Titel: | Neuere Steinbearbeitungsmaschinen. |
Autor: | Pr. |
Fundstelle: | Band 275, Jahrgang 1890, S. 481 |
Download: | XML |
Neuere Steinbearbeitungsmaschinen.
Mit Abbildungen auf Tafel
24.
Neuere Steinbearbeitungsmaschinen.
Die Einführung maschineller Arbeitsverfahren in den Steinbruchsbetrieben von
Gesteinsarten massiger Zusammensetzung, wie Marmor, Porphyr, Granit, zum Behufe des
Ausbringens von Blöcken und späterer Verarbeitung zu Platten u. dgl. gewährt in
jeder Richtung entschiedene Vortheile gegenüber dem bisher üblichen Ausspitzen der
Blockform mittels der Spitzhaue.
Es wird nicht nur der Gesteinsblock mit gröſserer Regelmäſsigkeit, Leichtigkeit und
Sicherheit aus dem Gebirge zu bringen sein, sondern es wird auch in Folge der
schmalen Schnittbreite an Werkstücksmaterial beträchtlich gewonnen und an
Arbeitskraft gespart, abgesehen davon, daſs die Handarbeit beinahe vollständig durch
Maschinenkraft ersetzt werden kann.
Obwohl die beim Tunnelbaue verwendeten Gesteinsbohrmaschinen mit Druckluft- oder
Preſswasserbetrieb auch in dem Steinbruche eingeführt werden könnten, so ist doch
ein wirthschaftlicher Vortheil von einer solchen Betriebsweise wegen der hohen
Anlagekosten und schon aus dem Grunde kaum zu erhoffen, weil damit der Sprengbetrieb
verbunden werden müſste, was wieder die Zuverlässigkeit des Ausbringens
verringert.
Hiernach beschränkten sich die maschinellen Hilfsmittel des Steinbruchsbetriebes auf
Stoſsbohrer, Handsäge u. dgl., deren Verwendbarkeit durch die örtlichen Verhältnisse
nur zu oft behindert ist Umsomehr dürfte daher die Erwähnung und Beschreibung eines
neueren Marmorbruches mit maschineller Einrichtung willkommen sein. Die in Fig. 1
dargestellte Anlage bezieht sich nach Revue générale des
Machines-outils, 1889 Bd. 3 Nr. 5 * S. 34, bezieh. The Engineering and Mining Journal, 1889 * S. 478, auf den Marmorbruch Traigneaux bei Philippeville, Namour, Belgien, welcher
von Léon Wilmart mit Maschinenbetrieb eingerichtet
wurde, wobei zu erwähnen ist, daſs ähnliche Werkseinrichtungen in Italien (Carrara,
Seravezza), in Bayern (Bioberg), Hannover (Oberkirchen) und in Finnland, Spanien,
Tunis und Algier sich vorfinden.
Der Arbeitsgang ist folgender: In jede Ecke des rechteckig auszuschneidenden
Gesteinsblockes werden mittels Rohrbohrer Löcher bis zu einer Tiefe gebohrt, welche
der künftigen Blockhöhe entspricht. Hierauf werden in zwei gegenüberstehenden
Ecklöchern die Standsäulen der Sägemaschine lothrecht eingelegt, deren Rollen,
entsprechend dem Sägefortschritte, stetig niedergestellt werden, bis das wagerecht
laufende Sägedrahtseil die vorgeschriebene Schnitttiefe ausgeführt hat.
Ist der Block durch zwei oder drei solcher Schnittflächen vom anstehenden Gebirge freigelegt, so wird
derselbe mittels Treibkeile von seiner Unterlage abgetrieben und gelöst, so daſs der
freigelegte Gesteinsblock bloſs eine unregelmäſsige
Bruchfläche aufweist.
Um dieser Bruchfläche eine möglichste Regelmäſsigkeit zu geben und den Block vor dem
Springen zu sichern, wird der 3 bis 4m lange und
2m hohe Block, selbstverständlich mit der
Längsseite, an das freie Gelände angeordnet.
Die Ecklöcher erhalten natürlich eine derartige Gröſse, daſs sowohl die Standsäulen
wie die Seilrollen ungehinderten Platz darin zur Aufstellung finden. Weil aber bei
kostbarem Steinmaterial dadurch ein wesentlicher Abbruch der Blockkanten entsteht,
so wird diese Einbuſse dadurch abgemindert, daſs entweder zwei sich verschneidende
kleinere Löcher neben einander in der Schnittrichtung oder drei dergleichen in
Winkelform oder vier in Kreuzform an jeder Blockecke gebohrt werden, wobei die
Steinbohrkerne als Werkstücke zu Säulen brauchbare Verwendung finden.
Während das Sägedrahtseil Mittel zur Kraftübertragung und Werkzeug zugleich ist, wird
das mit Stahlmessern wirkende Bohrwerk durch ein gewöhnliches Drahtseil
bethätigt.
Ursprünglich bestand der von Paul Gay 1880 verwendete
Sägedraht aus einem einzelnen Stücke weichen Quadratstahles von 3 bis 7mm Durchmesser, welcher mäſsig verwunden über die
erforderlichen Leitrollen geführt, an der Schnittstelle mittels Sand und Wasser
wirkt. Weil aber nach erfolgter Abnützung der Drahtkanten die Fortschiebung des
Sandes aufhört, so ist man nach vielfachen Versuchen zur Anwendung eines
dreidrähtigen Kabels von 3 bis 7mm Durchmesser
übergegangen, welches sich gut bewähren soll. Die Verbindung der Kabelenden erfolgt
mittels Splieſsung der Stahldrähte auf 1m,5 Länge,
wobei die einzelnen Drahtenden bloſs eingebogen und der Bewegungsrichtung
entsprechend hakenförmig zurückgelegt werden. Die Leistung wird durch die Stärke der
Windung beeinfluſst, weil bei kleiner Steigung oder starker Windung der Drähte,
selbst bei auffallender Abnützung des Sägekabels, noch so viel Kerben und Kanten an
denselben verbleiben, welche den arbeitenden Sand in der Schnittfurche fortzuleiten
vermögen, da nur den scharfen Sandkörnern im Vereine mit dem zuflieſsenden Wasser
allein die Arbeitswirkung, dem Sägekabel aber, wie schon erwähnt, die Fortrückung
des Sandes zugeschrieben werden kann.
Mit einem Kabelstrange von 180 bis 200m Länge
werden, bei 200k täglichem Sandbedarfe, annähernd
40 bis 50qm Schnittfläche in belgischem Marmor
geleistet, so daſs auf 1qm Schnittfläche 4 bis
5m Kabelverbrauch bezieh. auf 1m verbrauchte Kabellänge ¼ bis ⅕qm Schnittfläche gerechnet werden können.
Es wiegen 100m laufende Kabellänge von 6, 5½, 5 und
3½mm Durchmesser 16,5, 14,5, 12,5 und 6k,5, deren Grundpreis sich auf 28,0, 28,0, 31,5 und 32,8 M. für
100k stellt, so daſs der Ersatz von 100m Kabellänge ohne Rücksicht auf das verbleibende
Altmaterial 4,62 bezieh. 4,06, 3,94 und 3,16 M. kostet, woraus sich die
Schnittkosten von 1qm Steinfläche bloſs in Bezug
auf den Verschleiſs des Sägekabels mit 0,16 bis 0,25 M. berechnen.
Den über 800mm groſse Seilscheiben laufenden
Sägekabeln wird eine secundliche Geschwindigkeit von 4 bis 4m,25 gegeben, je nachdem dieselben im Steinbruche
oder auf dem Werkplatze arbeiten, während denselben bei 3 bis 4m Schnittlänge des Blockes ein Quervorschub
gegeben wird, der im Granit und Porphyr 20 bis 40 bezieh. im belgischen Marmor 100
bis 120, im weiſsen Marmor 300 und im Tuffstein (pierre d'Euville) bis 500mm in der Stunde betragen kann, wozu für ein
einzelnes Sägekabel annähernd 2 Betriebskraft anzunehmen sind.
In der in Fig.
1 Taf. 24 dargestellten Steinbruchsanlage von Traigneaux steht links das
Maschinenhaus A, in deren Nähe am Werkplatze mehrere
Blocksägen B sich vorfinden. Im Steinbruche ist ein
Bohrwerk C und ein Sägewerk D1 und D2 im Betriebe. Dem über Leitrollen E geführten Treibseile F
für das Bohrwerk, sowie dem Sägekabel G wird mittels je
einer Spannrolle H die erforderliche Spannung gegeben.
Die Leitrollenträger E, sowie das Bohrgerüste C werden durch Zugeisen verankert, während an den
Standsäulen die nach allen beliebigen Richtungen einstellbaren Rollenlager bequeme
Befestigung finden. Eine Kraftwinde J erleichtert den
Transport der Gesteinsblöcke.
Thonar's Bohrwerk (Fig. 2 bis 4) besteht aus
dem Blechrohre A von 500 bis 700mm Durchmesser und 3m,5 Höhe, an welchem der Stahlschuh B
angesetzt und der an seiner Stirnfläche an Stelle der üblichen schwarzen Diamanten
mit einer Schmirgel- und Weichmetallmischung ausgesetzt ist. Verschiedene Löcher in
der Schuhwandung vermitteln den Durchfluſs des Sand- und Wasserstromes nach dem
Bohrkerne.
Das Bohrgerüst besteht aus drei Winkelstützen I, dem
Fuſsringe J und der Kopfplatte H, sowie der selbständigen Spurplatte D für
die vierkantige Triebwelle C. Diese wird von der
Rillenscheibe G bethätigt und treibt mittels eines
Mitnehmers T, U (Fig. 4) die Bohrröhre A, welche nur durch ihr Eigengewicht den Bohrdruck
ausübt. Leitrollen R an N, O,
P vermitteln den Seiltrieb, welcher so bemessen ist, daſs die Bohrröhre 180
minutliche Umdrehungen bei 200 bis 250mm
stündlichem Vorschub in belgischem Marmor macht.
Die Bohrröhre wird vermöge eines Halseisens am Mitnehmer T, zweier Drahtseile X, welche am Querstücke
W enden und über die Stützrollen Y laufen, durch die Handwinde V auch zeitweise während des Bohrbetriebes aus dem Bohrorte gehoben, um
den zwischen der Steinseele und der inneren Rohrwand eingeklemmten Gesteinsbrei
auszuspülen. Nach beendetem Bohrvorgange wird die Bohrröhre A sammt Spindel C aus dem Bohrgerüste
entfernt und der abgedrückte Steinkern mittels der Winde V
ausgehoben. Zum Betriebe eines solchen Bohrwerkes werden 3 bis 3,5
angenommen.
Das Sägewerk für den Steinbruchsbetrieb (Fig. 5) besteht aus zwei
getrennten Theilen A und B, welche in die Eckbohrlöcher eingesetzt werden. Die Ausführung A ist aus einem U-Eisenrahmen zusammengesetzt, in
welchem das Seilscheibenlager sich führt und vermöge einer selbststeuernden
Schraubenspindel nach Maſsgabe des Schnittfortschrittes Höhenverstellung erhält. Am
Rahmenkopfe ist das Leitrollenlager und das steuernde Schneckentriebwerk angeordnet.
Diese Vorrichtung wird als ein Ganzes in das Bohrloch eingekeilt, während nach der
zweiten Bauart B (Fig. 5) die Standsäule,
auf welcher sich die Seilscheibe verschiebt und wagerecht dreht, in die geometrische
Achse des Bohrloches eingesetzt wird.
Die Verstellung in der Höhenrichtung wird durch ein Rollenkreuz p, p erreicht, welches ebenfalls auf der Standsäule
gleitend durch die Steuerspindel mit Handbetrieb niedergestellt wird. Bei dieser
Einrichtung sind mindestens zwei Bohrlöcher und verschiedene Leitrollenböcke
erforderlich, deshalb erscheint der Einbau viel umständlicher als bei der
geschlossenen Bauweise A.
Der Leitrollenbock E (Fig. 6) für das Trieb- und
Sägekabel besteht aus einem mittleren Standrohre, welches mittels drei Zugeisen am
Boden verankert wird. Der Rollenträger ist nicht nur nach jeder Richtung stellbar,
sondern auch jedes Einzellager unabhängig gemacht, so daſs die Rollenebenen in
beliebige Schräglagen gebracht werden können. Ebensowohl kann die Leitrolle auf
einem Gelenkzapfen an die Spitze des Standrohres angeordnet werden (Fig. 5), wodurch eine
gröſsere Freiheit in der Richtungswahl des Seiltriebes erreicht wird.
Der Spannscheibenbock H (Fig. 7) erhält
verschiedene Ausgestaltung, je nachdem das Drahtseil über eine stehende oder
beliebig schrägliegende Spannrolle unmittelbar oder mit Hilfe von Leitrollen geführt
wird. In der Hauptsache ist der Spannbock aus Balken zusammengebaut, wobei a die Schwellen, b die
Säulen, c der stellbare Führungsrahmen und d der Rollenwagen bedeuten.
Diese Spannwerke (H
Fig. 1) sind
selbstverständlich hoch am Steinbruchsrande angeordnet, damit die Drahtseile den
Arbeitsplatz nicht behindern.
Die Blocksäge (Fig. 8 bis 10) dient zur Zerlegung
der Gesteinsblöcke am Werkplatz. Das Sägegerüst besteht aus vier abgedrehten
Standsäulen A von 100mm Durchmesser, welche mit zwei ⊺-Trägerschienen B verbunden einen stehenden Rahmen von 3,35 und 2m,3 Weite und Höhe bilden. An den Säulen gleiten
die Lager C für die Seilscheiben D, während diese Lager durch Schraubenspindeln V gleichmäſsig dadurch niedergestellt werden, daſs eine
über Rollen R geführte Gliederkette G beide Spindeln gleichzeitig bethätigt.
Dieser Antrieb wird von der rechtsliegenden Scheibenwelle D mittels Schneckenrad und Stirnradtriebwerk V,
E auf die Kettenrolle R übertragen. Von der
Leitrollenwelle D1 wird
ein kleines Pumpwerk L betrieben, welches das
Spülwasser aus der Sammelgrube K in den Behälter H hebt, von wo es der Eingriffsstelle des Sägekabels
a zugeleitet wird.
Der auf einem kleinen Rollwagen Q aufgelegte Steinblock
wird frei an die neue Schnittstelle angestellt, indem vorher das Sägekabel mittels
eines rasch wirkenden Vorgeleges M durch Handbetrieb
aus der Schnittfurche ausgehoben wurde.
Die Plattensäge (Fig. 11 bis 14) wirkt mit
einer gröſseren Anzahl 3,5 bis 4mm starker
Sägekabel, welche mit 4m,5 Geschwindigkeit laufen
und 100 bis 120mm Schnitttiefe in der Stunde
hervorbringen.
Die Anordnung des Seilzuges ist aus Fig. 13 ersichtlich und
leicht verständlich, während das eigentliche Sägewerk (Fig. 11 und 12) in der
Bauart etwas von der vorbeschriebenen Blocksägemaschine abweicht.
Die vier Standsäulen a des Maschinengerüstes haben in
ihrem mittleren Längstheile den in Fig. 14 dargestellten
Querschnitt, in deren seitlichen Langschlitzen die Scheibenlager A gleiten, welche mittels vier Schraubenspindeln
gleichzeitige Verstellung erhalten können. Diese Säulen sind auf zwei Längsträger
k (Fig. 11) aufgeschraubt,
tragen einen Kopfrahmen d, wodurch ein Gerüst von 4,0
bezieh. 3,4 und 1m,7 Länge, Höhe und Tiefe
gebildet wird.
Der Abstand der einzelnen Seilscheiben wird der vorgeschriebenen Plattendicke
entsprechend mittels Beilagen geregelt und mit je einer durchgehenden Schraube g gesichert.
Weil aber die Seilscheiben dadurch leicht verzogen werden, so hat man diese Anordnung
dahin abgeändert, daſs man an Stelle voller Scheiben bloſs Spurkränze verwendet, die
man auf eine abgedrehte Trommel in bestimmten Abständen aufschiebt, durch Einlagen
hält und mittels eines Längskeiles treibt. Schwierigkeiten bereitet die Erzielung
einer gleichmäſsigen Kabelspannung, welche sicher nur dadurch zu erzwingen ist, daſs
man jedem einzelnen Sägekabel ein selbständiges Spanngewicht Q (Fig.
13) gibt.
Der Kraftbedarf einer solchen 10 fachen Plattensäge ist zu 4 bis 5
angegeben.
Die Steinplattenschleifmaschine besitzt eine mit 20
minutlichen Umläufen wagerecht kreisende, guſseiserne Scheibe von sechseckiger
Auſsenform und 1350mm äuſserem Durchmesser, welche
mit 36cylindrischen Schleifstücken ausgesetzt ist.
Je nach dem Zwecke bestehen diese Schleifstücke aus einer Metallschmirgelmasse von
entsprechender Mischung und Zusammensetzung, indem Schmirgelsand in ein Metallbad
geschüttet und dieses Gemisch in gewünschte Formen abgegossen wird.
Zum Schleifen von Marmorplatten wird eine Guſseisenschmirgelmasse gebraucht, während
Blei-, Zinn-, Antimon-, Messing- und Kupferschmirgelmasse für andere Gesteinsarten
verwendet wird.
Die lothrechte, mit Winkelrädern angetriebene Schleifscheibenspindel wird theilweise
entlastet und erhält ein Zwischenstück, welches mit doppeltem Universalgelenke an
die Antriebspindel und die Schleifscheibe angekuppelt ist, wodurch bei Verrückung
des Lagers dieser Zwischenwelle aus der Lothrechten auch eine Verstellung der
Schleifscheibe gegen die Marmorplatte nach der Breitseite derselben erreicht
wird.
Die auf den Tisch eines Rollenwagens aufgelegte Marmorplatte wird vermöge eines
Zahnstangentriebwerkes nach Art der Hobelmaschinen in Hubbewegung versetzt und unter
der kreisenden Schleifscheibe hin und her geführt, während durch deren Mittelöffnung
ein beständiger Wasserzufluſs unterhalten wird.
Zum Betriebe dieser Plattenschleifmaschine sind 3 bis 4 angenommen.
Die jährliche Leistung des Marmorbruches von Traigneaux ist zu 400cbm nach Maſs geschnittener Platten angegeben,
wobei eine Betriebskraft von 30 und eine Belegschaft von 30 Mann und 5
Jungen vorhanden war.
Pr.
Tafeln
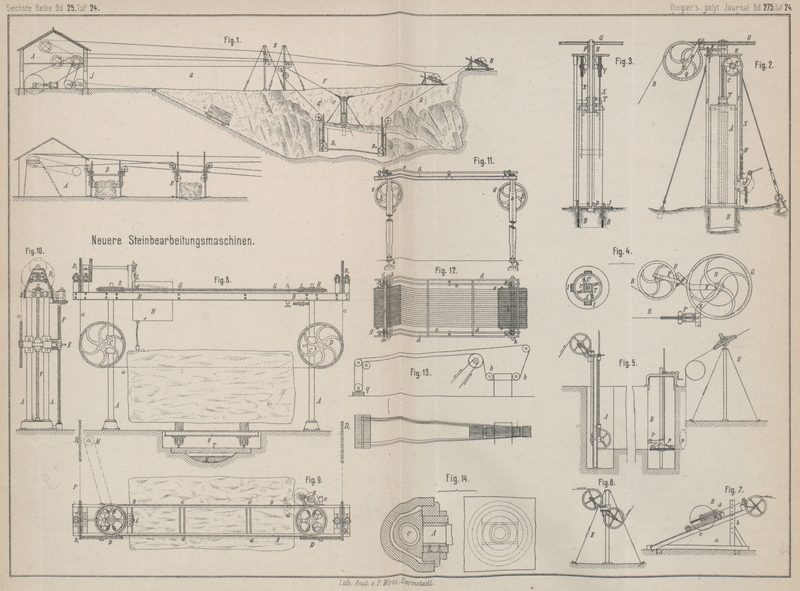