Titel: | Neuerungen im Eisenhüttenwesen. |
Autor: | W. Koort |
Fundstelle: | Band 272, Jahrgang 1889, S. 145 |
Download: | XML |
Neuerungen im Eisenhüttenwesen.
Mit Abbildungen auf Tafel
7.
Neuerungen im Eisenhüttenwesen.
Formerei und Gieſserei.
Elbridge Wheeler in Boston (Massachusets, Vereinigte
Staaten Amerikas) stellt Guſsstücke, welche ein geringeres specifisches Gewicht
haben als das Material, aus welchem dieselben gegossen werden, in der Weise her,
daſs in eine Gieſsform ein Kasten oder mehrere Kästen mit nicht metallischer Füllung
eingesetzt und dann mit schmiedbarem Metalle vollständig umgössen werden.
Wie aus Fig. 1
zu ersehen, ist auf einer Platte A eine Form A1 angebracht und in
dieser auf Füſsen a ein Kasten a1 aufgestellt. Der Mantel dieses Kastens
a1 (Fig. 2) aus Eisenblech
erhält eine geringere Höhe als die Form A1 und schlieſst Sand a
oder eine sonstige nicht metallische Masse ein. Die innerhalb der Form A1 einzunehmende Lage
des Kastens a1 richtet
sich nach der Dicke der vorgeschriebenen Wandungen. Bei solchen Gegenständen, welche
später zwischen Walzen oder einem Hammer weiter verarbeitet werden, stellt man den
Kasten zweckmäſsig in die Mitte der Form. Die Füſse a
werden aus einem dem anzufertigenden Körper entsprechenden Materiale hergestellt
oder es werden an Stelle der Füſse a Platten d angewendet, welche entweder in dem unteren Theile des
Kastens a1 (Fig. 2) oder
unterhalb des letzteren (Fig. 3 und 4) angebracht werden. Soll
der Block zwei oder mehrere Kästen erhalten, so ordnet man die Kästen nach Fig. 3 über
einander oder nach Fig. 4 neben einander an (D. R. P. Nr. 42891 vom 15. Februar 1887).
Die meisten Gieſsereien haben beim Kernmachen in Folge mangelhaften Materiales mit
vielen Schwierigkeiten zu kämpfen. Peter Gallas
empfiehlt daher das nachstehende einfache Verfahren (D. R. P. Nr. 44894 vom 20.
December 1887), Form- und Kernsand aus jedem beliebigen, überall erhältlichen
mageren Sande herzustellen.
Der Erfinder beschreibt dieses Verfahren folgendermaſsen:
„Gewöhnlicher, reiner Sand, der in seinem Naturzustande zu Form- und
Gieſsereizwecken nie zu gebrauchen ist, wird in den vorzüglichsten Form- und
Kernsand verwandelt, welcher alle nothwendigen Eigenschaften, als Porosität und
Widerstandsfähigkeit u.s.w., besitzt. Er wird hergestellt, indem man 19 Th. Sand
mit 2 Th. pulverisirtem Harze unter Hinzufügen von etwas lauem Wasser tüchtig
und innig mengt.
Auf diese einfache Weise künstlich hergestellter Kern- und Formsand, welcher in
getrocknetem Zustande dem Sandsteine an Stärke gleichkommt, wodurch in den
Kernen selbst sozusagen die Kerneisen erspart werden, besitzt eine Kräftigkeit
und Widerstandsfähigkeit, die jedem Drucke, den der Guſs auf den Kern ausübt,
widersteht. Dabei hat er eine derartige Fülle von Porosität, daſs alle beim
Gieſsen entstehenden Gase in vollkommener Weise abziehen, so daſs nie ein Brodeln und Kochen des
eingegossenen Metalles zu befürchten ist und immer reiner, blasenfreier Guſs
erzielt wird.“
Eine Form- und Gieſsvorrichtung für Rohre ist von Ludwig Pinka in Königgrätz vorgeschlagen worden (* D. R. P. Nr. 44291 vom 30.
Oktober 1887). Es wird mit ihr bezweckt, Rohre und Säulen stehend zu formen und zu
gieſsen.
Der mittels eines Schneckenvorgeleges drehbare Rahmen A
ist mit einem Deckel D versehen, welcher einerseits
durch Scharniere BB1
, andererseits durch Schrauben CC1 an dem Rahmen befestigt ist. Vor dem
Formen wird der Deckel geöffnet und nach dem Einlegen einer Form-platte E (Fig. 5 und 6) in den Rahmen wieder
geschlossen. Der Deckel bildet jetzt die vierte Seite der Formplatte. Dieser Deckel
ist für mehrere Formplatten derselbe. Die Formplatte E
hat auf der unteren Seite vier Nasen H, welche die
Platte beim Drehen des Rahmens A festhalten, indem sie
diesen zwischen sich fassen. Die Zwischenwände FF1
F2 sind mittels in
Schlitzen laufender Bolzen angeschraubt und verstellbar, um beim Gieſsen kleinerer
Rohre den mit Sand zu verstopfenden Raum zu verkleinern. Um auch die senkrechte
Ausdehnung des Stopfraumes zu verkleinern, werden die Einlagen SS1
S2 von den
Zwischenwänden abgeschraubt und ebenso die Einlagen S3
S3 entfernt. Die
Formplatte E bekommt dann bei den Nasen H, wo dieselbe auf dem Rahmen ruht, Unterlagen K (Fig. 8) von derselben Höhe
wie die abgeschraubten Einlagen der Zwischenwände. Beim Schlieſsen des Deckels D fällt dann derselbe in die Formplatte ein, bis wieder
die Oberkante der Zwischenwände an den Deckel anstöſst (Fig. 8). Auf dem einen
Ende der Formplatte ist ein Formkasten P angebracht,
welcher beim Formen von Flanschenrohren abzunehmen ist, um selbständig mit Formsand
ausgestampft und dann wieder an die Formplatte angesetzt zu werden.
Beim Formen von Muffenrohren ist derselbe fest angeschraubt. Dieser Formkasten P hat auf beiden Seiten Bolzen P1
, auf welche eine Centrirleiste J aufgesteckt wird. Diese hat so viele Löcher, als in der Formplatte Rohre
gegossen werden sollen, und dient dazu, beim Formen das Modell und beim Gieſsen den
Kern centrisch zu halten. Diese Centrirleiste ist für alle für diesen Rahmen
bestimmten Formplatten die nämliche. An den angeschraubten Formkasten P anstoſsend, ist ein Theil D1 des Deckels D um die Bolzen D2 umlegbar. Wird nämlich ein Flanschenrohr gegossen, so werden die Keile
N herausgestoſsen, der Deckeltheil D1 umgelegt, und der
Sand unter den Flanschen beseitigt, damit die Flanschen beim Schwinden des Rohres
Platz finden und nicht vom Rohre abreiſsen. Auf dem anderen Ende des Deckels ist
auch ein Theil desselben umlegbar und mittels der Keile V in der verlängerten Richtung des Deckels festgehalten. Beim Formen von
Flanschenrohren wird dieser Deckeltheil D3 um den Bolzen D4 umgelegt, um Platz zum festen Unter stampfen der Flanschen zu
gewinnen. Auf demselben Bolzen D4, um welchen sich der Deckeltheil D3 dreht, sind
Schraubenbolzen Z (leicht verschiebbar) aufgesteckt,
die dazu dienen, die Bügel R festzuhalten. Die Bügel
werden bloſs beim Gieſsen auf eine an der Formplatte angebrachte Stange R1 gesteckt und haben
den Zweck, die Kerne beim Gieſsen festzuhalten. In der Mitte der Formplatte befinden
sich auf beiden Enden Augen LL1 mit viereckigen Löchern, in welche nach dem
Abgieſsen Zapfen eingesteckt werden, mittels welchen die aus dem Rahmen A gehobene Formplatte umgedreht wird, um den trockenen
Formsand herauszuklopfen. Die vier Griffe MM1
M2
M3 dienen behufs
Umfassung beim Einlegen und Herausnehmen der Formplatte aus dem Rahmen A.
Mit dem vorstehend beschriebenen Apparate wird nun in folgender Weise gearbeitet:
Vor Allem wird der Rahmen A sammt der Formplatte E und den Wänden FF1
F2 aus der wagerechten
Lage (s. Zeichnung) in die senkrechte Lage gedreht. Das Einformen geschieht stehend
in die in den Rahmen A eingelegte Formplatte E, welche nach Vorgebrachtem mit ihren Zwischenwänden
FF1
F2 vier bis sechs
Formkästen ersetzt, somit das Gewicht einer solchen Garnitur fast der Hälfte des
Gewichtes von vier bis sechs Formkästen entspricht. Jede Formplatte kann ohne viele
Umstände an Ort und Stelle nach Belieben auf mehrere verschiedene Rohrdimensionen
umgeändert werden. Sind alle Rohre in der Formplatte eingestampft, so wird der
Rahmen wieder wagerecht gedreht, der Deckel geöffnet und die Formplatte in die
Trockenkammer befördert. In den leeren Rahmen wird wieder eine neue Formplatte
eingelegt, der Deckel geschlossen und von Neuem eingestampft, was sich bei allen
anderen Formplatten wiederholt. Die Kerne und das Stopfen der Formen sind wie bei
der bisherigen Fabrikation von stehend gegossenen Rohren. In den Formplatten können
Muffen- und Flanschenrohre, sowie Säulen abgegossen werden.
Nachdem alle Formplatten voll eingestampft, in die Trockenkammer befördert wurden,
werden sie und die Kerne mit einem Heizen der Kammer gleichzeitig und gleichmäſsig
getrocknet.
Sobald die Trocknung vorüber ist, wird eine Formplatte mit ihrem Inhalte in den
Rahmen eingelegt und der Deckel D geschlossen. Der
Apparat wird dann mit den Aufguſsenden nach unten gedreht, die Kerne werden
eingesetzt und mit den Bügeln R verschraubt. Darauf
wird der Apparat mit den Muffen nach unten gedreht, und ist damit die Form zum Gusse
fertig. Alle Rohre werden mit der Muffe nach unten gegossen und ist der Kern dabei
aus einem Stücke.
Nach dem Gusse wird der Apparat mit den Muffen nach oben gedreht, die Kernspindeln
herausgezogen und dann der Apparat wieder in die wagerechte Lage gebracht. Nachdem
der Deckel geöffnet und die Formplatte mit den abgegossenen Rohren bei Seite gelegt ist, wird eine frische
Formplatte aus der Trockenkammer in den Rahmen gelegt. Die bereits abgegossenen
Rohre bleiben so lange in der Form, bis alle den Tag vorher eingeformten Formplatten
abgegossen sind, und können dieselben daher ruhig abkühlen.
Die abgegossenen Rohre sind, so wie bei genau vorgerichteten Formkästen, gleich in
der Eisenstärke, von innen wie von auſsen sehr ansehnlich, ohne jede Naht. Der
Guſsputzer hat somit nur den Kern auszustoſsen, den etwa anhaftenden Sand
abzuklopfen, ohne Eisenputzen, Nähte u.s.w. entfernen zu müssen.
Bekanntlich haben Schäumapparate den Zweck, beim Gieſsen die Unreinigkeiten, des
Metalles abzusondern und auszuscheiden, damit schlackenfreier Guſs entsteht. Der in
Fig. 9 und
10
dargestellte Schäumapparat von P. Gallas in Frankfurt a. M. (D. R. P. Nr. 46022 vom 29. April 1888) besteht aus einem Einguſstrichter A im Oberkasten, Einlauftrichter B im Unterkasten, dem Metallsammelraume C, dem Schlackensammelraume D, dem Kerne E, welcher die Einlaſsrinne F vom Metallsammelraume C
trennt, und der Einlaſsrinne F, welche das flüssige
Metall nach der Form G führt. Als Neuerung bringt der
Erfinder einen Seiher H in dem Metallsammelraume an,
welcher das Metall abschäumt und die leichten Theile in dem Schlackensammelraume D zurückläſst.
In der Patentschrift Nr. 44119 (gültig vom 20. December 1887) beschreibt P. Gallas die Anwendung von nachstellbaren
Führungsohren in Verbindung mit Führungsstiften für Formkasten. Die Ohren an dem
Oberkasten haben an der inneren Seite genau die Form wie die äuſsere Seite der
Führungsstifte, so daſs Führungsstifte und Ohr an ihren Flächen genau auf einander
passen. Um Ober- und Unterkasten mit ihren beiderseitigen Führungen durch die
angebrachten Führungsstifte und Ohren genau regeln zu können, und um dieselben, wenn
abgenutzt, auch nachstellen zu können, ist an der einen inneren Seite der Ohren eine
Vertiefung angebracht, in welcher ein Stückchen Gummi oder eine Feder zur Erhaltung
der Spannung liegt, welche, wenn das Ohr am Formkasten-Obertheile angeschraubt ist,
zwischen dem Kasten und dem Ohre liegt. Gegenüber der Vertiefung ist ein Loch für
eine Schraube angebracht, durch deren Nachlassen oder Anziehen das Ohrentheil
geregelt wird.
W. Potthof, welcher bereits früher einen nachgiebigen
Untersatz für Formkästen vorgeschlagen hat, ersetzt (vgl. D. R. P. Nr. 43718 vom 1.
Oktober 1887) die bekannten elastischen Unterlagen oder Federn durch Gegengewichte
i (Fig. 11), die mittels
Hebel h oder durch über Rollen r (Fig.
12) geführte Ketten auf Hebung des Untersatzes wirken.
Zur Vermeidung der Trennungsarbeit nach dem Herausnehmen des Gusses aus der Form wird
an der Stelle, wo die Trennung stattfinden soll, also längs der Kante d
(Fig. 13)
in die Form b eine Nuth e
eingearbeitet. In diese Nuth wird ein die Wärme schlecht leitendes, aber auch höhere
Temperaturen aushaltendes Material (Asbest) eingelegt.
Während nunmehr beim Eingieſsen des flüssigen Metalles letzteres an den metallischen
Wänden der Form, also einem die Wärme gut leitenden Materiale, erstarrt und die
Kruste c bildet, findet dies an der Stelle, wo der
Asbest liegt, nicht statt, das eingegossene Metall bleibt also an dieser Stelle
flüssig, wenigstens viel flüssiger als an allen anderen Stellen der Form. Stürzt man
nun die Form um, so läuft zusammen mit dem die Form ausfüllenden Metalle auch jener
Streifen i heraus, welcher der mit Asbest gefüllten
Nuth e gegenüberliegt; beim Auseinandernehmen der Form
wird daher der Trichter B von dem eigentlichen
Guſsstücke A schon getrennt sein oder höchstens durch
ein leicht trennbares Häutchen mit letzterem noch zusammenhängen. Es gelingt also
auf diese Weise, ohne irgend welche besondere mechanische Nacharbeit, die bisher
umständliche Trennung von A und B zu bewirken (vgl. D. R. P. Nr. 46167 vom 1. Mai 1888, Schimansky in Berlin). Das Verfahren bezweckt,
Sturzguſs herstellen zu können, bei welchem Durchbrechungen vorhanden sind.
Horst Edler v. Querfurth in Schönheide (Sachsen) hat
einen Tiegelschmelzofen für schmiedbaren Guſs vorgeschlagen (vgl. D. R. P. Nr. 45281
vom 15. April 1888). Derselbe ist für continuirlichen Betrieb eingerichtet und
besteht aus einem runden, eisernen, innen ausgemauerten Gehäuse, um welches herum in
doppelten, über einander befindlichen Ringen die Gebläsekammern H1 und H2 angebracht sind
(Fig.
14), zu denen die Gebläserohre G1 und G2 getrennt führen. Im Ofen befindet sich ein
Schmelzcylinder D über Cylinder E auf der Ummauerung q. In dem oberen Theile
D des mit Abfluſsöffnung r versehenen Tiegels E findet die Beschickung
Platz, während der untere Theil E zur Aufnahme des gar
geschmolzenen Eisens dient.
Der Tiegel ist von einem Schmelzraume umschlossen, in welchem eine gleichmäſsige
ringförmige Schmelzzone durch tangential aus den Gebläsekammern H1 und H2 eintretende
schlitzförmige Gebläseluftkanäle F (Fig. 15) bedingt
wird.
Fig. 16 zeigt
eine Klopfvorrichtung für Formmaschinen (D. R. P. Nr. 43269 vom 12. Oktober 1887,
Hillerscheidt in Berlin). Dieselbe besteht in einem
drehbaren T-förmigen Hebel, dessen einer Arm mit dem Klopfer f, welcher gegen die am Formtische befestigten Knaggen i schlägt, versehen ist. Der zweite Arm trägt ein
Gewicht h zur Erhaltung der Mittelstellung, und der
dritte Arm ist mit einem Handgriffe g versehen.
Nach dem Pressen der Form faſst der Arbeiter mit der rechten Hand den Griff g, bewegt denselben kräftig auf und ab, wodurch f an die Knaggen i schlägt und den
Kasten bezieh. den Sand von der Formplatte durch diese Erschütterung lockert. Zu
gleicher Zeit bewegt der Arbeiter mit der linken Hand den Hebel d und kann während des Klopfens den Kasten bequem
abheben.
Fried. Bongardt in Duisburg benutzt zur Herstellung
harter Zahnflächen an verzahnten Kettenrollen, sowie zur Erzeugung harter
Innenflächen bei glatten Rollen eine Scharnierschale, welche aus scharnierartig
zusammengesetzten Ringtheilen besteht (D. R. P. Nr. 42970 vom 6. September
1887).
W.
Koort.
Tafeln
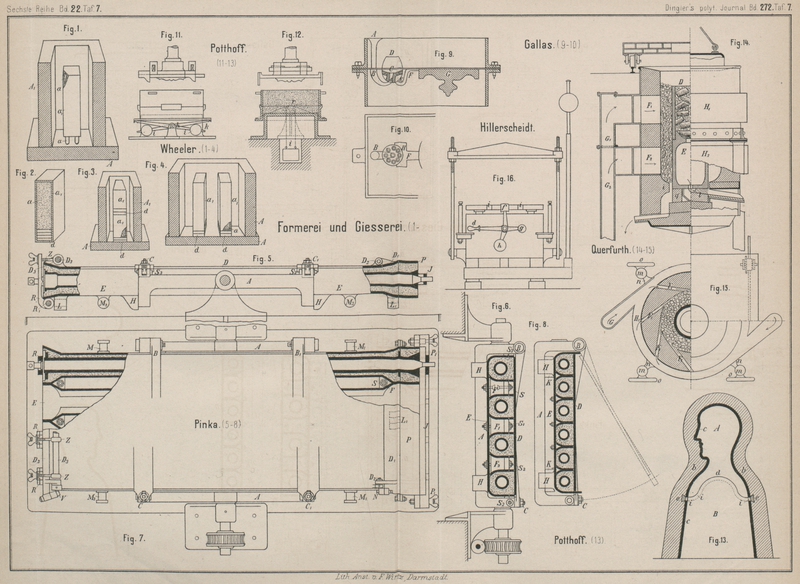