Titel: | Neuerungen im Metallhüttenwesen. |
Fundstelle: | Band 272, Jahrgang 1889, S. 392 |
Download: | XML |
Neuerungen im Metallhüttenwesen.
Mit Abbildungen auf Tafel
20.
Neuerungen im Metallhüttenwesen.
Aluminium, Magnesium, Alkalimetalle, Eisen-, Mangan-, Chrom-
und Aluminiumlegirungen.
Die technische Darstellung von Aluminium und Magnesium ist, abgesehen von den
pyrochemischen Darstellungsmethoden, bisher nur durch Elektrolyse der feuerflüssigen
Salze gelungen. Wenigstens ist es bisher nicht bekannt geworden, daſs durch die
Elektrolyse der wässerigen Lösungen (vgl. D. p. J.,
1888 268 125) irgendwie nennenswerthe Erfolge erzielt
worden seien. G. Nahnsen und J. Pfleger in Hannover
haben nun (vgl. D. R. P. Nr. 46753 vom 2. August 1888) gefunden, daſs die bei der
Elektrolyse wässeriger Lösungen theils durch Reactionswärme, theils durch künstliche
Wärmezufuhr zwecks erhöhter Leitungsfahigkeit des Elektrolyten erzielte höhere
Temperatur stets die Bildung von Oxydhydrat veranlasse, zumal das Aluminium, welches
bei 70 bis 80° schon das Wasser zersetze, bei der elektrolytischen Zerlegung in
statu nascenti auftrete und eben deshalb leichter auf das Wasser einwirken
könne.
Die elektrolytische Abscheidung von Aluminium u.s.w. soll aber in cohärenter Form und
ohne Nebenzersetzung vor sich gehen, wenn man im Gegensatze zu den bisher üblichen
Verfahren den Elektrolyten durch geeignete Abkühlmittel abkühlt, wie z.B. durch
Einleiten von stark abgekühlter Luft in die zu elektrolysirende Lösung oder durch
Circulirenlassen von Chlorcalciumlauge in Kühlschlangen. Die Erfinder geben an, daſs
bei + 4° C. sämmtliches Metall aus dem Elektrolyten gewonnen werden kann.
Es ist zu beachten, daſs die Lösungen der betreffenden Salze stark und gleichmäſsig
concentrirt sein müssen. Zu diesem Zwecke wird zu positiven Elektroden entweder
Retortenkohle verwendet, welche mit den Oxydhydraten der betreffenden Metalle
getränkt ist, oder man läſst den Elektrolyten durch eine Reihe von Kästen flieſsen
und schaltet dabei zwischen den Elektrolysirgefäſsen Kästen ein, in welchen die Metalloxydhydrate
zugeführt und durch ein Rührwerk aufgerührt werden.
A. Feldmann in Linden schmilzt zum Zwecke der Gewinnung
von Aluminium und dessen Legirungen die Fluorverbindungen des Aluminiums mit den
Chloriden der Metalle der alkalischen Erden und unterwirft die geschmolzene Masse
der Einwirkung des elektrischen Stromes oder der chemischen Wirkung eines
Alkalimetalles (Engl. Pat. Nr. 12575 v. J. 1887).
August Winkler in Görlitz benutzt nach dem D. R. P. Nr.
45824 vom 15. Mai 1888 geschmolzene phosphorsaure oder borsaure Thonerde oder eine
Mischung beider Verbindungen als Elektrolyt.
L. Grabau in Hannover benutzt gekühlte Gefäſse, um aus
der Schmelzmasse selbst eine Kruste an den Wänden des Reductionsgefäſses zu bilden
(Engl. Pat. Nr. 15593 v. J. 1887). Wir werden auf das D. R. P. näher
zurückkommen.
Derselbe Erfinder schlägt ein Verfahren zur continuirlichen Schmelzung oder auch zur
Reduction mittels des elektrischen Lichtbogens vor (D. R. P. Nr. 44511 vom 23.
November 1886), welches dadurch gekennzeichnet ist, daſs die Schmelzung nicht direkt
durch den Lichtbogen selbst erfolgen soll, sondern innerhalb eines flüssigen Poles
unter der Oberfläche und durch die Hitze desselben. Das zu schmelzende Material d wird nicht von oben in den Schmelzofen gebracht,
sondern als Pulver entweder mittels einer Preſsvorrichtung d1 (Fig. 1) durch den Boden
des Tiegels a oder in Stabform (Fig. 2) von der Seite her
unter den flüssigen Pol c gebracht. Das Schmelzgut
flieſst durch das Rohr e ab. Die mitabflieſsende
Polmasse wird beständig durch den zugleich als positiven Leitungsdraht dienenden
Metallstab f von oben oder von der Seite her ergänzt.
Mittels einer Zufuhrvorrichtung g wird letzterer in
erforderlichem Maſse in die flüssige Polmasse c des
Tiegels a vorgeschoben. Der sich beständig ergänzende
Metallpol ist jedoch nur dann erforderlich, wenn es sich um Schmelzung von
Materialien handelt, welche auch im flüssigen Zustande den elektrischen Strom nicht
leiten. Besonders geeignet hält der Erfinder das Verfahren zur Gewinnung von
Aluminiumbronze aus einer Mischung von Thonerde, Kohle und Kupfer.
Um Legirungen von Aluminium mit anderen Metallen herzustellen, mischt Andrew Mann in London nach dem D. R. P. Nr. 45775 vom
20. December 1887 Aluminiumsulfat mit einem Metallchlorid (Chlornatrium,
Chlorkalium, Chlorammonium) und erhitzt die Masse in einer Retorte, wobei sich die
folgende Umsetzung vollziehen soll:
Al2(SO4)3 + 6NaCl = Al2Cl6 + 3NaSO4 . . . . . . . . . . (I)
Die Masse wird alsdann mit Calciumoxyd versetzt und für einige Wochen liegen
gelassen, während welcher Zeit sich durch die Einwirkung des Chloraluminiums in der
Masse Chlorcalcium bildet:
3CaO + Al2Cl6 = 3CaCl2 + Al2O3 . . . . . . . .
. . (II)
Eine zweite Menge von schwefelsaurer Thonerde wird mit einem geeigneten
Reductionsmittel, vortheilhaft mit fein vertheilter Knochenkohle u.s.w., gemischt
und alsdann der aus der ersten Operation gewonnenen Masse zu gleichen Theilen
zugesetzt. Das Ganze enthält jetzt die Bestandtheile der Masse der ersten Operation,
sowie Aluminiumsulfit, welches sich aus dem Gemische des Sulfats mit dem
Reductionsmittel gebildet hat, nach folgender Gleichung:
Al2(SO4)3 + 12C = Al2S3 + 12CO . . . . . . . . . . (III)
Diese Reaction tritt unter dem Einflüsse der Hitze während der darauf folgenden
Operation ein.
Die Masse wird im Verhältnisse von 1 zu 2 mit dem geschmolzenen oder in kleine Stücke
oder in Pulverform gebrachten Metalle, dessen Legirung mit Aluminium erzielt werden
soll, in einem geeigneten Ofen auf Schmelzhitze erhitzt, worauf sich die Legirung
bildet.
Die chemische Reaction zwischen dem zu legirenden Metalle und den nach Gleichungen I,
II und III erzielten Verbindungen findet, wenn Kupfer legirt werden soll, nach
folgender Gleichung statt:
Al2Cl6 + Al2S3
+ 3CaCl2 + 6Cu = 6CuCl2 + 3CaS + 4Al
(in Legirung mit überschüssigem Kupfer).
Da Aluminiumlegirungen mit Kupfer allein hart und spröde werden, so setzt man, um
dieses zu vermeiden, dem Kupfer vor dem Schmelzen etwas Zink oder Messing zu.
F. Hornung in Berlin und F. W.
Kasemeyer in Bremen haben eine Vorrichtung zur elektrolytischen Gewinnung
von Alkalimetallen und Magnesium aus ihren Chloriden vorgeschlagen (D. R. P. Nr.
46334 vom 29. Januar 1888).
A ist die mit äuſserem Eisenmantel versehene Anode (Fig. 3), welche
gleichzeitig auch den Schmelztiegel bildet. In dieselbe ist am Rande ein Ringdeckel
P aus Porzellan dicht eingesetzt mit einem Kanäle
P1, an welchem sich
eine Ableitung C anschlieſst. In diesen Ringdeckel wird
eine Porzellanhülse S eingehängt, welche so lang ist,
daſs sie immer genügend tief in die Schmelze eintaucht. Durch diese Hülse wird
sodann die aus Eisen oder anderem passenden Metalle hergestellte hohle Kathode K in die Anode eingesenkt. Um das obere Ende der
Kathode ist eine Kammer K1 gebildet, welche sich mit ihrer Unterste auf den Ringdeckel P und die Hülse S dicht
aufsetzt. Diese Kammer ist auf der Oberseite geschlossen, auf der Unterseite dagegen
mit zahlreichen Perforationen k versehen (Fig. 4), durch
welche sie mit dem Raume zwischen Hülse S und Kathode
K frei communicirt. Ferner zweigt sich seitlich von
der Kammer ein Ableitungsstutzen M ab.
Durch die an beiden Enden offene Kathode wird es ermöglicht, die Schmelze in der
Anode auf einem solchen Niveau zu halten, daſs jede Communication zwischen den
beiden von der Hülse S gebildeten Räumen aufgehoben
bleibt.
Das während der Zersetzung der Schmelze an der Anode sich ausscheidende Chlorgas und
die an der Kathode sich ausscheidenden Metalldämpfe werden durch die Hülse von
einander getrennt gehalten und zwingt diese ersteres, den Weg nach der Ableitung C und letztere den Weg nach der Ableitung M zu nehmen.
Der Patentanspruch lautet: „Die elektrolytische Gewinnung von Alkalimetallen und
Magnesium mittels einer Zersetzungszelle, welche aus einem die Anode bildenden
Kohlentiegel und einer hohl gestalteten Kathode zusammengesetzt ist, durch
welche letztere die Nachfüllung geschieht, um die Schmelze beständig auf
derselben Höhe zu erhalten.“
Offenbar erstreckt sich nach dieser Fassung der Schutz auf eine Combination, welche
einem bestimmten Verfahren angepaſst ist, da die Zuführung der Beschickung durch
eine hohle Elektrode schon von Cowles (D. p. J., 1887 265 550)
vorgeschlagen wurde.
Das Verfahren der Aluminiumdarstellung von Curt Netto,
welches bereits in D. p. J., 1888 269 398, angedeutet wurde, ist unter Nr. 45198 vom 26. März 1887 ab im
Deutschen Reiche patentirt worden.
Nach diesem Verfahren ist es erforderlich, daſs die Körper, welche auf einander
einwirken sollen, zunächst getrennt von einander für die nachherige Umsetzung
vorbereitet werden, daſs diese Umsetzung möglichst augenblicklich bewirkt und der
Prozeſs nach beendeter Umsetzung plötzlich unterbrochen wird.
Das Verfahren wird daher wie folgt ausgeführt: 100 Gew.-Th. Kryolith und 30 bis 100
Gew.-Th. abgeknistertes Kochsalz werden in einem feuerfesten Thontiegel bei Rothglut
unter aufgesetztem Deckel zur Vermeidung von Verflüchtigung geschmolzen. Sobald die
Masse vollständig flüssig ist, werden 35 Gew.-Th. Natrium in einem oder auch
mehreren Stücken mittels eines später zu beschreibenden Gezähes auf den Boden des
Bades eingeführt. Die Umsetzung tritt sofort ein und ist schon nach wenigen
Augenblicken oder Minuten beendet, worauf man den Tiegel aus dem Feuer nimmt und
seinen Inhalt in eine tiegelartige guſseiserne Form gieſst, um eine rasche
Erstarrung der Masse zu erzielen. Nach dem Festwerden derselben wird die Form
umgestürzt und das Aluminium, welches in einem einzigen Klumpen nahe am Boden der
Form vereinigt ist, durch einige Hammerschläge von der Schlacke getrennt.
Damit der Prozeſs völlig gelingt, ist vor Allem erforderlich, daſs die Schmelze vor
dem Einbringen des Natriums gut flüssig ist. Das Schmelzen darf einerseits nicht zu
lange dauern, um die Auflösung von Silicium aus den Gefäſswänden zu beschränken,
andererseits aber auch der leicht eintretenden Verflüchtigung und hieraus sich
ergebenden Zähflüssigkeit des Bades wegen bei nicht zu hoher Temperatur geschehen.
Zur Vermeidung von Explosionen beim Einführen des Natriums in die flüssige Schmelze
darf das Natrium keine Hohlräume, keine Feuchtigkeit, kein Oel, keinen Asphalt oder
sonstige Kohlenwasserstoffverbindungen enthalten. Es ist daher vorzuziehen, das
Natrium unmittelbar vor seiner Benutzung in einem verschlossenen eisernen Tiegel
umzuschmelzen, in geeignete Formen zu gieſsen und nach dem Erstarren gegen
Feuchtigkeit zu schützen. Bei diesem Umschmelzen sind weitere Vorsichtsmaſsregeln
nicht erforderlich, nur ist eine möglichst niedere Temperatur anzuwenden und alles
Wasser natürlich fernzuhalten. Das Einführen des Natriums in das Bad muſs derart
erfolgen, daſs das Metall nicht an der Oberfläche des Bades zum Schmelzen kommt, da
es ebenso wenig möglich wäre, das flüssige, specifisch leichtere Natrium
unterzutauchen, wie z.B. Oel unter Wasser zu bringen. Das Natrium Würde in diesem
Falle also zum gröſsten Theil unbenutzt verbrennen.
Um daher das Natrium in fester Form schnell in die flüssige Schmelze, und zwar bis
auf den Boden des Bades einzuführen, bedient man sich zweckmäſsig eines Gezähes
(Fig. 5
bis 9),
welches aus einem Anfachen Eisenstab s besteht.
Um Abkühlung möglichst zu vermeiden, spieſst man das Stück Natrium g an diesen Stab s,
erwärmt die Scheibe a bis zur Rothglut, bringt den Stab
s und Scheibe a mit
Stange t bereits auſserhalb des Tiegels T in die aus Fig. 8 und 9 ersichtliche
gegenseitige Lage und taucht dann das Ganze plötzlich bis auf den Boden des Tiegels
T ein, ehe noch das Natrium Zeit findet, an der
Oberfläche des Bades zu schmelzen und in Brand zu gerathen. Die Scheibe a verhindert hierbei, daſs das specifisch leichte
Natrium nach dem Eintauchen in die Hohe steigt, während die in der Scheibe
angeordneten Löcher i ein vertheiltes Aufsteigen des
geschmolzenen Natriums in dem Bade gestatten.
Der sofortige Eintritt der von einer Flammenerscheinung begleiteten Umsetzung wird an
dem lebhaften Aufwallen der ganzen Masse, sowie an dem Erzittern der beiden
Eisenstäbe s und t
wahrgenommen. Sobald diese Erscheinungen aufhören, was nach wenigen Augenblicken
oder Minuten schon der Fall ist, kann man die Umsetzung als beendet erachten und den
Tiegel seines Inhaltes entleeren.
In Folge der äuſserst kurzen Dauer der Umsetzung hat die Einführung des eisernen
Gezähes in das Bad keine nachtheilige Einwirkung auf die Reinheit des
Aluminiums.
Je höher die Flüssigkeitsschicht des geschmolzenen Kryoliths ist, desto vollständiger
wird ein Entweichen von Natriumdämpfen verhindert. Diese Höhe sollte daher nicht
unter 30cm betragen.
Man kann jedoch auch andere Vorrichtungen verwenden, um das Natrium in das flüssige
Bad einzutragen.
Das Gezähe, welches sich zweckmäſsig als Taucher bezeichnen läſst, kann z.B. die
Gestalt einer Glocke haben oder in einem hohlen Gefäſse von irgend einer Form, als
Kugel, Cylinder, Ellipsoid, mit durchlochten Wandungen bestehen. Fig. 10 zeigt einen
solchen Taucher. Das aus
dünnem Schmiedeeisen hergestellte hohle Gefäſs a
enthält eine Anzahl Oeffnungen i und ist an der
eisernen Stange t befestigt. Dieses Gefäſs setzt man in
die zweitheilige Form h, welche dasselbe dicht
umschlieſst, gieſst darauf flüssiges Natrium durch den mit der Oeffnung f correspondirenden Einguſstrichter e ein, bis a gefüllt ist,
läſst das Natrium erstarren und entfernt dann die Form h von dem Gefäſse a. Der so hergestellte
Taucher ist nun zum Gebrauche fertig.
Fig. 11 zeigt
einen Tiegel F, der als Schmelz- und Reductionsgefäſs
dient. Nachdem dessen Inhalt geschmolzen ist, nimmt man ihn aus dem Ofen und deckt
ihn mit einem gutschlieſsenden Deckel D zu, welcher
mittels an seiner unteren Seite angeordneter Dorne oder Vorsprünge l eine Natriumscheibe g
trägt. Durch eine entsprechend geformte Zange k, welche
mit einer ringförmigen Klaue den unteren Theil des Tiegels mit der anderen,
gleichfalls ringförmigen Klaue den cylindrischen Knopf u des Deckels D umfaſst, drückt man den
Deckel fest auf und stürzt den Tiegel beliebig oft, wobei noch vorhandenes Natrium
in Folge seines geringeren specifischen Gewichtes immer wieder durch die
geschmolzene Masse nach oben steigt, bis sämmtliches Natrium gebunden bezieh.
aufgebraucht ist.
Handelt es sich um Darstellung von eisenhaltigem, aber siliciumarmen Aluminium für
die Erzeugung des Mitismetalles, so kann der in Fig. 12 dargestellte
Converter benutzt werden.
Das eiserne, auf der Welle xx angeordnete cylindrische
Gefäſs T wird mit der zu zersetzenden
Aluminiumverbindung und dem Fluſsmittel durch die Einfüllvorrichtung o beschickt. Das Ende n
des Heizrohres r mit dem Gasgenerator durch die Leitung
q in Verbindung gesetzt und durch p Luft zugeleitet. Sobald die das Rohr r durchstreichende Flamme die Charge zum Schmelzen
gebracht hat, wird durch die Einfüllvorrichtung o
festes oder flüssiges metallisches Natrium eingetragen, die Einfüllvorrichtung o verschlossen, die Verbindung von n mit q gelöst und und der
Converter T mittels der Riemenscheibe w in Rotation versetzt. Nach der kurz darauf
vollendeten Umsetzung bringt man den Converter in die senkrechte Lage, öffnet m und läſst Schlacke und Aluminium in einen
transportablen Stechtiegel laufen. Natürlich kann man auch einen ausgefütterten
Converter anwenden, welcher dann also ein eisenarmes Product liefert.
Nach der englischen Patentschrift Nr. 17532 vom 20. December 1887 will Netto das flüssige Natrium in das feuerflüssige
Kryolithbad hineinpumpen.
Zu diesem Zwecke werden der Natriumbehälter H (Fig. 13), die
durch einen Wasserdruckkolben J betriebene Kolbenpumpe
G und ein kleiner Regulator K innerhalb einer auf etwa 100° erhitzten Kammer L angeordnet, so daſs das hier geschmolzene Natrium durch die Leitung C nach dem Raume E und von
da durch den durchlöcherten Boden F in den Kippbehälter A gepumpt werden kann. Das Rohr C kann auch von oben in das Bad eingeführt werden (Fig. 14) und ist dann am
unteren Ende mit einer Brause E, deren Durchbohrungen
F nach oben gerichtet sind, versehen, um das
Natrium in möglichst feiner Vertheilung in das Kryolithbad einzuführen.
Der Hauptvortheil der eigenthümlichen Art und Weise, wie Netto die an sich bekannte Reaction zur Ausführung bringt, soll darin
begehen, daſs das Ausbringen des metallischen Aluminiums sowohl im vergleiche mit
dem Gehalt des Gemenges an Aluminium, als auch mit Bezug auf die Menge des
angewendeten Natriums ein gutes genannt werden muſs und daſs das Aluminium nicht in
Form von feinen, in der Schlacke vertheilten Kügelchen, sondern in einem
zusammenhängenden Klumpen (Regulus) erhalten wird.
Die Herstellung von Chromlegirungen ist wegen der schweren Reducirbarkeit der
Chromerze nicht leicht auszuführen. A. Eckardt in
Dortmund hat nun gefunden, daſs die Reduction von Chromerz leicht und vollständig
dadurch erreicht wird, daſs man dem Erze entsprechende Mengen Schlacken des sauren
Bessemerprozesses beimischt und dann durch reducirendes Einschmelzen im Schacht-,
Tiegel- oder Flammofen eine Legirung erhält, welche aus Chrom, Eisen und Mangan
besteht, die bei der Darstellung von Fluſseisen sich gut bewähren soll. Auch bietet
sich auf diese Weise eine Verwerthung der bisher unbenutzten Schlacken des sauren
Bessemerprozesses.
Wenn die Herstellung dieser Ferro-Chrom-Mangan-Legirungen im Hoch- oder Flammofen
vorgenommen werden soll, so kann das Verehren in folgender Weise ausgeführt
werden:
Chromerz und Schlacke werden fein gemahlen und mit so viel wasserfreiem Theer
versetzt, als zur Reduction des Erzes nothwendig erscheint. Aus der teigigen
Mischung von Theer, Erz und Schlacke preſst man Briquettes, welche dem Hochofen mit
Koks übergeben werden (vgl. D. R. P. Nr. 44896 vom 31. Januar 1888).
Nach Iron, 1889 S. 32, wird in den Werken zu Brooklyn
Chromstahl für gröbere und feinere Werkzeuge hergestellt, welcher auſser dem
Grundstoffe die folgenden Bestandtheile enthält:
Nr. 1
Nr. 1
Nr. 3
Nr. 3
Stahl
Proc.
Proc.
Proc.
Proc.
Kohlenstoff
1,1071
1,1453
0,7253
0,7417
Phosphor
0,0354
0,041
0,0186
0,0158
Chrom
0,7593
0,6827
0,5127
0,5283
Silicium
0,1292
0,1339
0,1754
0,1614
Schwefel
0,0065
0,0058
0,0052
0,0058
Mangan
0,0219
0,0221
0,0103
0,0103
Nr. 1
Nr. 2
Nr. 1
Nr. 2
Magnetstahl
Magnetstahl
Gestein-bohrerstahl
Gestein-bohrerstahl
Proc.
Proc.
Proc.
Proc.
Kohlenstoff
0,9571
0,9653
0,8508
0,848
Phosphor
0,0522
0,0438
0,0218
0,019
Chrom
0,494
0,5974
0,5455
0,4082
Wolfram
0,6186
0,7614
–
–
Silicium
0,055
0,0613
0,1246
0,1329
Schwefel
0,0043
0,005
0,0057
0,005
Mangan
0,0167
0,0167
0,0112
0,0094
Von W. Ch. Roberts-Austen wurden nach Chem. News, Bd. 57 S. 133, Goldlegirungen auf ihre
Zugfestigkeit geprobt. Hierbei ergab sich, daſs die zugesetzten Stoffe die
Festigkeit des Goldes in der Reihenfolge ihres Atomvolumens beeinflussen. Je gröſser
das Atomvolumen, desto mehr vermindert sich die Festigkeit.
Im Techniker, 1889 S. 38, findet sich ein Bericht über
Aluminiumbronze und sonstige Aluminiumlegirungen, welcher jedoch gegenüber den in
D. p. J., 1888 270 212
u. ff., nichts wesentlich Neues bietet. Erwähnt sei nur, daſs der unter dem Namen
Bombay-Stahl in England hergestellte Werkzeugstahl früher durch einen Zusatz von
Thonerde hergestellt wurde, während jetzt Aluminiumeisen zu diesem Zwecke verwendet
wird.
Ueber Hadfield's neues Eisenmanganmetall berichtet Rich. Akerman in Jern.-Cont.
Annaler, 1888 S. 351, daſs ein Mangangehalt von 3 bis 7 Proc. ein hartes
und sprödes Product liefert, auf welches die Härtung nicht einwirkt. Die gröſste
Härte scheint bei 5 bis 6 Proc. Mangan vorzukommen, während die Sprödigkeit bei
Gehalten von 4 bis 5 Proc. um so gröſser erscheint, je kleiner der Kohlenstoffgehalt
ist. Am vortheilhaftesten sollen Gehalte von 12 bis 14 Proc. Mangan sein. Mit ihnen
erreichte man eine Belastung von über 100k für
1qmm neben einer Verlängerung von 44 bis 50
Proc. bei 203mm Stablänge. Eine Stange mit 12,55
Mn und 0,7 Proc. C wurde nach jedesmaligem Härten siebenmal gestreckt und dadurch um
190,6 Proc. verlängert. Beim Reiſsen zeigte die Bruchfläche nur 8,93 Proc. des
ursprünglichen Querschnittes. Man betrachtet dieses Eisenmangan nicht als eine
Stahlart, sondern vergleicht sie mit einer Bronze (Berg- und
Hüttenmännische Zeitung, 1889 S. 115).
Ueber Mitisgüsse und Aluminiumeisen finden sich Mittheilungen in der Oesterreichischen Zeitschrift für Berg- und
Hüttenwesen, 1888 S. 673 und 1889 S. 81, welcher folgendes entnommen
wird.
Unter Ferro-Aluminium versteht man ein Eisen, welches 6 bis 10 Proc. Aluminium
enthält und gewöhnlich bei dem Mitisprozesse verwendet wird, welcher darin besteht,
aus einem äuſserst kohlenstonarmen, weichen Eisen unter Zuhilfenahme eines Zusatzes
von Aluminium direkt schmiedbaren Guſs zu erzeugen.
Es ist bekannt, daſs durch den Hochofenprozeſs unter entsprechenden Bedingungen
Aluminium aus seinen Verbindungen abgeschieden und ins Roheisen übergeführt wird. So
fand man im englischen Roheisen 0,5 bis 1 Proc., im schwedischen 0,75 Proc., im
Siegerländer Roheisen 0,077 Proc.
Während Karsten der Ansicht war, daſs sich Thonerde beim
Hochofen-Prozesse nicht reducire, glaubt Grüner durch
den erhöhten Kalkzuschlag die Abscheidung des Aluminiums begünstigen zu können.
Der sogen. Bombay-Wootz-Stahl soll seine guten
Eigenschaften nach Faraday und Le Blanc einem
Aluminiumgehalte verdanken, wohingegen Karsten und
Henry kein Aluminium in dem echten Wootz
finden konnten.
Faraday und Stodart wollen eine Legirung von Eisen und
Aluminium durch direkte Reduction der Thonerde erzeugt haben (vgl. Wedding, Eisenhüttenkunde, Bd. 1 S. 247).
Nach Lohage hat bei der Guſsstahlfabrikation ein Zusatz
von Thonerde und Mangan einen groſsen Einfluſs auf das Korn und den Lustre des
Stahles, indem sich neben Silicium-Mangan auch Silicium-Aluminium bilden soll,
welches sich aus dem flüssigen Stahle oberflächlich abscheidet.
Rogers, Knowles, Benzon, Deville, Tissier, Michel,
Calvert und andere Experimentatoren und Fabrikanten stellten bereits früher
mehr oder Weniger Aluminiumeisen dar oder befürworteten dessen Herstellung.
Aus neuerer Zeit stammt die Ausführung des Oestberg'schen Verfahrens in Amerika und England. Nach diesem werden
Schmiedeeisen-Abfälle in Graphittiegeln geschmolzen, die in einem eigenen Flammofen
Angesetzt sind. Diese Tiegel fassen 67 Pfund Einsatz und halten 6 bis 7
Beschickungen aus. Als Brennmaterial verwendet man Erdöl oder Erdölrückstände und
ist in den Stand gesetzt, 11 Schmelzungen in 12 Stunden auszuführen. Jeder Tiegel
ist mit einem Deckel bedeckt, der eine Oeffnung besitzt, welche sich direkt unter
einer solchen des Gewölbes befindet. Die Guſsformen bestehen aus einer Mischung von
Einern feuerfesten Thon, der gebrannt, zerkleinert und mit Melasse als Bindemittel
versehen ist. Dieses Material hat sich vorzüglich bewährt. Das Ausgieſsen geschieht
mittels einer bedeckten, heizbaren Guſspfanne.
Schmiedeeisen schmilzt nach Oestberg's Ansicht bei
ungefähr 4000° F. und es würde nothwendig sein, es weit über seinen Schmelzpunkt zu
erhitzen, wenn es flüssig genug sein sollte, um, in feine Formen gegossen, dieselben
gut auszufüllen. In dieser Ueberhitzung liegt nun die Gefahr, daſs das Eisen Gase
absorbirt, die es unmöglich machen würden, dichte Güsse herzustellen. Um diesem
Uebelstande abzuhelfen, machte Oestberg Gebrauch von
der wohl bekannten Thatsache, daſs der Schmelzpunkt gewisser Metalllegirungen unter
jenen der zusammensetzenden Bestandtheile liegt. Unter diesen Legirungen sind die
Aluminiumlegirungen sehr bemerkenswerth.
Bei der Erzeugung von Mitisgüssen wird in dem Augenblicke, in dem die Beschickung
geschmolzen erscheint, eine sehr geringe Menge Aluminium, etwa 0,05 Proc., in den
Tiegel gegeben, und zwar nicht als reines Aluminium, sondern in der Form einer
Aluminium-Eisen-Legirung, die 6 bis 8 Proc. Aluminium nebst etwa 1 bis 1,25 Proc. Si
enthält. Der Schmelzpunkt des Ganzen sinkt sofort um etwa 500° F.; die Beschickung,
die dann fast um 500° über ihren neuen Schmelzpunkt erhitzt erscheint, wird ungemein
flüssig und läſst sich in die feinsten Formen gieſsen. Dieser bedeutende
Flüssigkeitsgrad gestattet das Entweichen der Gase, die sonst den Guſs porös machen
würden. Als Resultat erhält man einen auſserordentlich dichten, festen und zähen
Guſs von Schmiedeeisen.
Es mag hier gleich erwähnt werden, daſs man durch den Aluminiumzusatz je nach Wunsch
ein härteres oder ein weicheres und sogar ein schweiſsbares Material erhalten
kann.
Der Mitisguſs erfährt in Amerika die günstigste Beurtheilung. Ledebur findet die wesentliche Aufgabe des Aluminiums in der Zerstörung
des im Eisenbade gelösten Eisenoxyduls. Letzterer ist also mit Henrotte der gleichen Meinung, daſs das Aluminium sich
wie der Phosphor bei der Herstellung der Bronze verhält, während Oestberg glaubt, daſs durch den Aluminiumzusatz die
Temperatur der Legirung so weit herabgesetzt werde, daſs das Metall die Eigenschaft
verliert, Gase zu erzeugen.
Nordenfeldt benutzt zur Herstellung von Mitiseisen den
in Fig. 15
abgebildeten Ofen, welcher aus drei Theilen besteht. Die dem Herde zunächst liegende
Abtheilung ist der Schmelzraum, die beiden anderen hinten angeordneten sind
Vorwärmräume. In jeder Abtheilung haben zwei Schmelztiegel aus Graphit Platz. Diese
Oefen werden womöglich mit flüssigem Brennstoffe geheizt. Den Zug besorgt eine Esse,
die mit Register versehen ist. Die Wände sind mit Luftkühlungskanälen durchzogen.
Der Kanal o dient dazu, die Verbrennungsproducte direkt
in den Kamin abzuführen während der Zeit, daſs die Tiegel ausgenommen werden. Die
Abtheilungen, welche die Tiegeln enthalten, sind mit Deckeln, die Schaulöcher
enthalten, schlieſsbar. Als Brennmaterial verwendet man mit Vortheil Nebenproducte
der Destillation des Erdöles oder Theer.
Der Zufluſs des Brennmateriales erfolgt durch ein Rohr, welches dasselbe in den
obersten Kübel bringt. Jeder enthält ein Ueberlaufrohr, durch welches die unten
liegenden Tröge versorgt werden, aus dem letzten Kübel flieſst der Brennstoff in
einen besonderen Behälter.
Die Verbrennungsluft dringt bei den Zwischenräumen der Trogreihe ein, verbrennt einen
Theil des Brennstoffes und verflüchtigt einen anderen Theil, und erst in der Kammer
d vollzieht sich die vollkommene Verbrennung, die
hiezu nöthige Luft tritt durch die Oeffnung m zu. Der
Luftzutritt ist regulirbar.
Die Verbrennung des Oeles ist eine vollkommene; die erzeugte Temperatur ist höher als
jene in metallurgischen Oefen bisher erreichte.
Der Einsatz für einen Tiegel beträgt 30k; englische
Tiegel halten 5 bis 6 Schmelzungen aus.
Das Einschmelzen dauert 75 Minuten, demnach ebenso lange, um für einen Ofen 60k zu erzeugen, woraus sich die Erzeugung für 12
Stunden mit Maximum 550k berechnet.
Das Verfahren, welches in diesem Ofen ausgeführt wird, unterscheidet sich von der
Herstellung des Tiegelguſsstahles im Wesentlichen nur durch das Eintragen von
Eisenoxyd haltigen Eisenbriquettes in die Tiegel und den Zusatz von Aluminium.
Nach der Revue universelle, 1888 III., 2. S. 190, soll
das Mitiseisen zu der Annahme berechtigen, die Schmiedearbeit umgehen zu können.
(Schluſs folgt.)
Tafeln
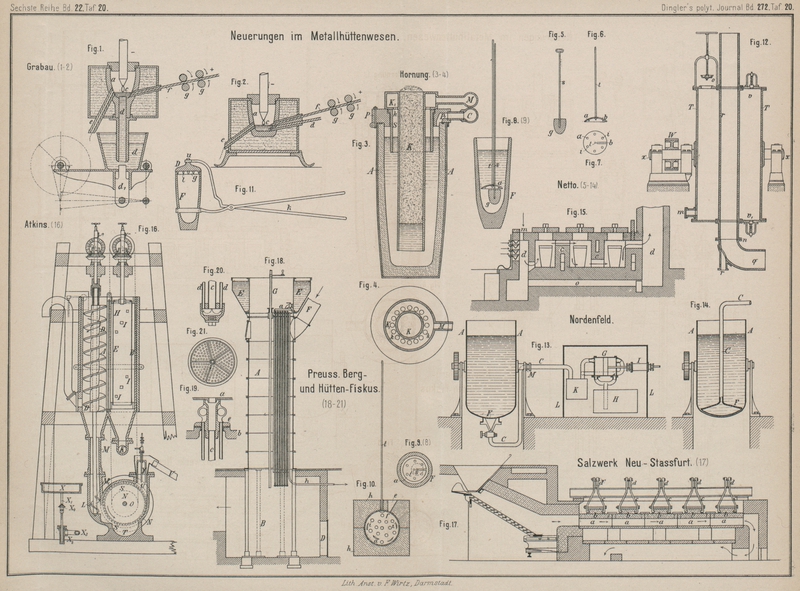