Titel: | Neuerungen im Metallhüttenwesen. |
Fundstelle: | Band 277, Jahrgang 1890, S. 481 |
Download: | XML |
Neuerungen im Metallhüttenwesen.
(Fortsetzung des Berichtes Bd. 275 * S.
246.)
Mit Abbildungen auf Tafel
25.
Neuerungen im Metallhüttenwesen.
Graf Eduard v. Rottermund in Limburg (Belgien) benutzt
vornehmlich bei den sogen. Chlorirungsprozessen zur Extraction von Metallen,
vorzugsweise von Edelmetallen, aus Erzen den in Fig. 1 dargestellten
Apparat. Derselbe besteht aus mehreren Recipienten A
aus mit Blei plattirtem Eisen. Der mittlere Theil derselben bildet einen
Hohlcylinder, welcher oben und unten durch conische Theile B und C begrenzt wird.
An seinem oberen Ende besitzt der conische Theil C einen
Hals, in den zwei Rohre E und F münden. Das Rohr E dient zur Abführung der
Flüssigkeiten nach auſsen, während das Rohr F zur
Verbindung mit dem benachbarten Recipienten dient.
In dem Hals, welcher durch eine Platte M hermetisch
verschlossen ist, ist ein Filter D unterhalb der beiden
Rohrmündungen E und F
angeordnet. In dem unteren conischen Theile B ist
zwischen zwei Bleiplatten gleichfalls ein Filter angebracht. Am Boden des Theiles
B befinden sich sechs mit Hähnen versehene Rohre.
Das eine derselben F dient zur Verbindung mit dem
benachbarten Recipienten, vier Rohre H der übrigen fünf
führen zu den die zur Behandlung der Erze nothwendigen Flüssigkeiten enthaltenden
Behältern K. Das letzte Rohr L dient zur Entleerung des Recipienten A.
Der cylindrische Theil jedes Recipienten ist mit einer Oeffnung G versehen, die durch einen Verschluſsdeckel hermetisch
verschlossen wird und zur Entfernung der Rückstände dient.
Die Wirkungsweise des vorliegenden Apparates ist folgende:
Durch den am oberen Theil angebrachten Hals füllt man die zwölf den Apparat bildenden
Recipienten A mit Erz, legt darauf die Filterplatte D ein und verschlieſst die Recipienten hermetisch.
Darauf öffnet man in einem der Rohre H den Hahn und
entläſst die erforderliche Flüssigkeit in den Recipienten. Dieselbe flieſst dann mit
dem nöthigen Druck durch das im Theil B angeordnete
Filter, durchdringt die Erze, ohne Hohlräume zu bilden, geht dann durch den
conischen Theil C, das Filter D und das Rohr F zum benachbarten
Recipienten.
Wenn die Flüssigkeit durch drei benachbarte Recipienten gedrungen ist, ist sie
gesättigt, und man läſst dieselbe durch das Rohr E
abflieſsen. Nachdem der erste Recipient durch die passende Flüssigkeit vollständig
gewaschen ist, wird derselbe aus der Reihe ausgeschlossen, indem man den Hahn im
Rohr H und den im Rohr F
des ersten Recipienten schlieſst. Der frühere zweite Recipient der ersten Reihe ist
jetzt der erste. Man öffnet darauf den Hahn des entsprechenden Rohres H, schlieſst dann den Hahn in dem Rohre E des dritten Recipienten und öffnet gleichzeitig den
Hahn des Rohres F, wodurch der vierte Recipient als
dritter in die neue nunmehr gebildete Reihe tritt. Hierauf öffnet man den Hahn des
Rohres E im vierten Recipienten, um die Flüssigkeit
abflieſsen zu lassen.
Bei diesem Verfahren ist man im Stande, die zweite passende Flüssigkeit durch die
schon mit der ersten Flüssigkeit gewaschenen Recipienten in Reihen von drei zu drei
flieſsen zu lassen, ohne mit dem gleichzeitigen Waschen der folgenden Recipienten
mit der ersten Flüssigkeit aufhören zu müssen.
Die Recipienten des Erfinders besitzen jeder vier Rohre, die mit den Behältern K, welche die verschiedenen Flüssigkeiten enthalten, in
Verbindung stehen. Hierdurch ist es möglich, die in denselben enthaltenen Erze durch
vier verschiedene Flüssigkeiten gleichzeitig und gesondert in Reihen von drei
Recipienten zu waschen (vgl. D. R. P. Nr. 51897 vom 18. September 1889).
Samuel Wilkins Cragg aus Baltimore in Maryland
(Nordamerika) will das bereits vielfach abgeänderte Plattner'sche Verfahren nochmals umgestalten. Nach seinem Vorschlage
werden die erhitzten Erzmassen mit trockenem Chlorgas
in einem mit Dampfmantel umgebenen Gefäſs in der Weise behandelt, daſs durch den
einströmenden Dampf die Temperatur in dem Chlorirungsgefäſs während der Behandlung
100 bis 150° C. beträgt, ohne daſs die zu chlorirenden Erze, sowie die Chlorgase mit
dem Erwärmungsmittel (Dampf, Gas) in Berührung kommen.
Gold und Silber sollen nach diesem Verfahren in wenigen Secunden chlorirt werden. Zur
Auslaugung der Chloride von Gold und Silber werden alsdann Cyankalium,
Kupfercyankalium, unterschwefligsaurer Kalk oder unterschwefligsaures Natron
vorgeschlagen. Wenn kein Silber vorhanden ist, so empfiehlt sich auch Alkohol. Bei
Anwendung der Cyanverbindungen ist ein Zusatz von Alkalicarbonat von Vortheil. Zum
Auslaugen dienen hölzerne Gefäſse, die mit einem Asphaltüberzug, Doppelboden und
entsprechendem Filter versehen sind, während die Chlorirung in guſseisernen
Gefäſsen, die mit Blei gefüttert sind, stattfindet.
Fig. 2 zeigt im
Senkrechtschnitt einen für die Chlorirung der zerkleinerten erhitzten Erze dienenden
Apparat. Derselbe soll namentlich für solche Erze geeignet sein, in welchen das Gold
eingesprengt ist und die einzelnen Goldblättchen so dünn sind, daſs schon nach ganz
kurzer Einwirkung des Chlors eine Umwandelung stattfindet.
Der Apparat besteht aus der senkrechten Kammer C, welche
in ihrem oberen Theile die mit Triebrad A1 versehene Welle A
aufnimmt. Die Welle A trägt an ihrem unteren Ende eine
passende, mit Oeffnungen B1 versehene Vertheilungsvorrichtung B.
Unterhalb der letzteren befinden sich in der Kammer C
unter rechtem Winkel zu einander angeordnete Reihen wagerechter Rohre H gelagert, welche mit dem Dampfraume L des die Kammer C
umgebenden Dampfmantels K in Verbindung stehen, so daſs
der durch den Zwischenraum L und die Röhren H passirende Dampf, die heiſse Luft u.s.w. eine
Erhitzung der in der Kammer befindlichen Erze und Gase herbeiführt, ohne mit diesen
letzteren in Berührung zu kommen.
Die zerkleinerten und erhitzten Erze werden mittels der Hand oder anderer passender
Zufuhrvorrichtung in den Trichter D geschüttet und beim
Hinabfallen durch den rotirenden Vertheiler B in der
Kammer C gleichmäſsig zerstreut. Die Kammer C ist mit Chlorgas gefüllt, welches durch das Rohr M eintritt und während der Operation durch den Dampf
u.s.w. des Dampfmantels bis zu 150° C. erhitzt wird. Durch die Röhren H wird ein zu schnelles Hinunterfallen der Erze
verhindert, so daſs die Chlorgase genügend auf das vorhandene Edelmetall einwirken
und dasselbe in Chlormetall umwandeln können. Zum Abführen der sich am Boden der
Kammer C ansammelnden Erze dient die Oeffnung C2. Das überschüssige Chlor wird durch das Rohr G abgeleitet.
Durch Fig. 3
wird ein Apparat veranschaulicht, in welchem die Erze längere Zeit der Einwirkung
des Chlors ausgesetzt bleiben. Zu diesem Zwecke befinden sich auf der durchgehenden
Welle A eine Anzahl wagerechter Scheiben B. Die Wandungen der Kammer C sind in der Weise angeordnet, daſs den Scheiben B entsprechend eine Reihe conischer Abtheilungen gebildet werden. Die zu
behandelnden Erze gelangen in einer Rinne E mittels
einer Schnecke in den Trichter D und fallen auf die
oberste Scheibe B, von der sie gegen die schrägen
Flächen der Kammerwand C geworfen werden. Die Erzstücke
gleiten dann auf die nächste rotirende Scheibe herab u.s.w., bis sie den Boden der
Kammer C erreicht haben.
In Fig. 4 und
5 ist die
Anordnung eines Apparates in Längs- und Querschnitt gezeigt, der sich besonders zur
Behandlung schwer aufschlieſsbarer Erze eignet. Derselbe besteht aus der wagerechten
Trommel a, welche von Rollen b in der Weise getragen wird, daſs eine Rotation um die Längsachse der
Trommel stattfinden kann. Im Inneren der Trommel sind Zellen oder Schaufeln c angebracht, welche bei einer Drehung die Erze in die
Höhe heben und ein gründliches Umrühren derselben bewirken. Zum Zwecke der Erwärmung
ist die Trommel a wieder mit einem Dampfmantel d umgeben. Der Eintritt des Dampfes erfolgt durch das
Rohr e und die Stopfbüchse e1, während die Einführung der Chlorgase
in die Trommel mittels des Rohres F und der Stopfbüchse
F1 stattfindet. Die
Ableitung des gebrauchten Dampfes und der Chlorgase geschieht auf der anderen Seite
der Trommel in ähnlicher Weise. Etwaiges Condensationswasser wird durch besondere
Hähne abgelassen.
Nachdem die Trommel mit Erzen gefüllt ist, wird dieselbe durch eine passende
Antriebsvorrichtung, welche auf den Zahnkranz g wirkt,
in Rotation versetzt. Die Schaufeln c heben die Erze
hoch und werfen dieselben von oben her durch den mit Chlorgasen erfüllten Raum,
wodurch die Erze immer wieder der Einwirkung der Gase ausgesetzt werden, bis eine
vollständige Chlorirung stattgefunden hat.
Ein Zusammenschmelzen der Masse wird verhindert, indem die aus der jeweiligen
höchsten Schaufel fallenden Erzmassen auf die Eisenstäbe oder Rohre h schlagen und zerbröckeln (vgl. D. R. P. Nr. 51117 vom
21. Juni 1889).
Um das Krank- oder Mehligwerden des Quecksilbers während des Amalgamationsprozesses
zu verhindern, wenden Johnson, Field und Beeman nicht
reines Quecksilber zum Amalgamiren an, sondern ein Amalgam desselben, beispielsweise
Zinkamalgam, welches in Berührung mit einer geeigneten verdünnten Säure Wasserstoff
entwickelt. Der nascirende Wasserstoff umgibt dann die losgetrennten, dem Einflüsse
der Luft sonst ausgesetzten Quecksilbertheilchen und verhindert auf diese Weise,
daſs sich dieselben mit einer grauen Haut überziehen. Auch kann der Wasserstoff
durch seine reducirende Wirkung bereits krank gewordenes Quecksilber wieder
beleben.
Nach dem D. R. P. Nr. 51023 vom 15. Mai 1889 (Firma J. und G.
Kumme in Berlin) wird zur Herstellung von Metallröhren durch galvanischen
Niederschlag ein Dorn von beliebiger Länge, welcher aus Eisen, Stahl oder anderem
geeigneten Material besteht und einen der lichten Weite des herzustellenden Rohres
entsprechenden Durchmesser besitzt, in das galvanische Bad gebracht und auf
demselben ein Niederschlag von gewünschter Stärke gebildet. Hierauf wird der Dorn
aus dem Bad genommen, die Metallumhüllung geglüht und dann durch Druck comprimirt.
Alsdann wird der Dorn aus der nunmehr fertigen Röhre gezogen. Man kann auch den Dorn
vor dem Glühen und Comprimiren aus der Hülle ziehen und diese Behandlung auf einem
zweiten Dorne vornehmen. Damit der Niederschlag auf dem Dorn nicht zu fest haftet,
kann der letztere vorher mit einem Ueberzuge von Graphit oder Blei überzogen
werden.
Man kann auch das beschriebene Verfahren zur Herstellung von Röhren aus Streifen
fertigen Bleches benutzen. Zu diesem Zwecke wird der Blechstreifen um einen Dorn
gerollt, welcher nur auf dem Längsstreifen, wo die Kanten des Blechstreifens
zusammenstoſsen, leitend gemacht ist. Auch die auf den Dorn gerollte Blechhülse wird
von auſsen durch eine Umhüllung geschützt und zwar bis auf den offen bleibenden, die
Blechkanten freilegenden Längsstreifen. Es bildet sich dann ein Niederschlag in der
Länge dieses offenen Streifens. Die Löthung ist hier also durch galvanische
Thätigkeit ersetzt. Wegen der Herstellung von Kupferröhren auf galvanischem Wege
siehe Elmore's Verfahren in der Englischen Patentschrift Nr.
15831 vom Jahre 1886, sowie The Electrician, London,
Bd. 20 S. 436. Elmore läſst bekanntlich während der
Bildung des Niederschlages eine Bearbeitung durch Rollen oder Walzen eintreten, um
in dem Niederschlage das krystallinische Gefüge zu zerstören und damit seine
Festigkeit zu erhöhen.
Bei der Fabrikation von Platten, Blechen und sonstigen Gegenständen aus Kupfer und
seinen Legirungen wendet Th. H. Martin in Swansea
(England) bewegliche und zerlegbare Blockformen an, um das schnelle Herüberschaffen
der Stücke von einem Ende der Walze nach dem anderen zu ermöglichen. Die Formen sind
um Zapfen drehbar oder aus einander nehmbar in besonderen Gestellen angeordnet, die
fahrbar eingerichtet und mit einem Kupferboden bezieh. einem Klappboden versehen
sind, nach dessen Lösung die Blöcke ohne Weiteres aus den Formen herausfallen.
Fig. 6 bis 11 der
Zeichnung zeigen derartige Ingotformen in mehreren Ausführungsbeispielen.
Die Ingotform C1 (Fig. 6 und 7) ist eine
doppelte; jede Form ist mittels wagerechter Zapfen gelagert und mit einem inneren
Kupferbelag oder Boden C1 und einem abnehmbaren Deckel e versehen.
Das ganze Gestell für die Form ruht auf einer Schiene f1, welche
mittels Säulen von der Ofenplattform B getragen wird,
wogegen die Füſse des Formgestelles auf dem Flurboden stehen. Am Gestell ist eine
Rolle g behufs schnelleren Transportes der aus der Form
gekippten Ingots vorgesehen.
Die Ingotformen (Fig.
8 und 9) haben einen Klappboden h und eine jede
Form wird von einem Zapfen i der Ofenplattform B getragen. Beim Auslösen des Klappbodens fällt der
Ingot direkt auf den Flurboden.
Kupfer zu groſsen Platten läſst man in die in Fig. 10 im Grundriſs und
in Fig. 11 im
Schnitt dargestellten eisernen Formen C2 einflieſsen. Diese bestehen aus einem niedrigen
Wagen b2, einer
kupfernen Bodenplatte c2 und einem oberen zerlegbaren Rahmen a2, dessen Theile mittels Stangen und Keile
zusammengehalten werden. Die eigentliche Form liegt also, wie dargestellt, auf einem
Wagen.
Die Kupferplatten, Kupferbolzen oder Kupferblöcke läſst man zunächst in den Formen
sich setzen, kippt sie heraus und führt sie dann mittels deren Fahrgestell nach den
Walzen.
Blöcke oder Ingots für die gröſseren Bolzen, Bleche, Platten und Stangen können
direkt aus den Formen C1 und C2,
ohne jedes Nachwärmen, mittels Walzen vor- und nachgewalzt werden (vgl. D. R. P. Nr.
50715 vom 20. Oktober 1888).
Während bisher bei der elektrolytischen Läuterung des Kupfers die gegossenen Anoden
und Kathodenbleche in den Elektrolyten (Kupfersulfat) senkrecht eingehängt wurden,
schlägt Smith in Ansonia (Connecticut) nach dem D. R. P. Nr. 50371 vom
28. November 1888 vor, bei der elektrolytischen Kupferraffination wagerecht
liegende, senkrecht über einander angebrachte Elektroden zu verwenden; dieselben
werden, wie nachstehend erläutert ist, durch isolirte Träger gestützt und haben
baumwollene Filter- oder Spanntücher zwischen sich.
Fig. 12 stellt
einen Stapel zwischen Holzklötzchen aufgeschichteter Kupferplatten dar; aa sind zwei solcher Platten der oberen Lage. Die
unteren Lagen sind durch die dunkleren Linien darunter bezeichnet; bb sind die Holzleisten, welche die Platten tragen und
von einander getrennt halten. Die wagerechten punktirten Linien unter den dunklen
Linien veranschaulichen das zwischen den Kupferlagen ausgespannte Zeug.
Fig. 13 zeigt
die Stapel von drei Behältern und die Art und Weise, wie sie verbunden werden, um
eine verbundene Reihe von Zellen zu bilden. Ein senkrechter Raum c auf der linken Seite von jedem Stapel stellt eine
schmale Kammer dar, welche durch eine quer durch jeden Behälter gehende Scheidewand
gebildet wird.
Durch diese Einrichtung sollen Vorrichtungen, um die Circulation des Elektrolyten
aufrecht zu erhalten, entbehrlich werden. Auch sollen die Bäder vor Wärmeverlusten
und der Elektrolyt soll vor Verdampfung geschützt sein.
Nicolas Lébédeff in St. Petersburg will Eisen, Kupfer
und andere Metalle direkt aus ihren Erzen gewinnen, indem er die Oxyde der
betreffenden Metalle in Tiegeln oder in Flammöfen schmilzt und sie dann der
Einwirkung reducirender Gase (Kohlenoxyd, Wasserstoff, Kohlenwasserstoff), die unter
Druck eingeführt werden, unterwirft (D. R. P. Nr. 51892 vom 9. Mai 1889). In Fig. 14 ist
als Beispiel ein zu dem angegebenen Zwecke zu verwendender Handflammofen
dargestellt.
Zu beiden Seiten des Schachtes c dieses im senkrechten
Schnitt gezeigten Flammofens ist je ein Schmelzherd a
bezieh. b angeordnet. Das niederzuschmelzende Erz d wird durch den Schacht c
eingetragen und am Fuſse desselben durch einen Scheidekamm f nach beiden Seiten gegen a bezieh. b hingeleitet. Von hier zieht man das Erz, das in dem
Schacht c durch das den Ofen durchstreichende Herdfeuer
vorgeröstet wird, nach Bedarf auf die Schmelzherde a
und b, woselbst das Einschmelzen vor sich geht und
woselbst die nöthigen reducirenden Gase durch die Rohre e in die geschmolzene Masse eingeführt werden.
Diese Röhren e können übrigens auch dazu dienen,
oxydirende Gase (wie Luft, Kohlensäure, Wasserdampf u.s.w.) in die Masse
einzuführen, um dieselbe beispielsweise von Metalloiden zu befreien, welche dem zu
gewinnenden Metall schaden könnten, und welche durch das Rösten oder eine sonstige
vorgängige Behandlung nicht vollständig beseitigt sein sollten.
Der Ofen kann mit jeder Art Brennstoff geheizt werden, ebenso wohl mit festem als flüssigem
oder gasförmigem. Wünscht man bei der Verwendung von gasförmigem Brennstoff hohe
Temperaturen, so kann man sich beispielsweise des Wassergases, Naphtagases o. dgl.
bedienen. Statt des dargestellten Schmelzofens kann jeder andere passende
Schmelzapparat verwendet werden.
E. Walsh jr. in St. Louis (Missouri, Nordamerika) hat
unter Nr. 51208 ein vom 1. Mai 1889 gültiges D. R. P. für einen Apparat zum
Condensiren von Zinkdämpfen und Sammeln des metallischen Zinks erhalten, welcher in
den Fig. 15
bis 17
dargestellt ist.
Die gerösteten Zinkerze werden mit Brennmaterial gemischt durch den Trichter b in den Ofen a gebracht.
In letzteren mündet die seitlich angesetzte Condensationskammer c, die mit feuerfestem Stein ausgekleidet ist und eine
conische Form erhält, die nach auſsen mit geringem Gefälle enger wird.
In Fortsetzung des äuſseren Endes der Condensationskammer c ist zweckmäſsig ein aus Guſseisen oder anderem passenden Material
bestehender Cylinder d eingeschaltet, in welchen von
oben ein Beschickungstrichter e mündet. Der Cylinder
d wird auſsen durch einen Deckel f abgeschlossen, der in der Mitte eine Stopfbüchse g für die hindurchtretende Welle h hat. Auf dieser Welle ist ein Cylinder d und eine Transportirscheibe i, welche ungefähr den Cylinderdurchmesser besitzt, so angebracht, daſs
sich deren Anfangspunkt (im Sinne der Drehrichtung derselben) unter oder etwas
hinter dem zugekehrten Rande der Trichteröffnung e
befindet.
Die Welle h wird durch eine Schnecke in Drehung gesetzt,
welche mit einem Schraubenrad der Welle in Eingriff steht, das auſserhalb des
Cylinders liegt. Die Welle l, die in Lagern m läuft, trägt die Antriebsscheibe n. Die
Transportirscheibe kann natürlich auch in anderer geeigneter Weise ihre Drehung
erhalten. Durch den tiefsten Theil der Condensationskammer c werden eine Reihe von Kanälen oder Röhren o
vorgesehen, welche unterhalb der Kammer c in einem Trog
p oder eine andere Ableitung für das metallische
Zink führen.
Nachdem die Beschickung des Ofens a mit dem Kohlen- und
Erzgemisch aus den Trichtern b und die Füllung der
Condensationskammer c mit kohlenstoffhaltigem Material
aus dem Beschickungstrichter e vorgenommen ist, gehen
beim Betriebe, sobald das Beschickungsgemisch und das sich daran anschlieſsende
kohlenstoffhaltige Material der Kammer c eine
Temperatur von 1500° F. angenommen haben, Zinkdampf und Kohlensäure, wie sie bei der
Reduction im Ofen erzeugt werden, durch das kohlenstoffhaltige Material in die
Condensationskammer c, und hierbei wird die Kohlensäure
unmittelbar in Kohlenoxyd verwandelt, welches mit dem Zinkdampf weiter durch die
kühleren Theile des kohlenstoffhaltigen Materials in der Kammer c geht, wobei der Zinkdampf condensirt, als flüssiges
Metall am Boden des Condensationsbehälters c wieder geschlagen und durch
die Röhren o in den Behälter abgelassen wird. Das
Kohlenoxyd geht durch den Trichter e (oder andere
Windkanäle) nach dem Abzug. Die Transportirschraube i,
welche währenddessen langsam gedreht wird, drückt das kohlenstoffhaltige Material,
welches durch den Trichter e eingeführt wird,
continuirlich den Condensationsbehälter c entlang, so
zwar, daſs es an der Mündung nach dem Ofen a hin, wo es
an die Stelle des verbrauchten Brennmaterials tritt, auf eine Temperatur von 1500°
F. erhalten wird, die nach Vorstehendem erforderlich ist, die Kohlensäure in
Kohlenoxyd zu verwandeln, während das kohlenstoffhaltige Material hinter diesem
Theil im Behälter c durch die hindurchstreichenden Gase
selbst auf Temperaturen von 1200 bis 800° gebracht wird, wie sie zur Condensation
der Zinkdämpfe geeignet sind.
Wegen der früheren Vorschläge von Walsh vgl. D. p. J., 1888 269 400.
(Fortsetzung folgt.)
Tafeln
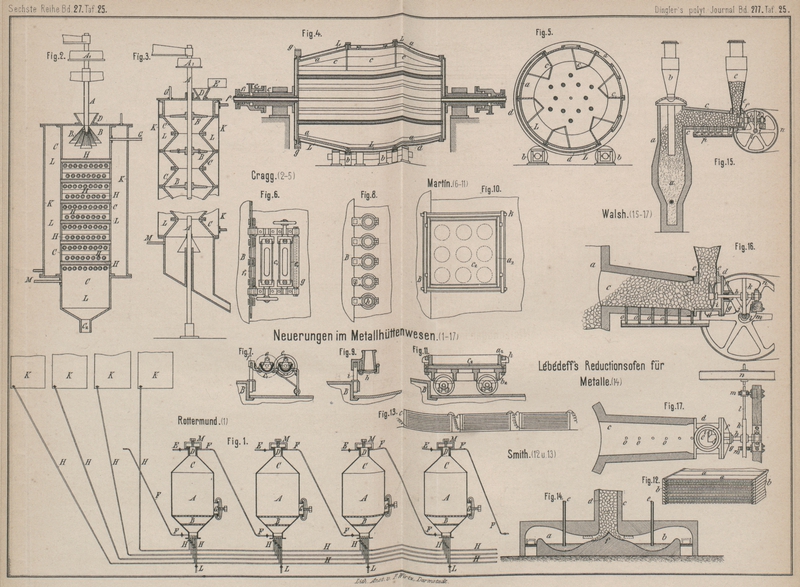