und S2 verbunden sind.
Jeder Generator besitzt so viele nach aufwärts gerichtete Ausfluſsöffnungen d, als die Ofenzahl der Garnitur beträgt.
Auſserdem stehen diese Generatoren einerseits mit einem Ventilator durch eine Röhre
v, v1 und v2 (Fig. 6) und am anderen
Ende durch einen Kanal mit der Koksofenesse E in
Verbindung. Diese Gasgeneratoren enthalten zu etwa ⅔ ihrer Höhe in
Scheiterhaufenform lose über einander gelegte feuerfeste Ziegel, wodurch den
durchziehenden Gasen eine groſse Berührungsfläche dargeboten wird.
Der Ventilator Z (Fig. 5 und 6), welcher am besten im
Ammoniakhause untergebracht ist, bläst beständig eine gewisse Menge atmosphärischer
Luft durch die Windleitung v abwechselnd in die
Generatoren R1 und R2 ein, um die zur
Ofenbeheizung verwendeten Gase zur Verbrennung gelangen zu lassen.
Bei dem Ofengange werden die aus dem Ammoniakhause kommenden Gase nur in die Gasrohre
g1 geleitet, und
mittels des Rohrstutzens h1 in jeden Sohlkanal S1 so viel Gase eingelassen, als zur Erhitzung des
Koksofens nöthig erscheint.
Zugleich mit diesen Gasen kommt, wie schon früher kurz erwähnt, frische Luft vom
Ventilator in den Generator R1, wird daselbst an den glühenden Ziegeln bis zu 1000° erhitzt, und strömt
durch die Oeffnungen d1
ebenfalls in den Sohlkanal S1, wo die beiden Ströme Gas und Luft bei der hohen Temperatur und Mischung
vollständig verbrennen, und im brennenden Zustande durch die Seitenöffnungen c1 und die
Senkrechtkanäle w1 in
den oberen Gaskanal O gelangen, von hier aus durch die
Senkrechtkanäle w2 und
Oeffnung c2 in den
Sohlkanal S2
herabsteigen, um endlich längs des Generators R2, dessen Ziegel sie noch recht in Glut versetzen,
den Weg zur Esse zu finden.
Es ist selbstverständlich, daſs bei diesem Verlaufe die Rohrstutzen h2 geschlossen sind,
ebenso die vom Ventilator kommende Windleitung v2 zum Generator R2.
Nach etwa einer Stunde dieses Ganges werden die betreffenden Ventile umgeklappt, so
daſs augenblicklich der umgekehrte Weg eingeschlagen wird.
Der Rohrstutzen h1 und
die Windleitung v1
werden geschlossen, dafür jene h2 und v2 geöffnet. Es gelangen die Gase in den Sohlkanal
S2, vermischen sich
und verbrennen daselbst mit der in dem Generator R2 sich erhitzenden Luft, passiren aufsteigend die
Wandkanäle w2, den
oberen Gaskanal O, absteigend die Wandkanäle w1, Sohlkanal S1 und Generator R1, an den sie noch den
Rest ihrer hohen Temperatur abgeben und mit etwa 420° zur Esse gelangen.
Wird ein Ofen gezogen, oder will man denselben einige Zeit kalt stellen, so sperrt
man die Ventile o ab; ebenso kann man durch Absperrung
der Hähne h1
h2 und Oeffnungen d1
d2 das Einblasen des
Gases in den Sohlkanal hindern.
Man hat es also ganz und gar in der Hand, den Ofengang zu reguliren und den
Verkokungsprozeſs durch Steigerung der Temperatur, durch Mehreinlassen des Gases zu
beschleunigen oder zu verlangsamen, es ist dies ein reiner Retortenprozeſs, wie man
sich ihn nicht besser denken kann. Der Prozeſs dauert 30 bis 48 Stunden.
Das Ausbringen an Koks ist relativ um 6 bis 7 Proc. höher, und zwar nur wegen des
möglichst vollständigen Luftabschlusses, der bei diesen Koksöfen eine Grundbedingung
ist.
Werden wagerechte Gaskanäle gewählt (Fig. 3), so streichen die
Gase einmal in der Richtung abcd und dann umgekehrt in
der Richtung dcba. Man gibt jedoch den senkrechten
Wandkanälen den Vorzug, weil hierbei die Koksöfen stabiler sind und die Wandungen
dünner gehalten werden können.
Hinsichtlich des Vorganges im Ammoniakhause ist folgendes zu erwähnen. Die von den
Koksöfen mittels Exhaustor angesogenen Gase, Welche bei der Destillation
westfälischer Kohle aus 0,61 Proc. Benzindampf, 1,63 Proc. Aethylen, 0,43 Proc.
Schwefelwasserstoff, 1,41 Proc. Kohlensäure, 6,49 Proc. Kohlenoxydgas, 53,32 Proc.
Wasserstoff und 36,11 Proc. Methylwasserstoff bestehen, gelangen durch die Röhre F zuerst in den sogen. Gaskühler K (Fig. 4 und 5). Derselbe besteht aus
einem Eisencylinder mit den beiden Böden i, die eine
Reihe von kleineren Böden l fassen, durch welche stets
frisches Wasser von dem oberen Raume m nach dem unteren
Raume n und dann durch das Rohr p hindurch abflieſst, während das Gas, von dem Einmündungsrohre f kommend, nach aufwärts strömt, sich abkühlt und durch
Rohr q einem zweiten bezieh. einem dritten genau so
construirten Gaskühler zugeleitet wird.
Von den Gaskühlern strömt das Gas zu den Gaswäschern W,
welche ebenfalls aus Eisencylindern gröſserer Dimension bestehen und in ihrem
Inneren, je 10cm von einander entfernt, gelochte
Bleche r enthalten, über welche beständig Wasser in
Regenform hinabtröpfelt, während das vom Gaskühler durch 5 kommende Gas dem Regen entgegen geleitet wird, wobei ein Uebergang des
Ammoniaks aus dem Gase in das Wasser eintritt und zugleich Theer mit
niedergeschlagen wird. Ammoniakwasser und Theer finden ihren Abfluſs bei t.
In den Gaskühlern verliert das Gas 75 Proc. seines Ammoniaks als Ammoniakwasser und
einen groſsen Theil seines Theeres, welche beiden Producte nach den Cisternen Y (Fig. 6) abgeleitet werden.
In Fig. 5 sind
sechs Gaskühler und sechs Gaswäscher vorhanden, welche alle unter einander verbunden
sind und einer von dem anderen das Kühl- und Waschwasser stetig aus dem höher
gelegenen Behälter X (Fig. 4) entnehmen.
In den Gaswäschern verliert das Gas die restlichen 25 Proc. Ammoniakwasser, sowie
auch eine bedeutende Menge Theer, was dadurch erzielt wird, daſs das unten
abtropfende Ammoniakwasser in den ersten und zweiten Gaswäscher so oft wieder
hinaufgepumpt wird und abermals herabtröpfelt, bis dasselbe eine hinreichende
Anreicherung erfahren hat. Im dritten Gaswäscher jedoch kommt nur immer reines
Wasser dem Gase entgegen, so daſs das von hier durch das betreffende Rohr n1 des dritten
Gaswäschers entweichende Gas nur Spuren von 0,008 Proc. Ammoniak nachweisbar
enthält.
Gaskühler und Gaswäscher verbrauchen für den Ofen täglich 5cbm Wasser. Man rechnet nach der Erfahrung für die
Gaskühler eine Fläche von 2qm,5 und für die
Gaswäscher eine Waschfläche von 2qm,6 auf je
100cbm täglich durchströmendes Gas.
Die Anreicherung bezieh. Zurückleitung des Ammoniakwassers erfolgt so lange, bis
dasselbe auf 3 bis 3,5° B. gebracht wird, wobei daſs Wasser 1,777 Proc. reines
Ammoniak aufgelöst erhält.
Von diesem so angereicherten Wasser erhält man je nach der Menge des gewinnbaren
Ammoniaks 10 bis 17 Proc. auf je 100k trockener
Kohle.
Bei 14 Proc. Ausbringen an Ammoniakwasser verhält sich:
1,777 Ammoniak : x = 100 : 14,
woraus sich x auf 0,24878 Proc.
Ammoniak für 100k trockener Kokskohle
berechnet.
Der in den Cisternen Y gesammelte Theer trennt sich vom
Ammoniak nach dem specifischen Gewichte von selbst. Die geschiedenen Producte werden
mittels Pumpen in eigene Gefäſse gebracht, worauf der Theer sogleich in Fässer
gefüllt wird, während das Ammoniakwasser entweder als solches ebenfalls in Fässer
gefüllt und dem Verschleiſse übergeben oder in einen Raum ins Ammoniakhaus gepumpt
wird, wo dessen weitere Verarbeitung zu schwefelsaurem Ammoniak erfolgt.
Diese Verarbeitung geht auf die Art vor sich, daſs zunächst die dem rohen
Ammoniakwasser beigemischten Säuren durch Kalk gebunden werden. Das reine Ammoniak
wird dann durch verdünnte Schwefelsäure als schwefelsaures Ammoniak ausgeschieden.
Zur Sättigung von 100k Ammoniak sind 235k wasserfreie Schwefelsäure erforderlich. Liefert
eine Kohle 0,244 Proc. Ammoniak, so ergibt dies 0,94 Gew.-Th. schwefelsaures
Ammoniak auf 100k lufttrockener Kohle.
Vom Gasometer geht, nach Abzug von 10 Proc. Gesammtverlust, der gröſsere Theil der
Gase, etwa. 64 Proc., wie bereits erwähnt, zum Koksofenbetriebe durch die
Röhrenleitung Z zurück, während ein kleinerer Theil,
etwa 26 Proc., für beliebige Zwecke, wie Beleuchtung, Heizung u.s.w. verfügbar
bleibt.
Die zum Koksofen betriebe zurückgeleiteten Gase kommen in die Sohlkanäle der Koksöfen
mit heiſser atmosphärischer Luft in Berührung, welch letztere nun mittels eines
eigenen Ventilators Z in die glühenden Generatoren R1 und R2 eingeblasen wird,
dort deren hohe Temperatur annimmt und weiter von da erhitzt in die Sohlkanäle
eintritt.
Die in letzteren möglichst vollkommen zur Verbrennung gelangenden Gase heizen die
Koksofen wände, besorgen dann abwechselnd die Aushitzung der Generatoren und
entweichen endlich aus der Koksofenesse E.
Auch die alten Rundöfen (Bienenkorböfen) werden nach dem Patente Nr. 37280 (1888 270 7), welches sich auf Verbindung von einthürigen
(Bienenkorb- oder muffeiförmigen) Koksöfen mit Lufterhitzern bezieht, für die
Gewinnung von Theer und Ammoniak eingerichtet. Simmersbach gibt in der Zeitschrift für Berg-,
Hütten- und Salinenwesen, 1887 S. 307, an, daſs man damit ein das frühere
um 12 bis 15 Proc. übersteigendes Ausbringen an vorzüglichem Koks bei reichlicher
Theer- und Ammoniakausbeute erzielt. Es sind daher bereits zahlreiche Rundöfen in
der angegebenen Weise umgebaut worden.
Was nun die wirthschaftliche Seite der Koksgewinnung anbetrifft, so ist es Thatsache,
daſs der Werth der Kohle sich im Koks beträchtlich erhöht. Handelt es sich um
Gewinnung der Nebenproducte, wobei natürlich die Beschaffenheit der zu verkokenden
Kohle in erster Linie in Betracht zu ziehen ist, so sind die Anlagen allerdings ganz
bedeutend kostspieliger. Im Interesse unserer Handelsbilanz kann aber nur gewünscht
werden, daſs immer mehr Werke sich zur Gewinnung der Nebenproducte entschlieſsen.
Nach den Veröffentlichungen des Kaiserl. statistischen Amtes wurden nämlich im J.
1888 noch 356886 Doppelcentner schwefelsaures Ammoniak gegenüber 339259
Doppelcentnern im J. 1887 aus anderen Ländern eingeführt. An dieser Einfuhr
betheiligen sich vorzugsweise die folgenden Länder: Groſsbritannien mit 246004, die
Niederlande mit 26951, Frankreich mit 15939 und Oesterreich-Ungarn mit 10785
Doppelcentnern.
Die Einfuhr von Theer aller Art betrug im Vorjahre allein 316474 Doppelcentner; wobei
zu berücksichtigen ist, daſs die groſsen deutschen Anilinfarbenfabriken weniger den
Theer selbst, als Benzol und dessen Homologen in groſsen Mengen vom Auslande her
einführen.
Zieht man nun in Betracht, daſs das schwefelsaure Ammoniak, sobald es sich um
Stickstoffdüngung in der Landwirthschaft handelt, mit dem Chilesalpeter in
Concurrenz tritt, bei welchem die Einfuhr im vergangenen Jahre 2664072 Doppelcentner
betrug, so dürfte der Schluſs wohl berechtigt sein, daſs wir in dem Maſse, wie wir
die Anlagen zur Gewinnung der Nebenproducte bei der Koksindustrie vermehren, unsere
Handelsbilanz verbessern werden.
W. Koort.
Tafeln
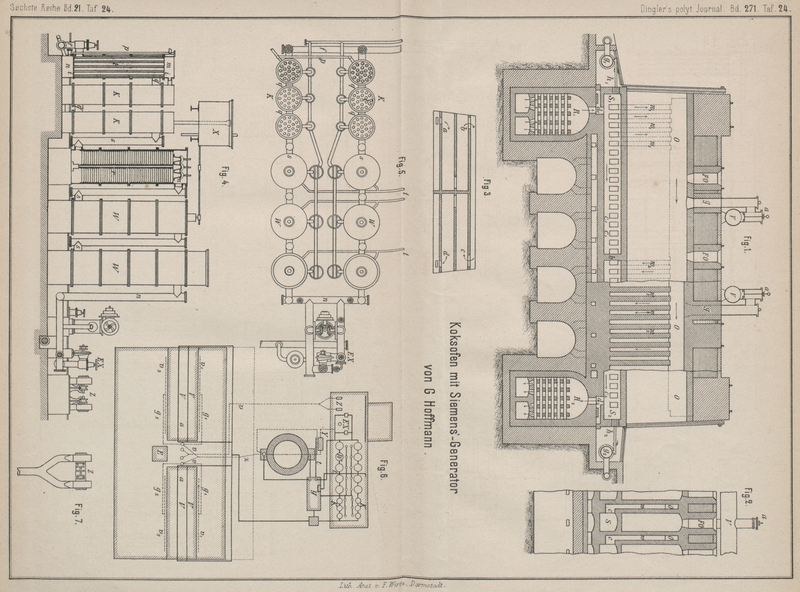